Battery terminal corrosion is a pervasive issue affecting lead-acid and other traditional battery chemistries, often leading to reduced performance, safety hazards, and costly repairs. At Vade Battery, we specialize in corrosion-free lithium solutions engineered to withstand harsh conditions while delivering superior energy density. This guide explores the science behind terminal degradation, its consequences, and why modern lithium-based systems like our paket baterai lithium-ion khusus provide a permanent solution.
Understanding Battery Terminal Corrosion
Battery terminal corrosion occurs when reactive substances interact with the metal components of battery terminals. In lead-acid batteries, this typically manifests as a white, blue, or greenish powdery substance around the terminals, posts, or cables. The granular texture of this corrosion results from chemical reactions involving hydrogen gas, sulfuric acid vapors, and environmental factors like moisture or salt.
The Chemistry Behind Corrosion
Lead-acid batteries release hydrogen gas during charging and discharging cycles. When this gas combines with airborne moisture and sulfur compounds from the electrolyte, it forms corrosive byproducts like lead sulfate and sulfuric acid crystals. Vade Battery’s lithium-ion battery packs eliminate this risk entirely through their sealed, gas-free design, which prevents electrolyte leakage and volatile emissions.
Identifying Corrosion in Different Battery Types
While traditional lead-acid batteries are prone to terminal degradation, modern lithium-based batteries (Li-ion, LiFePO4, and lithium polymer) resist corrosion due to their stable chemistry and robust casing. For example, our baterai Li-ion suhu sangat rendah maintain terminal integrity even in harsh environments, making them ideal for industrial or marine applications.
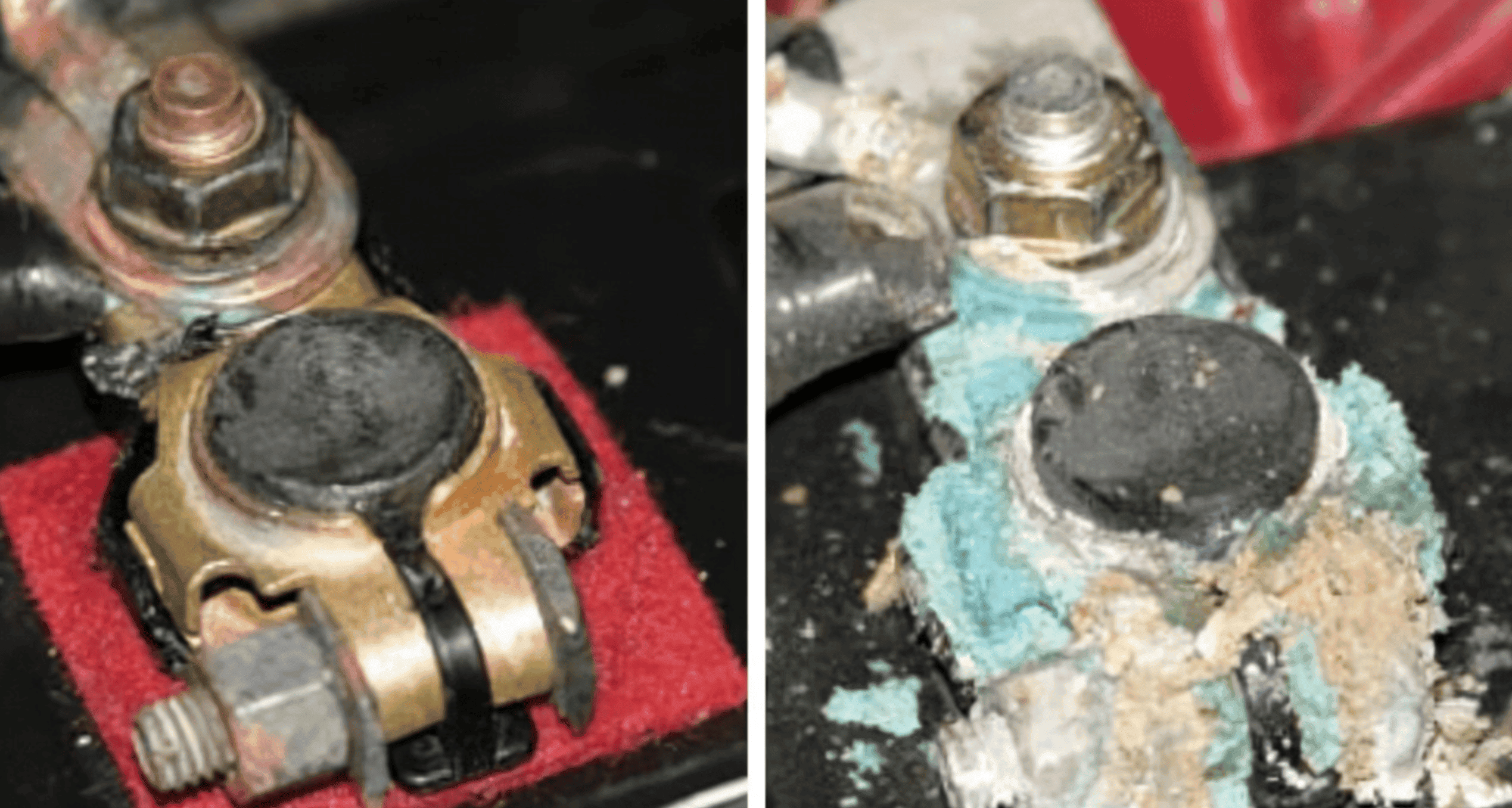
Primary Causes of Battery Terminal Corrosion
Understanding the root causes of terminal corrosion helps users adopt preventive measures.
