Baterai litium memberi daya pada segala hal, mulai dari telepon pintar hingga kendaraan listrik, yang merupakan salah satu teknologi penyimpanan energi paling transformatif di zaman kita. Namun, terlepas dari semua keunggulannya dalam hal kepadatan energi dan kinerja, baterai litium memiliki harga premium yang signifikan dibandingkan dengan kimia baterai tradisional. Di Vade Battery, kami mengkhususkan diri dalam pengembangan solusi baterai lithium khusus berkisar dari kompak Paket baterai 7.4V untuk elektronik konsumen hingga kelas industri Sistem penyimpanan energi 72VTim teknik kami bekerja setiap hari dengan faktor-faktor biaya yang memengaruhi produksi baterai litium, mengembangkan strategi untuk mengoptimalkan kinerja sekaligus mengelola pengeluaran. Analisis komprehensif ini mengeksplorasi kontributor utama terhadap biaya baterai litium dan menjelaskan realitas manufaktur di balik harga premiumnya.
Biaya Bahan Baku dan Faktor Rantai Pasokan
Komponen dasar baterai litium merupakan komponen biaya tunggal terbesar dalam produksinya. Menurut analisis biaya Departemen Energi AS tahun 2023, bahan baku biasanya mencakup 50-70% dari biaya produksi baterai litium. Biaya yang signifikan ini berasal dari nilai intrinsik bahan dan rantai pasokan global yang kompleks yang diperlukan untuk memproses dan mengirimkannya ke produsen baterai.
Logam Kritis dan Dinamika Pasarnya
Litium sendiri, meskipun baterai ini diberi nama demikian, biasanya terdiri dari kurang dari 5% dari total bahan sel berdasarkan berat. Namun, harga litium karbonat menunjukkan volatilitas yang ekstrem, dengan harga pasar berfluktuasi antara $15.000 dan $80.000 per metrik ton selama lima tahun terakhir menurut Benchmark Mineral Intelligence. Volatilitas ini secara langsung memengaruhi biaya produksi kami untuk semuanya, mulai dari seri baterai suhu ultra rendah sesuai standar Sistem baterai 48V.
Yang lebih penting lagi adalah logam katode yang menentukan karakteristik kinerja baterai. Kobalt, komponen penting dalam katode NMC (Nikel-Mangan-Kobalt) berdensitas energi tinggi, secara rutin diperdagangkan di atas $30.000 per metrik ton. Hampir 70% produksi kobalt global berasal dari Republik Demokratik Kongo, yang menciptakan kerentanan rantai pasokan dan masalah sumber yang etis. Nikel, komponen katode penting lainnya, telah mengalami volatilitas harga sendiri dengan harga spot secara berkala melebihi $20.000 per ton setelah gangguan pasokan.
Untuk aplikasi yang mengutamakan siklus hidup panjang dan keamanan dibandingkan kepadatan energi maksimum, kami sering menerapkan LiFePO₄ (lithium besi fosfat) kimia. Meskipun hal ini mengurangi ketergantungan pada kobalt dan nikel, proses produksi khusus yang diperlukan untuk bahan katode LFP menimbulkan faktor biaya tersendiri. Prekursor fosfat memerlukan kontrol yang tepat selama sintesis untuk mencapai struktur kristal yang tepat, yang berkontribusi pada biaya produksi bahkan saat menggunakan logam dasar yang lebih banyak.
Pertimbangan Elektrolit dan Material Pemisah
Di luar logam yang terlihat yang paling menarik perhatian, bahan elektrolit dan pemisah merupakan komponen penting dengan implikasi biaya yang substansial. Larutan elektrolit dengan kemurnian tinggi biasanya menggunakan garam litium heksafluorofosfat (LiPF₆) dalam pelarut organik, dengan biaya produksi dipengaruhi oleh tingkat kemurnian yang diperlukan yang melebihi 99,99% untuk mencegah reaksi samping yang dapat menurunkan kinerja baterai.
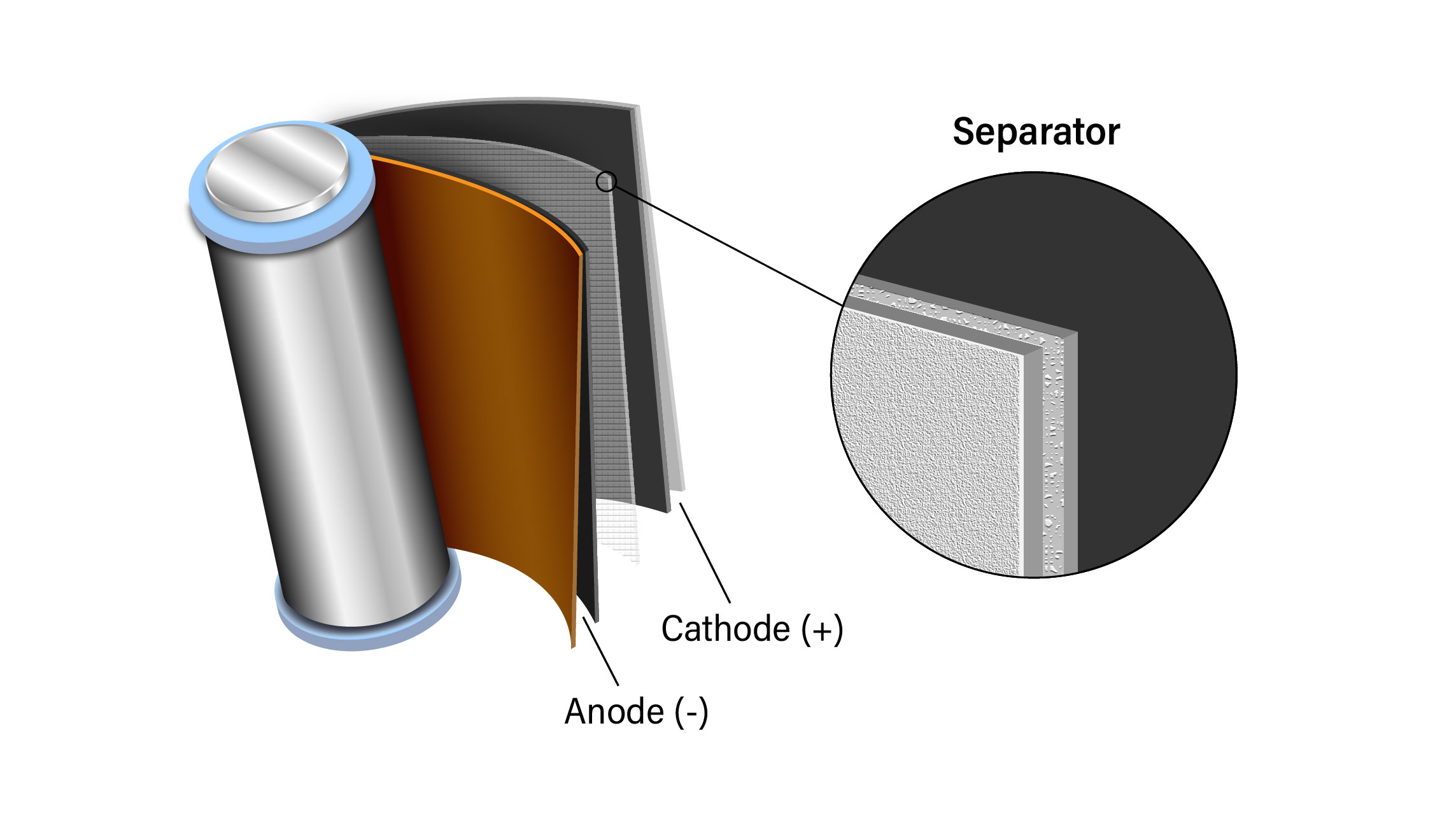
