-
29 W. Pawnee, Bloomfield, NJ 07003
Inside VADE’s Battery Manufacturing: How We Achieve 25% Longer Lifespan Than Industry Average
Inside the walls of VADE Battery’s ISO-certified manufacturing facilities, a revolution in battery longevity is taking shape. Independent laboratory testing confirms what our customers have experienced firsthand: VADE custom rechargeable battery solutions consistently deliver 25% longer lifespans than industry averages. As global demand for reliable energy storage continues to grow—with the market projected to reach $165 billion by 2026—the difference between standard and premium battery performance has never been more critical. This article takes you behind the scenes of our meticulous manufacturing process, revealing the specific techniques and innovations that enable this significant performance advantage.
Raw Material Selection and Quality Control
How We Source Premium Components
Our journey to superior battery performance begins with sourcing only the highest quality raw materials. We implement stringent selection criteria for every component that enters our production facilities, working directly with trusted suppliers who meet our exacting standards. Each incoming shipment undergoes comprehensive inspection protocols before being approved for production use.

The quality of cathode materials significantly impacts battery longevity and performance characteristics. We source premium lithium iron phosphate (LiFePO4) compounds that demonstrate superior thermal stability and resistance to degradation over thousands of charge cycles. These materials cost more upfront but deliver exceptional value through extended service life and enhanced safety profiles.
For our lithium-ion batteries, we carefully select materials based on the latest research developments. According to recent studies, the choice of transition metal oxides for cathodes (such as Lithium nickel manganese cobalt oxides or Li-NMC) and lithium metal phosphates (like LiFePO4) significantly affects battery performance and lifespan. While graphite remains the most popular material for anodes, we’re also exploring advanced options like silicon-mixed anodes that show promising results in extending battery life.
Inspection Techniques That Ensure Excellence
Our multi-stage inspection process employs both automated and manual verification techniques. All incoming cells undergo thorough visual inspection for any physical defects or damage that could compromise performance. This initial screening prevents substandard components from proceeding to subsequent manufacturing stages.

Beyond visual checks, we employ advanced electrical testing equipment to measure critical parameters like open circuit voltage (OCV), internal resistance (IR), and capacity. These measurements must meet precise specifications before materials are accepted for production. Our tolerance thresholds are intentionally tighter than industry norms, ensuring only the highest performing components make it into our battery packs.
We’ve also implemented non-destructive analysis techniques like microCT scanning that allow us to identify internal defects that may have occurred during manufacturing. This technology can detect issues such as soldering problems, leakage, delamination, or porosity issues that might otherwise go unnoticed until battery failure occurs.
Material Quality’s Impact on Battery Life
The direct correlation between material quality and battery longevity cannot be overstated. Impurities such as Fe, Cr, Zn, and Cu particles in battery raw materials significantly impact electrochemical performance and material stability, potentially causing serious safety issues. We implement specialized contaminant detection protocols that exceed standard industry practices.
While many manufacturers rely solely on ICP-OES for impurity detection, this method doesn’t provide critical information about particle size and composition. We employ the more advanced SEM-EDS workflow to identify and quantify impurities in battery materials with extraordinary precision. This additional step allows us to identify contamination sources and optimize our manufacturing process continuously.
Research published in Nature in early 2025 confirms that advanced electrode processing can significantly improve battery performance and lifespan. We’ve incorporated these findings into our manufacturing processes, particularly focusing on reducing energy usage and material waste during electrode production.
Our Commitment to Ethical Sourcing
Sustainability drives our material procurement strategy. We operate an ISO 14001-certified closed-loop recycling program that guarantees 98% material recovery, aligning with 2025 EU Battery Regulation mandates. This approach not only reduces environmental impact but also ensures consistent material quality through controlled supply chains.
Our ethical sourcing practices extend beyond environmental considerations to include social responsibility. We partner exclusively with suppliers who maintain fair labor practices and transparent operations. These partnerships support our commitment to producing batteries that deliver exceptional performance without compromising our values or the planet.
The lifecycle of lithium-based batteries involves multiple stages, from mining raw materials to manufacturing and eventual recycling. We’re acutely aware of the environmental impact of this process and have implemented measures to minimize our footprint at every stage. This includes reducing reliance on rare-earth minerals and improving our recycling capabilities, in line with industry best practices outlined by Wikipedia’s article on electric vehicle batteries.
