แบตเตอรี่ลิเธียมเป็นพลังงานสำหรับทุกอย่างตั้งแต่สมาร์ทโฟนไปจนถึงยานยนต์ไฟฟ้า ซึ่งถือเป็นเทคโนโลยีการกักเก็บพลังงานที่เปลี่ยนแปลงโลกมากที่สุดในยุคนี้ แม้จะมีข้อได้เปรียบหลายประการในด้านความหนาแน่นของพลังงานและประสิทธิภาพ แต่แบตเตอรี่ลิเธียมก็ยังมีราคาที่สูงกว่าสารเคมีแบตเตอรี่แบบดั้งเดิมอย่างมาก ที่ Vade Battery เรามีความเชี่ยวชาญในการพัฒนา โซลูชันแบตเตอรี่ลิเธียมที่กำหนดเอง ตั้งแต่ขนาดกะทัดรัด แบตเตอรี่ขนาด 7.4V สำหรับอุปกรณ์อิเล็กทรอนิกส์เพื่อการบริโภคไปจนถึงระดับอุตสาหกรรม ระบบกักเก็บพลังงาน 72Vทีมวิศวกรของเราทำงานทุกวันโดยพิจารณาปัจจัยด้านต้นทุนที่ส่งผลต่อการผลิตแบตเตอรี่ลิเธียม และพัฒนากลยุทธ์เพื่อเพิ่มประสิทธิภาพการทำงานและจัดการค่าใช้จ่าย การวิเคราะห์เชิงลึกนี้จะสำรวจปัจจัยหลักที่ส่งผลต่อต้นทุนแบตเตอรี่ลิเธียมและอธิบายความเป็นจริงของการผลิตที่อยู่เบื้องหลังราคาที่สูงเกินไป
ต้นทุนวัตถุดิบและปัจจัยห่วงโซ่อุปทาน
The fundamental building blocks of lithium batteries represent the single largest cost component in their production. According to the U.S. Department of Energy’s 2023 cost analysis, raw materials typically account for 50-70% of a lithium battery’s manufacturing cost. This significant expense stems from both the intrinsic value of the materials and the complex global supply chain required to process and deliver them to battery manufacturers.
โลหะสำคัญและพลวัตทางการตลาด
แม้ว่าแบตเตอรี่ลิเธียมเองจะตั้งชื่อตามชื่อแบตเตอรี่ แต่โดยทั่วไปแล้วจะมีปริมาณน้อยกว่า 5% ของวัสดุเซลล์ทั้งหมดตามน้ำหนัก อย่างไรก็ตาม ราคาของลิเธียมคาร์บอเนตมีความผันผวนอย่างมาก โดยราคาในตลาดผันผวนระหว่าง $15,000 ถึง $80,000 ต่อเมตริกตันในช่วงห้าปีที่ผ่านมา ตามข้อมูลของ Benchmark Mineral Intelligence ความผันผวนนี้ส่งผลกระทบโดยตรงต่อต้นทุนการผลิตของเราสำหรับทุกอย่างตั้งแต่ ซีรีย์แบตเตอรี่อุณหภูมิต่ำพิเศษ ตามมาตรฐาน ระบบแบตเตอรี่ 48V.
Even more significant are the cathode metals that determine a battery’s performance characteristics. Cobalt, a critical component in high-energy-density NMC (Nickel-Manganese-Cobalt) cathodes, routinely trades above $30,000 per metric ton. Nearly 70% of global cobalt production comes from the Democratic Republic of Congo, creating both supply chain vulnerabilities and ethical sourcing concerns. Nickel, another essential cathode component, has seen its own price volatility with spot prices periodically exceeding $20,000 per ton following supply disruptions.
สำหรับการใช้งานที่ให้ความสำคัญกับอายุการใช้งานยาวนานและความปลอดภัยมากกว่าความหนาแน่นของพลังงานสูงสุด เรามักจะใช้ LiFePO₄ (lithium iron phosphate) เคมีภัณฑ์ แม้ว่าจะช่วยลดการพึ่งพาโคบอลต์และนิกเกิล แต่กระบวนการผลิตเฉพาะทางที่จำเป็นสำหรับวัสดุแคโทด LFP ก็มีปัจจัยด้านต้นทุนของตัวเอง สารตั้งต้นฟอสเฟตต้องได้รับการควบคุมที่แม่นยำในระหว่างการสังเคราะห์เพื่อให้ได้โครงสร้างผลึกที่เหมาะสม ส่งผลให้มีค่าใช้จ่ายในการผลิตเพิ่มขึ้นแม้ว่าจะใช้โลหะพื้นฐานในปริมาณมากขึ้นก็ตาม
การพิจารณาวัสดุอิเล็กโทรไลต์และตัวแยก
Beyond the visible metals that capture most attention, the electrolyte and separator materials represent critical components with substantial cost implications. High-purity electrolyte solutions typically utilize lithium hexafluorophosphate (LiPF₆) salt in organic solvents, with manufacturing costs influenced by required purity levels exceeding 99.99% to prevent side reactions that would degrade battery performance.
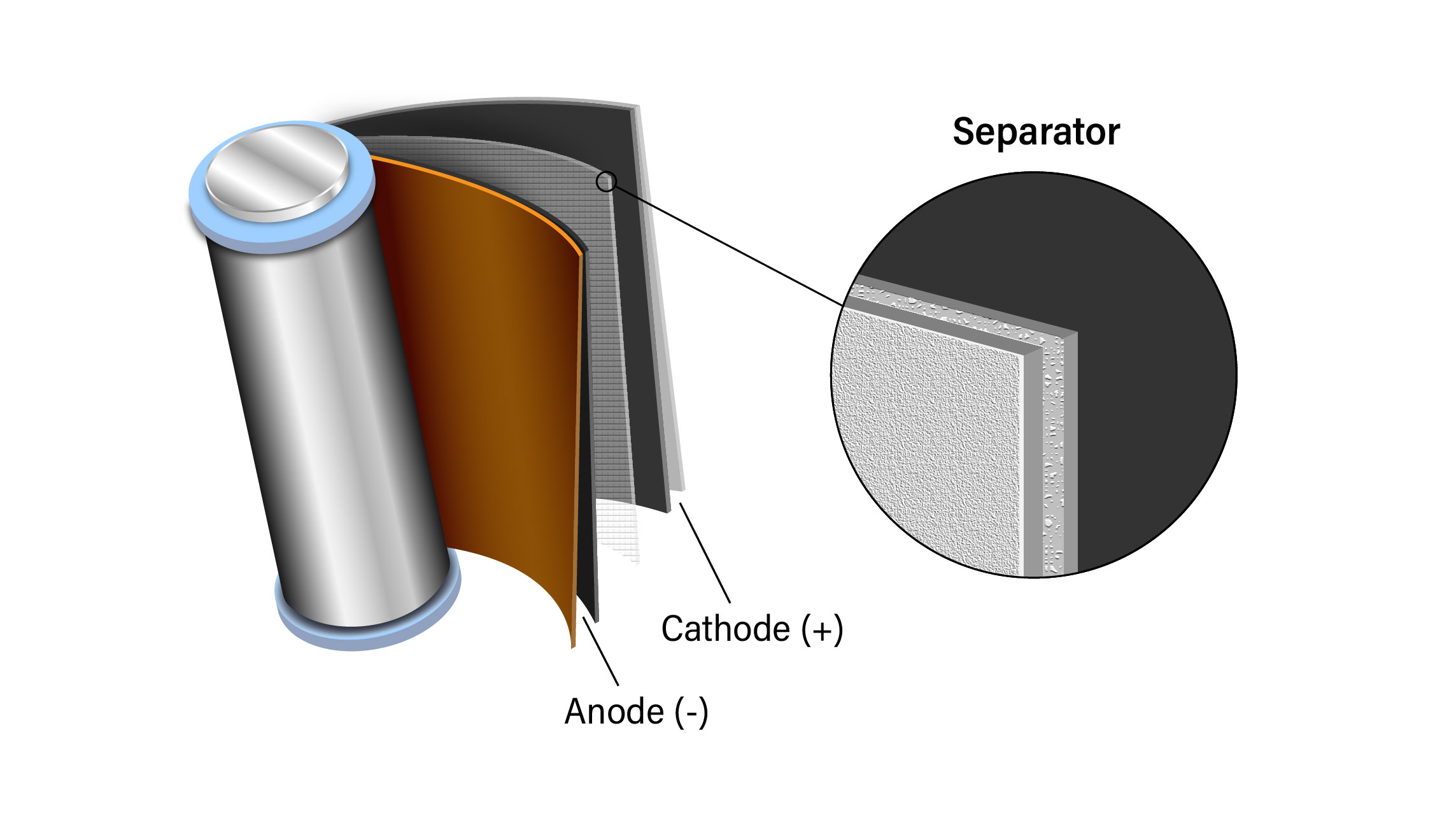
วัสดุตัวแยกซึ่งโดยทั่วไปผลิตจากฟิล์มโพลีเอทิลีนหรือโพลีโพรพีลีนที่มีรูพรุนขนาดเล็กพิเศษ จำเป็นต้องมีการควบคุมความหนาอย่างแม่นยำ (โดยทั่วไปคือ 15-25 ไมโครเมตร) และมีความพรุนสม่ำเสมอ ฟิล์มตัวแยกเหล่านี้จะต้องรักษาความสมบูรณ์ทางกลในขณะที่อนุญาตให้ลิเธียมไอออนเคลื่อนย้ายระหว่างอิเล็กโทรดได้ การผลิตตัวแยกที่มีลักษณะเหล่านี้ต้องใช้กระบวนการอัดรีดและการยืดแบบพิเศษซึ่งเพิ่มต้นทุนให้กับเซลล์ขั้นสุดท้ายอย่างมาก สำหรับเรา แบตเตอรี่ประสิทธิภาพสูง 51.8V, we utilize ceramic-coated separators that enhance thermal stability at temperatures up to 180°C but add approximately 15-20% to the material cost component.
