-
29 W. Pawnee, Bloomfield, NJ 07003
¿Por qué es tan caro fabricar baterías de litio?
Las baterías de litio alimentan todo, desde teléfonos inteligentes hasta vehículos eléctricos, y representan una de las tecnologías de almacenamiento de energía más transformadoras de nuestro tiempo. Sin embargo, a pesar de todas sus ventajas en densidad energética y rendimiento, las baterías de litio tienen un precio significativamente superior en comparación con las baterías tradicionales. En Vade Battery, nos especializamos en el desarrollo Soluciones de baterías de litio personalizadas que van desde compactos Paquetes de baterías de 7,4 V Para electrónica de consumo y de grado industrial. Sistemas de almacenamiento de energía de 72 VNuestro equipo de ingeniería trabaja diariamente con los factores de costo que influyen en la producción de baterías de litio, desarrollando estrategias para optimizar el rendimiento y al mismo tiempo controlar los gastos. Este análisis integral explora los principales factores que contribuyen a los costos de las baterías de litio y explica las realidades de fabricación detrás de sus precios premium.
Costos de las materias primas y factores de la cadena de suministro
Los componentes fundamentales de las baterías de litio representan el mayor costo de su producción. Según el análisis de costos de 2023 del Departamento de Energía de EE. UU., las materias primas suelen representar entre el 50 y el 701 % del costo de fabricación de una batería de litio. Este gasto significativo se debe tanto al valor intrínseco de los materiales como a la compleja cadena de suministro global necesaria para procesarlos y entregarlos a los fabricantes de baterías.
Metales críticos y su dinámica de mercado
El litio en sí, a pesar de dar a estas baterías su nombre, generalmente comprende menos del 5% del total de materiales de la celda en peso. Sin embargo, el precio del carbonato de litio exhibe una volatilidad extrema, con tasas de mercado que fluctúan entre $15,000 y $80,000 por tonelada métrica durante los últimos cinco años según Benchmark Mineral Intelligence. Esta volatilidad afecta directamente nuestros costos de producción para todo, desde nuestros Serie de baterías de temperatura ultrabaja al estándar Sistemas de batería de 48 V.
Aún más importantes son los metales catódicos que determinan las características de rendimiento de una batería. El cobalto, un componente esencial en los cátodos NMC (níquel-manganeso-cobalto) de alta densidad energética, se comercializa habitualmente por encima de $30.000 por tonelada métrica. Casi 70% de la producción mundial de cobalto proviene de la República Democrática del Congo, lo que genera vulnerabilidades en la cadena de suministro y preocupaciones sobre el abastecimiento ético. El níquel, otro componente esencial de los cátodos, ha experimentado su propia volatilidad de precios, con precios spot que periódicamente superan los $20.000 por tonelada tras interrupciones del suministro.
Para aplicaciones que priorizan la vida útil prolongada y la seguridad sobre la densidad máxima de energía, a menudo implementamos LiFePO₄ (fosfato de hierro y litio) Química. Si bien esto reduce la dependencia del cobalto y el níquel, los procesos de fabricación especializados necesarios para los materiales de cátodos LFP introducen sus propios factores de costo. Los precursores de fosfato requieren un control preciso durante la síntesis para lograr una estructura cristalina adecuada, lo que contribuye a los gastos de producción incluso cuando se utilizan metales básicos más abundantes.
Consideraciones sobre el material del separador y del electrolito
Más allá de los metales visibles que más llaman la atención, los materiales del electrolito y del separador representan componentes críticos con importantes implicaciones económicas. Las soluciones electrolíticas de alta pureza suelen utilizar sal de hexafluorofosfato de litio (LiPF₆) en disolventes orgánicos, y los costes de fabricación se ven afectados por los niveles de pureza requeridos superiores a 99,991TP₆T para evitar reacciones secundarias que degradarían el rendimiento de la batería.
