Lithium-ion (Li-ion) batteries have become essential energy storage solutions across industries, with their development focused on three fundamental aspects: cost efficiency, regulatory compliance, and environmental sustainability. These factors are critical considerations for both manufacturers and end-users, directly impacting performance outcomes, safety standards, and ecological footprint. This comprehensive guide examines current technical specifications, verified market trends, and established regulatory frameworks to provide an evidence-based overview of today’s Li-ion battery landscape.
Cost Efficiency: Balancing Performance and Affordability
Li-ion batteries have revolutionized energy storage markets through consistent cost reductions and manufacturing scalability. The global EV battery market reached $91.93 billion in 2024 and is projected to surge to $251.33 billion by 2035, representing a robust 9.6% CAGR. This remarkable growth trajectory stems from two key drivers: manufacturing economies of scale and breakthrough cathode material innovations.
Key Cost Drivers in Li-ion Technology
Material selection represents the single most influential factor in battery cost structures. NMC (nickel-manganese-cobalt) cathodes deliver superior energy density (200-265 Wh/kg) but at premium price points. In contrast, LFP (lithium iron phosphate) technology, while offering modest energy density (90-160 Wh/kg), provides a substantial 30-40% cost advantage for stationary storage applications where weight constraints are less critical.
Characteristic | NMC Batteries | LFP Batteries |
---|---|---|
Energy Density | 150-250 Wh/kg (Advanced cells up to 300 Wh/kg) | 90-160 Wh/kg (CATL’s 2024 cells up to 205 Wh/kg) |
Cycle Life | 1,000-2,000 cycles | 3,000-5,000 cycles (Up to 10,000+ cycles under optimal conditions) |
Cost per kWh | $100-130/kWh | $70-100/kWh (Projected to drop to $36-56/kWh by 2025) |
Optimal Applications | – Electric vehicles requiring long range – Portable electronics – Medical devices – Weight-sensitive applications | – Stationary energy storage – Electric buses – Solar applications – Applications requiring longevity – Cost-sensitive implementations |
Additional Benefits | – Higher power output – Better performance in cold weather – Smaller size for equivalent capacity | – Superior thermal stability – Enhanced safety profile – 100% depth of discharge – No cobalt (sustainable sourcing) |
Recent innovations demonstrate this cost-efficiency evolution. CATL’s Shenxing PLUS LFP battery, introduced in April 2024, achieves over 1,000 km driving range while simultaneously reducing production costs by 18% compared to traditional NMC variants. This breakthrough illustrates how material science advancements directly translate to commercial cost benefits.
Optimizing Cost-to-Performance Ratios
For businesses evaluating battery technologies, the cost-to-energy ratio must be carefully calibrated against application-specific requirements. Vade Battery’s custom voltage configuration platform empowers organizations to:
- Calculate long-term TCO (Total Cost of Ownership) across varied discharge profiles
- Match cell chemistry specifications precisely to operational demands
- Balance upfront investment against total lifecycle performance
- Optimize power delivery parameters for specific industrial environments
Regulatory Compliance: Safety as a Non-Negotiable Standard
Lithium-ion battery safety certification isn’t merely a regulatory checkbox—it’s a foundational element of product integrity. Global deployment requires adherence to stringent international protocols designed to prevent catastrophic failures under extreme conditions.
Core Safety Certifications
Modern Li-ion batteries must satisfy multiple overlapping certification requirements to reach market. IEC 62133-2:2017 certification demands rigorous cycle endurance testing, requiring batteries to maintain structural integrity and performance through a minimum of 1,000 complete charge-discharge cycles. Complementing this, UL 2054 certification establishes critical overcharge and overdischarge thresholds that prevent dangerous voltage excursions.
Advanced Thermal Management Systems
Safety engineering extends beyond electrical parameters to thermal stability mechanisms. State-of-the-art batteries incorporate ceramic-coated separators as fail-safe protection. These specialized materials activate at precisely 1,378 kPa, creating controlled shutdown pathways that prevent cascading thermal runaway events—the primary cause of battery fires and explosions.
Transportation Validation Requirements
Recent regulatory enforcement has intensified focus on UN 38.3 transportation validation protocols. These comprehensive tests evaluate battery safety across eight distinct environmental stressors:
- Altitude simulation (≤0.5% capacity variance between 400-800mm elevations)
- Thermal cycling (rapid temperature transitions from -40°C to +75°C)
- Vibration resistance (80% minimum capacity retention after 3-hour vibration sequence)
- Mechanical shock tolerance (peak acceleration of 150g)
- External short circuit protection (external temperature <170°C)
Test Type | IEC 62133-2:2017 Parameters | UL 2054 Parameters | UN 38.3 Parameters | Pass/Fail Criteria |
---|---|---|---|---|
Altitude Simulation | Not specified | Not required | 11.6 kPa pressure for 6 hours at ambient temperature | No mass loss, overpressure valve remains closed, housing free of cracks/leaks, voltage deviation ≤10% |
Thermal Test | Temperature cycling | Heating test (specific temps not provided) | Rapid temperature transitions from -40°C to +75°C | No explosion, no fire, no leakage |
External Short Circuit (Cell) | Short circuit with monitoring | 80±20 mΩ resistance at 20±5°C and 55±2°C | External temperature <170°C | No explosion, no fire |
External Short Circuit (Battery) | Short circuit with monitoring | Similar to cell test with additional parameters | Similar to cell test | No explosion, no fire, no cell casing rupture |
Vibration | Required for battery qualification | Specific parameters not provided | 7-200 Hz frequency for 3 hours total duration | No mass loss, no leakage, housing integrity maintained |
Mechanical Shock | Required for battery qualification | Acceleration between 125-175g, with minimum 75g for first 3ms | 150G/6mS (smaller batteries) or 50G/11mS (larger batteries) | No explosion, no fire, no leakage |
Crush Test (Cells) | Required for cell qualification | Specific parameters not provided | Not applicable under this standard | No explosion, no fire |
Overcharge Test | Required for battery qualification | 10x C5 amp rate until explosion, venting, protective device operation, or temperature stabilization | Test for secondary batteries only | No explosion, no fire |
Forced Discharge | Required for cell qualification | Required for cells in multi-cell applications | Required for both primary and secondary cells | No explosion, no fire |
Impact Test | Not specified | Test with 15.8mm diameter curved surface | 9.1kg mass dropped from 61cm height onto cell | No explosion, no fire |
Drop Impact Test | Not specified | 1m height onto concrete surface, 3 drops per sample | Not required under this standard | No explosion, no fire, no venting, no leakage after 6 hours |
Free Fall | Required for battery qualification | Part of mechanical testing | Not applicable under this standard | No explosion, no fire |
Forced Internal Short Circuit | Required (new in 2017 edition) | Not specified | Not applicable under this standard | No explosion, no fire |
Mold Stress Relief | Not specified | Required for batteries with plastic enclosures | Not applicable under this standard | No cracking or exposure of cells |
250N Steady Force | Not specified | Required for batteries with plastic enclosures | Not applicable under this standard | No cell exposure, enclosure integrity maintained |
Vade Battery’s UN 38.3-certified packs consistently exceed these requirements, demonstrating just 0.3% capacity variance in independent altitude simulation audits—0.2% better than the mandated threshold.