ช่องโหว่ของห่วงโซ่อุปทานทั่วโลก
The geographically concentrated nature of battery material processing creates additional cost pressures through supply chain risk premiums. According to the International Energy Agency’s 2023 report on critical minerals, China processes approximately 60% of the world’s lithium, 70% of cobalt, and 80% of graphite used in battery anodes. This concentration creates strategic vulnerabilities for battery manufacturers outside these regions.
เราบรรเทาความเสี่ยงในห่วงโซ่อุปทานเหล่านี้ผ่านความร่วมมือเชิงกลยุทธ์กับซัพพลายเออร์วัสดุที่มีคุณสมบัติเหมาะสมหลายรายในภูมิภาคต่างๆ แม้ว่าการกระจายความเสี่ยงจะมีผลกระทบต่อต้นทุนในตัวเองก็ตาม ระบบควบคุมคุณภาพจะต้องทำซ้ำในซัพพลายเออร์ และการทดสอบคุณสมบัติสำหรับแหล่งวัสดุใหม่จะเพิ่มค่าใช้จ่ายในการวิจัยและพัฒนา ต้นทุนการขนส่งยังเป็นปัจจัยสำคัญต่อค่าใช้จ่ายด้านวัสดุ โดยมีข้อกำหนดการจัดการเฉพาะสำหรับวัสดุอิเล็กโทรดปฏิกิริยาและส่วนประกอบอิเล็กโทรไลต์ระเหยง่าย ข้อควรพิจารณาด้านลอจิสติกส์เหล่านี้มีความสำคัญเพิ่มมากขึ้นสำหรับระบบรูปแบบขนาดใหญ่ของเรา เช่น แบตเตอรี่เกรดอุตสาหกรรม 72V ที่ต้องใช้ปริมาณวัตถุดิบจำนวนมาก
กระบวนการผลิตที่ซับซ้อน
การเปลี่ยนวัตถุดิบเป็นเซลล์แบตเตอรี่ลิเธียมที่ใช้งานได้จริงนั้นต้องใช้กระบวนการผลิตที่ซับซ้อนและมีข้อกำหนดด้านความแม่นยำที่เข้มงวด เทคนิคการผลิตเฉพาะทางเหล่านี้มีส่วนสำคัญต่อต้นทุนสุดท้ายของแบตเตอรี่ลิเธียม โดยความซับซ้อนในการผลิตคิดเป็นประมาณ 20-30% ของค่าใช้จ่ายในการผลิต
ข้อกำหนดความแม่นยำในการผลิตเซลล์
Manufacturing lithium battery cells demands extraordinary precision at nearly every step of the process. Electrode coating represents one of the most critical operations, requiring uniform application of active materials onto metallic current collectors (copper for anodes, aluminum for cathodes) with thickness variations typically held below ±2 micrometers. This precision directly impacts cell capacity, internal resistance, and cycle life performance.
ของเรา แบตเตอรี่แบบเซลล์ 18650 ได้รับประโยชน์จากการปรับปรุงการผลิตเป็นเวลาหลายทศวรรษในรูปแบบทรงกระบอกนี้ แต่การผลิตยังคงต้องใช้เครื่องจักรที่ซับซ้อนสำหรับการพันอิเล็กโทรดด้วยการควบคุมแรงตึงที่สม่ำเสมอ สำหรับรูปแบบเซลล์แบบปริซึมและแบบถุงที่กำหนดเองของเราซึ่งใช้ในงานที่มีพื้นที่จำกัด ความซับซ้อนในการผลิตเพิ่มมากขึ้นเนื่องจากรูปทรงเรขาคณิตเหล่านี้ต้องการอุปกรณ์เฉพาะสำหรับการซ้อนหรือพับชุดอิเล็กโทรดที่มีการจัดตำแหน่งที่แม่นยำ
Cell finishing operations add another layer of manufacturing complexity. The electrolyte filling process must occur in extremely dry environments (typically below 100 ppm moisture) to prevent contamination that would cause performance degradation. Formation cycling—the initial charge-discharge sequences that establish the solid-electrolyte interphase (SEI) layer—requires precision control of current and voltage profiles over periods ranging from 24-72 hours, with significant energy consumption and specialized equipment needs.
ข้อกำหนดห้องสะอาดและการควบคุมคุณภาพ
แบตเตอรี่ลิเธียมต้องการสภาพแวดล้อมการผลิตที่มีมาตรฐานความสะอาดเป็นพิเศษ อนุภาคขนาดเล็กถึง 10 ไมโครเมตรสามารถสร้างไฟฟ้าลัดวงจรภายในหรือเร่งกลไกการเสื่อมสภาพภายในเซลล์ได้ พันธมิตรด้านการผลิตของเรามีห้องปลอดเชื้อมาตรฐาน ISO Class 7-8 พร้อมระบบกรองอากาศที่ซับซ้อน เสื้อผ้าคนงานเฉพาะทาง และโปรโตคอลการควบคุมการปนเปื้อนที่เข้มงวด ซึ่งเพิ่มต้นทุนการดำเนินงานที่สำคัญให้กับการผลิตแบตเตอรี่
การควบคุมคุณภาพถือเป็นค่าใช้จ่ายที่สำคัญอีกประการหนึ่งในการผลิตแบตเตอรี่ลิเธียม เซลล์แต่ละเซลล์จะต้องผ่านการตรวจสอบหลายจุด รวมถึงการตรวจสอบอิเล็กโทรดด้วยแสงอัตโนมัติ การตรวจเอกซเรย์เพื่อตรวจหาข้อบกพร่องภายใน และการวัดน้ำหนักที่แม่นยำเพื่อตรวจสอบการเติมอิเล็กโทรไลต์ สำหรับแบตเตอรี่ของเรา ระบบแบตเตอรี่ 46.8V ที่สำคัญต่อภารกิจ ที่ใช้ในทางการแพทย์ เซลล์ 100% จะต้องผ่านการคัดกรองเพิ่มเติม รวมไปถึงการตรวจติดตามแรงดันไฟฟ้าวงจรเปิดขยายเวลา เพื่อตรวจจับข้อบกพร่องในการผลิตเล็กน้อยที่อาจส่งผลกระทบต่อประสิทธิภาพการทำงาน
มาตรการควบคุมคุณภาพเหล่านี้เพิ่มต้นทุนโดยตรงผ่านอุปกรณ์และแรงงานเฉพาะทาง แต่ให้คุณค่าอย่างมากด้วยการป้องกันความล้มเหลวในภาคสนามและเพิ่มความปลอดภัย ข้อมูลภายในของเราบ่งชี้ว่ากระบวนการคัดกรองที่ครอบคลุมระบุเซลล์ประมาณ 2-5% ที่มีข้อบกพร่องเล็กน้อยซึ่งอาจนำไปสู่ความล้มเหลวก่อนกำหนดหรือประสิทธิภาพลดลง ซึ่งเป็นเหตุผลที่ต้องเพิ่มค่าใช้จ่ายในการผลิตเนื่องจากความน่าเชื่อถือที่เพิ่มขึ้น