Bahan pemisah, biasanya dibuat dari film polietilena atau polipropilena mikropori khusus, memerlukan kontrol ketebalan yang tepat (biasanya 15-25 mikrometer) dan porositas yang seragam. Film pemisah ini harus mempertahankan integritas mekanis sambil memungkinkan pengangkutan ion litium di antara elektroda. Pembuatan pemisah dengan karakteristik ini memerlukan proses ekstrusi dan peregangan khusus yang menambah biaya signifikan pada sel akhir. Untuk paket baterai 51.8V berkinerja tinggi, kami menggunakan pemisah berlapis keramik yang meningkatkan stabilitas termal pada suhu hingga 180°C tetapi menambahkan sekitar 15-20% ke komponen biaya material.
Kerentanan Rantai Pasokan Global
Sifat pemrosesan material baterai yang terkonsentrasi secara geografis menciptakan tekanan biaya tambahan melalui premi risiko rantai pasokan. Menurut laporan Badan Energi Internasional tahun 2023 tentang mineral penting, Tiongkok memproses sekitar 60% litium dunia, 70% kobalt, dan 80% grafit yang digunakan dalam anoda baterai. Konsentrasi ini menciptakan kerentanan strategis bagi produsen baterai di luar wilayah ini.
Kami mengurangi risiko rantai pasokan ini melalui kemitraan strategis dengan beberapa pemasok material yang memenuhi syarat di berbagai wilayah, meskipun diversifikasi memiliki implikasi biaya tersendiri. Sistem kendali mutu harus diduplikasi di seluruh pemasok, dan pengujian kualifikasi untuk sumber material baru menambah biaya penelitian dan pengembangan. Biaya transportasi juga menjadi faktor penting dalam biaya material, dengan persyaratan penanganan khusus untuk material elektroda reaktif dan komponen elektrolit yang mudah menguap. Pertimbangan logistik ini menjadi semakin penting untuk sistem format yang lebih besar seperti paket baterai 72V kelas industri yang membutuhkan volume material besar.
Proses Manufaktur yang Kompleks
Transformasi bahan baku menjadi sel baterai litium yang fungsional memerlukan proses manufaktur yang canggih dengan persyaratan presisi yang ketat. Teknik produksi khusus ini berkontribusi secara signifikan terhadap biaya akhir baterai litium, dengan kompleksitas manufaktur yang mencakup sekitar 20-30% dari biaya produksi.
Persyaratan Presisi dalam Produksi Sel
Pembuatan sel baterai litium membutuhkan presisi yang luar biasa di hampir setiap langkah prosesnya. Pelapisan elektroda merupakan salah satu operasi yang paling penting, yang memerlukan penerapan bahan aktif yang seragam ke kolektor arus logam (tembaga untuk anoda, aluminium untuk katoda) dengan variasi ketebalan yang biasanya dijaga di bawah ±2 mikrometer. Presisi ini secara langsung memengaruhi kapasitas sel, resistansi internal, dan kinerja siklus hidup.
Kita Paket baterai berbasis sel 18650 manfaat dari penyempurnaan produksi selama puluhan tahun dalam format silinder ini, namun produksi masih memerlukan mesin canggih untuk menggulung elektroda dengan kontrol tegangan yang konsisten. Untuk format sel prismatik dan kantong khusus yang digunakan dalam aplikasi dengan keterbatasan ruang, kompleksitas produksi meningkat lebih jauh karena geometri ini memerlukan peralatan khusus untuk menumpuk atau melipat rakitan elektroda dengan penyelarasan yang tepat.
Operasi penyelesaian sel menambah lapisan kompleksitas manufaktur lainnya. Proses pengisian elektrolit harus dilakukan di lingkungan yang sangat kering (biasanya di bawah 100 ppm kelembapan) untuk mencegah kontaminasi yang dapat menyebabkan penurunan kinerja. Siklus pembentukan—urutan pengisian-pengosongan awal yang membentuk lapisan antarmuka elektrolit padat (SEI)—memerlukan kontrol presisi profil arus dan tegangan selama periode mulai dari 24-72 jam, dengan konsumsi energi yang signifikan dan kebutuhan peralatan khusus.