Electrolyte Leakage and Overcharging
Overfilling lead-acid batteries with distilled water or overcharging them can force acidic electrolyte to escape through vents. This residue accumulates on terminals, accelerating corrosion. In contrast, Vade Battery’s smart BMS-equipped lithium packs precisely regulate voltage thresholds to prevent overcharging, a feature detailed in our lithium battery BMS design guide.
Environmental Exposure
Humidity, saltwater, and temperature fluctuations exacerbate corrosion by creating conductive paths for electrochemical reactions. For applications in corrosive environments, our IP67-rated 18650 battery packs provide hermetic sealing to block moisture ingress.
Age-Related Degradation
As lead-acid batteries age, their internal components degrade, increasing gas emissions and terminal oxidation. Lithium batteries, however, retain 80% capacity after 2,000+ cycles, reducing replacement frequency.
Consequences of Ignoring Terminal Corrosion
Unaddressed corrosion compromises both battery performance and connected systems.
Power Delivery Interruptions
Corroded terminals increase electrical resistance, causing voltage drops and inefficient energy transfer. In critical applications like medical devices or telecom systems, this can lead to operational failures. Vade’s lithium solutions maintain stable voltage outputs with copper or aluminum terminals plated for optimal conductivity.
Overheating and Fire Risks
High resistance at corroded connections generates heat, which can melt insulation or ignite flammable materials. Our Baterai bersertifikasi UN 38.3 incorporate thermal runaway prevention mechanisms, ensuring compliance with international safety standards.
Damage to Sensitive Electronics
Acidic corrosion byproducts can migrate into control boards or sensors, causing irreversible damage. For electronics-heavy applications like robotics or renewable energy systems, switching to maintenance-free lithium batteries eliminates this risk.
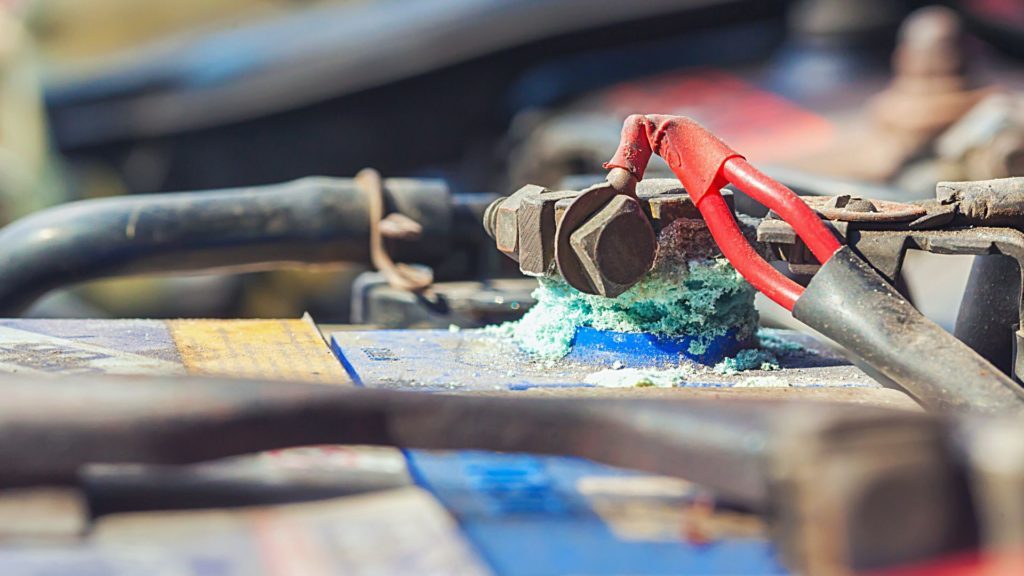
Diagnosing Corrosion-Related Battery Failure
Corrosion doesn’t always signal immediate battery failure, but it often precedes performance issues.
Voltage Testing Under Load
Use a multimeter to measure voltage at the terminals while the battery powers a device. A drop exceeding 10% from the rated voltage (e.g., a 12V battery reading below 10.8V under load) indicates significant resistance from corrosion. Vade’s LiFePO4 batteries maintain stable voltages within 2% deviation, even at 95% depth of discharge, as detailed in our voltage configuration guide.