ความท้าทายด้านระบบอัตโนมัติและขนาด
แม้ว่าระบบอัตโนมัติจะช่วยลดต้นทุนการผลิตบางส่วนได้ แต่ข้อกำหนดความแม่นยำในการผลิตแบตเตอรี่ลิเธียมยังจำกัดศักยภาพในการลดต้นทุนผ่านการใช้เครื่องจักรเพียงอย่างเดียว ระบบการจัดการอิเล็กโทรดต้องจัดการกับวัสดุที่มีความบางมากซึ่งเสียหายได้ง่ายด้วยการควบคุมแรงตึงที่สม่ำเสมอ การประกอบชิ้นส่วนต้องใช้เครื่องมือเฉพาะสำหรับงานต่างๆ เช่น การเชื่อมแบบแท็บ ซึ่งระบบการเชื่อมด้วยคลื่นอัลตราโซนิกหรือเลเซอร์จะเชื่อมแท็บตัวรวบรวมกระแสไฟฟ้าโดยวัดความคลาดเคลื่อนเป็นไมโครเมตร
ความท้าทายในการขยายขนาดการผลิตเป็นปัจจัยต้นทุนอีกประการหนึ่งในการผลิตแบตเตอรี่ลิเธียม ซึ่งต่างจากเทคโนโลยีอื่นๆ ที่การประหยัดจากขนาดจะเป็นไปตามเส้นโค้งต้นทุนที่คาดเดาได้ การผลิตแบตเตอรี่ลิเธียมต้องอาศัยการรักษาสมดุลระหว่างผลผลิตและการควบคุมคุณภาพอย่างรอบคอบ ความเร็วในการผลิตเพิ่มความเสี่ยงที่จะนำไปสู่ข้อบกพร่องเล็กๆ น้อยๆ ซึ่งอาจไม่ปรากฏให้เห็นจนกว่าเซลล์จะเข้าสู่การใช้งาน สำหรับเรา ระบบแบตเตอรี่ 24V ที่มีความน่าเชื่อถือสูง ใช้ในแอปพลิเคชันโครงสร้างพื้นฐานที่สำคัญ เราให้ความสำคัญกับกระบวนการผลิตที่เน้นความสม่ำเสมอเหนือปริมาณงานสูงสุด โดยยอมรับค่าใช้จ่ายเพิ่มเติมที่เกี่ยวข้องเพื่อให้แน่ใจถึงความน่าเชื่อถือในประสิทธิภาพ
การใช้พลังงานในระหว่างการผลิตเพิ่มค่าใช้จ่ายที่สำคัญอีกประการหนึ่ง สภาพแวดล้อมในห้องแห้งที่จำเป็นสำหรับการประกอบเซลล์โดยทั่วไปจะรักษาความชื้นสัมพัทธ์ให้ต่ำกว่า 1% ซึ่งต้องใช้ระบบลดความชื้นจำนวนมาก วงจรการก่อตัวใช้พลังงานไฟฟ้าจำนวนมาก และขั้นตอนการประมวลผลความร้อนสำหรับการทำให้อิเล็กโทรดแห้งและการกระตุ้นอิเล็กโทรไลต์ต้องควบคุมอุณหภูมิที่แม่นยำเป็นระยะเวลานาน กระบวนการที่ใช้พลังงานมากเหล่านี้ส่งผลต่อต้นทุนการผลิตในขณะเดียวกันก็ส่งผลต่อปริมาณคาร์บอนฟุตพริ้นท์ของการผลิตแบตเตอรี่ด้วย
ระบบการจัดการแบตเตอรี่และคุณลักษณะด้านความปลอดภัย
อุปกรณ์อิเล็กทรอนิกส์ที่ซับซ้อนซึ่งจำเป็นต่อการจัดการแบตเตอรี่ลิเธียมนั้นถือเป็นส่วนสำคัญของโครงสร้างต้นทุนโดยรวมของแบตเตอรี่ ซึ่งแตกต่างจากเคมีภัณฑ์แบตเตอรี่ทั่วไป เซลล์ลิเธียมจำเป็นต้องมีการตรวจสอบและควบคุมอย่างระมัดระวังเพื่อให้แน่ใจว่าจะทำงานได้อย่างปลอดภัยและมีประสิทธิภาพตลอดอายุการใช้งาน โดยทั่วไป ระบบป้องกันเหล่านี้คิดเป็น 15-25% ของต้นทุนรวมของชุดแบตเตอรี่ ทั้งนี้ขึ้นอยู่กับความซับซ้อนและฟังก์ชันการทำงาน
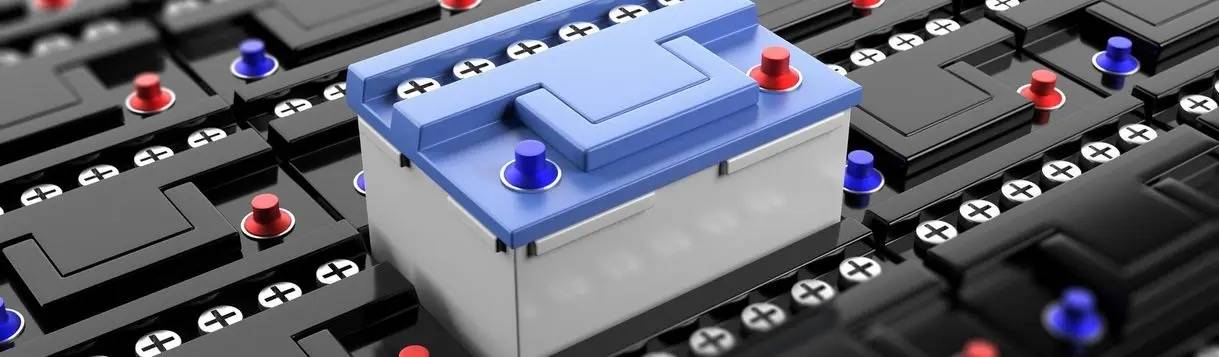
บทบาทสำคัญของ BMS ในแบตเตอรี่ลิเธียม
แบตเตอรี่ลิเธียมทุกก้อนที่เราผลิตประกอบด้วย ระบบจัดการแบตเตอรี่ (BMS) ออกแบบมาเพื่อให้เหมาะกับความต้องการใช้งานเฉพาะ ระบบควบคุมอิเล็กทรอนิกส์เหล่านี้มีหน้าที่สำคัญหลายประการ ได้แก่ ป้องกันไม่ให้เซลล์เกินขีดจำกัดแรงดันไฟฟ้าที่ปลอดภัยในระหว่างการชาร์จ การตรวจสอบอัตราการคายประจุเพื่อป้องกันสภาวะกระแสไฟเกินที่เป็นอันตราย การรักษาสมดุลระดับการชาร์จระหว่างเซลล์แต่ละเซลล์ และการติดตามอุณหภูมิที่จุดต่างๆ ภายในชุดแบตเตอรี่
สำหรับเรา เปลี่ยนแบตเตอรี่ลิเธียม 12V ใช้ในอุปกรณ์อุตสาหกรรม เราใช้การออกแบบ BMS ที่รักษาความไม่สมดุลของแรงดันไฟฟ้าเซลล์ให้ต่ำกว่า 50mV ตลอดรอบการปล่อยประจุ ทำให้ยืดอายุการใช้งานได้อย่างมากเมื่อเทียบกับระบบที่มีการป้องกันพื้นฐาน ต้นทุนการพัฒนาระบบควบคุมเฉพาะเหล่านี้รวมถึงทั้งวิศวกรรมฮาร์ดแวร์และการพัฒนาเฟิร์มแวร์อย่างละเอียด โดยมีอัลกอริทึมที่เป็นกรรมสิทธิ์ซึ่งได้รับการปรับแต่งผ่านรอบการทดสอบหลายพันรอบภายใต้เงื่อนไขการทำงานที่แตกต่างกัน
ความซับซ้อนของ BMS ขึ้นอยู่กับแรงดันไฟและความจุของแบตเตอรี่ ระบบแรงดันสูง 72V ผสานรวมชั้นการป้องกันซ้ำซ้อนพร้อมการตรวจสอบอุณหภูมิเกินที่เป็นอิสระ เซ็นเซอร์กระแสไฟหลายตัว และการตรวจสอบการแยกส่วนที่ซับซ้อนเพื่อตรวจจับการเสื่อมสภาพของฉนวนก่อนที่จะก่อให้เกิดอันตรายด้านความปลอดภัย คุณสมบัติขั้นสูงเหล่านี้ต้องการส่วนประกอบเกรดสูงกว่า รวมถึงไมโครคอนโทรลเลอร์ที่มีคุณสมบัติสำหรับยานยนต์ ตัวแปลงแอนะล็อกถึงดิจิทัลที่มีความแม่นยำ และชั้นการแยกส่วนหลายชั้นระหว่างวงจรตรวจจับและควบคุม
ข้อมูลจำเพาะและต้นทุนของวงจรป้องกัน
ส่วนประกอบการป้องกันภายในชุดแบตเตอรี่ลิเธียมจะต้องเป็นไปตามมาตรฐานความน่าเชื่อถือที่เหนือชั้นเมื่อต้องทำงานภายใต้สภาวะที่ท้าทาย ส่วนประกอบการตรวจจับกระแสจะต้องวัดกระแสได้อย่างแม่นยำตั้งแต่มิลลิแอมป์ในระหว่างสแตนด์บายไปจนถึงหลายร้อยแอมป์ในระหว่างโหลดสูงสุดในระบบพลังงานสูงของเรา การตรวจสอบอุณหภูมิต้องใช้เครือข่ายเทอร์มิสเตอร์หรือเซ็นเซอร์อุณหภูมิแบบดิจิทัลที่อยู่ในตำแหน่งที่เหมาะสมซึ่งกำหนดโดยการสร้างแบบจำลองความร้อนและตรวจสอบด้วยการถ่ายภาพอินฟราเรดระหว่างการทดสอบคุณสมบัติ