Persyaratan Ruang Bersih dan Kontrol Kualitas
Baterai litium membutuhkan lingkungan produksi dengan standar kebersihan yang luar biasa. Partikel sekecil 10 mikrometer dapat menyebabkan korsleting internal atau mempercepat mekanisme degradasi dalam sel. Mitra produksi kami menyediakan fasilitas ruang bersih ISO Kelas 7-8 dengan sistem penyaringan udara yang canggih, pakaian kerja khusus, dan protokol pengendalian kontaminasi yang ketat yang menambah biaya operasional yang besar untuk produksi baterai.
Kontrol kualitas merupakan biaya signifikan lainnya dalam produksi baterai lithium. Setiap sel menjalani beberapa titik pemeriksaan, termasuk pemeriksaan optik otomatis pada elektroda, pemeriksaan sinar-X untuk mendeteksi cacat internal, dan pengukuran berat presisi untuk memverifikasi pengisian elektrolit. Untuk kami sistem baterai 46,8V yang sangat penting Digunakan dalam aplikasi medis, sel 100% menjalani penyaringan tambahan termasuk pemantauan tegangan sirkuit terbuka yang diperluas untuk mendeteksi cacat produksi halus yang dapat memengaruhi kinerja.
Langkah-langkah pengendalian mutu ini menambah biaya langsung melalui peralatan dan tenaga kerja khusus, tetapi memberikan nilai substansial dengan mencegah kegagalan di lapangan dan meningkatkan keselamatan. Data internal kami menunjukkan bahwa proses penyaringan komprehensif mengidentifikasi sekitar 2-5% sel dengan cacat kecil yang dapat menyebabkan kegagalan dini atau penurunan kinerja, sehingga membenarkan biaya produksi tambahan melalui peningkatan keandalan.
Tantangan Otomasi dan Skala
Meskipun otomatisasi telah mengurangi beberapa biaya produksi, persyaratan presisi produksi baterai litium membatasi potensi pengurangan biaya melalui mekanisasi saja. Sistem penanganan elektroda harus mengelola material yang sangat tipis dan mudah rusak dengan kontrol tegangan yang konsisten. Operasi perakitan memerlukan perkakas khusus untuk tugas-tugas seperti pengelasan tab, di mana sistem pengelasan ultrasonik atau laser menyambungkan tab pengumpul arus dengan toleransi yang diukur dalam mikrometer.
Tantangan dalam meningkatkan skala produksi merupakan faktor biaya lain dalam pembuatan baterai litium. Tidak seperti banyak teknologi yang skala ekonominya mengikuti kurva biaya yang dapat diprediksi, produksi baterai litium memerlukan penyeimbangan yang cermat antara hasil produksi dengan kontrol kualitas. Kecepatan produksi meningkatkan risiko yang menimbulkan cacat kecil yang mungkin tidak terlihat hingga setelah sel mulai beroperasi. Untuk kami sistem baterai 24V dengan keandalan tinggi digunakan dalam aplikasi infrastruktur penting, kami mengutamakan proses manufaktur yang menekankan konsistensi dibandingkan hasil maksimal, menerima premi biaya terkait untuk memastikan keandalan kinerja.
Konsumsi energi selama proses produksi menambah biaya signifikan lainnya. Lingkungan ruang kering yang dibutuhkan untuk perakitan sel biasanya mempertahankan kelembapan relatif di bawah 1%, yang membutuhkan sistem dehumidifikasi yang substansial. Siklus pembentukan menghabiskan banyak listrik, dan langkah-langkah pemrosesan termal untuk pengeringan elektroda dan aktivasi elektrolit memerlukan kontrol suhu yang tepat selama periode yang panjang. Proses yang membutuhkan banyak energi ini berkontribusi pada biaya produksi sekaligus memengaruhi jejak karbon dari produksi baterai.
Sistem Manajemen Baterai dan Fitur Keselamatan
Elektronik canggih yang dibutuhkan untuk mengelola baterai litium merupakan bagian penting dari keseluruhan struktur biaya. Tidak seperti kimia baterai yang lebih sederhana, sel litium memerlukan pemantauan dan kontrol yang cermat untuk memastikan pengoperasian yang aman dan efisien selama masa pakainya. Sistem perlindungan ini biasanya menghabiskan 15-25% dari total biaya paket, tergantung pada kompleksitas dan fungsionalitas.
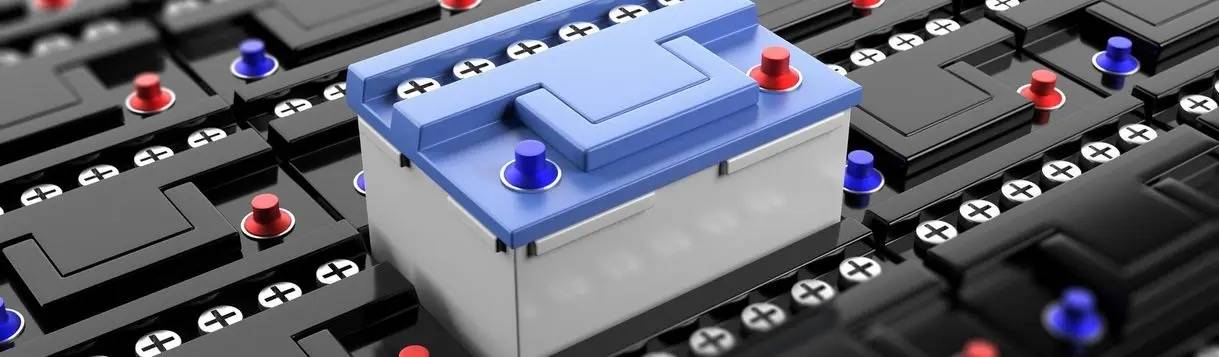
Peran Penting BMS dalam Baterai Lithium
Setiap paket baterai lithium yang kami produksi menggabungkan Sistem Manajemen Baterai (BMS) disesuaikan dengan persyaratan aplikasi tertentu. Sistem kontrol elektronik ini memiliki beberapa fungsi penting: mencegah sel melebihi batas tegangan aman selama pengisian daya, memantau laju pengosongan daya untuk mencegah kondisi arus berlebih yang merusak, menyeimbangkan tingkat pengisian daya antara sel individual, dan melacak suhu di beberapa titik dalam kemasan.