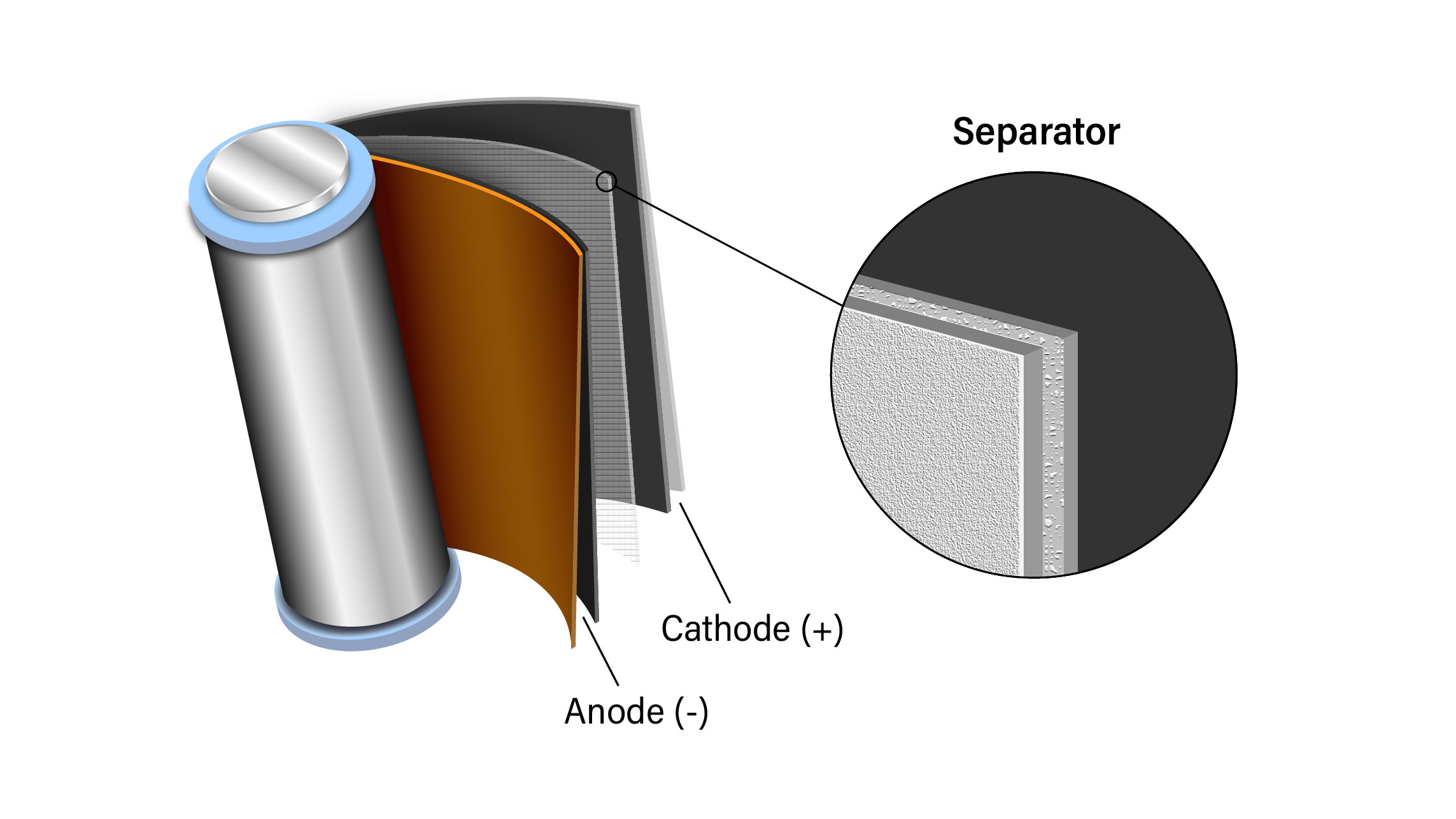
Los materiales separadores, que normalmente se fabrican a partir de películas microporosas especializadas de polietileno o polipropileno, requieren un control preciso del espesor (normalmente de 15 a 25 micrómetros) y una porosidad uniforme. Estas películas separadoras deben mantener la integridad mecánica y, al mismo tiempo, permitir el transporte de iones de litio entre electrodos. La fabricación de separadores con estas características requiere procesos especializados de extrusión y estiramiento que añaden un coste significativo a la celda final. Paquetes de baterías de 51,8 V de alto rendimientoUtilizamos separadores revestidos de cerámica que mejoran la estabilidad térmica a temperaturas de hasta 180 °C, pero agregan aproximadamente 15-201 TP3T al componente de costo del material.
Vulnerabilidades de la cadena de suministro global
La concentración geográfica del procesamiento de materiales para baterías genera presiones adicionales de costos debido a las primas de riesgo en la cadena de suministro. Según el informe de 2023 de la Agencia Internacional de la Energía sobre minerales críticos, China procesa aproximadamente 601 TP³T del litio mundial, 701 TP³T de cobalto y 801 TP³T de grafito utilizado en ánodos de baterías. Esta concentración genera vulnerabilidades estratégicas para los fabricantes de baterías fuera de estas regiones.