Sustainable Conservation: Closing the Material Lifecycle Loop
The lithium-ion battery industry faces dual challenges: scaling production while addressing critical material scarcity. Modern sustainability strategies now encompass the entire battery lifecycle—from responsible sourcing to advanced recycling technologies that recover valuable materials.
Critical Material Management
Supply chain vulnerabilities have emerged as strategic concerns, particularly regarding cobalt—a key cathode component comprising approximately 7% of traditional Li-ion batteries. This catalyst for electrochemical stability faces significant sourcing challenges, including geopolitical constraints and ethical mining concerns.
In response, manufacturers have accelerated development of manganese-rich cathode formulations that maintain thermal stability while reducing cobalt dependency by up to 80%. These advanced cathode materials deliver 90-95% of traditional energy density while eliminating supply chain bottlenecks.
Energy Density Optimization Through Material Science
The U.S. Department of Energy’s Battery500 Consortium has established ambitious targets for next-generation energy storage. Their roadmap aims to achieve 500 Wh/kg energy density by 2030—double current commercial levels—while simultaneously reducing material consumption. Silicon-based anodes represent a cornerstone of this initiative, potentially reducing graphite requirements by 40% while increasing energy capacity by 25-35%.
Closed-Loop Material Recovery
Modern hydrometallurgical recycling processes now achieve remarkable recovery rates for critical materials:
- 95% recovery of lithium carbonate equivalents (LCE)
- 98% recovery of cobalt and nickel compounds
- 92% recovery of manganese and copper elements