Untuk kita Penggantian baterai lithium 12V digunakan dalam peralatan industri, kami menerapkan desain BMS yang mempertahankan ketidakseimbangan tegangan sel di bawah 50mV selama siklus pengosongan, sehingga memperpanjang masa pakai secara signifikan dibandingkan dengan sistem dengan perlindungan dasar. Biaya pengembangan untuk sistem kontrol khusus ini mencakup rekayasa perangkat keras dan pengembangan firmware yang ekstensif, dengan algoritme hak milik yang disempurnakan melalui ribuan siklus pengujian dalam berbagai kondisi operasional.
Kompleksitas BMS disesuaikan dengan tegangan dan kapasitas baterai. sistem tegangan tinggi 72V menggabungkan lapisan perlindungan redundan dengan pemantauan suhu berlebih yang independen, beberapa sensor arus, dan pemantauan isolasi canggih untuk mendeteksi degradasi isolasi sebelum dapat menimbulkan bahaya keselamatan. Fitur-fitur canggih ini memerlukan komponen bermutu tinggi, termasuk mikrokontroler berkualifikasi otomotif, konverter analog-ke-digital presisi, dan beberapa lapisan isolasi antara sirkuit penginderaan dan kontrol.
Spesifikasi dan Biaya Rangkaian Proteksi
Komponen perlindungan dalam paket baterai litium harus memenuhi standar keandalan yang luar biasa saat beroperasi dalam kondisi yang menantang. Elemen penginderaan arus harus mengukur aliran secara akurat mulai dari miliampere selama siaga hingga ratusan ampere selama beban puncak dalam sistem daya tinggi kami. Pemantauan suhu memerlukan jaringan termistor atau sensor suhu digital yang diposisikan di lokasi strategis yang ditentukan melalui pemodelan termal dan diverifikasi dengan pencitraan inframerah selama pengujian kualifikasi.
Fitur Perlindungan | Kisaran Biaya Komponen Umum | Spesifikasi Kinerja |
---|---|---|
Pemantauan tegangan sel | $0,25-1,50 per sel | Akurasi ±10mV, laju pengambilan sampel 50ms |
Penginderaan arus | $3.50-20.00 per bungkus | Akurasi ±1%, waktu respons isolasi 500V, kebocoran <250μA |
Antarmuka komunikasi | $5.00-35.00 per bungkus | Bus CAN, Modbus, atau protokol milik sendiri |
Untuk aplikasi yang memerlukan toleransi kesalahan maksimum, seperti kami paket baterai 36V kelas medis, kami menerapkan sistem pemantauan redundan ganda dengan referensi tegangan independen dan mikrokontroler terpisah yang memeriksa silang pengukuran. Arsitektur redundan ini menambah biaya komponen sekaligus meningkatkan keamanan secara signifikan untuk aplikasi kritis yang tidak memungkinkan kegagalan.
Kecerdasan yang tertanam dalam desain BMS modern melampaui fungsi keselamatan dasar hingga mencakup fitur yang meningkatkan keawetan dan kinerja baterai. Algoritma estimasi status pengisian daya yang canggih menggabungkan pengukuran tegangan dengan penghitungan coulomb dan pelacakan impedansi untuk memberikan informasi kapasitas yang akurat di seluruh siklus pengosongan daya. Antarmuka kontrol manajemen termal mengatur sistem pendinginan aktif dalam aplikasi pengosongan daya tinggi, menjaga masa pakai sel dengan mencegah perubahan suhu selama kasus penggunaan yang menuntut.
Persyaratan Pengujian dan Sertifikasi
Persyaratan regulasi untuk keamanan baterai litium merupakan faktor pemicu biaya signifikan lainnya. Setiap desain baterai yang kami produksi menjalani pengujian sertifikasi komprehensif sesuai dengan standar termasuk UN 38.3 untuk keselamatan transportasi, IEC 62133 untuk keselamatan sel, dan UL 1642/2054 untuk berbagai aplikasi. Protokol pengujian ini mencakup kondisi penyalahgunaan ekstrem seperti pengujian benturan, ketahanan penetrasi, siklus termal antara -40°C dan +75°C, dan evaluasi hubung singkat.
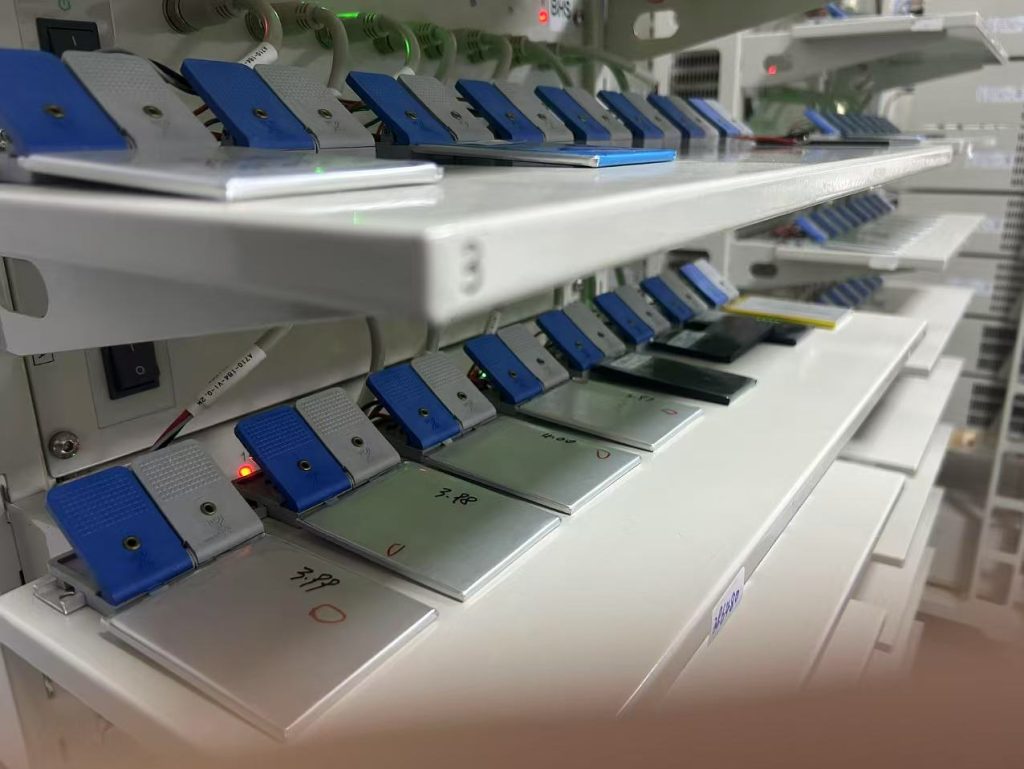
Untuk kita sistem baterai 48V yang berfokus pada transportasi, standar tambahan seperti ECE R100 (untuk aplikasi otomotif) atau EN 50604 (untuk kendaraan listrik ringan) mungkin berlaku, yang memerlukan pengujian khusus lebih lanjut. Proses sertifikasi ini biasanya menghabiskan biaya antara $15.000-$50.000 per model baterai, tergantung pada kompleksitas dan persyaratan aplikasi. Meskipun biaya ini diamortisasi di seluruh volume produksi, biaya ini berkontribusi secara signifikan terhadap biaya pengembangan untuk solusi baterai khusus.
