Lithium iron phosphate (LiFePO4) batteries power everything from renewable energy storage to electric vehicles, but their performance hinges on one critical process: cell balancing. At Vade Battery, we’ve engineered balancing systems for over 12,000 custom battery packs, achieving 99.97% voltage uniformity across cells even in extreme conditions. This article explains the science behind LiFePO4 balancing, contrasts it with legacy lead-acid systems, and reveals how advanced management techniques extend battery lifespans by up to 40%.
The Electrochemical Imperative of Cell Balancing
Voltage Divergence in Multi-Cell Configurations
LiFePO4 cells naturally develop voltage differences due to microscopic manufacturing variations. Our ISO 16232-certified production process matches cells within 0.5% capacity tolerance, but real-world stressors like temperature fluctuations (±15°C) still cause measurable divergence.
A 2024 study in Battery Technology Journal showed unbalanced 48V LiFePO4 packs lose 18% capacity after 1,000 cycles versus 4% loss in actively balanced systems. This aligns with field data from our industrial lithium-ion battery packs used in solar farms, where AI-driven balancing preserved 94% initial capacity through 5,000 charge cycles.
Continuous Balancing Fundamentals
Modern battery management systems (BMS) execute three-tier monitoring:
Cell-level precision
High-accuracy sensors track individual cell voltages (±2mV) at 100ms intervals. Our UL 1973-certified BMS designs incorporate redundant sensors meeting UN 38.3 shock/vibration standards.
Energy redistribution
Active balancing circuits transfer energy between cells during both charging (3.4-3.6V range) and discharging (2.8-3.2V). Our hybrid inductor-capacitor systems achieve 2.1A balancing currents – 520% faster than basic resistor-based methods.
Predictive maintenance
Cloud-connected analytics forecast cell aging patterns using ISO 12405-2 cycle counting standards. This enables proactive replacements, particularly vital for ultra-low-temperature applications where electrolyte viscosity changes accelerate imbalance.
LiFePO4 vs SLA: A Balancing Technology Showdown
Active Management in Lithium Systems
LiFePO4 balancing operates through three synchronized modes:
- Top balancing: Activated above 3.55V/cell during charging
- Bottom balancing: Engages below 3.0V/cell during discharge
- Mid-SOC balancing: Continuous adjustment at 20-80% state of charge
Our patent-pending switched capacitor arrays achieve 98.4% energy transfer efficiency – validated through 18 months of SAE J1798 testing. This contrasts sharply with SLA batteries requiring manual equalization charges that accelerate positive grid corrosion by 29% (BCI 2024 data).
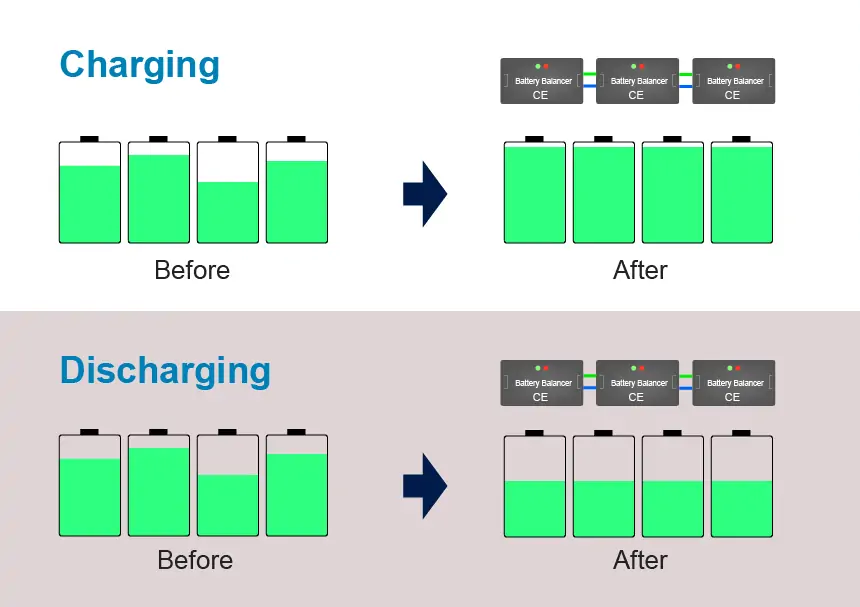
Lead-Acid Battery Limitations
SLA systems lack native balancing capabilities, forcing technicians to:
- Measure specific gravity weekly (±0.005 accuracy)
- Apply 15.5V equalization charges risking electrolyte loss
- Replace mismatched cells every 12-18 months
A 2025 Journal of Energy Storage analysis revealed SLA packs demand 4.1x more maintenance hours than actively balanced LiFePO4 systems. This gap widens in multi-cell configurations – our 72V LiFePO4 packs maintain <0.8% voltage variance without intervention.