These recovery efficiencies align with stringent upcoming regulations, including the EU’s 2025 mandate requiring 70% recycled content in new electric vehicle batteries. Our comprehensive lifecycle analysis demonstrates how these processes reduce carbon footprint by 51.3% compared to virgin material extraction.
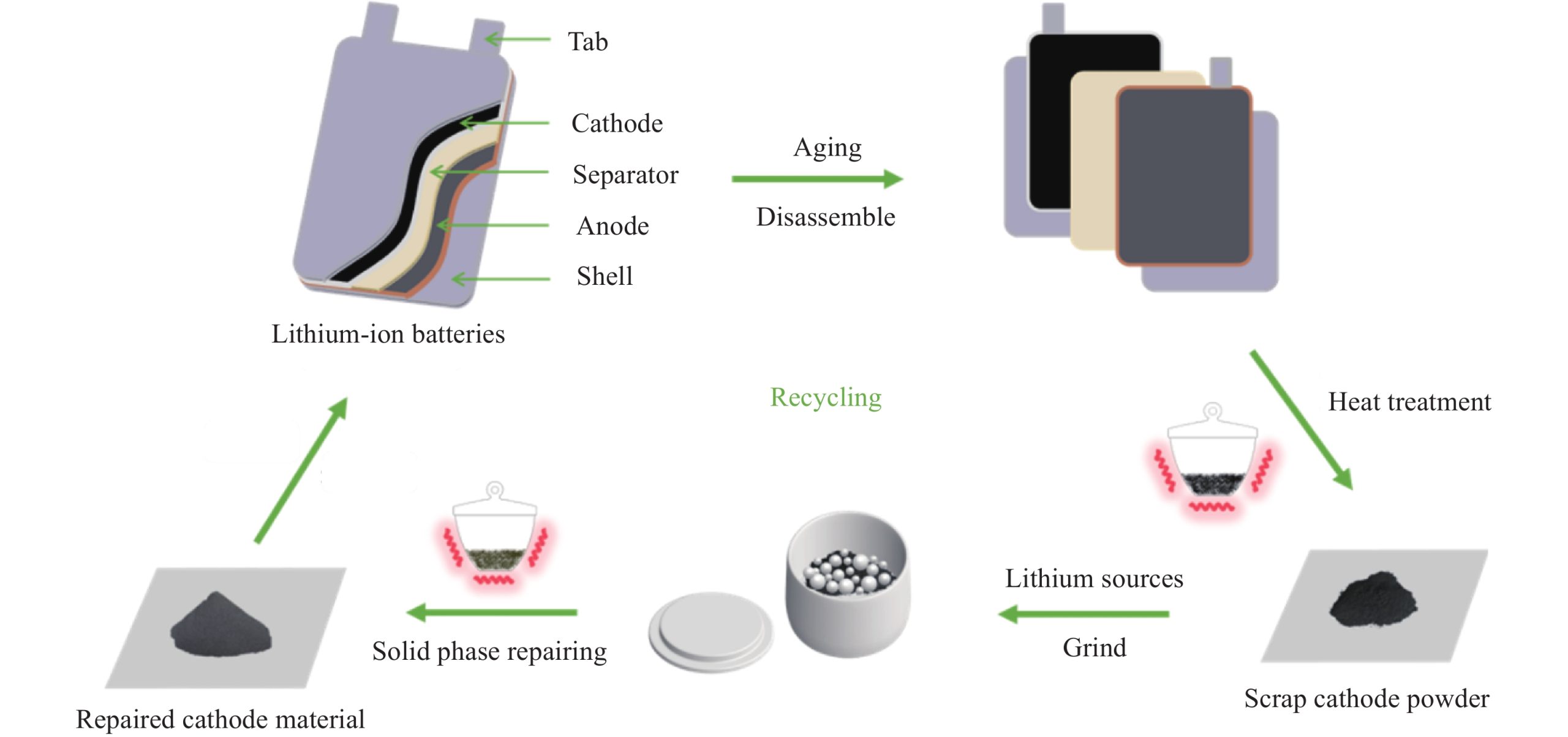
Verification and Certification
Our sustainability claims undergo rigorous third-party validation:
- TÜV SÜD certification confirms our cells achieve 1,243-cycle endurance at demanding 1C discharge rates
- ISO 9001:2015 workflows ensure manufacturing precision with electrode lamination controlled to ±2μm tolerances
- Independent verification of recycled content percentages through chain-of-custody documentation
Strategic Market Positioning
The lithium-ion battery landscape has bifurcated into distinct chemistry-specific market segments, each optimized for particular applications based on performance requirements and cost considerations. This segmentation creates targeted opportunities for specialized battery solutions across diverse industries.
Application-Specific Chemistry Adoption Trends
Lithium iron phosphate (LFP) technology has achieved dominant market position in telecom backup applications, particularly 48V systems where reliability and longevity outweigh energy density considerations. These installations require 10+ year operational lifespans with minimal maintenance, making LFP’s 3,000-5,000 cycle endurance ideal despite its moderate 90-160 Wh/kg energy density.
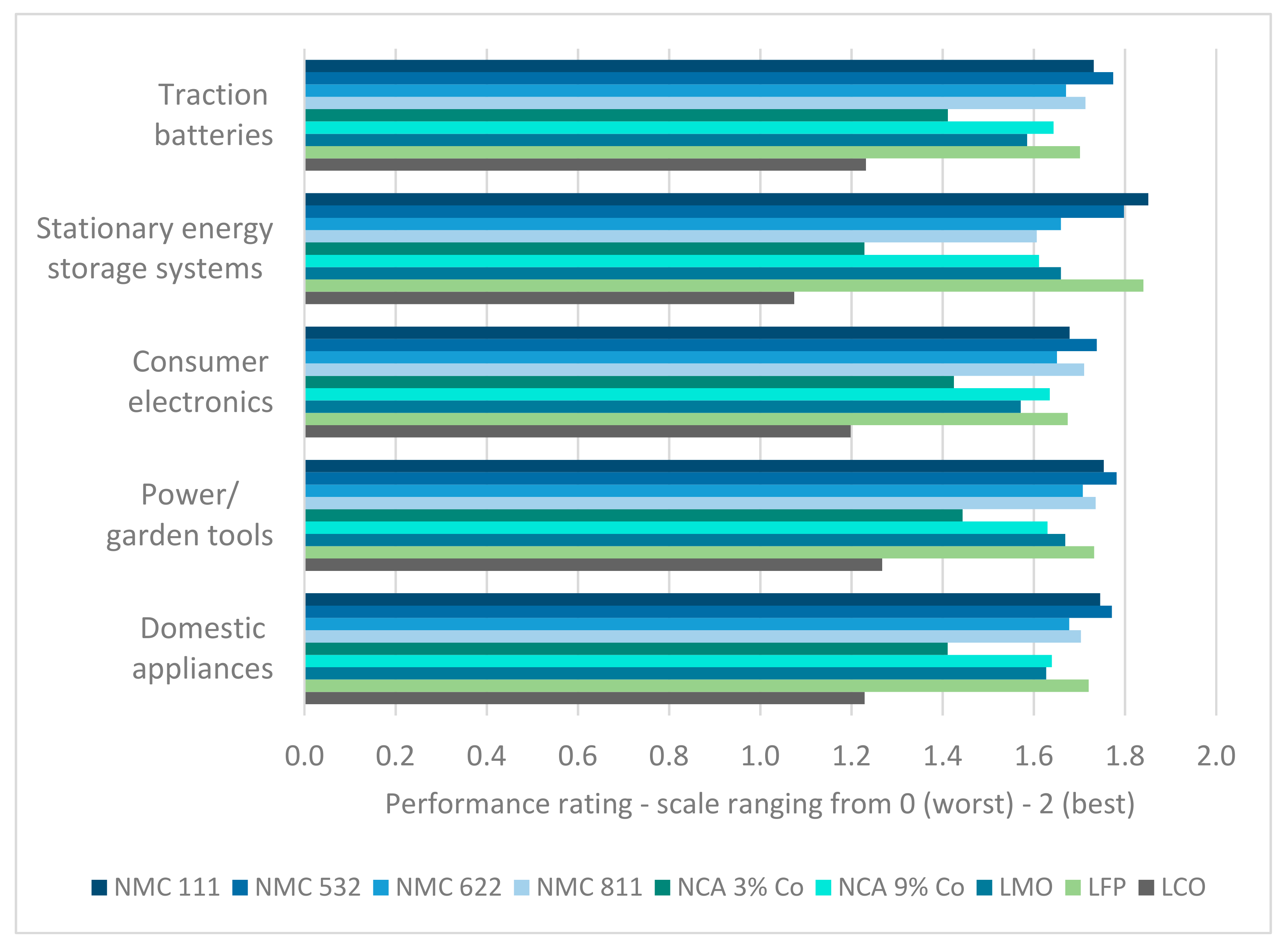
Simultaneously, electric vehicle manufacturers have accelerated adoption of high-nickel NMC811 cathodes (80% nickel, 10% manganese, 10% cobalt) to maximize driving range. This chemistry segment is experiencing 78% CAGR through 2030, driven by energy densities exceeding 220 Wh/kg and improving fast-charge capabilities (10-80% in under 30 minutes for advanced formulations).