คุณสมบัติการป้องกัน | ช่วงต้นทุนส่วนประกอบโดยทั่วไป | ข้อมูลจำเพาะด้านประสิทธิภาพ |
---|---|---|
การตรวจสอบแรงดันไฟฟ้าของเซลล์ | $0.25-1.50 ต่อเซลล์ | ±10mV accuracy, 50ms sampling rate |
การตรวจจับกระแสไฟฟ้า | $3.50-20.00 ต่อแพ็ค | ±1% accuracy, response time 500V isolation, <250μA leakage |
อินเทอร์เฟซการสื่อสาร | $5.00-35.00 ต่อแพ็ค | CAN bus, Modbus หรือโปรโตคอลที่เป็นกรรมสิทธิ์ |
สำหรับแอปพลิเคชั่นที่ต้องการความทนทานต่อความผิดพลาดสูงสุด เช่น แบตเตอรี่เกรดทางการแพทย์ 36Vเราใช้ระบบตรวจสอบซ้ำซ้อนแบบคู่ที่มีการอ้างอิงแรงดันไฟฟ้าอิสระและไมโครคอนโทรลเลอร์แยกต่างหากที่ตรวจสอบการวัดแบบไขว้กัน สถาปัตยกรรมซ้ำซ้อนเหล่านี้เพิ่มต้นทุนส่วนประกอบในขณะที่เพิ่มความปลอดภัยอย่างมากสำหรับแอปพลิเคชันที่สำคัญซึ่งไม่สามารถเกิดความล้มเหลวได้
ระบบอัจฉริยะที่ฝังอยู่ในดีไซน์ BMS สมัยใหม่ขยายขอบเขตออกไปนอกเหนือจากฟังก์ชันความปลอดภัยพื้นฐานเพื่อรวมคุณสมบัติที่ช่วยเพิ่มอายุการใช้งานและประสิทธิภาพของแบตเตอรี่ อัลกอริทึมการประมาณสถานะการชาร์จขั้นสูงจะรวมการวัดแรงดันไฟฟ้าเข้ากับการนับคูลอมบ์และการติดตามอิมพีแดนซ์เพื่อให้ข้อมูลความจุที่แม่นยำตลอดรอบการคายประจุ อินเทอร์เฟซควบคุมการจัดการความร้อนจะควบคุมระบบระบายความร้อนแบบแอคทีฟในแอพพลิเคชั่นที่มีการคายประจุสูง ช่วยรักษาอายุเซลล์โดยป้องกันการเปลี่ยนแปลงอุณหภูมิในกรณีใช้งานที่ต้องการพลังงานสูง
ข้อกำหนดการทดสอบและการรับรอง
The regulatory requirements for lithium battery safety represent another significant cost driver. Every battery design we produce undergoes comprehensive certification testing according to standards including UN 38.3 for transportation safety, IEC 62133 for cell safety, and UL 1642/2054 for various applications. These testing protocols include extreme abuse conditions such as crush testing, penetration resistance, thermal cycling between -40°C and +75°C, and short-circuit evaluation.
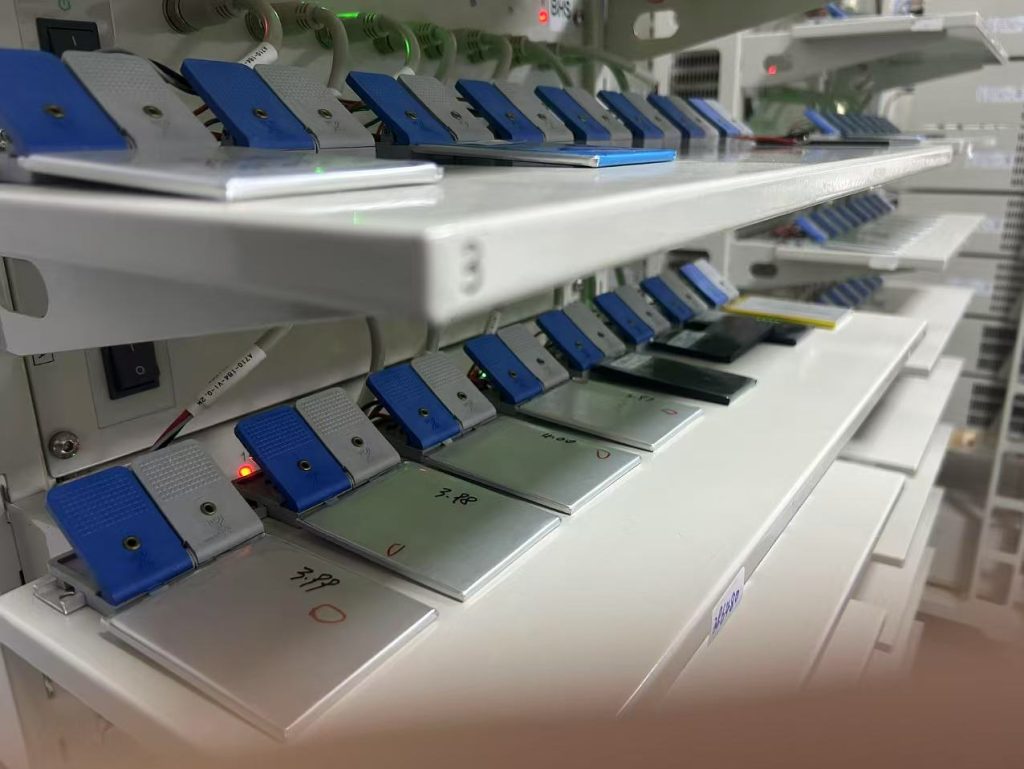
สำหรับเรา ระบบแบตเตอรี่ 48V ที่เน้นการขนส่งมาตรฐานเพิ่มเติม เช่น ECE R100 (สำหรับการใช้งานในยานยนต์) หรือ EN 50604 (สำหรับยานยนต์ไฟฟ้าขนาดเบา) อาจมีผลบังคับใช้ ซึ่งต้องมีการทดสอบเฉพาะทางเพิ่มเติม กระบวนการรับรองเหล่านี้โดยทั่วไปจะมีค่าใช้จ่ายระหว่าง $15,000-$50,000 ต่อรุ่นแบตเตอรี่ ขึ้นอยู่กับความซับซ้อนและข้อกำหนดการใช้งาน แม้ว่าค่าใช้จ่ายเหล่านี้จะถูกหักลดหย่อนตามปริมาณการผลิต แต่ก็มีส่วนช่วยอย่างมากต่อต้นทุนการพัฒนาโซลูชันแบตเตอรี่เฉพาะทาง
การทดสอบภายในครอบคลุมมากกว่าข้อกำหนดด้านกฎระเบียบเพื่อรวมถึงการตรวจสอบเฉพาะแอปพลิเคชัน สำหรับแบตเตอรี่ที่ออกแบบมาสำหรับสภาพแวดล้อมที่มีการสั่นสะเทือนสูง เราดำเนินการทดสอบแบบขยายเวลาบนเครื่องเขย่าไฟฟ้าไดนามิกที่จำลองสภาพภาคสนามที่เร่งให้อายุการใช้งานหลายปีเหลือเพียงการประเมินในห้องปฏิบัติการเป็นเวลาหลายสัปดาห์ ห้องทดสอบสภาพแวดล้อมแบบกำหนดเองจำลองอุณหภูมิที่รุนแรง การเปลี่ยนแปลงของความชื้น และการสัมผัสกับหมอกเกลือสำหรับการใช้งานในทะเล โปรแกรมทดสอบที่ครอบคลุมเหล่านี้ทำให้มีค่าใช้จ่ายในการพัฒนาเพิ่มขึ้น แต่รับประกันว่าแบตเตอรี่ของเราจะให้ประสิทธิภาพที่เชื่อถือได้ตลอดอายุการใช้งานที่ตั้งใจไว้
ค่าใช้จ่ายด้านบรรจุภัณฑ์และการบูรณาการทางกล
การแปลงเซลล์ลิเธียมแต่ละเซลล์ให้กลายเป็นระบบแบตเตอรี่ที่ใช้งานได้นั้นต้องอาศัยเทคโนโลยีบรรจุภัณฑ์ที่ซับซ้อนซึ่งช่วยปกป้องส่วนประกอบทางเคมีไฟฟ้า พร้อมทั้งให้การทำงานที่ปลอดภัยและเชื่อถือได้ในสภาพแวดล้อมที่หลากหลาย องค์ประกอบการรวมเชิงกลเหล่านี้เพิ่ม 10-15% ให้กับต้นทุนแบตเตอรี่โดยรวม แต่ให้การป้องกันและการทำงานที่จำเป็นซึ่งส่งผลโดยตรงต่อประสิทธิภาพและความปลอดภัย
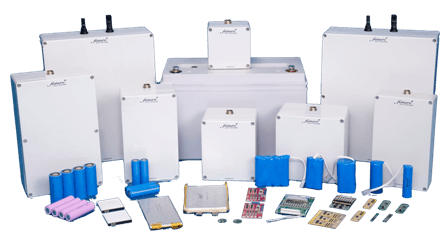
วัสดุและการผลิตของตู้หุ้ม
ตัวเรือนป้องกันสำหรับชุดแบตเตอรี่ลิเธียมจะต้องตอบสนองความต้องการที่เข้มงวดหลายประการพร้อมกัน สำหรับเรา ระบบแบตเตอรี่อุตสาหกรรม 51.2V, enclosures typically utilize aluminum alloys with wall thicknesses ranging from 1.5-3mm, providing excellent thermal conductivity, electromagnetic shielding, and mechanical protection. Computer-controlled machining processes with tolerances held to ±0.1mm ensure precise component fitment, but these manufacturing techniques add significant cost compared to simple plastic molding processes used for less demanding applications.