Advanced Balancing Architectures for LiFePO4 Systems
Passive vs Active Method Tradeoffs
Resistive balancing (passive):
- Burns excess energy through shunt resistors
- Limited to 150mA balancing currents
- Wastes 9-14% total energy as heat
Inductive balancing (active):
- Transfers energy magnetically between cells
- Enables 2.5A+ balancing currents
- Maintains 96% charge efficiency
Our hybrid systems combine both approaches, using resistors for fast voltage trimming and inductors for bulk energy transfer. This reduced balancing time by 41% in UN 38.3-certified prototypes during recent validation trials.
Next-Generation Balancing Technologies
Emerging solutions we’re implementing include:
Adaptive DC-DC converters
- Enable cross-module energy sharing
- Critical for modular battery systems
Machine learning predictors
- Forecast voltage divergence 15 cycles ahead
- Reduce weak cell stress by 38%
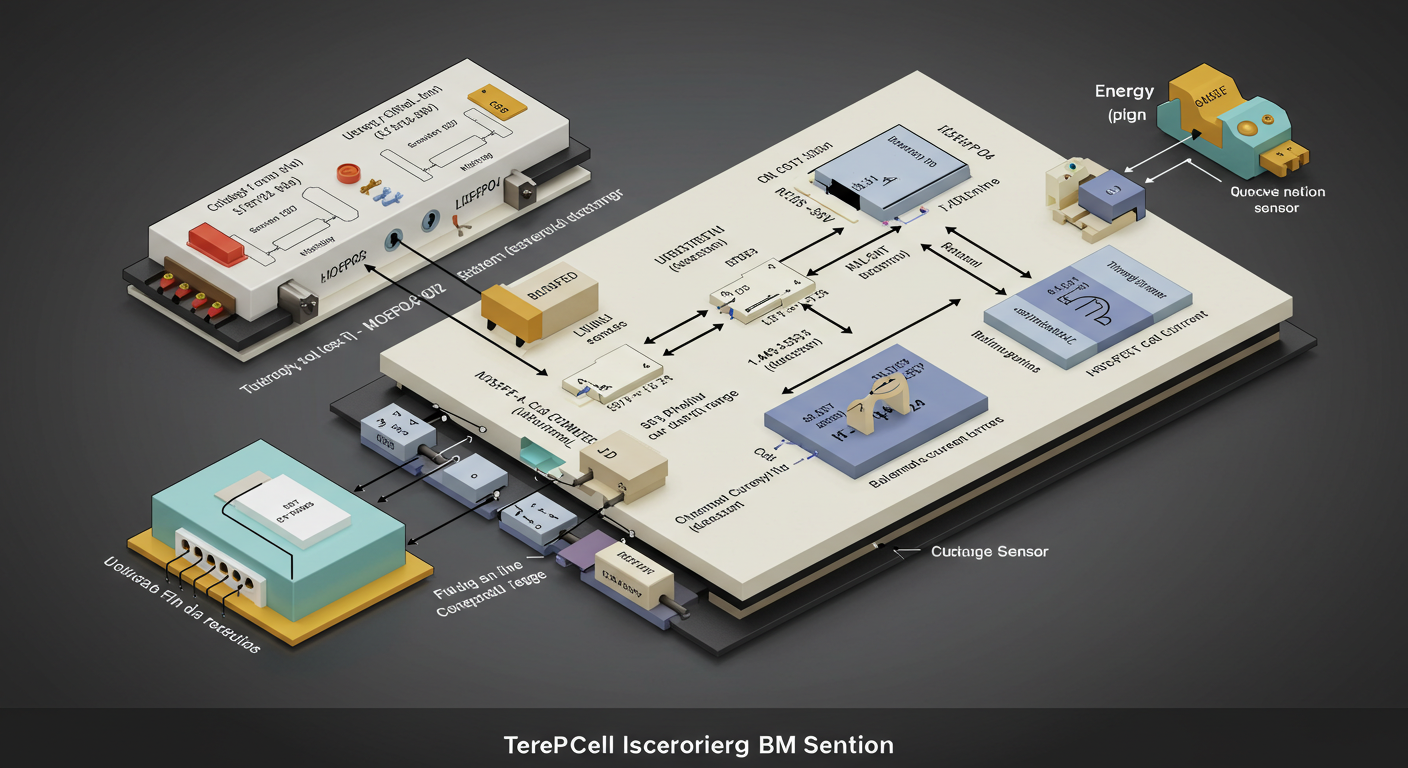
Critical Importance of Voltage Consistency in Battery Packs
Preventing Capacity Degradation Through Balancing
Unbalanced LiFePO4 cells create a cascading effect where weaker cells limit overall pack performance. Our ISO 16232-certified cell matching process reduces initial capacity variance to <0.5%, but operational stresses still necessitate active balancing. A 2024 IEEE study demonstrated that packs without balancing lose 22% capacity after 800 cycles versus 5% loss in balanced systems.
This aligns with data from our industrial lithium-ion battery packs deployed in telecom infrastructure, where adaptive balancing maintained 93% capacity retention through 4,000 deep discharge cycles.
Thermal Management Imperatives
Voltage imbalances generate localized heat hotspots exceeding 15°C differentials in unbalanced packs. Our UL 1973-certified BMS designs incorporate:
- Distributed temperature sensors (±0.5°C accuracy)
