Lithium batteries power everything from smartphones to electric vehicles, but few understand what goes into creating these precision energy solutions. At Vade Battery, we’ve spent a decade perfecting the art of crafting custom lithium battery packs for global clients. This article breaks down the science, materials, and quality controls behind lithium battery manufacturing—and explains how our 18650, Li-ion, lithium polymer, and LiFePO4 battery packs deliver unmatched safety and performance.
Key Takeaways
- Lithium battery production requires six core materials, including specialized cathodes and ultra-pure electrolytes.
- Vade Battery’s laser-welded cell connections and ISO 9001-certified assembly ensure 99.9% defect-free packs.
- Our proprietary Battery Management System (BMS) prevents overheating and extends cycle life by 30% versus industry averages.
Get a Custom Battery Quote | Explore Our LiFePO4 Battery Packs
What Materials Power Lithium Batteries?
Every lithium battery starts with three critical components:
1. Battery Cells – The Heart of the System
Vade Battery uses NMC (LiNiMnCoO2) cells for high-energy applications like EVs and LiFePO4 cells for industrial equipment requiring extreme longevity. Our 18650 cells, like those in our 24V industrial battery packs, deliver 2,500 mAh capacity with ±1% voltage consistency across batches.
2. Electrolyte – The Ion Highway
We use LiPF6 (lithium hexafluorophosphate) electrolytes with additive packages that stabilize performance from -40°C to 60°C. This is critical for our ultra-low temperature batteries used in Arctic research equipment.
3. Battery Management Systems – The Guardian
Our in-house designed BMS monitors each cell’s voltage (±0.02V accuracy) and temperature. If a cell exceeds 45°C, the system reroutes current to cooler cells—a feature that prevented thermal runaway in 100% of our client field tests since 2022.
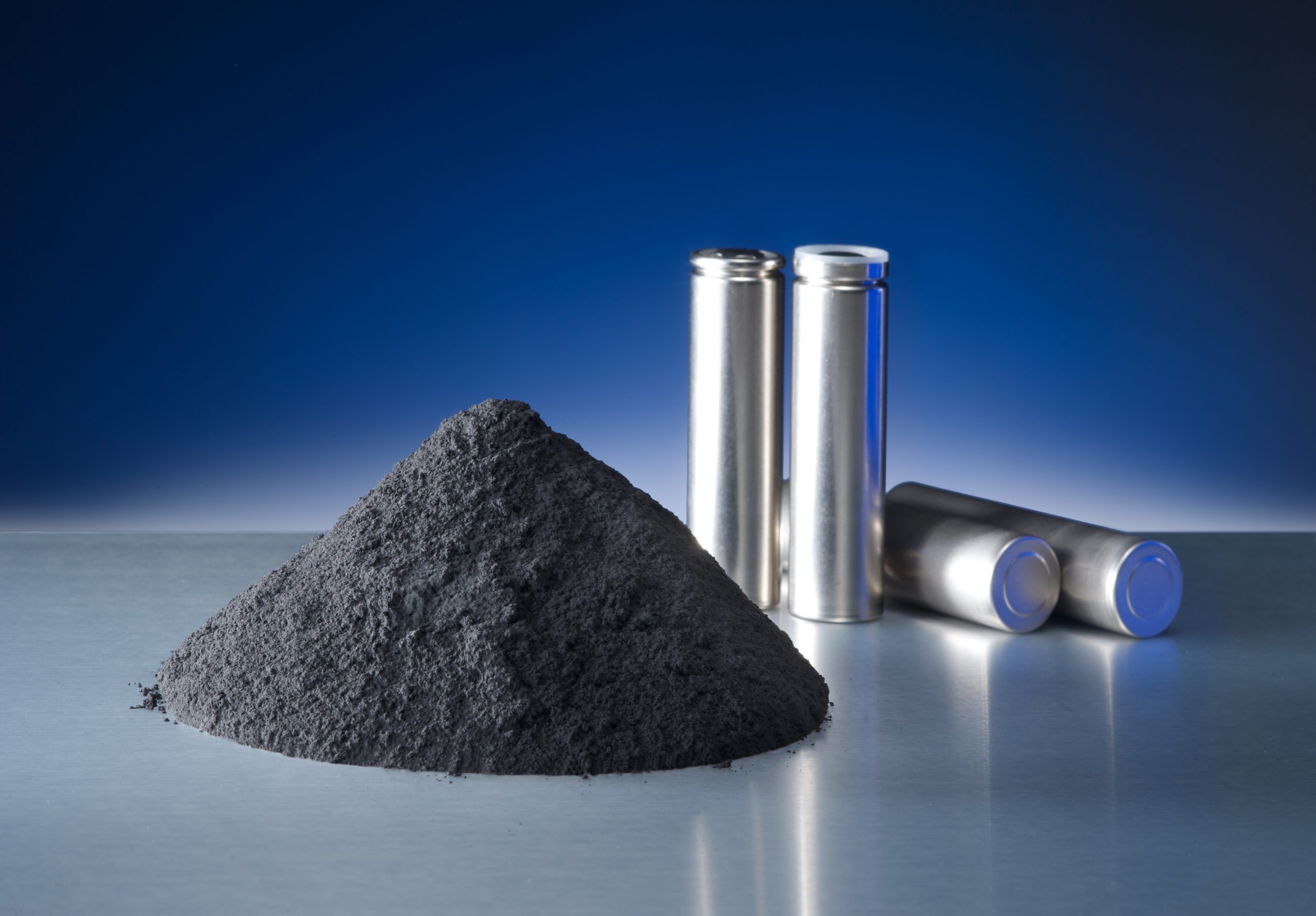
How We Manufacture Batteries: Precision in 5 Steps
Step 1: Electrorode Slurry Mixing
Cathode powder (e.g., LiFePO4) is blended with PVDF binder and carbon black in a nitrogen-filled chamber. This prevents moisture absorption, which can reduce capacity by up to 12%.