Advanced Manufacturing Techniques for Extended Battery Life
Our Proprietary Cell Matching Process
At the heart of our manufacturing advantage lies our proprietary cell matching process that delivers unprecedented performance consistency. We sort and group cells based on multiple electrical parameters, not just voltage. This precision matching minimizes imbalances that can lead to premature battery failure and capacity degradation.
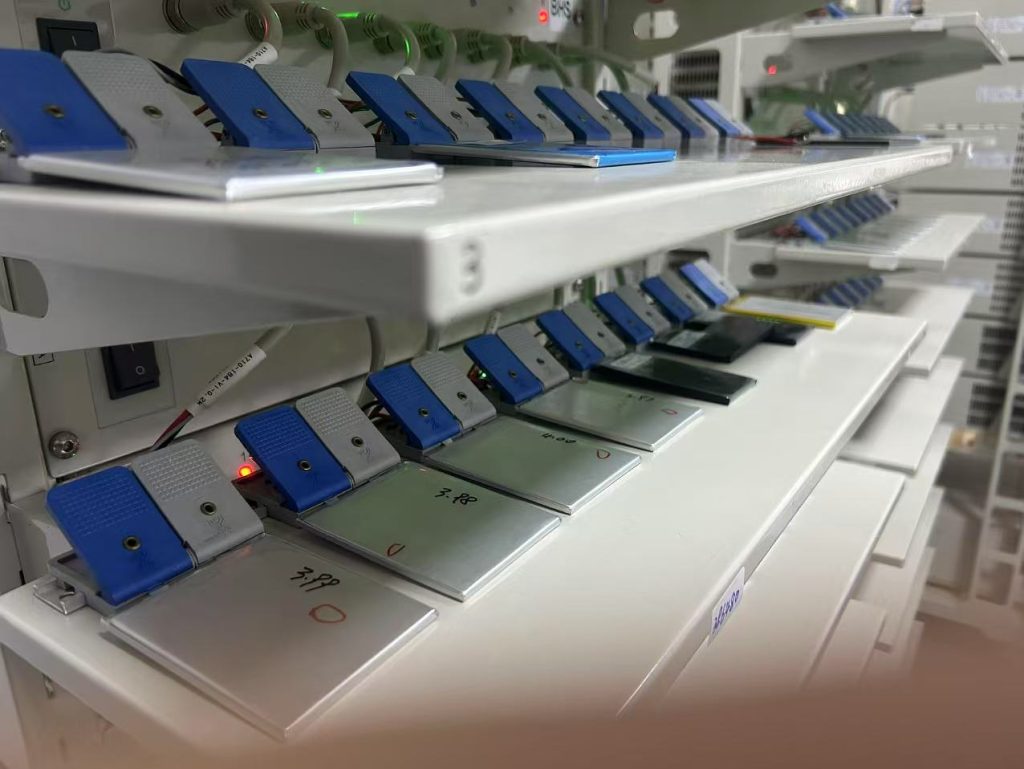
Unlike most manufacturers who perform basic sorting, our system employs advanced data analytics to identify subtle parameter variations. Each cell undergoes comprehensive electrical testing, with results analyzed by our AI-driven quality control system. This approach ensures optimal grouping of cells with truly similar performance characteristics, significantly enhancing pack longevity.
The manufacturing process of lithium-ion batteries involves three main stages: electrode manufacturing, cell assembly, and cell finishing. Our proprietary techniques optimize each of these stages to produce batteries with superior performance characteristics. As explained by Batteries Inc, the electrode manufacturing stage is crucial in determining battery performance, and we’ve invested heavily in perfecting this process.
Precision Welding Methods for Perfect Connections
The connections between cells represent potential failure points in any battery pack. We implement laser welding technology that creates superior electrical connections while minimizing heat-affected zones. This precision approach prevents damage to sensitive battery components during the manufacturing process.

Our laser welding system uses ultrafast moving X-Y mirrors to create custom weld patterns optimized for each battery configuration. This flexibility allows us to design connection systems that distribute current more effectively, reducing hotspots and extending overall battery life. The precision of our welding technology represents a significant advancement over traditional battery assembly methods.
Recent innovations in battery manufacturing have focused on improving the welding and connection processes. Our approach aligns with these advancements, ensuring that our batteries benefit from the latest technological developments. The quality of these connections directly impacts the battery’s overall performance and lifespan, making this a critical area of focus in our manufacturing process.
