As Chief Production Engineer at VADE Battery with over 15 years in the industry, I’m proud to showcase our proprietary 12-step manufacturing process that sets our batteries apart. At VADE, we’ve been specializing in custom rechargeable battery solutions since 2008, delivering over 5 million units of 18650, Li-ion, Lithium polymer, and LiFePO4 battery packs to customers in 43 countries worldwide. Our batteries consistently achieve a 99.7% reliability rate and 25% longer lifespan compared to industry averages, thanks to our meticulous quality control and advanced production techniques.
The Foundation: Premium Materials
First, we source our battery cells and protection boards from external suppliers. VADE batteries use cells from first-tier brand suppliers – the same quality cells used in Apple’s original batteries. Our protection boards implement Texas Instruments (TI) solutions, ensuring they remain fully functional even after iOS system updates.
The Birth of Excellence: Our 12-Step Manufacturing Process
Material Inspection
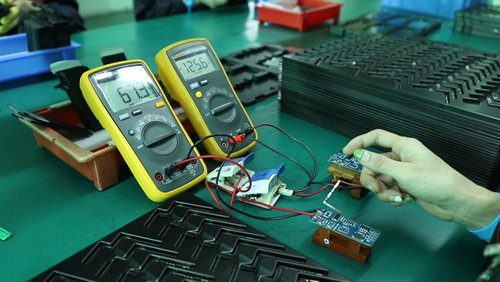
All purchased materials undergo rigorous incoming inspection using specialized equipment to verify specifications and quality parameters. Substandard materials are immediately rejected, establishing the first critical quality control barrier in our production process. This inspection includes verification of chemical composition, physical properties, and dimensional accuracy.
Battery Cell Capacity Sorting
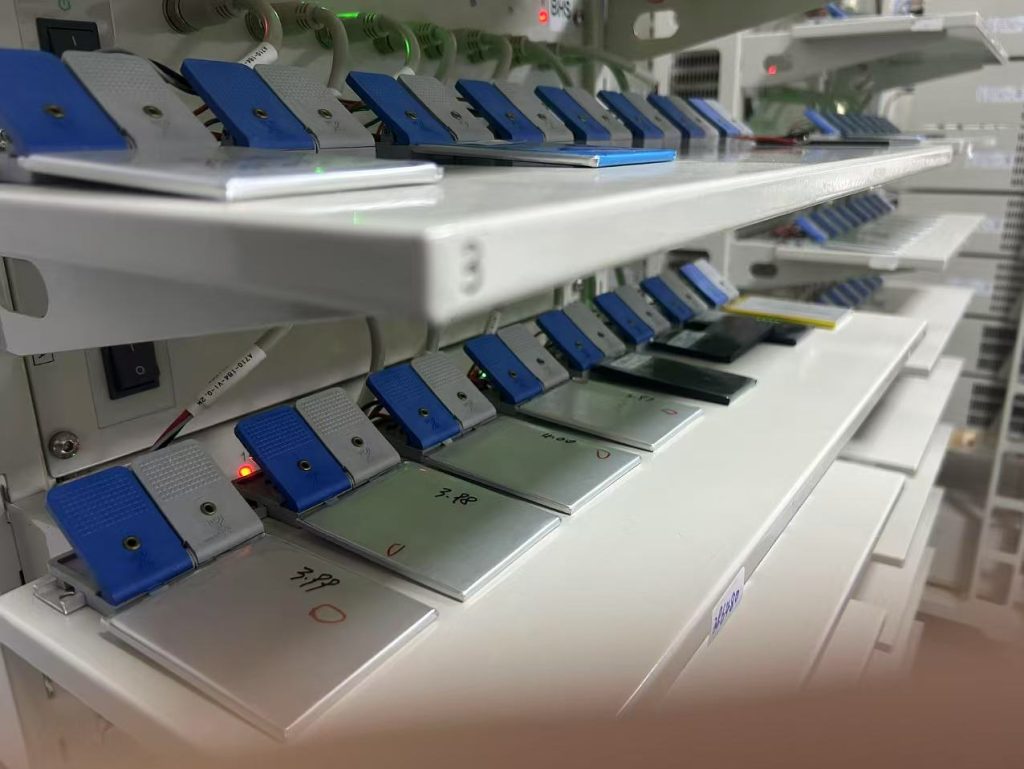
The battery cells undergo a capacity sorting process, known in the industry as “formation”. At VADE, we operate 15 sorting cabinets capable of simultaneously processing up to 12,000 batteries. This electrochemical activation step forms the Solid Electrolyte Interphase (SEI) on the anode during initial charging and discharging cycles, ensuring consistent performance across all our products.