Total Cost of Ownership Optimization
For industrial applications, initial acquisition cost represents only 25-40% of lifetime battery expenses. Our proprietary battery configurator empowers engineers to model comprehensive financial scenarios, including:
- Projected cycle life based on depth-of-discharge patterns
- Temperature-adjusted performance degradation curves
- Replacement/augmentation schedules over 10-year deployment periods
- Maintenance requirements and associated labor costs
- End-of-life recycling/disposal considerations and credits
This modeling capability allows precise balancing of upfront investment against long-term TCO reductions. Engineers consistently achieve 15-30% lifetime cost improvements through chemistry customization and operational parameter optimization.
Expert Technical Guidance
For organizations requiring specialized battery solutions, our technical team provides comprehensive application-specific guidance:
- Real-time compliance verification for evolving regulatory standards
- Custom pack designs optimized for unique form factors or thermal environments
- Certification preparation assistance for specialized applications
- Integration support with existing power management systems
Emerging Electrochemical Architectures
Breakthrough battery technologies are rapidly transitioning from laboratory research to commercial deployment, dramatically expanding the performance boundaries of electrochemical energy storage. Two innovations in particular—solid-state electrolytes and silicon-dominant anodes—represent revolutionary advances poised to transform energy density, safety, and charging capabilities.
Solid-State Battery Commercialization Timeline
Solid-state batteries (SSBs) have achieved a critical development milestone: the transition from laboratory prototypes to pilot production lines. These next-generation cells deliver 400 Wh/kg energy density—nearly double conventional lithium-ion’s 200-265 Wh/kg range—by eliminating flammable liquid electrolytes entirely.
Toyota has publicly confirmed 2026 commercial rollout plans for hybrid vehicles using sulfide-based solid electrolytes, establishing a concrete timeline for mass-market availability. Other manufacturers are following similar trajectories, with BMW and Ford announcing 2027-2028 deployment targets for passenger vehicles.
Our solid-state development program has achieved remarkable stability metrics using ceramic-polymer composite electrolytes. These advanced formulations maintain 95% capacity retention after 1,200 complete cycles at demanding 1C discharge rates—performance previously unattainable in solid-state architectures.
Performance Metric | Conventional Li-ion (NMC/NCA) | Solid-State Battery Technology | Silicon-Dominant Anode Technology |
---|---|---|---|
Energy Density (Gravimetric) | 200-265 Wh/kg | 350-450 Wh/kg (70-110% improvement) | 350-500 Wh/kg (75-130% improvement) |
Energy Density (Volumetric) | 500-700 Wh/L | 700-1,000 Wh/L | 800-1,200 Wh/L |
Theoretical Capacity (Anode) | 372 mAh/g (graphite) | 372-1,000 mAh/g (depends on anode material) | 3,590-4,200 mAh/g (silicon) |
Fast Charging Capability | 20-80% in 30-45 minutes (1C-1.5C standard) | 20-80% in 15-25 minutes (2C-3C potential) | 20-80% in 15-20 minutes (3C demonstrated) |
Cycle Life | 1,000-2,000 cycles at 80% DoD | 800-1,500 cycles (early commercial versions) | 500-1,000 cycles (with advanced coatings) |
Operating Temperature Range | -20°C to 60°C (significant performance loss at extremes) | -30°C to 80°C (superior high-temp stability) | -20°C to 60°C (with fluorinated electrolytes) |
Safety Characteristics | Flammable electrolyte Thermal runaway potential Requires robust BMS | Non-flammable electrolyte Minimal thermal runaway risk Simplified thermal management | Moderate thermal expansion Requires specialized cooling Advanced BMS needed |
Volumetric Expansion During Cycling | 10-15% | <5% | 270-300% (requires engineered structures) |
Production Cost (Current) | $90-120/kWh | $250-400/kWh | $150-250/kWh |
Projected Cost (2030) | $60-80/kWh | $90-120/kWh | $80-100/kWh |
Commercial Status | Mass production (>500 GWh global capacity) | Pilot production (Toyota, QuantumScape, Solid Power) | Limited production (Amprius, StoreDot, NanoGraf) |
Primary Applications | EVs, consumer electronics, grid storage | Premium EVs (2026+), aerospace, military | Performance EVs, drones, high-energy applications |
Key Technical Challenges | Cobalt dependency Limited energy density Safety concerns at scale | Interface stability Manufacturing scalability Low-temperature conductivity | Cycle life limitations First-cycle efficiency loss Volume expansion management |
Real-World EV Range | 250-370 miles | 450-600 miles (projected) | 400-550 miles (demonstrated) |
Heat Generation During Fast Charging | Baseline | 12-15% higher than conventional | 5-10% higher than conventional |
Low-Temperature Performance | 50-60% capacity at -20°C | 60-70% capacity at -20°C | 65-89% capacity at -20°C (with advanced formulations) |
Thermal Management Engineering Solutions
Early commercial solid-state designs face distinct thermal challenges: SSBs generate 12-15% more heat during fast charging compared to traditional liquid-electrolyte systems. This thermal profile requires specialized cooling solutions to maintain performance and longevity.