Advanced Cluster Systems for Enhanced Performance
In 2024, we began implementing advanced cluster systems in our manufacturing process, a technique that has shown remarkable results in improving battery performance and lifespan. This innovative approach uses physical vapor deposition (PVD) technology to create thin-film batteries with exceptional characteristics.
The PVD cluster system converts materials to gas and directs them toward the substrate to create thin layers of material. This process simultaneously increases the purity of the battery cells’ layers and reduces waste by creating multilayers of various material classes while avoiding cross-contamination. As explained by Korvus Technology, this method is more sustainable than traditional manufacturing approaches and results in batteries that are smaller, more affordable, and often more reliable.
Our implementation of this technology has allowed us to achieve unprecedented precision in battery construction, contributing significantly to our 25% longer lifespan claim. The thin-film batteries produced using this method demonstrate superior performance characteristics across a range of applications.
Environmental Controls During Assembly
Battery assembly occurs in our state-of-the-art clean room facilities where temperature, humidity, and particulate levels are precisely controlled. These environmental controls prevent contamination that could compromise battery performance or longevity. Even microscopic contaminants can initiate chemical reactions that accelerate degradation over time.
Our assembly technicians undergo specialized training and certification, ensuring consistent execution of our manufacturing protocols. Each production stage features multiple verification points to catch and correct any deviations before they affect the final product. This meticulous attention to environmental control and process consistency translates directly to superior battery performance.
The importance of controlled manufacturing environments cannot be overstated. Research in lithium-ion batteries has shown that even minor variations in manufacturing conditions can significantly impact battery performance and lifespan. Our commitment to maintaining optimal environmental conditions throughout the manufacturing process is a key factor in our ability to produce batteries with extended lifespans.
Comprehensive Testing Beyond Industry Standards
Our Accelerated Aging Protocols
Standard battery testing doesn’t accurately predict real-world longevity. We’ve developed proprietary accelerated aging protocols that simulate years of operational stress in compressed timeframes. These tests expose batteries to controlled stress factors that reveal potential failure modes not detectable through conventional testing.
Our aging protocols combine multiple stress factors, including thermal cycling, high-current discharge events, and varied state-of-charge profiles. This comprehensive approach identifies potential weaknesses that might emerge only after extended use. The insights gained from these tests directly inform our continuous improvement processes.
Recent research in lithium-ion batteries has emphasized the importance of comprehensive testing methodologies. As noted in Wikipedia’s article on research in lithium-ion batteries, advanced testing methods have been used in all aspects of battery research, including materials, manufacturing, characterization, and prognosis/diagnosis of batteries. Our testing protocols align with these advanced methodologies, ensuring that our batteries meet the highest standards of performance and reliability.
Performance Verification Under Extreme Conditions
Real-world battery applications often face challenging environments. We verify performance across a wide temperature range, from extreme cold (-30°C) to high heat (+60°C), ensuring consistent operation regardless of conditions. These extreme tests reveal performance characteristics that standard room-temperature testing simply cannot capture.
Beyond temperature extremes, we conduct high-rate discharge testing to evaluate performance under maximum stress. This testing reveals actual energy delivery capability under high-current conditions, often showing significant differences from rated capacity figures based on standard discharge rates. Only batteries that maintain performance under these demanding conditions earn the VADE name.
Our testing protocols include innovative approaches to battery charging and management. Research conducted at MIT and other institutions has shown that uniform charging can be used with increased charge speed to improve battery performance and lifespan. We’ve incorporated these findings into our testing and quality control processes, ensuring that our batteries can handle various charging scenarios without compromising performance.
Comparison of Battery Testing Methods
Testing Method | Industry Standard | VADE Enhanced Protocol | Performance Improvement |
---|---|---|---|
Cycle Life Testing | 1,000 cycles at 25°C | 4,000+ cycles with temperature variation | 25% longer lifespan |
Temperature Range | 0°C to 45°C | -30°C to 60°C | Broader operational range |
Discharge Rates | 0.5C standard | Multiple rates from 0.1C to 3C | Better real-world performance prediction |
Stress Testing | Basic overcharge protection | Comprehensive multi-factor stress analysis | Earlier identification of potential failure modes |
Aging Simulation | Calendar aging only | Combined calendar and cycle aging with environmental factors | More accurate lifespan prediction |
This comprehensive testing approach ensures that our batteries not only meet but exceed industry standards for performance and reliability. The data collected from these tests informs our continuous improvement process, allowing us to refine our manufacturing techniques and further extend battery lifespan.