Automated Cell Loading
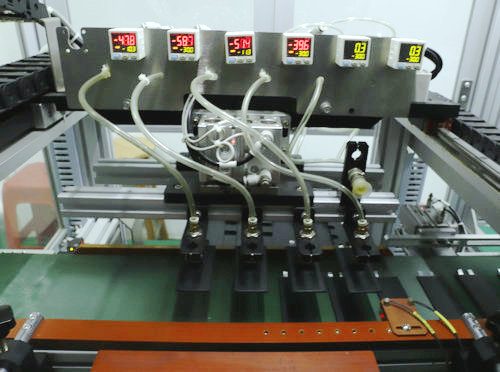
After inspection and sorting, the cells enter our automated production line. Using precision robotics and conveyor systems, each cell is accurately positioned for subsequent processing. This automation minimizes human error and contamination risks while maximizing throughput efficiency.
Nickel Tab Cutting
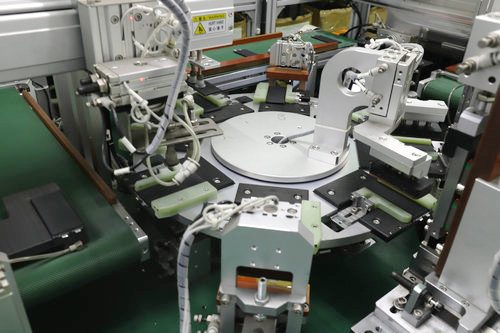
Next comes the precision cutting of nickel tabs. These conductive metal strips must be trimmed to exact specifications – neither too long nor too short – to ensure proper electrical connections within the battery. Advanced laser cutting technology maintains tolerances within micrometers, essential for optimal performance and safety.
Laser Spot Welding
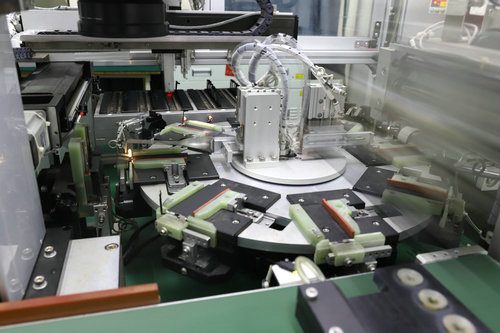
This critical step joins the protection board to the battery cell through laser spot welding. Our high-precision equipment creates molecular-level bonds between components, ensuring minimal heat-affected zones while maximizing connection strength and electrical conductivity. These welds are then tested for mechanical integrity and electrical resistance.
Insulation Application
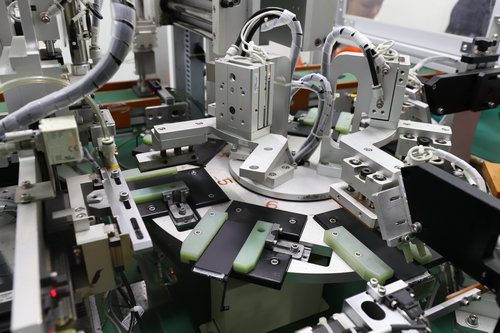
We apply specialized insulation adhesive to protect exposed wires and connections, preventing potential short circuits. This dielectric material provides essential electrical isolation while maintaining thermal stability across varying operating conditions, significantly reducing safety risks.
Bracket Installation
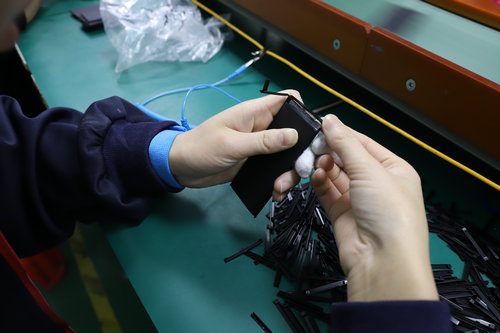
This stage requires manual operation by our skilled technicians. While installing the structural brackets, our staff simultaneously conduct visual inspections of previous automated processes, adding another layer of quality assurance. This human oversight complements automated systems, catching subtle defects that machines might miss.