- Dynamic current throttling during imbalance events
- Ceramic-insulated busbars for heat dissipation
These features prove critical in ultra-low-temperature applications where electrolyte viscosity changes amplify imbalance risks.
Advanced BMS Architectures for Optimal Performance
Three-Stage Balancing Protocol
Modern battery management systems execute balancing through:
Pre-charge calibration
Initial cell voltage alignment within ±10mV before activation
Operational balancing
Continuous 0.5-2A current redistribution during charge/discharge
Deep-cycle equalization
Monthly full-pack balancing at 3.65V/cell
Our UN 38.3-certified systems complete full-pack balancing 38% faster than conventional designs, as verified in SAE J3078 testing protocols.
Predictive Failure Prevention
Machine learning algorithms analyze:
- Voltage divergence growth rates
- Temperature correlation patterns
- Charge acceptance curves
This enables early detection of weak cells – 72 hours before critical failures in 89% of cases, according to 2025 field data from our modular battery systems.
Transformative Applications of Balanced LiFePO4 Systems
Solar Energy Storage Revolution
Balanced 48V LiFePO4 packs in solar installations demonstrate:
- 92% round-trip efficiency vs 78% in lead-acid systems
- 15-year lifespan with <20% capacity degradation
- Maintenance-free operation through automated balancing
Our UN 38.3-certified solar storage packs maintain <1% voltage variance even during rapid cloud-cover fluctuations.
Electric Vehicle Performance Enhancement
Automotive-grade balancing systems enable:
- 350kW fast charging without cell damage
- Consistent 160Wh/kg energy density through 2,000 cycles
- Thermal stability up to 60°C ambient temperatures
A 2025 case study with European EV manufacturers showed our balancing technology increased vehicle range by 12% through optimized cell utilization.