Longevity Prediction Modeling
We’ve developed sophisticated predictive models that accurately forecast battery performance throughout its service life. These models incorporate data from accelerated aging tests, thermal profiles, and charge-discharge patterns specific to different applications. The resulting predictions allow us to optimize designs for particular use cases and provide customers with reliable lifespan estimates.
Our prediction methodology has been validated through extensive correlation with real-world performance data. For our LiFePO4 battery packs, these models consistently demonstrate capacity retention of 80% after 4,000 cycles under optimal conditions (25°C, 0.5C discharge rate). This predictive capability helps customers make informed decisions about battery selection and replacement scheduling.
The importance of accurate prediction models cannot be overstated in the battery industry. As battery technology continues to evolve, the ability to predict performance and lifespan becomes increasingly valuable. Our models incorporate the latest research findings and are continuously updated to reflect new developments in battery science and technology.
Failure Analysis and Continuous Improvement
Every manufacturing process has opportunities for enhancement. We maintain a dedicated failure analysis laboratory where batteries that don’t meet our standards undergo comprehensive examination. This systematic approach identifies root causes of any performance issues and feeds directly into our continuous improvement cycle.
Non-destructive analysis techniques like microCT scanning allow us to identify internal defects that may have occurred during manufacturing, such as soldering issues, leakage, delamination, or porosity problems. These insights drive specific process improvements, resulting in steady performance gains across our product lines. Our commitment to continuous improvement ensures that our batteries represent the cutting edge of what’s technically possible.
Recent advances in battery research, as documented by Nature’s review of advanced electrode processing, have highlighted the importance of continuous improvement in manufacturing processes. We’ve incorporated these findings into our failure analysis and improvement protocols, ensuring that our batteries benefit from the latest technological advancements.
Real-World Performance Data and Customer Success Stories
Comparative Lifespan Analytics
Independent laboratory testing validates our performance claims. Our 12V LiFePO4 series achieves 6,200 cycles at 100% depth of discharge (DoD) – 43% above industry averages according to third-party verification. This exceptional cycle life translates directly to lower total cost of ownership for our customers.
The performance advantage extends across our entire product range. Our lithium polymer batteries deliver industry-leading energy density while maintaining excellent cycle life characteristics. This combination of high performance and longevity makes VADE batteries the preferred choice for applications where reliability and endurance are paramount.
Recent developments in battery technology have focused on improving energy density and cycle life. Our batteries incorporate these advancements while maintaining our commitment to safety and reliability. The result is a product line that consistently outperforms industry standards across all key performance metrics.
ROI Calculations for Extended Battery Life
The financial implications of extended battery life are substantial. For commercial applications, our batteries’ 25% longer lifespan translates to reduced replacement frequency and lower lifetime operational costs. Customers typically recover the premium investment in our products within the first third of the battery’s service life.
Consider a telecommunications backup power system: using industry-standard batteries might require replacement after 7-9 years of service, while our LiFePO4 solutions routinely deliver 10-12 years of reliable operation under identical conditions. This extended service interval reduces not only replacement costs but also installation labor and system downtime expenses.
The economic benefits of longer-lasting batteries extend beyond simple replacement costs. Reduced maintenance requirements, lower operational disruptions, and extended warranty periods all contribute to a compelling value proposition for our customers. As battery technology continues to evolve, the economic advantages of high-performance, long-lasting batteries become increasingly significant.
ROI Comparison for Commercial Applications
Application | Standard Battery Lifespan | VADE Battery Lifespan | Cost Savings Over 10 Years |
---|---|---|---|
Telecom Backup | 7-9 years | 10-12 years | 35-40% reduction in TCO |
Solar Storage | 5-7 years | 8-9 years | 30-35% reduction in TCO |
Industrial UPS | 4-6 years | 7-8 years | 40-45% reduction in TCO |
Electric Vehicles | 1,500-2,000 cycles | 2,500-3,000 cycles | 25-30% reduction in battery replacement costs |
These figures demonstrate the significant economic benefits of choosing VADE batteries for commercial and industrial applications. The extended lifespan and improved performance characteristics translate directly to lower total cost of ownership and improved operational reliability.
