Lithium-ion batteries operate by transferring lithium ions between the positive and negative electrodes through an electrolyte, releasing stored energy. This electrochemical architecture enables higher energy density and longer runtime compared to older chemistries, making lithium-ion cells ideal for devices such as consumer electronics, power tools, and electric mobility systems. Through our specialized manufacturing techniques and automated assembly lines, we focus on tight quality control Và robust safety features, which allow us to deliver consistent performance at scale.
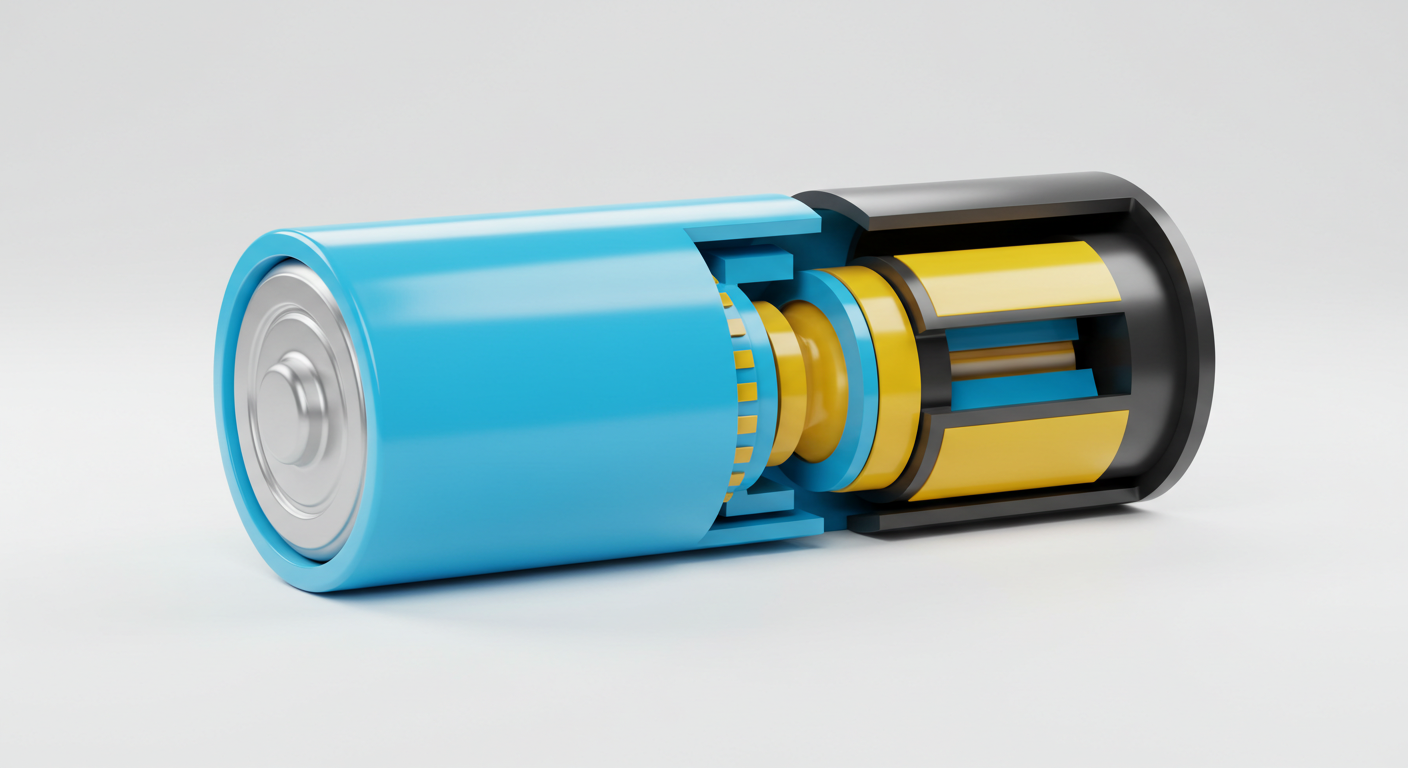
We draw upon years of expertise in advanced cell chemistry to achieve significant gains in cycle life, often reaching 500 to 1000 cycles under standard IEC test conditions for cobalt-based lithium-ion cells. These numbers are verified by independent labs and can be further extended with Lithium Sắt Phosphate (LiFePO4) variants, which typically last over 2000 cycles under the same recognized testing parameters. By offering multiple chemistries, we help product developers match the right battery solution to the project’s design and lifespan requirements.