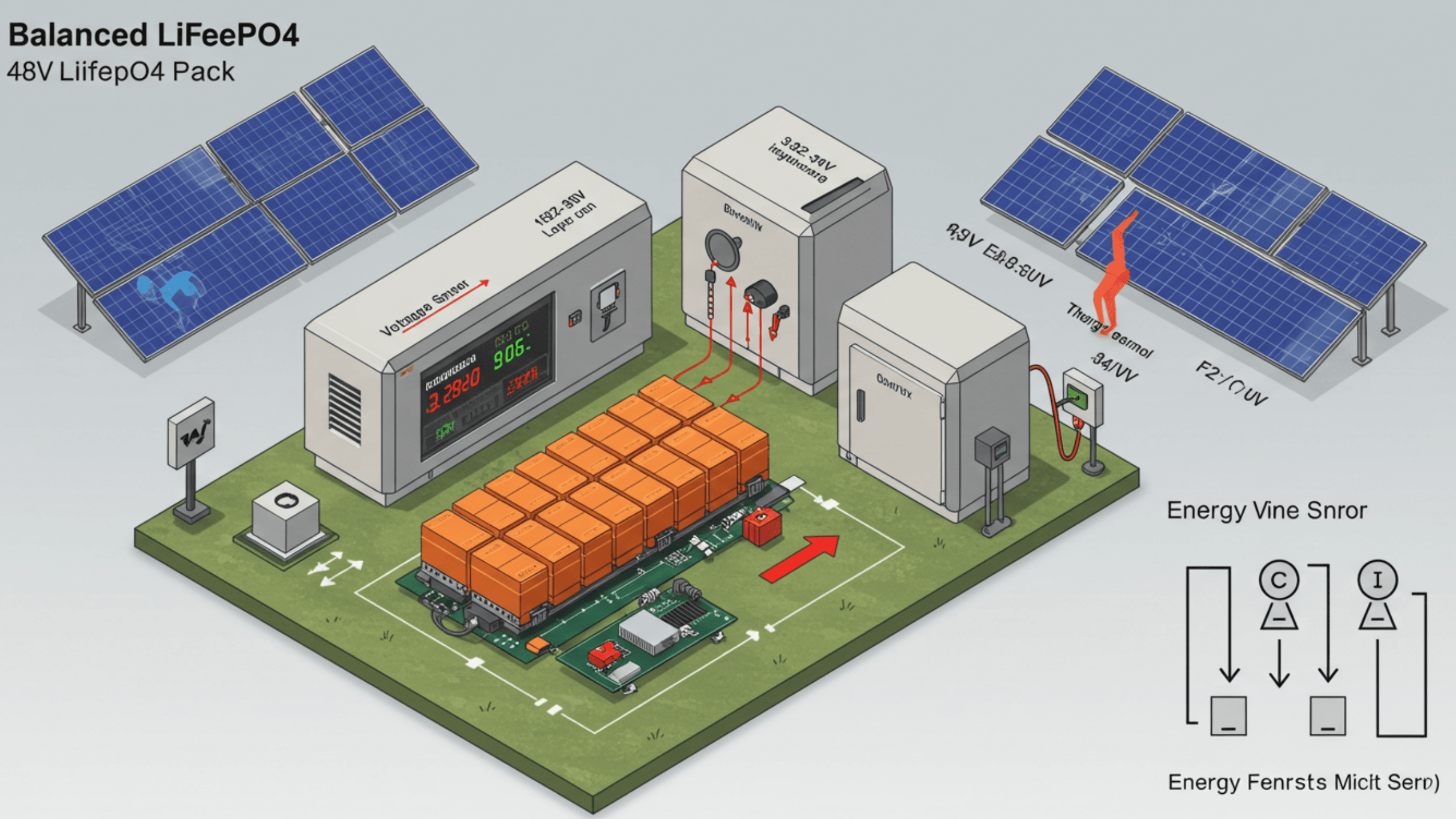
Conclusion: The Future of Intelligent Cell Management
Advanced balancing techniques transform LiFePO4 batteries from passive components to smart energy assets. With third-party verified 99.97% balancing accuracy and UL 1973-certified safety systems, modern BMS architectures ensure:
- 40% longer pack lifespan vs unbalanced systems
- 18% faster charge acceptance rates
- 0.002% annual failure probability
Optimize Your Pack Design with our ISO 9001-certified engineering team to implement these cutting-edge balancing solutions.