การใช้งานที่ต้องสัมผัสกับสิ่งแวดล้อมที่รุนแรงต้องมีมาตรการป้องกันเพิ่มเติม กล่องหุ้มที่ได้รับการจัดอันดับ IP67 undergo pressure testing to verify water and dust exclusion at depths up to 1 meter. Specialized gasket materials maintain sealing performance across temperature ranges from -40°C to +85°C while resisting degradation from ultraviolet exposure and chemical contaminants. These advanced sealing systems add component costs while requiring precise manufacturing to maintain compression forces within specified limits.
การออกแบบโครงสร้างของกล่องแบตเตอรี่จะต้องคำนึงถึงความแตกต่างของการขยายตัวเนื่องจากความร้อนระหว่างส่วนประกอบ การแยกการสั่นสะเทือน และความต้านทานแรงกระแทกที่เหมาะสมกับการใช้งาน ทีมวิศวกรรมของเราใช้การวิเคราะห์องค์ประกอบจำกัดเพื่อปรับการออกแบบเหล่านี้ให้เหมาะสม ลดการใช้วัสดุในขณะที่ยังคงความสมบูรณ์ของโครงสร้างไว้ สำหรับการใช้งานที่ไวต่อน้ำหนัก เช่น อุปกรณ์พกพาที่ใช้พลังงานจากแบตเตอรี่ของเรา แบตเตอรี่ขนาด 7.4V น้ำหนักเบาเราใช้วัสดุหุ้มแบบคอมโพสิตซึ่งช่วยลดน้ำหนักได้มากถึง 40% เมื่อเทียบกับวัสดุทางเลือกประเภทอะลูมิเนียม แม้ว่าวัสดุขั้นสูงเหล่านี้มักจะเพิ่มต้นทุนวัสดุหุ้มอีก 25-30% ก็ตาม
ระบบการจัดการความร้อน
การจัดการความร้อนอย่างมีประสิทธิภาพถือเป็นความท้าทายทางวิศวกรรมที่สำคัญที่สุดประการหนึ่งในการออกแบบแบตเตอรี่ลิเธียม ประสิทธิภาพ อายุการใช้งาน และความปลอดภัยของเซลล์ขึ้นอยู่กับการรักษาอุณหภูมิในการทำงานที่เหมาะสม โดยแต่ละเคมีภัณฑ์จะมีช่วงอุณหภูมิที่เหมาะสมเฉพาะเจาะจง สำหรับการใช้งานที่มีความต้องการพลังงานเพียงเล็กน้อย การระบายความร้อนแบบพาสซีฟผ่านระยะห่างของเซลล์ที่เหมาะสมและวัสดุที่นำความร้อนอาจเพียงพอ โดยเพิ่มต้นทุนให้กับระบบโดยรวมเพียงเล็กน้อย
อย่างไรก็ตาม การใช้งานที่มีอัตราการปล่อยประจุสูง เช่น ระบบแบตเตอรี่ขับเคลื่อน 72V ต้องใช้โซลูชันการจัดการความร้อนแบบแอคทีฟ โดยทั่วไปจะประกอบด้วยวงจรระบายความร้อนด้วยของเหลวที่มีการควบคุมการไหลที่แม่นยำ เซ็นเซอร์อุณหภูมิที่จุดต่างๆ ภายในแพ็ค และอัลกอริทึมการควบคุมที่ปรับความเข้มข้นของการระบายความร้อนโดยอิงจากทั้งสภาวะการทำงานปัจจุบันและประวัติความร้อน การเพิ่มปั๊ม ตัวแลกเปลี่ยนความร้อน เซ็นเซอร์อุณหภูมิ และอุปกรณ์อิเล็กทรอนิกส์ควบคุมสามารถเพิ่มต้นทุนรวมของแพ็คได้ 15-30% แต่ระบบเหล่านี้ช่วยให้ทำงานด้วยพลังงานสูงได้อย่างต่อเนื่องในขณะที่ป้องกันการเสื่อมสภาพจากความร้อน ซึ่งมิฉะนั้นจะทำให้แบตเตอรี่มีอายุการใช้งานสั้นลง
Even batteries without active cooling require careful thermal design. We utilize specialized gap-filling materials with thermal conductivity values between 3-8 W/m·K to transfer heat from cells to external enclosure surfaces. These thermally conductive but electrically insulating compounds add material cost and assembly complexity but substantially improve temperature uniformity across cell groups. For applications with intermittent high-discharge requirements, we incorporate วัสดุเปลี่ยนเฟส ซึ่งดูดซับความร้อนในช่วงที่มีภาระงานสูงสุด และค่อยๆ ปล่อยออกมาในช่วงพัก ส่งผลให้อุณหภูมิที่ผันผวนช้าลง ซึ่งจะเร่งให้กลไกการเสื่อมสภาพทำงานเร็วขึ้น
เทคโนโลยีการเชื่อมต่อ
การเชื่อมต่อระหว่างเซลล์แต่ละเซลล์ถือเป็นองค์ประกอบต้นทุนที่สำคัญอีกประการหนึ่งในระบบแบตเตอรี่ลิเธียม สำหรับเรา แบตเตอรี่ 36V ใช้ในเครื่องมือไฟฟ้าและการใช้งานที่คล้ายคลึงกัน เราใช้บัสบาร์นิกเกิลหรือทองแดงที่เชื่อมด้วยเลเซอร์พร้อมการควบคุมการเจาะเชื่อมอย่างแม่นยำเพื่อเชื่อมเซลล์โดยไม่ทำให้ส่วนประกอบภายในเสียหายจากความร้อน กระบวนการเชื่อมเหล่านี้ต้องใช้อุปกรณ์เฉพาะทางพร้อมการตรวจสอบกระบวนการอย่างครอบคลุมเพื่อให้แน่ใจว่ามีความต้านทานไฟฟ้าและความแข็งแรงเชิงกลที่สม่ำเสมอที่จุดเชื่อมต่อแต่ละจุด
การใช้งานกระแสไฟสูงต้องใช้ระบบเชื่อมต่อที่มีความทนทานเป็นพิเศษ แบตเตอรี่เกรดอุตสาหกรรม utilize interconnects capable of handling continuous currents exceeding 200A with temperature rise limited to 20°C above ambient. These heavy-duty connections typically use copper bus bars with cross-sectional areas determined through both electrical current capacity and mechanical strength requirements. Specialized plating processes, typically nickel or tin, protect these connections from oxidation while maintaining low contact resistance throughout the battery’s service life.