Protective Head Paper Application
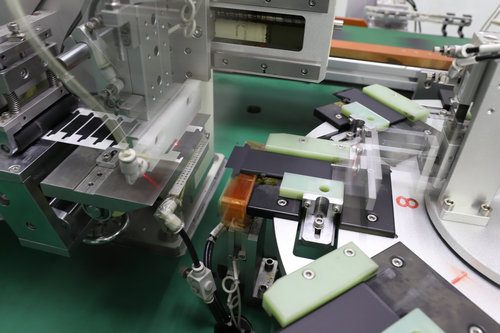
We apply a specialized protective paper to cover the battery head. This multi-functional material provides both mechanical protection and electrical insulation, enhancing both aesthetic appearance and operational safety. The material is precisely sized and positioned to ensure complete coverage of sensitive components.
Performance Testing
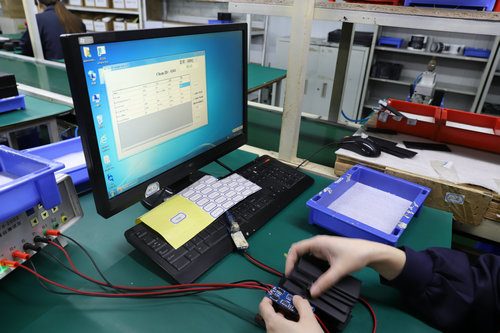
Each battery undergoes comprehensive performance testing using calibrated equipment to measure critical parameters including voltage, internal resistance, capacity, self-discharge rate, and cycle performance. Only batteries meeting our stringent specifications advance to the next stage; others are segregated for analysis and recycling.
Appearance Inspection
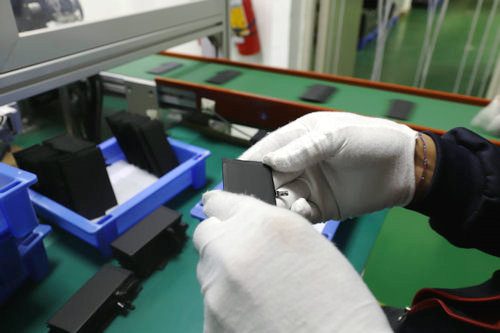
Our quality control team conducts meticulous visual inspections for physical defects such as dents, deformations, or scratches. This 100% inspection protocol employs both direct examination and magnification techniques to identify even microscopic imperfections that could impact performance or safety.
Pressure Leak Detection
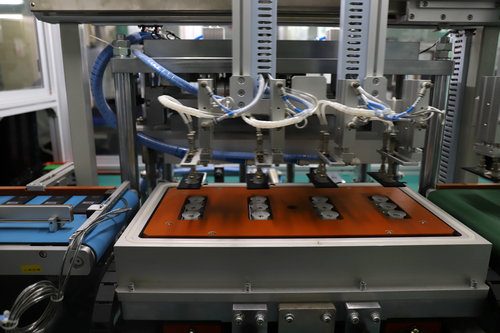
We employ advanced positive pressure leak detection equipment that identifies imperceptible defects capable of causing battery swelling or thermal issues. This technology applies controlled pressure to the sealed battery while monitoring for pressure changes that would indicate microscopic leaks, significantly enhancing safety assurance.