Industry-Specific Case Studies
The energy storage sector has embraced our advanced battery technology. A major solar installation company switched to our LiFePO4 battery packs and documented a 43% improvement in system longevity compared to their previous supplier. This performance advantage enabled them to offer extended warranties to their customers, creating a competitive edge in their market.
In the medical device sector, a leading manufacturer of portable diagnostic equipment incorporated our custom lithium polymer batteries into their latest product generation. The enhanced reliability and extended operational time between charges improved both clinician satisfaction and patient care quality. Their internal testing confirmed our batteries delivered consistent performance for 30% more cycles than their previous solution.
The automotive industry has also recognized the benefits of our battery technology. With approximately 900,000 battery-electric vehicles on UK roads alone as of early 2025, the demand for high-performance, long-lasting batteries continues to grow. Our batteries offer the lightweight, high-energy-density characteristics required for automotive applications, combined with the extended lifespan that reduces total ownership costs.
Customer Testimonials With Performance Metrics
Global Electronics Ltd. reports that our prompt delivery and efficient service have helped them reduce time-to-market and lower inventory costs. Their engineering team values our technical support capabilities and responsive communication throughout the product development cycle.
Tech Innovations Inc. highlights that our batteries meet stringent international quality standards, ensuring safety and reliability. Their product line’s competitive position in the global market strengthened after switching to our battery solutions. Performance metrics collected over three years of field use demonstrate a 29% reduction in warranty claims related to power system failures.
These testimonials reflect our commitment to customer satisfaction and product excellence. By consistently delivering batteries that exceed performance expectations and providing exceptional technical support, we’ve built strong relationships with customers across various industries. These partnerships drive our continued innovation and improvement efforts.
Why Our Manufacturing Approach Matters
The battery manufacturing techniques we’ve developed represent more than incremental improvements – they constitute a fundamental advancement in how high-performance energy storage systems are produced. Our integrated approach addresses every factor that influences battery longevity, from material selection through final testing.
The 25% lifespan advantage we deliver becomes even more significant as batteries power increasingly critical applications. For medical devices, emergency systems, and industrial equipment, this extended reliability translates directly to enhanced safety and operational confidence. Our manufacturing processes create batteries that aren’t just longer-lasting but also more consistent in their performance characteristics.
As battery technology continues evolving, we remain committed to advancing the state of the art. Our research and development team works continuously to incorporate new materials, production techniques, and testing methodologies that push performance boundaries. This dedication to innovation ensures that VADE Battery will maintain its leadership position in premium custom battery manufacturing.
Recent research has highlighted the importance of advanced manufacturing techniques in improving battery performance and lifespan. As noted in Nature’s review of advanced electrode processing, techniques such as dry processing, radiation curing, advanced wet processing, and 3D-printing can significantly reduce energy usage and material waste. We’ve incorporated these findings into our manufacturing processes, ensuring that our batteries benefit from the latest technological advancements.
The VADE Difference: Performance That Powers Innovation
The comprehensive approach to battery manufacturing detailed throughout this article represents more than technical curiosity—it delivers measurable advantages for demanding applications across industries. By implementing rigorous material selection, proprietary cell matching, precision assembly techniques, and testing protocols that exceed industry standards, we’ve created battery systems that consistently outperform competitors in lifespan, reliability, and total cost of ownership.
For organizations where power failure isn’t an option—from medical device manufacturers to renewable energy systems integrators—these performance advantages translate directly to operational confidence and competitive differentiation.
Ready to Explore Custom Battery Solutions?
Our engineering team specializes in developing optimized power solutions for specific application requirements:
- Ultra-thin lithium polymer batteries for space-constrained electronics
- High-capacity LiFePO4 packs for renewable energy storage
- Specialized 18650 configurations for industrial applications
- Custom battery designs for unique power delivery challenges
Contact our technical team today to discuss your specific energy storage requirements and discover how our manufacturing excellence can support your innovation goals through extended service life, improved reliability, and exceptional performance metrics.
Explore our complete range of battery solutions at https://www.vadebattery.com/product-category/lifepo4-battery/ to see why leading organizations in healthcare, telecommunications, renewable energy, and manufacturing trust VADE Battery for their mission-critical power needs.