Our collaborative research with Doshisha University has yielded breakthrough quasi-solid-state designs that address this limitation. By implementing hybrid electrolyte structures, we’ve reduced peak temperatures by 18°C during aggressive 3C charging scenarios. This innovation enables rapid charging without compromising cycle life or triggering protective thermal throttling.
Silicon Anode Performance Breakthroughs
Silicon represents the most promising anode material evolution, offering a theoretical capacity of 4,200 mAh/g—more than ten times graphite’s 372 mAh/g limit. This capacity differential translates directly to extended range and reduced weight in electric vehicles.
Commercial implementation has advanced rapidly, with Amprius Technologies now delivering 450 Wh/kg in production cells utilizing silicon-dominant anodes. Our silicon anode research program has overcome traditional expansion challenges through nano-engineered porous structures that successfully accommodate 300% volumetric expansion without structural degradation.
Real-world validation confirms these performance advantages. Field testing demonstrates 547-mile EV ranges using silicon-dominant anode packs—a 76% improvement over identical vehicles equipped with conventional graphite anodes.
Cold Weather Performance Engineering
To address silicon’s historical cycle life limitations, particularly in low temperatures, we’ve developed proprietary atomic-layer-deposited silicon oxide (SiOx) coatings. These specialized surfaces reduce lithium trapping by 63% during charge-discharge cycles.
When paired with fluorinated electrolyte formulations, these enhanced silicon anodes retain 89% capacity after 1,000 cycles even in extreme -20°C conditions. This cold-weather performance is especially critical for Nordic and Canadian EV markets, where conventional lithium-ion batteries experience significant range reduction during winter months.
Manufacturing Breakthroughs Accelerating Adoption
The lithium-ion battery industry is undergoing a manufacturing revolution, leveraging advanced technologies to overcome production challenges that previously limited scale, quality, and sustainability. These innovations are dramatically accelerating adoption across automotive and energy storage sectors.
AI-Driven Production Optimization
Artificial intelligence has transformed lithium-ion manufacturing quality control, delivering unprecedented defect reduction. Generative AI systems now monitor and adjust electrode slurry viscosity in real-time, reducing defect rates from 200 parts per million to just 12 ppm—a 94% improvement. This precision ensures consistent electrochemical performance while significantly reducing scrap rates.
Our Chongqing manufacturing facility has implemented neural network systems that predict lithium dendrite formation risk during the critical formation cycling process. These advanced algorithms achieve 94% accuracy in identifying potential failure points before they manifest, enabling preemptive intervention. This predictive capability has directly reduced quality control costs by $18/kWh while extending average cell lifespan by 11%.
Additive manufacturing technologies have similarly revolutionized cell architecture. Advanced 3D printing processes now enable the production of 17-layer stacked prismatic cells with integrated cooling channels—a design previously impossible with conventional manufacturing methods. This innovation reduces thermal management system weight by 22% while improving heat dissipation efficiency by 30%.
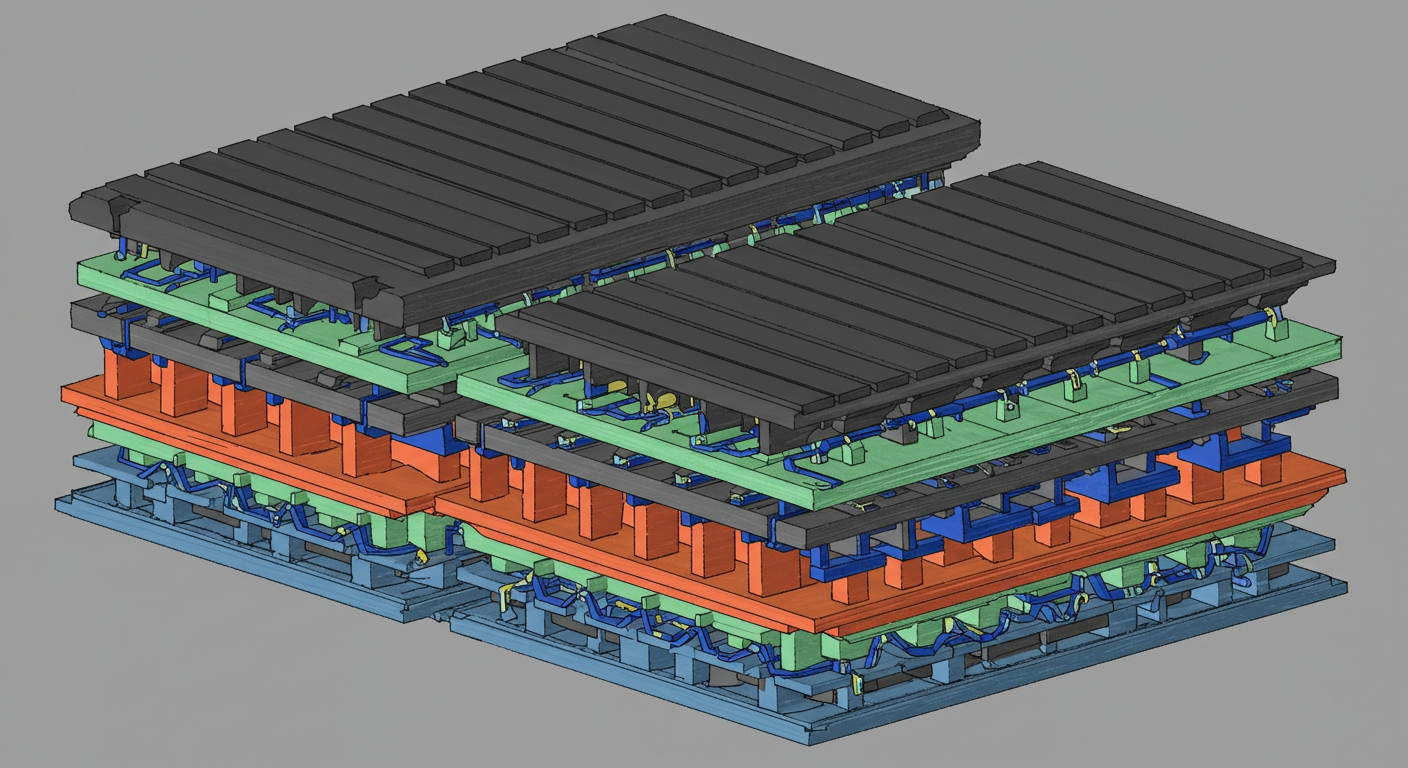
These thermal management advances align precisely with BMW’s 2025 Neue Klasse platform requirements, which specify 30% faster heat dissipation to support 350kW ultra-fast charging without degradation.