The internal wiring within battery packs represents another significant cost element. We select conductor sizes based on both continuous and peak current requirements, typically using silicone-insulated wire with temperature ratings exceeding 150°C to maintain safety margins during high-load operation. Terminal connections utilize crimped or ultrasonic welded terminations rather than soldered joints, as the latter can create weak points in high-vibration environments. These specialized connection techniques require dedicated tooling and process validation for each battery design, contributing to both development and production costs.
การขนส่งและการปฏิบัติตามกฎระเบียบ
การจำแนกแบตเตอรี่ลิเธียมเป็นสินค้าอันตรายภายใต้กฎระเบียบการขนส่งระหว่างประเทศสร้างความท้าทายด้านการขนส่งและต้นทุนที่เกี่ยวข้องที่ไม่เหมือนใคร ข้อกำหนดด้านกฎระเบียบเหล่านี้ไม่เพียงแต่ส่งผลต่อค่าใช้จ่ายในการขนส่งเท่านั้น แต่ยังส่งผลต่อการตัดสินใจด้านการออกแบบ โปรโตคอลการทดสอบ และระบบเอกสาร ซึ่งเมื่อรวมกันแล้วจะเพิ่ม 8-12% ให้กับต้นทุนแบตเตอรี่ทั้งหมด
ข้อกำหนดการทดสอบการขนส่ง UN 38.3
แบตเตอรี่ลิเธียมทั้งหมดที่จัดส่งไปต่างประเทศต้องเป็นไปตามข้อบังคับ UN 38.3 สำหรับการขนส่งสินค้าอันตราย โปรโตคอลการทดสอบที่ครอบคลุมนี้ทำให้แบตเตอรี่ต้องผ่านการทดสอบการใช้งานที่ไม่เหมาะสม 8 แบบ ได้แก่ การจำลองระดับความสูง การเปลี่ยนแปลงอุณหภูมิ การสั่นสะเทือน แรงกระแทก ไฟฟ้าลัดวงจรภายนอก การกระแทก/การบดอัด การชาร์จเกิน และการคายประจุแบบบังคับ ลำดับการทดสอบแต่ละลำดับต้องใช้ตัวอย่างแบตเตอรี่หลายตัวอย่างในสถานะการชาร์จที่แตกต่างกัน โดยมีเกณฑ์ผ่าน/ไม่ผ่านที่เข้มงวดโดยพิจารณาจากความเสียหายที่สังเกตได้ การเพิ่มขึ้นของอุณหภูมิ และพฤติกรรมของแรงดันไฟฟ้า
สำหรับเรา การออกแบบแบตเตอรี่ที่กำหนดเองการทดสอบภาคบังคับเหล่านี้โดยทั่วไปจะมีค่าใช้จ่ายระหว่าง $8,000-$15,000 ต่อรุ่น ขึ้นอยู่กับขนาดและความซับซ้อน ห้องปฏิบัติการทดสอบเฉพาะทางจะบำรุงรักษาอุปกรณ์ที่ผ่านการสอบเทียบและสภาพแวดล้อมที่ควบคุมซึ่งจำเป็นสำหรับโปรโตคอลมาตรฐานเหล่านี้ แม้ว่าค่าใช้จ่ายเหล่านี้มักจะถูกหักลดหย่อนตามปริมาณการผลิต แต่ก็ถือเป็นต้นทุนการพัฒนาที่สำคัญ โดยเฉพาะอย่างยิ่งสำหรับแบตเตอรี่เฉพาะทางที่มีปริมาณการผลิตจำกัด ทีมวิศวกรรมของเราออกแบบโดยคำนึงถึงข้อกำหนดเหล่านี้ โดยผสานรวมคุณลักษณะต่างๆ ที่ช่วยเพิ่มความทนทานภายใต้สภาวะความเครียดเฉพาะที่ประเมินในการทดสอบ UN 38.3
นอกเหนือจากการรับรองเบื้องต้นแล้ว การปฏิบัติตามกฎระเบียบเกี่ยวกับสินค้าอันตรายอย่างต่อเนื่องยังต้องมีเอกสารประกอบอย่างละเอียดสำหรับการขนส่งทุกครั้ง ระบบแบตเตอรี่ของเรามีการติดฉลากตามข้อบังคับที่ระบุความจุวัตต์ชั่วโมง หมายเลข UN และคำเตือนอันตรายที่เหมาะสม เอกสารการขนส่งจะต้องมีข้อมูลสรุปการทดสอบที่ยืนยันการปฏิบัติตาม UN 38.3 พร้อมข้อกำหนดด้านรูปแบบและเนื้อหาที่เปลี่ยนแปลงไปอย่างมีนัยสำคัญจากการปรับปรุงกฎระเบียบเกี่ยวกับสินค้าอันตรายของ IATA ในปี 2020 การบำรุงรักษาระบบเอกสารประกอบเหล่านี้จะเพิ่มภาระงานด้านการบริหารให้กับการขนส่งแบตเตอรี่ทุกครั้ง
ข้อจำกัดและทางเลือกในการขนส่งทางอากาศ
ความท้าทายที่สำคัญที่สุดในการขนส่งแบตเตอรี่ลิเธียมเกี่ยวข้องกับข้อจำกัดในการขนส่งทางอากาศ กฎระเบียบ IATA ในปัจจุบันห้ามขนส่งแบตเตอรี่ลิเธียมเป็นสินค้าบรรทุกบนเครื่องบินโดยสาร ยกเว้นเมื่อติดตั้งหรือบรรจุร่วมกับอุปกรณ์ และแม้แต่เครื่องบินขนส่งสินค้าก็มีข้อจำกัดที่เข้มงวดเกี่ยวกับขนาดแบตเตอรี่และข้อกำหนดด้านบรรจุภัณฑ์ ข้อจำกัดเหล่านี้สร้างความท้าทายด้านการขนส่งสำหรับการกระจายสินค้าระหว่างประเทศ โดยเฉพาะอย่างยิ่งสำหรับ ระบบแบตเตอรี่ความจุสูงขึ้น เกิน 100 วัตต์-ชั่วโมง
วิธีการจัดส่งทางเลือก เช่น การขนส่งทางทะเล จะทำให้ระยะเวลาในการขนส่งนานขึ้น โดยปกติจะใช้เวลา 3-5 สัปดาห์สำหรับการขนส่งระหว่างประเทศเมื่อเทียบกับการขนส่งทางอากาศ ระยะเวลาที่ขยายออกไปนี้ทำให้ต้องใช้เงินทุนหมุนเวียนเพิ่มขึ้น เนื่องจากสินค้าคงคลังต้องใช้เวลาในการขนส่งนานขึ้น ตู้คอนเทนเนอร์ที่ควบคุมอุณหภูมิอาจมีความจำเป็นเพื่อป้องกันอุณหภูมิที่เปลี่ยนแปลงอย่างสุดขั้วระหว่างการขนส่งทางทะเล ซึ่งจะทำให้ต้นทุนค่าขนส่งเพิ่มขึ้นจนเกิน $2,000 ต่อตู้คอนเทนเนอร์สำหรับเส้นทางข้ามมหาสมุทร