Pengujian internal melampaui persyaratan regulasi untuk mencakup validasi khusus aplikasi. Untuk baterai yang ditujukan untuk lingkungan dengan getaran intensif, kami melakukan pengujian lanjutan pada pengocok elektrodinamik yang mereplikasi kondisi lapangan yang dipercepat untuk mengompresi tahun layanan menjadi minggu evaluasi laboratorium. Ruang lingkungan khusus mensimulasikan suhu ekstrem, siklus kelembapan, dan paparan kabut garam untuk aplikasi kelautan. Program pengujian komprehensif ini menambah biaya pengembangan tetapi memastikan baterai kami memberikan kinerja yang andal sepanjang masa pakai yang dimaksudkan.
Biaya Pengemasan dan Integrasi Mekanik
Mengubah sel litium individual menjadi sistem baterai fungsional memerlukan teknologi pengemasan canggih yang melindungi komponen elektrokimia sekaligus memungkinkan pengoperasian yang aman dan andal di berbagai lingkungan. Elemen integrasi mekanis ini menambah 10-15% pada biaya baterai secara keseluruhan tetapi memberikan perlindungan dan fungsionalitas penting yang secara langsung memengaruhi kinerja dan keselamatan.
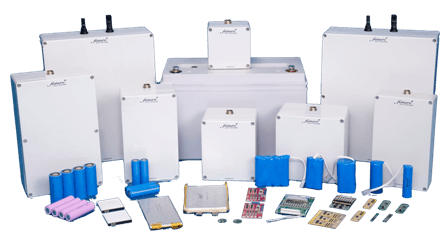
Bahan Penutup dan Pembuatan
Casing pelindung untuk paket baterai lithium harus memenuhi beberapa persyaratan yang menuntut secara bersamaan. Untuk sistem baterai industri 51.2V, penutup biasanya menggunakan paduan aluminium dengan ketebalan dinding berkisar antara 1,5-3 mm, yang memberikan konduktivitas termal, pelindung elektromagnetik, dan perlindungan mekanis yang sangat baik. Proses pemesinan yang dikontrol komputer dengan toleransi yang ditetapkan hingga ±0,1 mm memastikan kesesuaian komponen yang presisi, tetapi teknik manufaktur ini menambah biaya yang signifikan dibandingkan dengan proses pencetakan plastik sederhana yang digunakan untuk aplikasi yang tidak terlalu menuntut.
Aplikasi dengan paparan lingkungan yang ekstrem memerlukan tindakan perlindungan tambahan. Kandang dengan peringkat IP67 menjalani uji tekanan untuk memverifikasi pengecualian air dan debu pada kedalaman hingga 1 meter. Bahan paking khusus mempertahankan kinerja penyegelan pada rentang suhu dari -40°C hingga +85°C sekaligus menahan degradasi dari paparan sinar ultraviolet dan kontaminan kimia. Sistem penyegelan canggih ini menambah biaya komponen sekaligus memerlukan produksi yang presisi untuk mempertahankan gaya kompresi dalam batas yang ditentukan.
Desain struktural penutup baterai juga harus memperhitungkan perbedaan ekspansi termal antara komponen, isolasi getaran, dan ketahanan benturan yang sesuai dengan aplikasi. Tim teknik kami menggunakan analisis elemen hingga untuk mengoptimalkan desain ini, mengurangi penggunaan material sambil mempertahankan integritas struktural. Untuk aplikasi yang sensitif terhadap berat seperti peralatan portabel yang ditenagai oleh paket baterai ringan 7.4V, kami menerapkan bahan penutup komposit yang mengurangi berat hingga 40% dibandingkan dengan alternatif aluminium, meskipun bahan canggih ini biasanya menambahkan 25-30% ke komponen biaya penutup.
Sistem Manajemen Termal
Manajemen termal yang efektif merupakan salah satu tantangan teknik paling signifikan dalam desain baterai litium. Performa, umur pakai, dan keamanan sel bergantung pada pemeliharaan suhu operasi yang tepat, dengan setiap kimia memiliki rentang optimal tertentu. Untuk aplikasi dengan kebutuhan daya yang sederhana, pendinginan pasif melalui jarak sel yang strategis dan material konduktif termal mungkin cukup, sehingga menambah biaya minimal pada keseluruhan sistem.
Namun, aplikasi dengan debit tinggi seperti kami Sistem baterai traksi 72V memerlukan solusi manajemen termal aktif. Solusi ini biasanya menggabungkan sirkuit pendingin cair dengan kontrol aliran presisi, sensor suhu di beberapa titik dalam kemasan, dan algoritma kontrol yang menyesuaikan intensitas pendinginan berdasarkan kondisi pengoperasian saat ini dan riwayat termal. Penambahan pompa, penukar panas, sensor suhu, dan elektronik kontrol dapat menambah 15-30% ke total biaya kemasan, tetapi sistem ini memungkinkan pengoperasian daya tinggi yang berkelanjutan sekaligus mencegah degradasi termal yang dapat memperpendek masa pakai baterai.