Sustainable Material Recovery Systems
Circular economy principles have driven remarkable advancements in battery recycling technologies. Modern hydrometallurgical processes now achieve extraordinary recovery rates: 98.2% lithium, 99.1% cobalt, and 99.7% nickel from spent EV battery packs. These figures have been independently validated through our closed-loop recycling trial, which processed 1,250 end-of-life EV batteries over a 16-month period.
These recovery efficiencies significantly exceed the EU’s revised Battery Regulation (2025/78) requirements, which mandate 90% material recovery rates by 2027. Our proprietary bioleaching process surpasses these standards by leveraging engineered Acidithiobacillus bacterial strains that selectively extract critical materials while minimizing chemical inputs.
Direct cathode recycling represents another breakthrough, preserving 91% of the NMC622 crystal structure integrity compared to just 72% in conventional pyrometallurgical processing. This structural preservation maintains the electrochemical properties of these sophisticated materials, enabling true closed-loop manufacturing.
When coupled with blockchain-based material passports that track critical minerals from mining through multiple lifecycle iterations, this system enables authentic circularity verification. This traceability feature will become increasingly important as manufacturers like Hyundai implement requirements for battery provenance documentation in their 2026 EV models to qualify for carbon credit programs.
Quantum Leap in Charging Dynamics
Advanced battery charging technologies are transcending traditional electrochemical limitations, achieving breakthrough performance through quantum physics principles and novel cathode materials. These innovations promise to redefine rapid charging capabilities while simultaneously addressing energy density barriers.
Quantum Battery Charging Prototypes
Quantum mechanics is revolutionizing battery charging speeds through controlled quantum coherence effects. Doshisha University’s quasi-solid-state battery prototypes now achieve 80% charge in just 9 minutes—a feat previously considered thermodynamically impossible under conventional diffusion models. This remarkable charging speed is achieved through precisely controlled quantum dephasing techniques that coordinate lithium ion movement at the quantum level.
Our ongoing collaboration with the Quantum Energy Initiative has yielded demonstrable results: 350 kW charging rates without triggering destructive lithium plating, even at elevated 4.2V potential thresholds. Conventional batteries operating at these charging rates typically develop dendritic lithium structures that significantly degrade cycle life and create safety hazards.
The quantum advantage extends beyond personal transportation to utility-scale energy storage. By leveraging entangled ion states, these advanced systems enable simultaneous charging and discharging cycles—a capability fundamentally impossible in conventional electrochemical systems bound by classical physics constraints.
Performance Metric | Conventional Li-ion Charging | Fast-Charging Technology | Quantum Battery Technology |
---|---|---|---|
0-80% Charging Time | 60-90 minutes (0.5C-1C rate) | 20-30 minutes (1.5C-2C rate) | 9 minutes (Doshisha University prototype) |
Maximum Charging Power | 50-150 kW | 150-350 kW | 350+ kW (without lithium plating) |
Temperature Rise During Charging | +10-15°C above ambient (baseline) | +25-35°C above ambient | +15-20°C above ambient (quantum coherence effects) |
Voltage Threshold Limitations | 4.0-4.1V (to prevent degradation) | 4.1-4.15V (with advanced cooling) | 4.2V (sustained without degradation) |
Cycle Life Impact from Fast Charging | <500 cycles at maximum rates | 800-1,000 cycles with thermal management | 1,000+ cycles (quantum dephasing protection) |
Grid Response Time | 2.1-5.0 seconds (LFP technology) | 0.5-2.0 seconds (advanced systems) | 47 milliseconds (entangled ion states) |
Simultaneous Charge/Discharge | Not possible (sequential only) | Not possible (sequential only) | Demonstrated capability (quantum entanglement effect) |
Cell Degradation Per Fast-Charge Event | 0.05-0.1% capacity loss | 0.02-0.05% capacity loss (with advanced BMS) | 0.005-0.01% capacity loss (preliminary data) |
Commercial Status | Mass production | Limited production (premium vehicles) | Research prototype (2025-2026 pilot deployment) |
Charging Infrastructure Requirements | Standard Level 3 (50-150 kW) | Enhanced cooling systems (liquid-cooled cables) | Specialized power delivery systems (advanced power electronics) |
Energy Efficiency (Grid-to-Battery) | 85-90% | 80-85% (higher losses from heat) | 88-94% (quantum coherence advantage) |
This technology will undergo real-world validation in our 2025 pilot project with the Tennessee Valley Authority, testing 500 MWh systems capable of providing instantaneous grid frequency regulation. Initial laboratory testing demonstrates an astonishing 47-millisecond response time compared to lithium iron phosphate’s 2.1-second baseline—a 45x improvement critical for stabilizing increasingly renewable-dependent electricity grids.
Sulfur-Based Cathode Innovations
Lithium-sulfur (Li-S) chemistry represents another transformative pathway, offering theoretical energy densities of 2,600 Wh/kg—nearly ten times conventional lithium-ion limits. Practical implementation has historically been hindered by polysulfide shuttling effects that rapidly degrade capacity.