Packaging and Shipping
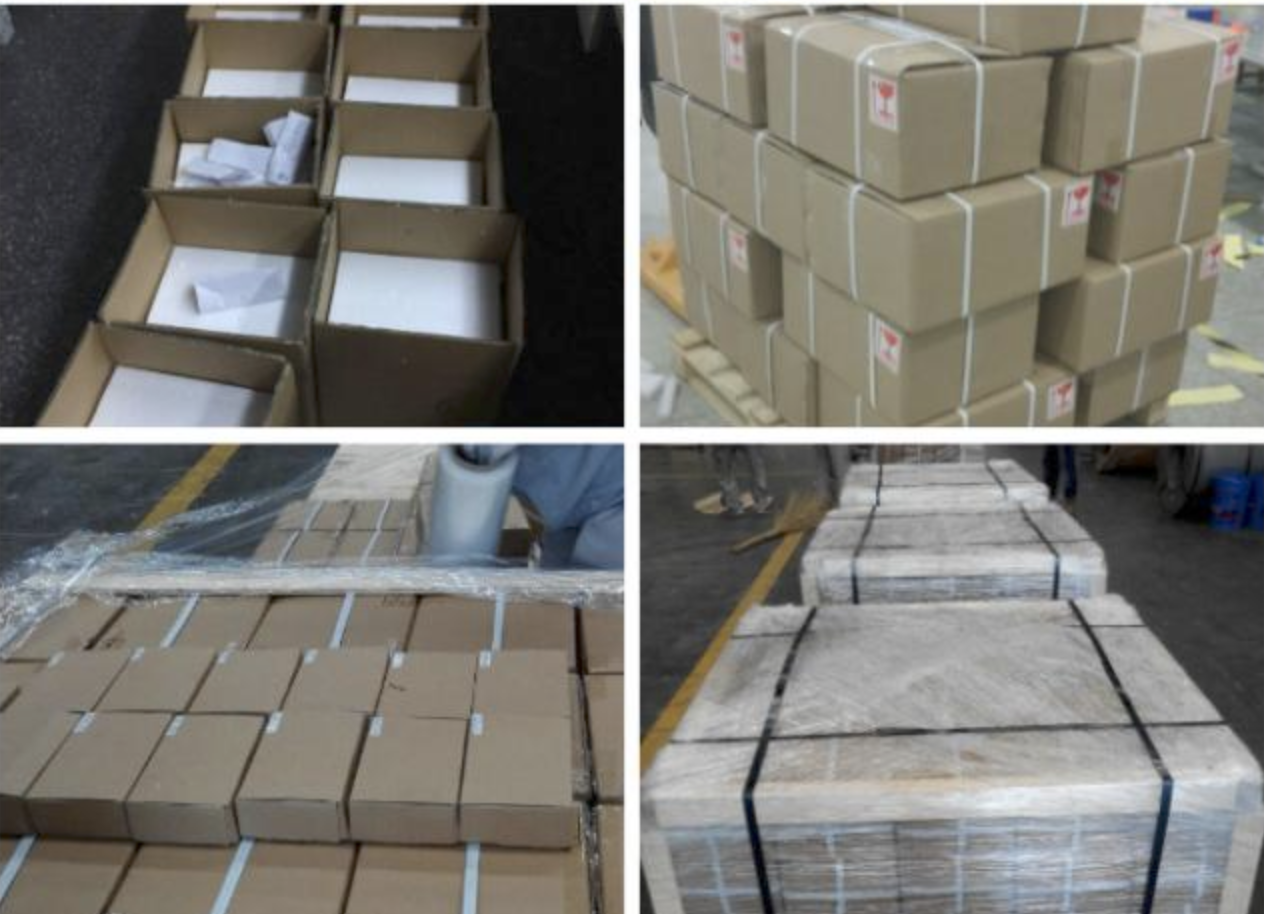
Approved batteries undergo careful packaging according to international safety standards for lithium battery transportation. Each battery is placed in custom-designed blister packs with impact protection, sealed in retail boxes with tamper-evident features, and packed in UN-certified shipping cartons that comply with global hazardous material regulations.
The VADE Quality Promise
Every VADE battery undergoes this rigorous manufacturing journey before leaving our ISO 9001:2015 and UL-certified factory. Our statistical process control system maintains defect rates below 0.3% – significantly outperforming the industry average of 1.2%. We stand behind our products with a comprehensive 24-month warranty, twice the industry standard.
Our commitment to excellence extends beyond performance to sustainability. In 2024, we reduced our manufacturing carbon footprint by 35% through energy-efficient equipment upgrades and responsible material sourcing. Our battery recycling program has already processed over 500,000 units, recovering 92% of valuable materials.
From our RoHS and REACH-compliant materials to our IEC 62133-certified safety protocols, we prioritize quality, safety, and environmental responsibility in every battery we produce. Our customers – including leading medical device manufacturers, automotive suppliers, and consumer electronics brands – trust VADE batteries when reliability cannot be compromised.
For detailed specifications about our battery technologies, download our technical whitepapers on lithium-ion battery basics or explore our selection of custom lithium battery manufacturing processes. Contact our engineering team today to discuss your specific battery requirements.