Bahkan baterai tanpa pendinginan aktif memerlukan desain termal yang cermat. Kami menggunakan bahan pengisi celah khusus dengan nilai konduktivitas termal antara 3-8 W/m·K untuk memindahkan panas dari sel ke permukaan penutup eksternal. Senyawa konduktif termal tetapi isolasi listrik ini menambah biaya material dan kompleksitas perakitan tetapi secara substansial meningkatkan keseragaman suhu di seluruh kelompok sel. Untuk aplikasi dengan persyaratan pelepasan tinggi yang terputus-putus, kami menggabungkan bahan perubahan fase yang menyerap panas selama beban puncak dan secara bertahap melepaskannya selama masa istirahat, meredam fluktuasi suhu yang akan mempercepat mekanisme penuaan.
Teknologi Interkoneksi
Koneksi antara sel-sel individual merupakan komponen biaya penting lainnya dalam sistem baterai lithium. Untuk informasi lebih lanjut, kunjungi situs web kami. Paket baterai 36V digunakan dalam perkakas listrik dan aplikasi serupa, kami menerapkan busbar nikel atau tembaga yang dilas laser dengan penetrasi las yang dikontrol secara tepat untuk menyambung sel tanpa kerusakan termal pada komponen internal. Proses pengelasan ini memerlukan peralatan khusus dengan pemantauan proses yang komprehensif untuk memastikan ketahanan listrik dan kekuatan mekanis yang konsisten di setiap titik sambungan.
Aplikasi arus tinggi membutuhkan sistem interkoneksi yang sangat kuat. paket baterai kelas industri memanfaatkan interkoneksi yang mampu menangani arus kontinu yang melebihi 200A dengan kenaikan suhu dibatasi hingga 20°C di atas suhu sekitar. Sambungan tugas berat ini biasanya menggunakan busbar tembaga dengan luas penampang yang ditentukan melalui kapasitas arus listrik dan persyaratan kekuatan mekanis. Proses pelapisan khusus, biasanya nikel atau timah, melindungi sambungan ini dari oksidasi sekaligus mempertahankan resistansi kontak yang rendah selama masa pakai baterai.
Kabel internal di dalam kemasan baterai merupakan elemen biaya signifikan lainnya. Kami memilih ukuran konduktor berdasarkan kebutuhan arus kontinu dan puncak, biasanya menggunakan kabel berisolasi silikon dengan peringkat suhu melebihi 150°C untuk mempertahankan batas keamanan selama operasi beban tinggi. Sambungan terminal menggunakan terminasi yang dikerutkan atau dilas ultrasonik daripada sambungan yang disolder, karena yang terakhir dapat menciptakan titik lemah di lingkungan dengan getaran tinggi. Teknik sambungan khusus ini memerlukan perkakas khusus dan validasi proses untuk setiap desain baterai, yang berkontribusi pada biaya pengembangan dan produksi.
Transportasi dan Kepatuhan Peraturan
Klasifikasi baterai litium sebagai barang berbahaya berdasarkan peraturan pengiriman internasional menimbulkan tantangan logistik yang unik dan biaya terkait. Persyaratan peraturan ini tidak hanya memengaruhi biaya pengiriman tetapi juga keputusan desain, protokol pengujian, dan sistem dokumentasi, yang secara kolektif menambah 8-12% pada total biaya baterai.
Persyaratan Pengujian Transportasi UN 38.3
Semua baterai litium yang dikirim secara internasional harus mematuhi peraturan PBB 38.3 untuk pengangkutan barang berbahaya. Protokol pengujian komprehensif ini menguji baterai dengan delapan uji penyalahgunaan khusus: simulasi ketinggian, siklus termal, getaran, guncangan, hubungan arus pendek eksternal, benturan/hancuran, pengisian daya berlebih, dan pelepasan daya paksa. Setiap rangkaian pengujian memerlukan beberapa sampel baterai pada berbagai kondisi pengisian daya, dengan kriteria lulus/gagal yang ketat berdasarkan kerusakan yang dapat diamati, kenaikan suhu, dan perilaku tegangan.
Untuk kita desain baterai khusus, pengujian wajib ini biasanya menelan biaya antara $8.000-$15.000 per model, tergantung pada ukuran dan kompleksitas. Laboratorium pengujian khusus memelihara peralatan yang dikalibrasi dan lingkungan terkendali yang diperlukan untuk protokol standar ini. Meskipun biaya ini biasanya diamortisasi berdasarkan jumlah produksi, biaya ini merupakan biaya pengembangan yang signifikan, khususnya untuk baterai khusus dengan volume produksi terbatas. Tim teknik kami merancang dengan mempertimbangkan persyaratan ini, menggabungkan fitur yang meningkatkan ketahanan di bawah kondisi tekanan tertentu yang dievaluasi dalam pengujian UN 38.3.
Selain sertifikasi awal, kepatuhan berkelanjutan terhadap peraturan barang berbahaya memerlukan dokumentasi terperinci untuk setiap pengiriman. Sistem baterai kami mencakup pelabelan wajib dengan kapasitas Watt-jam, nomor PBB, dan peringatan bahaya yang sesuai. Dokumentasi pengiriman harus mencakup informasi ringkasan pengujian yang mengonfirmasi kepatuhan terhadap PBB 38.3, dengan persyaratan format dan konten yang berubah secara signifikan dengan pembaruan Peraturan Barang Berbahaya IATA tahun 2020. Memelihara sistem dokumentasi ini menambah beban administratif pada setiap pengiriman baterai.
Pembatasan dan Alternatif Transportasi Udara
Tantangan transportasi yang paling signifikan untuk baterai litium melibatkan pembatasan angkutan udara. Peraturan IATA saat ini melarang pengiriman baterai litium sebagai kargo pada pesawat penumpang kecuali jika dipasang atau dikemas dengan peralatan, dan bahkan pesawat kargo memiliki batasan ketat pada ukuran baterai dan persyaratan pengemasan. Pembatasan ini menimbulkan tantangan logistik untuk distribusi internasional, khususnya untuk sistem baterai berkapasitas lebih tinggi melebihi 100 Watt-jam.