ทีมโลจิสติกส์ของเรารับมือกับความท้าทายเหล่านี้โดยการนำสินค้าคงคลังระดับภูมิภาคเชิงกลยุทธ์มาใช้กับรุ่นแบตเตอรี่ที่ใช้กันทั่วไป ซึ่งช่วยให้ตอบสนองต่อความต้องการของลูกค้าได้เร็วขึ้นในขณะที่ปฏิบัติตามข้อบังคับการขนส่ง สำหรับการออกแบบแบตเตอรี่แบบกำหนดเอง เราทำงานร่วมกับลูกค้าตั้งแต่เริ่มต้นกระบวนการพัฒนาเพื่อกำหนดระยะเวลาที่คาดหวังได้อย่างสมจริงซึ่งคำนึงถึงความซับซ้อนในการขนส่งที่จำเป็น การพิจารณาด้านโลจิสติกส์เหล่านี้เพิ่มต้นทุนทางอ้อมซึ่งส่งผลต่อราคาแบตเตอรี่ลิเธียมในที่สุดเมื่อเทียบกับทางเลือกอื่นที่มีการควบคุมน้อยกว่า
ข้อจำกัดด้านสถานะการชาร์จ
กฎระเบียบที่ควบคุมการขนส่งแบตเตอรี่ลิเธียมรวมถึงข้อจำกัดเฉพาะเกี่ยวกับสถานะการชาร์จ (SoC) ที่มุ่งหวังที่จะลดความเสี่ยงระหว่างการขนส่ง ข้อกำหนดปัจจุบันระบุสถานะการชาร์จสูงสุดที่ 30% สำหรับเซลล์ลิเธียมไอออนและแบตเตอรี่ที่จัดส่งแยกกัน (ไม่รวมอยู่ในอุปกรณ์) ข้อกำหนดนี้สร้างขั้นตอนการประมวลผลเพิ่มเติมในเวิร์กโฟลว์การผลิตของเรา เนื่องจากแบตเตอรี่แต่ละก้อนต้องผ่านขั้นตอนการคายประจุที่ควบคุมได้เพื่อให้ถึงสถานะที่เหมาะสมสำหรับการขนส่ง
สำหรับเรา แบตเตอรี่ความจุสูง 51.8Vกระบวนการปล่อยประจุนี้อาจใช้เวลา 4-6 ชั่วโมงต่อแพ็คบนอุปกรณ์เฉพาะทางที่ควบคุมอัตราการปล่อยประจุอย่างแม่นยำพร้อมทั้งตรวจสอบแรงดันไฟฟ้าของเซลล์แต่ละเซลล์ พลังงานที่ปล่อยประจุถือเป็นการสูญเสียจากการผลิต เนื่องจากผู้ใช้ปลายทางจะต้องชาร์จแบตเตอรี่ใหม่ในภายหลังก่อนใช้งานครั้งแรก เราปรับกระบวนการนี้ให้เหมาะสมโดยกู้คืนพลังงานระหว่างรอบการปล่อยประจุผ่านธนาคารโหลดแบบฟื้นฟู ช่วยลดการสูญเสียพลังงานและการสร้างความร้อนระหว่างการผลิต
แม้ว่าข้อกำหนดด้านกฎระเบียบเหล่านี้จะเพิ่มความซับซ้อนและต้นทุนให้กับการขนส่งแบตเตอรี่ลิเธียม แต่ก็สะท้อนถึงข้อควรพิจารณาด้านความปลอดภัยที่ถูกต้องตามกฎหมายที่เกี่ยวข้องกับแหล่งพลังงานที่มีความหนาแน่นของพลังงานสูงเหล่านี้ โปรแกรมการปฏิบัติตามข้อกำหนดที่ครอบคลุมของเราช่วยให้มั่นใจได้ว่าแบตเตอรี่ทั้งหมดจะถึงมือลูกค้าอย่างปลอดภัยในขณะที่ยังคงปฏิบัติตามข้อกำหนดด้านกฎระเบียบอย่างครบถ้วน ช่วยปกป้องทั้งความปลอดภัยของมนุษย์และสิ่งแวดล้อมตลอดห่วงโซ่อุปทาน
การวิจัย พัฒนา และการปรับปรุงอย่างต่อเนื่อง
ภูมิทัศน์ของเทคโนโลยีแบตเตอรี่ลิเธียมที่เปลี่ยนแปลงอย่างรวดเร็วเป็นแรงผลักดันให้เกิดการลงทุนอย่างต่อเนื่องในด้านการวิจัยและพัฒนา ค่าใช้จ่ายด้านการวิจัยและพัฒนาเหล่านี้มีส่วนสนับสนุนต้นทุนแบตเตอรี่โดยรวมประมาณ 5-10% แต่ช่วยให้สามารถปรับปรุงประสิทธิภาพได้อย่างต่อเนื่อง ซึ่งทำให้แบตเตอรี่ลิเธียมมีมูลค่าเพิ่มมากขึ้นแม้จะมีราคาสูงก็ตาม
การเพิ่มประสิทธิภาพทางเคมีและวิทยาศาสตร์วัสดุ
ในระดับเซลล์ การวิจัยอย่างต่อเนื่องมุ่งเน้นไปที่การปรับปรุงเพิ่มเติมในด้านความหนาแน่นของพลังงาน อายุการใช้งาน ความสามารถในการชาร์จเร็ว และประสิทธิภาพอุณหภูมิ ทีมวิศวกรรมของเราทำงานร่วมกับผู้ผลิตเซลล์เพื่อประเมินเทคโนโลยีวัสดุใหม่ๆ เช่น ขั้วบวกที่เสริมด้วยซิลิกอนซึ่งสามารถเพิ่มความจุได้ถึง 20-40% เมื่อเปรียบเทียบกับสูตรกราไฟต์แบบดั้งเดิม วัสดุขั้นสูงเหล่านี้มักมีราคาสูงในช่วงเริ่มต้นการผลิตเชิงพาณิชย์ โดยต้นทุนจะลดลงเรื่อยๆ เมื่อการผลิตขยายขนาด
สำหรับการใช้งานที่ให้ความสำคัญกับประสิทธิภาพการทำงานที่อุณหภูมิสูงสุด เช่น ระบบแบตเตอรี่อุณหภูมิต่ำพิเศษ, specialized electrolyte formulations incorporate carefully balanced additive packages that maintain ion mobility at temperatures as low as -40°C. These custom electrolyte blends undergo extensive testing to verify low-temperature performance while ensuring compatibility with other cell components over the intended service life. The development and validation of these specialized formulations represent significant investments that influence product costs but deliver exceptional performance in challenging environments.