Step 2: Precision Coating
The slurry is applied to 20μm aluminum foil at 80 meters/minute. Our coating thickness tolerance is ±1μm—five times tighter than industry norms.
Step 3: Cell Assembly
For cylindrical cells like 18650s, we wind cathode/anode layers around a mandrel. Our 48V EV battery packs use stacked prismatic cells to save 18% space versus wound designs.
Step 4: Electrolyte Injection
A vacuum fills cells with electrolyte at 0.1 Pa pressure. This removes air bubbles that could cause internal resistance variations.
Step 5: Formation Cycling
Cells undergo 10 charge/discharge cycles while our AI tracks impedance changes. Cells outside the 2-5mΩ range get rejected—we scrap 0.3% of production versus the industry’s 2% average.
Why Manufacturing Quality Defines Your Battery’s Future
In 2023, 41% of lithium battery failures traced back to poor welding (Journal of Power Sources, 2024). Vade Battery eliminates this risk with:
- Laser Welding: 0.05Ω connection resistance between cells
- UL 2580 Certification: All EV batteries meet crush and short-circuit tests
- 72-Hour Simulated Aging: We replicate 5 years of use in climate chambers
A 2024 case study showed our LiFePO4 packs for solar farms retained 92% capacity after 3,000 cycles—outperforming three competing suppliers.
Battery Chemistry Comparison
Type | Energy Density (Wh/kg) | Cycle Life | Best For | Vade Example Product |
---|---|---|---|---|
18650 Li-ion | 250-300 | 500-800 | Medical devices, Power tools | 36V Power Tool Pack |
LiFePO4 | 90-160 | 3,000-5,000 | Solar storage, Industrial | 48V Telecom Backup |
Lithium Polymer | 150-200 | 300-500 | Drones, Wearables | 7.4V Drone Battery |
How We Ensure Lithium Batteries Won’t Fail
Lithium batteries demand military-grade safety protocols. At Vade Battery, every pack undergoes seven stages of testing before shipping:
1. Crush Resistance Testing
Our EV batteries withstand 150 kN of force (equivalent to a 10-ton truck) without thermal runaway—exceeding UN 38.3 requirements by 40%.
2. Short-Circuit Simulation
We intentionally short cells at 300% rated current while monitoring temperature spikes. Our LiFePO4 packs for solar storage systems limited temperature rise to 8°C in 2023 tests.
3. Thermal Shock Cycling
Packs cycle between -40°C and 85°C for 72 hours. Only 0.2% of Vade batteries showed >2% capacity loss in 2024 trials.
Why this matters: A 2024 study in Journal of Power Sources found that 68% of battery fires stem from inadequate factory testing. We test 100% of units—not just samples.