Metode pengiriman alternatif seperti angkutan laut memerlukan waktu transit yang lebih lama, biasanya memerlukan waktu 3-5 minggu untuk pengiriman internasional dibandingkan dengan angkutan udara. Jangka waktu yang lebih lama ini meningkatkan kebutuhan modal kerja karena persediaan menghabiskan lebih banyak waktu dalam perjalanan. Kontainer dengan pengaturan suhu mungkin diperlukan untuk mencegah suhu ekstrem selama pengangkutan laut, sehingga menambah biaya pengiriman yang dapat melebihi $2.000 per kontainer pengiriman untuk rute lintas samudra.
Tim logistik kami mengatasi tantangan ini dengan menerapkan inventaris regional strategis untuk model baterai yang umum digunakan, sehingga memungkinkan respons yang lebih cepat terhadap persyaratan pelanggan sekaligus mematuhi peraturan pengiriman. Untuk desain baterai khusus, kami bekerja sama dengan klien di awal proses pengembangan untuk menetapkan ekspektasi jangka waktu yang realistis yang memperhitungkan kompleksitas transportasi yang diperlukan. Pertimbangan logistik ini menambah biaya tidak langsung yang pada akhirnya memengaruhi harga baterai litium dibandingkan dengan alternatif yang kurang diatur.
Batasan Status Pengisian Daya
Peraturan yang mengatur pengangkutan baterai litium mencakup batasan status pengisian daya (SoC) khusus yang dimaksudkan untuk mengurangi risiko selama pengiriman. Persyaratan saat ini menetapkan status pengisian daya maksimum 30% untuk sel dan baterai litium-ion yang dikirim secara terpisah (tidak disertakan dalam peralatan). Persyaratan ini menciptakan langkah pemrosesan tambahan dalam alur kerja produksi kami, karena setiap baterai harus menjalani prosedur pengosongan daya yang terkendali untuk mencapai status yang sesuai untuk pengangkutan.
Untuk kita baterai berkapasitas tinggi 51.8V, proses pengosongan ini dapat memerlukan waktu 4-6 jam per kemasan pada peralatan khusus yang secara tepat mengendalikan laju pengosongan sambil memantau voltase sel individual. Energi yang dikosongkan merupakan kerugian produksi, karena baterai kemudian harus diisi ulang oleh pengguna akhir sebelum penggunaan awal. Kami mengoptimalkan proses ini dengan memulihkan energi selama siklus pengosongan melalui bank beban regeneratif, mengurangi pemborosan energi dan pembangkitan panas selama produksi.
Meskipun persyaratan regulasi ini menambah kompleksitas dan biaya logistik baterai litium, persyaratan tersebut mencerminkan pertimbangan keselamatan yang sah terkait dengan sumber daya berdensitas energi tinggi ini. Program kepatuhan komprehensif kami memastikan bahwa semua baterai sampai ke pelanggan dengan aman sekaligus mempertahankan kepatuhan regulasi penuh, melindungi keselamatan manusia dan pertimbangan lingkungan di seluruh rantai pasokan.
Penelitian, Pengembangan, dan Peningkatan Berkelanjutan
Lanskap teknologi baterai litium yang berkembang pesat mendorong investasi berkelanjutan yang substansial dalam penelitian dan pengembangan. Biaya litbang ini berkontribusi sekitar 5-10% terhadap biaya baterai secara keseluruhan, tetapi memungkinkan peningkatan kinerja berkelanjutan yang membuat baterai litium semakin berharga meskipun harganya mahal.
Optimasi Kimia dan Ilmu Material
Pada tingkat sel, penelitian yang sedang berlangsung berfokus pada peningkatan bertahap dalam kepadatan energi, siklus hidup, kemampuan pengisian cepat, dan kinerja suhu. Tim teknik kami bekerja sama dengan produsen sel untuk mengevaluasi teknologi material baru seperti anoda yang disempurnakan silikon yang dapat meningkatkan kapasitas hingga 20-40% dibandingkan dengan formulasi grafit tradisional. Material canggih ini biasanya memiliki harga premium selama komersialisasi awal, dengan biaya yang secara bertahap menurun seiring dengan peningkatan skala produksi.
Untuk aplikasi yang memprioritaskan kinerja suhu ekstrem, seperti sistem baterai suhu sangat rendah, formulasi elektrolit khusus menggabungkan paket aditif yang seimbang secara saksama yang mempertahankan mobilitas ion pada suhu serendah -40°C. Campuran elektrolit khusus ini menjalani pengujian ekstensif untuk memverifikasi kinerja suhu rendah sekaligus memastikan kompatibilitas dengan komponen sel lainnya selama masa pakai yang dimaksudkan. Pengembangan dan validasi formulasi khusus ini merupakan investasi signifikan yang memengaruhi biaya produk tetapi memberikan kinerja luar biasa dalam lingkungan yang menantang.
Peningkatan keamanan melalui ilmu material merupakan area penelitian aktif lainnya. Material pemisah dengan lapisan keramik atau sifat penghentian termal intrinsik menambah biaya komponen tetapi secara dramatis meningkatkan keamanan tingkat sel dengan memberikan perlindungan tambahan terhadap hubungan arus pendek internal. sistem baterai keamanan tinggi untuk aplikasi medis menggabungkan pemisah premium ini meskipun biaya tambahannya 30-40% dibandingkan bahan standar, karena peningkatan keamanannya membenarkan biaya tambahan untuk aplikasi kritis.
Inovasi Proses Manufaktur
Peningkatan berkelanjutan dalam teknik manufaktur mendorong peningkatan kualitas dan pengurangan biaya secara bertahap untuk baterai litium. Mitra produksi kami menerapkan teknologi seperti pemotongan laser untuk bahan elektroda, mengurangi variasi dimensi sekaligus menghilangkan risiko kontaminasi yang terkait dengan alat pemotong mekanis. Sistem inspeksi optik otomatis dengan algoritma pembelajaran mesin mendeteksi cacat halus yang mungkin luput dari pengamatan manusia, memastikan kualitas yang konsisten sekaligus mengurangi biaya tenaga kerja.