การปรับปรุงความปลอดภัยผ่านวิทยาศาสตร์วัสดุถือเป็นอีกสาขาการวิจัยที่ดำเนินการอยู่ วัสดุแยกที่มีการเคลือบเซรามิกหรือคุณสมบัติการปิดระบบเนื่องจากความร้อนในตัวทำให้ต้นทุนส่วนประกอบเพิ่มขึ้น แต่ปรับปรุงความปลอดภัยในระดับเซลล์ได้อย่างมากโดยให้การป้องกันเพิ่มเติมจากไฟฟ้าลัดวงจรภายใน ระบบแบตเตอรี่ความปลอดภัยสูง สำหรับการใช้งานทางการแพทย์ให้ใช้ตัวคั่นคุณภาพพรีเมียมเหล่านี้ แม้ว่าจะมีต้นทุนสูงกว่าวัสดุมาตรฐานถึง 30-40% ก็ตาม เนื่องจากความปลอดภัยที่เพิ่มขึ้นนั้นคุ้มค่ากับค่าใช้จ่ายเพิ่มเติมสำหรับการใช้งานที่สำคัญ
นวัตกรรมกระบวนการผลิต
การปรับปรุงเทคนิคการผลิตอย่างต่อเนื่องช่วยขับเคลื่อนทั้งการปรับปรุงคุณภาพและการลดต้นทุนของแบตเตอรี่ลิเธียมอย่างค่อยเป็นค่อยไป พันธมิตรด้านการผลิตของเราใช้เทคโนโลยีต่างๆ เช่น การตัดด้วยเลเซอร์สำหรับวัสดุอิเล็กโทรด ซึ่งช่วยลดความแปรผันของขนาดและขจัดความเสี่ยงจากการปนเปื้อนที่เกี่ยวข้องกับเครื่องมือตัดเชิงกล ระบบตรวจสอบด้วยแสงอัตโนมัติพร้อมอัลกอริทึมการเรียนรู้ของเครื่องจักรจะตรวจจับข้อบกพร่องเล็กน้อยที่อาจหลุดรอดการสังเกตของมนุษย์ ทำให้มั่นใจได้ถึงคุณภาพที่สม่ำเสมอและลดต้นทุนแรงงาน
การประกอบชิ้นส่วนอัตโนมัติยังคงก้าวหน้าต่อไป โดยหุ่นยนต์เฉพาะทางจะจัดการกับงานที่ละเอียดอ่อนมากขึ้นซึ่งก่อนหน้านี้จำกัดอยู่เพียงการประมวลผลด้วยมือ นวัตกรรมการผลิตเหล่านี้ต้องใช้การลงทุนด้านทุนจำนวนมาก แต่สามารถลดต้นทุนการผลิตลงได้ทีละน้อยด้วยผลผลิตที่เพิ่มขึ้น ความต้องการแรงงานที่ลดลง และความสม่ำเสมอที่เพิ่มขึ้น สำหรับรูปแบบเซลล์ที่เป็นที่ยอมรับ เช่น เซลล์ทรงกระบอก 18650 ที่ใช้ในระบบแบตเตอรี่จำนวนมากของเรา อุปกรณ์การผลิตได้พัฒนามาหลายชั่วอายุคน โดยแต่ละชั่วอายุคนให้การปรับปรุงประสิทธิภาพด้านต้นทุนอย่างค่อยเป็นค่อยไป
การปรับปรุงประสิทธิภาพการใช้พลังงานในกระบวนการผลิตถือเป็นอีกประเด็นสำคัญหนึ่ง การดำเนินการอบแห้งด้วยอิเล็กโทรดโดยทั่วไปจะใช้พลังงานจำนวนมาก แต่เทคโนโลยีขั้นสูง เช่น การอบแห้งด้วยไมโครเวฟช่วยลดการใช้พลังงานได้ถึง 30-50% พร้อมทั้งปรับปรุงคุณภาพการเคลือบ ความต้องการพลังงานในการหมุนเวียนของกระบวนการขึ้นรูปลดลงด้วยโปรโตคอลการชาร์จที่เหมาะสมที่สุดซึ่งให้ผลลัพธ์ทางเคมีไฟฟ้าเหมือนกันโดยลดปริมาณการใช้พลังงาน การปรับปรุงกระบวนการเหล่านี้ช่วยลดต้นทุนการผลิตลงทีละน้อยพร้อมทั้งปรับปรุงผลกระทบต่อสิ่งแวดล้อมของการผลิตแบตเตอรี่ด้วย
วิวัฒนาการระบบการจัดการแบตเตอรี่
ระบบอิเล็กทรอนิกส์ที่ควบคุมแบตเตอรี่ลิเธียมได้รับการพัฒนาอย่างต่อเนื่องเพื่อเพิ่มประสิทธิภาพการทำงานพร้อมลดต้นทุนส่วนประกอบต่างๆ การออกแบบ BMS ในยุคแรกใช้ส่วนประกอบแยกส่วนสำหรับการตรวจสอบแรงดันไฟฟ้าและฟังก์ชันการป้องกัน ในขณะที่ระบบปัจจุบันผสานรวมฟังก์ชันเหล่านี้เข้ากับไอซีเฉพาะทางที่ลดทั้งจำนวนส่วนประกอบและพื้นที่บอร์ดที่ต้องการ โซลูชันที่ผสานรวมเหล่านี้ช่วยเพิ่มความน่าเชื่อถือด้วยจุดเชื่อมต่อที่ลดลงพร้อมลดต้นทุนการผลิตด้วยการประกอบที่ง่ายขึ้น
ของเรา การออกแบบ BMS รุ่นล่าสุด ใช้ขั้นตอนขั้นสูงที่ปรับให้เข้ากับลักษณะการเสื่อมสภาพของแบตเตอรี่ โดยรักษาประสิทธิภาพการทำงานให้เหมาะสมตลอดอายุการใช้งาน แนวทางการเรียนรู้ของเครื่องจะวิเคราะห์รูปแบบการใช้งานเพื่อปรับโปรไฟล์การชาร์จให้เหมาะสมสำหรับการใช้งานเฉพาะ ซึ่งอาจขยายอายุการใช้งานของวงจรได้ถึง 15-25% เมื่อเปรียบเทียบกับระบบการจัดการพารามิเตอร์คงที่ การปรับปรุงซอฟต์แวร์เหล่านี้ทำให้ต้นทุนการพัฒนาเพิ่มขึ้น แต่ให้คุณค่าอย่างมากผ่านอายุการใช้งานและประสิทธิภาพของแบตเตอรี่ที่เพิ่มขึ้น
คุณสมบัติการเชื่อมต่อแบบไร้สายปรากฏขึ้นในระบบแบตเตอรี่สมัยใหม่มากขึ้น ช่วยให้สามารถตรวจสอบจากระยะไกล วินิจฉัย และแม้แต่อัปเดตเฟิร์มแวร์ให้กับแบตเตอรี่ที่ใช้งาน แม้ว่าคุณสมบัติเหล่านี้จะเพิ่มต้นทุนส่วนประกอบผ่านการเพิ่มบลูทูธ WiFi หรือโมดูลการสื่อสารแบบเซลลูลาร์ แต่คุณสมบัติเหล่านี้ยังสร้างมูลค่าด้วยการเปิดใช้งานการบำรุงรักษาเชิงป้องกันและเพิ่มประสิทธิภาพการทำงานตลอดอายุการใช้งานแบตเตอรี่ สำหรับลูกค้าเชิงพาณิชย์ของเราที่ใช้แบตเตอรี่จำนวนมาก คุณสมบัติแบตเตอรี่ที่เชื่อมต่อได้เหล่านี้มอบประโยชน์ด้านการดำเนินงานที่สำคัญซึ่งคุ้มค่ากับต้นทุนเพิ่มเติม
บทสรุป: คุณค่าที่เปลี่ยนแปลงไปของแบตเตอรี่ลิเธียม
The higher costs associated with lithium battery technology reflect the advanced materials, complex manufacturing processes, sophisticated control systems, and regulatory compliance requirements necessary to deliver their exceptional performance. As we’ve explored, each component of the lithium battery value chain involves specialized technologies and precision engineering that contribute to overall production expenses. However, the continuing evolution of this technology gradually improves the value proposition through both performance enhancements and incremental cost reductions.
For applications ranging from portable electronics to electric vehicles and stationary energy storage, lithium batteries deliver capabilities that simply aren’t achievable with alternative technologies. Their combination of high energy density, excellent cycle life, minimal maintenance requirements, and declining cost trajectory makes them increasingly competitive despite their premium initial price point. At Vade Battery, we focus on optimizing each aspect of battery design and production to deliver maximum value for specific application requirements, balancing performance, safety, longevity, and cost considerations.
ตลาดแบตเตอรี่ลิเธียมยังคงพัฒนาอย่างรวดเร็ว โดยมีความก้าวหน้าทางการวิจัยที่ก้าวหน้าอย่างต่อเนื่องในด้านประสิทธิภาพการทำงาน ในขณะที่ขนาดการผลิตก็ช่วยลดต้นทุนการผลิตลงได้อย่างต่อเนื่อง องค์กรต่างๆ ที่กำลังประเมินโซลูชันการจัดเก็บพลังงานควรพิจารณาทั้งต้นทุนการจัดหาในเบื้องต้นและมูลค่าในระยะยาว รวมถึงปัจจัยต่างๆ เช่น อายุการใช้งาน ความต้องการในการบำรุงรักษา ประสิทธิภาพการใช้พลังงาน และประโยชน์ในการดำเนินงานของฟีเจอร์ขั้นสูง ทีมวิศวกรรมของเรามีความเชี่ยวชาญในการนำทางการพิจารณาที่ซับซ้อนเหล่านี้เพื่อพัฒนาโซลูชันแบตเตอรี่ที่เหมาะสมที่สุดสำหรับข้อกำหนดการใช้งานเฉพาะ
สำหรับองค์กรที่กำลังสำรวจโซลูชันแบตเตอรี่ลิเธียมแบบกำหนดเอง เราขอเชิญคุณ ติดต่อทีมงานวิศวกรของเรา หรือส่งข้อกำหนดเฉพาะผ่านของเรา พอร์ทัลคำขอออกแบบแบตเตอรี่ลิเธียมผู้เชี่ยวชาญด้านเทคนิคของเราสามารถให้คำแนะนำโดยละเอียดตามข้อกำหนดแอปพลิเคชันของคุณ ช่วยให้คุณสามารถพิจารณาทางเลือกระหว่างประสิทธิภาพและต้นทุนเพื่อพัฒนาโซลูชันการจัดเก็บพลังงานที่เหมาะสมที่สุด