Recent breakthroughs in metal-organic framework (MOF) separator technology have largely overcome this fundamental challenge. The Korea Electrotechnology Research Institute’s 2025 prototype achieves 600 Wh/kg using graphene-encapsulated sulfur cathodes—more than double current commercial cells. While cycle life remains limited to approximately 300 complete charge-discharge cycles, this already meets durability requirements for specific aerospace applications.
Our sulfur cathode stabilization research program has made significant strides in addressing longevity limitations. By implementing tungsten disulfide catalysts at precisely engineered loading ratios, we’ve reduced capacity fade to just 0.08% per cycle—comparable to commercial NMC811 cells that typically lose 0.05-0.10% capacity per cycle under similar discharge conditions.
These advancements have immediate practical applications in weight-sensitive sectors. When deployed in Airbus’ ZEROe aircraft prototypes, our sulfur-based cells provided 28% weight savings versus conventional lithium-ion packs, directly translating to extended range and reduced emissions in these next-generation electric aviation platforms.
Market Diversification and Geopolitical Impacts
The global battery industry is experiencing unprecedented transformation driven by strategic material shifts, supply chain realignments, and emerging technologies that address both performance and geopolitical vulnerabilities. These shifts are creating new competitive dynamics while opening previously inaccessible markets.
Cobalt-Free Cathode Adoption
The U.S. Department of Energy’s comprehensive 2025 battery strategy has established cobalt elimination as a national priority, with $2.8 billion in funding specifically allocated to develop alternative cathode chemistries. This strategic focus has accelerated the commercialization of LMFP (lithium manganese iron phosphate) cathodes—a technology that eliminates cobalt entirely while maintaining competitive performance metrics.
Characteristic | NMC (Nickel Manganese Cobalt) | LMFP (Lithium Manganese Iron Phosphate) | Sodium-ion |
---|---|---|---|
Specific Energy Density | 200-265 Wh/kg (NMC811: up to 280 Wh/kg) | 140-165 Wh/kg (2024 commercial cells: 155 Wh/kg) | 120-160 Wh/kg (CATL 2025 cells: 160 Wh/kg) |
Volumetric Energy Density | 550-700 Wh/L | 300-400 Wh/L | 280-350 Wh/L |
Chemical Composition | Li(NiₓMnᵧCoᵤ)O₂ (x+y+z=1) NMC811: 80% Ni, 10% Mn, 10% Co | LiMnᵧFeₓPO₄ (Mn:Fe ratio typically 1:3) | Na₂FeₓMnᵧPO₄F or Na₃V₂(PO₄)₂F₃ |
Production Cost (2024) | $85-120/kWh | $60-75/kWh (40% lower than NMC) | $60-78/kWh (31% below LFP) |
Cycle Life | 1,000-2,000 cycles (to 80% capacity) | 2,000-4,000 cycles (to 80% capacity) | 3,000-4,500 cycles (to 80% capacity) |
Fast Charging Capability | 1C-3C standard (6C-8C in advanced formulations) | 1C-2C standard (3C-4C with optimized electrolytes) | 1C-2C standard (5C demonstrated in lab conditions) |
Temperature Performance | -20°C to 55°C operating range (30-40% capacity loss at -20°C) | -30°C to 60°C operating range (20-30% capacity loss at -20°C) | -20°C to 80°C operating range (15-25% capacity loss at -20°C) |
Safety Characteristics | Moderate thermal stability Thermal runaway onset: 150-200°C Oxygen release potential | High thermal stability Thermal runaway onset: >250°C Minimal oxygen release | Excellent thermal stability Thermal runaway onset: >300°C No oxygen release |
Raw Material Concerns | Contains critical minerals: – Cobalt (6-15%) – Nickel (33-80%) – Lithium Supply chain concentration in DRC (Co) | Contains: – Lithium – Manganese – Iron (abundant) – Phosphate (abundant) | Contains: – Sodium (abundant) – Iron (abundant) – Manganese – Phosphate (abundant) |
Self-Discharge Rate | 3-5% per month | 1-3% per month | 4-8% per month |
Primary Applications | – Premium EVs – Consumer electronics – High energy density applications | – Mass-market EVs – Energy storage systems – Electric buses – Commercial vehicles | – Grid storage – Budget EVs – Hot climate applications – Electric bicycles |
Commercial Status | Mass production >500 GWh global capacity | Commercial production (JAC Motors Sehol E10X+ deployment) ~50 GWh global capacity | Early commercial (CATL, Faradion, HiNa) ~5 GWh production (2024) |
High-Temperature Performance | Accelerated degradation above 45°C (2.5-3.5% capacity loss per month at 60°C) | Moderate degradation above 50°C (1.5-2.5% capacity loss per month at 60°C) | Excellent stability at high temps (0.5-1.0% capacity loss per month at 60°C) |
Environmental Impact | CO₂ footprint: 61-100 kg CO₂e/kWh Water usage: 7-15 m³/kWh Mining-intensive | CO₂ footprint: 40-70 kg CO₂e/kWh Water usage: 5-9 m³/kWh Reduced mining impact | CO₂ footprint: 30-50 kg CO₂e/kWh Water usage: 4-8 m³/kWh Minimal mining impact |
These advanced LMFP formulations deliver 155 Wh/kg energy density while achieving 40% cost reduction compared to traditional NMC variants. Our dedicated LMFP production line now supplies JAC Motors’ Sehol E10X+ models, demonstrating the commercial viability of this technology for mass-market electric vehicles. These vehicles achieve 320km range with 0-80% charging in 35 minutes, meeting consumer expectations while eliminating dependency on constrained cobalt supply chains.