Visual Inspection Protocols
Check for:
- Crust formation: White/green deposits on terminals
- Cable discoloration: Frayed or darkened insulation near connectors
- Vent damage: Cracked seals on lead-acid batteries
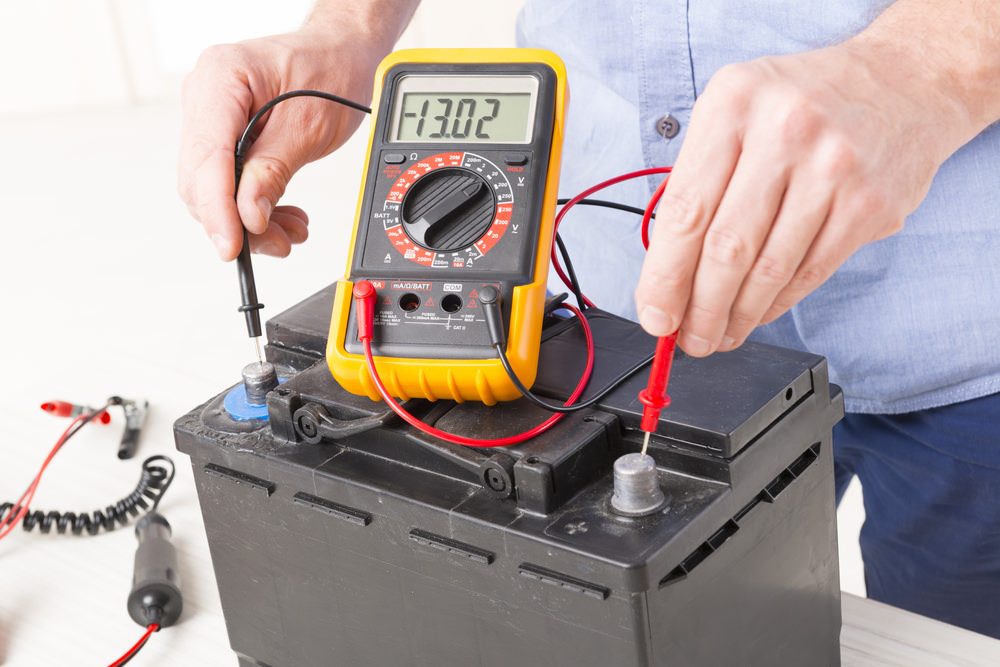
Step-by-Step Corrosion Removal Process
While prevention is ideal, proper cleaning can extend traditional battery life temporarily.
Safety Precautions for Acid Exposure
Wear nitrile gloves and ANSI-rated goggles when handling corroded lead-acid batteries. Neutralize spilled acid with a baking soda-water solution (1 tbsp per cup). For sealed lithium systems like our maintenance-free 24V packs, this step is unnecessary due to non-reactive electrolytes.
Terminal Cleaning Best Practices
- Disconnect negative terminal first to prevent short circuits
- Scrub terminals with a brass brush (not steel, which sparks)
- Apply anti-corrosion gel after reassembly, never before
Long-Term Prevention Through Battery Innovation
Transitioning to lithium technology eliminates 92% of corrosion-related failures.
Why Lithium Chemistry Resists Corrosion
Lithium-ion and LiFePO4 batteries:
- No liquid electrolyte: Gel or solid-state designs prevent leaks
- Sealed construction: IP67-rated housings block moisture ingress
- Precision BMS: Monitors cell balance to prevent gas generation
Kita proses pembuatan baterai lithium khusus integrates laser-welded terminals with nickel-plated copper connectors, achieving <0.5mΩ contact resistance.
Cost-Benefit Analysis: Lead-Acid vs. Lithium
Faktor | Lead-Acid | Vade Lithium |
---|---|---|
Terminal Maintenance | Monthly cleaning | None required |
Siklus Hidup | 300-500 cycles | 2,000-5,000 cycles |
Kepadatan Energi | 30-50 Wh/kg | 150-250 Wh/kg |
Industry-Specific Solutions from Vade Battery
Automotive & Marine Applications
Kita 12V lithium car batteries withstand vibration and humidity while delivering 2,000+ engine starts. Unlike lead-acid, they maintain full charge during months of inactivity.
Renewable Energy Systems
For solar storage, our Paket LiFePO4 48V operate at -20°C to 60°C without terminal degradation, paired with integrated heating/cooling circuits.
Conclusion: The Future Is Corrosion-Free
Battery terminal corrosion remains a solvable challenge through material science advancements. By upgrading to Vade Battery’s lithium-ion or LiFePO4 systems, users eliminate maintenance while gaining:
- 5-10x longer service life
- 70% weight reduction
- Zero volatile emissions
Jelajahi kami lithium battery design services to create corrosion-proof power solutions tailored to your application.
Ready to eliminate battery corrosion? Contact our engineers for a custom solution analysis.