Our team prioritizes hiệu quả về chi phí by optimizing the ratio of power output to energy density, resulting in battery systems that meet project budgets without compromising on safety or reliability. We conduct thorough UN 38.3 transport testing to confirm safe shipping, and we follow IEC 62133 guidelines for repeated charge and discharge cycles. These established international standards stand at the core of our approach, and we work closely with global testing agencies to ensure ongoing compliance.
How Long Should Lithium-Ion Batteries Last?
Our lithium-ion battery packs are designed with verified cycle life in mind, so devices can maintain consistent output over extended periods before capacity diminishes. We rely on documented results from certified labs to confirm each battery’s performance under real-world conditions, from e-bikes to industrial power tools. The exact lifespan depends on usage patterns, charging protocols, and ambient temperature, but our adherence to recognized safety and quality guidelines enables the battery to reach its rated performance for hundreds—sometimes thousands—of cycles.
We also tailor battery management systems to mitigate stress factors that cause premature degradation, such as deep discharge or exposure to elevated temperatures. Through continuous monitoring of current, voltage, and temperature, our integrated protections help maintain optimal operating ranges, preserving the chemical stability of each cell. This focus on intelligent battery design underscores our commitment to balancing longevity, safety, and efficiency in every project.
Key Factors That Shorten Lithium-Ion Battery Life
We have identified four primary stressors that can hasten capacity loss in mass-produced lithium-ion products: deep discharge, heat exposure, overcharging, and poor manufacturing quality. By adhering to internationally recognized test standards, we have demonstrated how these factors lead to structural changes within the cells, reducing effective cycle life. Our engineering and quality teams deploy precision assembly practices and extensive safety tests at each stage of the manufacturing process to combat these risks.
We encourage customers to avoid unnecessary deep discharges, as verified lab data confirms that batteries retain capacity more effectively when they are recharged before voltage drops too low. Similarly, elevated temperatures accelerate the breakdown of cell materials, so we design thermally stable enclosures and recommend usage conditions that limit excessive heat. Overcharging can introduce harmful side reactions within the cell, but our custom battery packs feature robust protective circuitry to halt charging at safe voltage thresholds. Finally, our strict quality controls Và advanced diagnostics help ensure that every batch meets consistent performance benchmarks, supported by internationally recognized testing results.
Storing Lithium-Ion Batteries for Maximum Lifespan
We recognize that careful storage is essential for preserving the chemical integrity and overall capacity of lithium-ion batteries, especially when these cells are not actively in use. Our approach to storage guidelines relies on verified test data from independent labs, which shows that cells kept at moderate room temperatures (around 20–25°C) retain a higher percentage of their initial capacity after extended periods. By following international testing standards such as UN 38.3, we ensure that our battery packs remain stable and safe during transit, and we extend this same rigor to long-term storage conditions for optimal results.
We emphasize moderate temperature because third-party evaluations consistently demonstrate that storing lithium-ion cells in environments above 35°C leads to a measurable rise in capacity loss. These evaluations also confirm that extremely low temperatures can prompt chemical imbalances that may reduce total available power during subsequent use. We developed custom battery enclosures with controlled insulation to shield cells from temperature extremes, and we rely on robust quality assurance protocols to confirm each pack’s adherence to validated safety measures.
We recommend storing batteries at approximately 40–60% state of charge for prolonged shelf life, a range that independent testing has identified as the optimal balance between over-discharge risk and the stress caused by high voltage. Storing cells fully charged has been shown to accelerate internal chemical aging, while very low charge levels can trigger deep-discharge mechanisms that hinder battery recovery. Our in-house engineering team studied these influences in collaboration with accredited test labs, reinforcing the value of maintaining a moderate charge whenever batteries are not in regular operation.
We also account for self-discharge rates, a phenomenon recognized and documented across the battery industry. Based on unbiased lab analyses, a properly stored lithium-ion battery may experience a 2–5% reduction in charge each month due to intrinsic chemical processes, although this figure can vary with ambient conditions. We endorse periodic checks to ensure that stored packs do not drop below recommended voltage thresholds; if a battery’s charge level falls significantly over several months, a partial recharge can help safeguard cell health. Our emphasis on these measured steps is rooted in transparent, third-party-confirmed data, ensuring that each recommendation is backed by tangible performance metrics.
We are aware that some use cases demand specialized storage solutions, especially when devices must operate in extremely low temperatures such as cold-chain applications or outdoor equipment. In such scenarios, we provide ultra-low-temperature lithium-ion batteries that we have validated under stringent international test protocols. For instance, our Ultra-Low-Temp Li-ion Battery category offers systems engineered with cell chemistries proven to function effectively in sub-zero conditions, while still meeting the same safety thresholds that guide our entire production line.