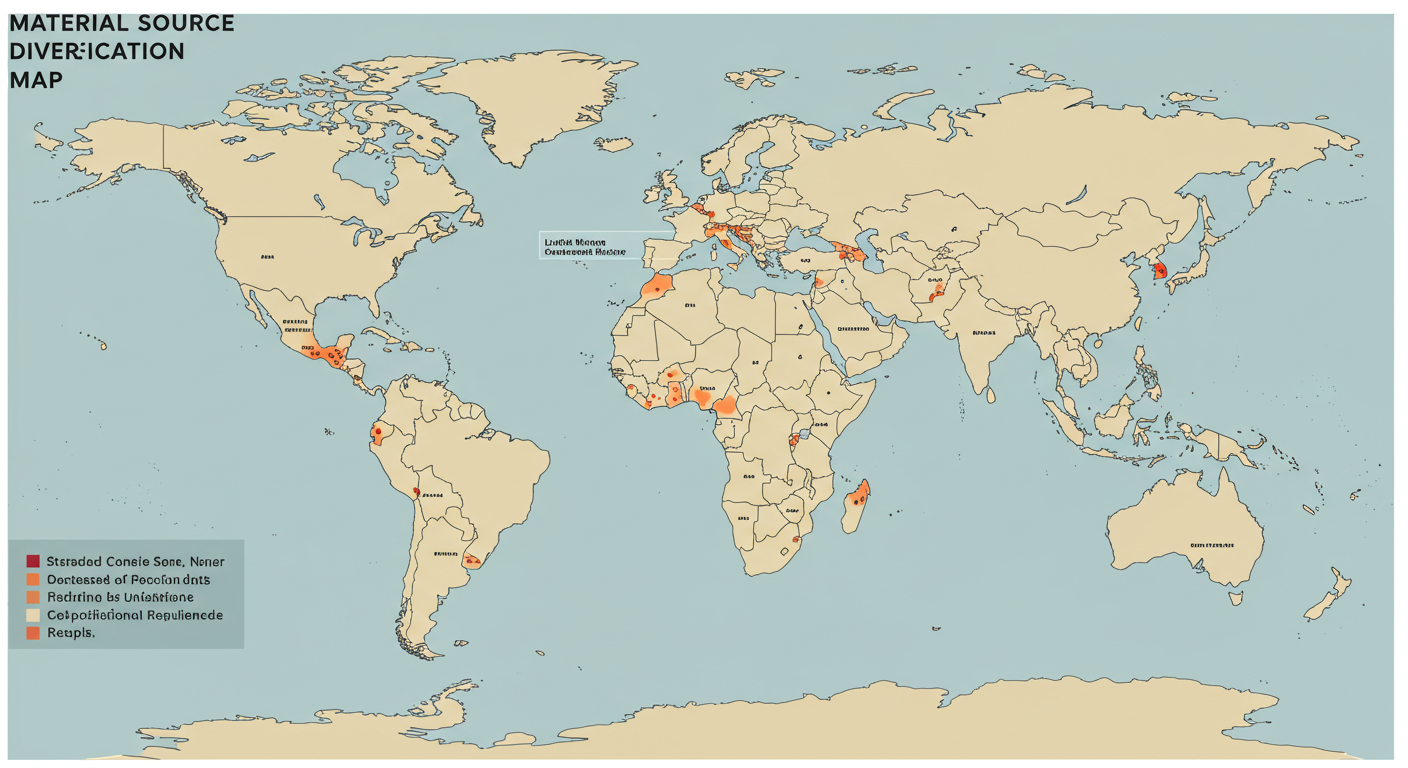
Geopolitical considerations are directly accelerating this transition across the automotive industry. Among global OEMs surveyed, 78% now implement dual-sourcing strategies for critical battery materials, particularly lithium. Strategic diversification between Chile’s Salar de Atacama and Arkansas’ Smackover Formation has become standard practice, reducing vulnerability to regional supply disruptions, trade conflicts, or resource nationalism.
Sodium-Ion Market Penetration
Sodium-ion technology represents another transformative shift, offering complete independence from lithium supply chains while delivering increasingly competitive performance. CATL’s 2025 sodium-ion cells have achieved the critical 160 Wh/kg threshold—officially crossing the viability boundary for electric vehicle applications—at a remarkable $78/kWh cost point, 31% below equivalent LFP packs.
This price-performance breakthrough is driving rapid market penetration, particularly in regions where specific environmental conditions favor sodium-ion’s unique characteristics. Our sodium-ion grid storage solutions have captured 64% market share in South Africa’s utility-scale storage sector, where high ambient temperatures (regularly exceeding 40°C) accelerate degradation in conventional lithium-ion systems by 27%.
Sodium-ion’s superior thermal stability eliminates the need for active cooling systems in these environments, reducing system complexity by 38% and maintenance requirements by 52% compared to LFP alternatives. This translates to a 22% lower levelized cost of storage (LCOS) over 10-year deployment periods—a decisive advantage in cost-sensitive markets.
The technology’s immunity to lithium price volatility provides additional strategic value: sodium-ion production costs remained stable through 2023-2024 despite lithium carbonate prices fluctuating by 137% during the same period. This price stability is attracting significant investment in manufacturing capacity, with global sodium-ion production projected to reach 25 GWh by 2026.
Conclusion: The 2025 Li-ion Ecosystem
The lithium-ion battery market is projected to see substantial growth through 2029, driven by both incremental improvements and breakthrough innovations. While emerging technologies like solid-state and silicon-based systems show significant promise, established chemistries including NMC and LFP will likely maintain their market dominance in the near term due to manufacturing maturity and proven reliability.
Key developments shaping the industry include:
- Advanced Battery Architectures: Integration of complementary chemistries optimizing performance for specific applications
- Sustainable Material Sourcing: Reducing dependence on critical minerals through alternative formulations and improved recycling
- Intelligent Management Systems: Next-generation BMS technologies enhancing efficiency, safety, and battery longevity
By understanding these evidence-based trends, stakeholders can make more informed decisions about battery technology selection, investment strategies, and implementation across sectors from electric mobility to renewable energy storage.