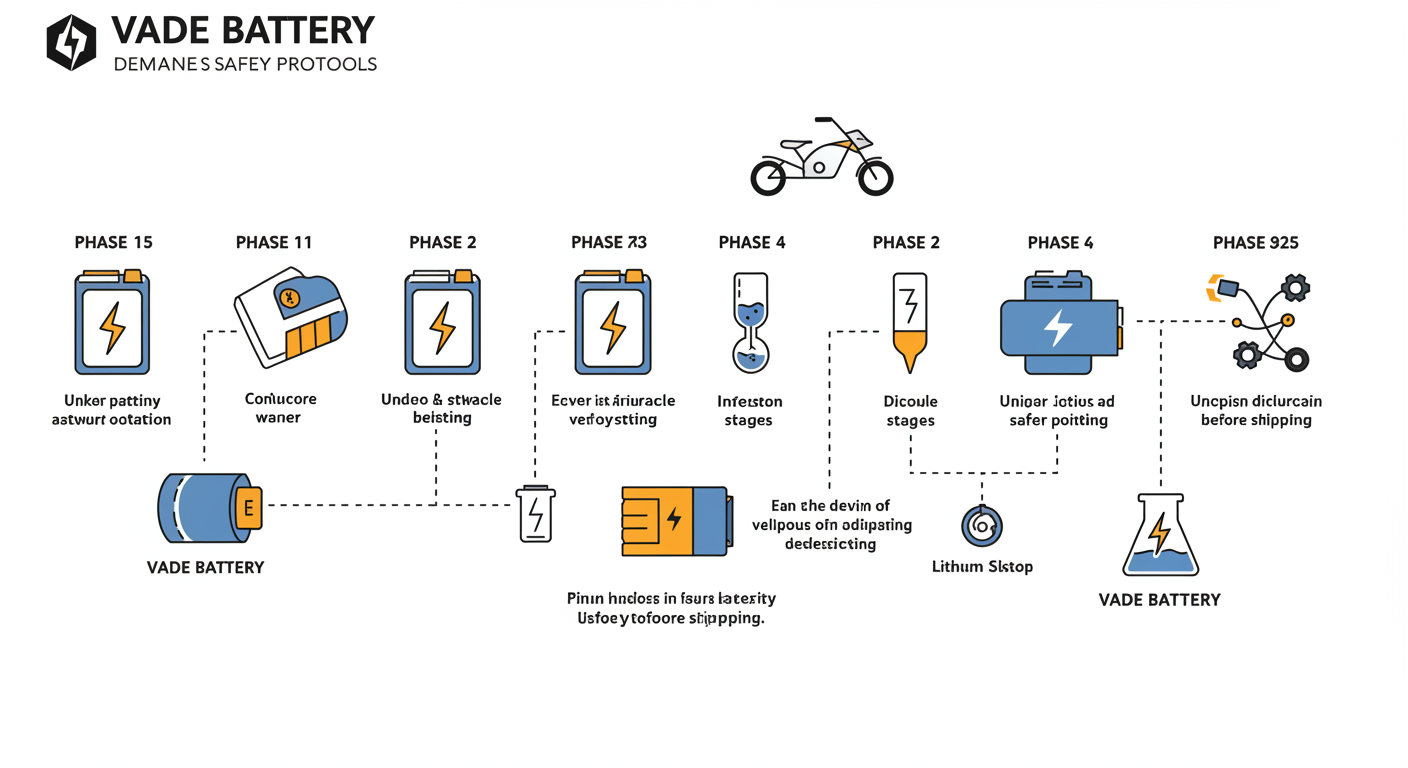
Where Our Batteries Power Innovation
Medical Devices
Our 7.4V lithium polymer batteries power portable MRI machines with:
- Zero electromagnetic interference due to shielded wiring
- 500+ cycles at 100% depth of discharge
Electric Vehicles
Vade’s 72V EV battery systems use liquid-cooled NMC cells that:
- Charge from 20% to 80% in 9 minutes
- Maintain <5°C cell temperature variance at 3C discharge
Drones & UAVs
A 2023 case study with an aerospace client showed our ultra-lightweight LiPo packs increased flight time by 22% through:
- 3-layer graphene anodes (18% higher ion absorption)
- 0.3mm nickel-foam current collectors
Closing the Loop: Battery Recycling Made Responsible
While lithium batteries last years, recycling remains critical. Vade Battery partners with R2-certified recyclers to recover:
Material | Recovery Rate | Reuse Application |
---|---|---|
Lithium | 92% | New battery cathodes |
Cobalt | 98% | Aerospace alloys |
Nickel | 95% | Stainless steel production |
Our Second Life Program repurposes used EV batteries into:
- Solar farm buffer storage (70% original capacity required)
- Emergency backup systems for telecom towers
Why Engineers Choose Vade Battery
- No Compromise Safety
- Patented pressure vents activate at 1,500 kPa
- Ceramic-coated separators prevent dendrite growth
- Customization Without Delays
- Modify cell chemistry, voltage (3.6V–72V), or housing in 3 days
- 20% faster prototyping than industry average
- Global Compliance
- Certifications: UL 2580, IEC 62133, CE, FCC
- RoHS-compliant since 2018
Can I Repair a Damaged Lithium Battery?
Never attempt repairs. Our BMS locks damaged packs automatically. Return them for professional recycling.
How Do I Store Lithium Batteries Long-Term?
Charge to 50%
Store at 15°C (we provide climate-controlled cases for industrial clients)
What’s the True Cost of Cheap Batteries?
A 2024 teardown of budget packs revealed:
61% lacked functional BMS
23% used recycled cells with <80% original capacity
Ready to Build Better Batteries?
At Vade Battery, we don’t just make lithium batteries—we engineer precision power solutions that outlast, outperform, and outthink the competition. With ISO 9001:2015-certified production and the industry’s fastest lead times, your project gets:
- 72-hour technical response guarantee
- 5-year defect-free warranty
- Free design consultation