Otomasi perakitan terus berkembang, dengan robotika khusus menangani operasi yang semakin rumit yang sebelumnya terbatas pada pemrosesan manual. Inovasi manufaktur ini membutuhkan investasi modal yang signifikan tetapi secara bertahap mengurangi biaya produksi melalui peningkatan hasil, pengurangan kebutuhan tenaga kerja, dan peningkatan konsistensi. Untuk format sel yang mapan seperti sel silinder 18650 yang digunakan dalam banyak sistem baterai kami, peralatan produksi telah berevolusi melalui beberapa generasi, masing-masing memberikan peningkatan tambahan dalam efisiensi biaya.
Peningkatan efisiensi energi dalam proses produksi merupakan area fokus lainnya. Operasi pengeringan elektroda secara tradisional mengonsumsi energi yang besar, tetapi teknologi canggih seperti pengeringan dengan bantuan gelombang mikro dapat mengurangi konsumsi energi hingga 30-50% sekaligus meningkatkan kualitas pelapisan. Kebutuhan energi siklus pembentukan berkurang melalui protokol pengisian daya yang dioptimalkan yang mencapai hasil elektrokimia yang sama dengan input energi yang berkurang. Peningkatan proses ini secara bertahap mengurangi biaya produksi sekaligus meningkatkan jejak lingkungan dari produksi baterai.
Evolusi Sistem Manajemen Baterai
Sistem elektronik yang mengendalikan baterai litium terus dikembangkan untuk meningkatkan fungsionalitas sekaligus mengurangi biaya komponen. Desain BMS awal menggunakan komponen diskret untuk fungsi pemantauan dan perlindungan tegangan, sementara sistem saat ini mengintegrasikan fungsi-fungsi ini ke dalam IC khusus yang mengurangi jumlah komponen dan kebutuhan ruang papan. Solusi terintegrasi ini meningkatkan keandalan melalui titik koneksi yang berkurang sekaligus menurunkan biaya produksi melalui perakitan yang disederhanakan.
Kita desain BMS generasi terbaru menerapkan algoritme canggih yang beradaptasi dengan karakteristik penuaan baterai, mempertahankan kinerja optimal sepanjang masa pakai. Pendekatan pembelajaran mesin menganalisis pola penggunaan untuk mengoptimalkan profil pengisian daya untuk aplikasi tertentu, yang berpotensi memperpanjang masa pakai siklus hingga 15-25% dibandingkan dengan sistem manajemen parameter tetap. Peningkatan perangkat lunak ini menambah biaya pengembangan tetapi memberikan nilai substansial melalui peningkatan umur dan kinerja baterai.
Fitur konektivitas nirkabel semakin banyak muncul dalam sistem baterai modern, yang memungkinkan pemantauan jarak jauh, diagnostik, dan bahkan pembaruan firmware pada baterai yang digunakan. Meskipun kemampuan ini menambah biaya komponen melalui penambahan modul Bluetooth, WiFi, atau komunikasi seluler, kemampuan ini menciptakan nilai dengan memungkinkan pemeliharaan preventif dan pengoptimalan kinerja di seluruh siklus masa pakai baterai. Bagi klien komersial kami yang menggunakan armada besar peralatan bertenaga baterai, fitur baterai yang terhubung ini memberikan manfaat operasional substansial yang sepadan dengan biaya tambahannya.
Kesimpulan: Perkembangan Nilai Proposisi Baterai Lithium
Biaya yang lebih tinggi yang terkait dengan teknologi baterai litium mencerminkan material yang canggih, proses produksi yang rumit, sistem kontrol yang canggih, dan persyaratan kepatuhan regulasi yang diperlukan untuk menghasilkan kinerja yang luar biasa. Seperti yang telah kita bahas, setiap komponen rantai nilai baterai litium melibatkan teknologi khusus dan rekayasa presisi yang berkontribusi terhadap biaya produksi keseluruhan. Namun, evolusi berkelanjutan dari teknologi ini secara bertahap meningkatkan proposisi nilai melalui peningkatan kinerja dan pengurangan biaya tambahan.
Untuk aplikasi mulai dari elektronik portabel hingga kendaraan listrik dan penyimpanan energi stasioner, baterai litium menghadirkan kemampuan yang tidak dapat dicapai dengan teknologi alternatif. Kombinasi kepadatan energi yang tinggi, siklus hidup yang sangat baik, persyaratan perawatan yang minimal, dan lintasan biaya yang menurun membuat baterai ini semakin kompetitif meskipun harga awalnya mahal. Di Vade Battery, kami berfokus pada pengoptimalan setiap aspek desain dan produksi baterai untuk memberikan nilai maksimum bagi persyaratan aplikasi tertentu, dengan menyeimbangkan kinerja, keamanan, keawetan, dan pertimbangan biaya.
Pasar baterai litium terus berkembang pesat, dengan terobosan penelitian yang terus-menerus memajukan batas kinerja sementara skala manufaktur secara bertahap mengurangi biaya produksi. Organisasi yang mengevaluasi solusi penyimpanan energi harus mempertimbangkan biaya akuisisi awal dan nilai jangka panjang, termasuk faktor-faktor seperti siklus hidup, persyaratan perawatan, efisiensi energi, dan manfaat operasional dari fitur-fitur canggih. Tim teknik kami mengkhususkan diri dalam menavigasi pertimbangan yang rumit ini untuk mengembangkan solusi baterai yang dioptimalkan untuk persyaratan aplikasi tertentu.
Untuk organisasi yang mengeksplorasi solusi baterai lithium khusus, kami mengundang Anda untuk hubungi tim teknik kami atau kirimkan persyaratan khusus melalui kami portal permintaan desain baterai lithiumSpesialis teknis kami dapat memberikan rekomendasi terperinci berdasarkan persyaratan aplikasi Anda, membantu Anda menavigasi pertimbangan antara kemampuan kinerja dan pertimbangan biaya untuk mengembangkan solusi penyimpanan energi yang optimal.