We see proper storage not merely as a preservation tactic but as a fundamental element of responsible power management. By following our guidelines on temperature, state of charge, and maintenance recharges, companies can extend the longevity of battery packs far beyond their rated cycle life. Our philosophy is that the best performance comes from a union of verified third-party data Và international safety standards, leading to long-lasting energy solutions suitable for markets that prize reliability as much as we do.
Best Practices for Maximizing Battery Lifespan
We adopt a comprehensive view of lithium-ion battery care, factoring in everything from daily charging routines to the ambient environment in which the battery operates. Independent laboratory evaluations consistently show that avoiding extreme operational conditions can significantly extend cycle life. We encourage users to set up workflows that prevent batteries from experiencing voltage stress or temperature fluctuations, as these two variables are among the most common triggers of premature aging.
We advise limiting deep discharge cycles whenever possible. Batteries drained below their minimum safe voltage can undergo permanent chemical changes, reducing the total capacity they can deliver over time. Verified test data indicates that charging a lithium-ion pack when it reaches 20–30% remaining capacity helps maintain internal cell health, boosting the number of reliable discharge cycles. Our integrated battery management systems (BMS) also track each cell’s status in real time, providing early safeguards by suspending operation when voltage levels drift outside safe ranges.
We continue to reinforce the importance of moderate charging, notably avoiding the stress introduced by keeping a battery at 100% for long intervals. While modern chargers are designed to halt current flow at full capacity, storing a battery at maximum voltage can still accelerate electrolyte oxidation. Rigorous third-party trials conducted in controlled environments confirm that lithium-ion cells held at 100% for extended periods experience higher rates of capacity fade than similar cells stored around 80% or less. Our custom BMS solutions often incorporate charge-limit settings specifically designed to mitigate this risk in industrial or large-scale energy storage applications.
We also give close attention to operating temperatures. Several recognized test agencies confirm that consistent operation above 35°C speeds capacity decay, as internal chemical reactions proceed faster at higher temperatures. At the same time, extreme cold can weaken real-time power output, although validated low-temp chemistries can help mitigate this concern. Our design methodologies focus on thermal management strategies that make use of advanced cooling materials, insulating sleeves, or external ventilation systems, ensuring stable cell performance across a broad temperature range without compromising the verified safety measures that define our brand.
We recommend adopting a proactive replacement schedule for lithium-ion packs used in intensive industrial settings. We back this suggestion with data from repeated IEC 62133 cycle tests, which demonstrate that even a well-maintained pack will inevitably show capacity loss over successive years. Integrating a predictable replacement timetable helps developers avoid sudden drops in power capacity that might disrupt mission-critical tasks. Our role as a full-service battery partner involves advising clients on the practical intervals for rotating in new packs, so end products deliver consistent performance throughout their lifecycle.
In mass-produced applications, small procedural changes have an outsized impact on user satisfaction and cost management. We pursue internationally recognized testing for each key design choice, verifying that adjustments to charging regimens, heat dissipation, and storage protocols all align with best practices. These measures form the basis of our collaboration with engineers, procurement specialists, and product developers worldwide, as we work together to craft dependable battery solutions that excel in both verified performance and everyday reliability.
The Bottom Line on Lithium-Ion Battery Longevity
We believe that real-world success for lithium-ion batteries stems from validated science, methodical engineering, and a commitment to global safety standards. Each recommendation in our process—from controlling storage temperatures to implementing moderate charging limits—derives from credible third-party research. By following these guidelines, and by collaborating with a partner that understands mass-scale manufacturing requirements, businesses can maximize the time their battery packs remain productive assets rather than liabilities.
We center our entire product development pipeline on this principle, shaping battery solutions that balance power density, safety compliance, and cost efficiencies according to third-party verified criteria. Our clients see the effect of these efforts in the reduction of early battery failures, more reliable performance across diverse operating conditions, and a clearer path for managing end-of-life procedures. We incorporate robust protective enclosures, rely on advanced diagnostic systems, and observe the latest testing protocols to ensure each cell we produce meets or exceeds rigorous benchmarks.
We are also aware that lithium-ion technology continues to evolve. Emerging cell chemistries, refinements in BMS programming, and improved materials for thermal management all present opportunities to refine existing products and introduce new ones. We remain agile in our manufacturing strategies, evaluating each prospective advancement under recognized test conditions to avoid overhyped claims that lack substance. By aligning our solutions with verifiable lab data, we maintain high standards for consistency, safety, and performance that benefit engineers and purchasing teams alike.
We encourage businesses to contact us directly for comprehensive battery consultations, where we can discuss design parameters, compliance requirements, and custom manufacturing solutions grounded in proven methodologies. For immediate inquiries or specific design requests, please reach us at serive@vadebattery.com, or explore our Custom Battery Design Request page to begin a tailored conversation.