Mitigamos estos riesgos de la cadena de suministro mediante asociaciones estratégicas con múltiples proveedores de materiales calificados en diferentes regiones, aunque la diversificación tiene sus propias implicaciones de costos. Los sistemas de control de calidad deben duplicarse entre los proveedores, y las pruebas de calificación para nuevas fuentes de materiales se suman a los gastos de investigación y desarrollo. Los costos de transporte también influyen significativamente en los gastos de material, con requisitos de manipulación especializados para materiales de electrodos reactivos y componentes de electrolitos volátiles. Estas consideraciones logísticas se vuelven cada vez más importantes para nuestros sistemas de formato más grande como nuestro Paquetes de baterías de 72 V de grado industrial que requieren volúmenes sustanciales de material.
Procesos de fabricación complejos
La transformación de materias primas en celdas funcionales de baterías de litio requiere procesos de fabricación sofisticados con estrictos requisitos de precisión. Estas técnicas de producción especializadas contribuyen significativamente al costo final de las baterías de litio, y la complejidad de la fabricación representa aproximadamente entre 20 y 301 TP3T de los gastos de producción.
Requisitos de precisión en la producción celular
La fabricación de celdas de baterías de litio exige una precisión extraordinaria en prácticamente cada paso del proceso. El recubrimiento de electrodos es una de las operaciones más críticas, ya que requiere la aplicación uniforme de materiales activos sobre los colectores de corriente metálicos (cobre para los ánodos, aluminio para los cátodos), con variaciones de espesor que suelen mantenerse por debajo de ±2 micrómetros. Esta precisión influye directamente en la capacidad de la celda, la resistencia interna y el ciclo de vida.
Nuestro Paquetes de baterías basados en celdas 18650 Benefíciese de décadas de perfeccionamiento en la fabricación de este formato cilíndrico, pero la producción aún requiere maquinaria sofisticada para enrollar electrodos con un control de tensión constante. Para nuestros formatos de celdas prismáticas y de bolsa personalizados que se utilizan en aplicaciones con limitaciones de espacio, la complejidad de fabricación aumenta aún más, ya que estas geometrías requieren equipos especializados para apilar o plegar conjuntos de electrodos con una alineación precisa.
Las operaciones de acabado de celdas añaden un nivel adicional de complejidad a la fabricación. El proceso de llenado de electrolito debe realizarse en entornos extremadamente secos (normalmente con una humedad inferior a 100 ppm) para evitar la contaminación que podría degradar el rendimiento. El ciclo de formación (las secuencias iniciales de carga y descarga que establecen la capa de interfase sólido-electrolito [ISE]) requiere un control preciso de los perfiles de corriente y voltaje durante periodos de entre 24 y 72 horas, con un consumo energético significativo y la necesidad de equipos especializados.
Requisitos de sala limpia y control de calidad
Las baterías de litio exigen entornos de fabricación con estándares de limpieza excepcionales. Partículas tan pequeñas como 10 micrómetros pueden crear cortocircuitos internos o acelerar los mecanismos de degradación dentro de las celdas. Nuestros socios de producción mantienen instalaciones de sala limpia ISO Clase 7-8 con sofisticados sistemas de filtración de aire, prendas de trabajo especializadas y rigurosos protocolos de control de la contaminación que agregan costos operativos sustanciales a la fabricación de baterías.
El control de calidad representa otro gasto significativo en la producción de baterías de litio. Cada celda se somete a múltiples puntos de inspección, incluida la inspección óptica automatizada de los electrodos, el examen con rayos X para detectar defectos internos y las mediciones de peso de precisión para verificar el llenado de electrolito. Sistemas de baterías de 46,8 V de misión crítica Utilizadas en aplicaciones médicas, las células 100% se someten a pruebas adicionales que incluyen un monitoreo extendido de voltaje de circuito abierto para detectar defectos de fabricación sutiles que podrían afectar el rendimiento.
Estas medidas de control de calidad añaden costes directos a través de equipos y mano de obra especializados, pero aportan un valor sustancial al evitar fallos en el campo y mejorar la seguridad. Nuestros datos internos indican que los procesos de selección exhaustivos identifican aproximadamente entre el 2 y el 51 % de las células con defectos menores que podrían provocar fallos prematuros o una reducción del rendimiento, lo que justifica el gasto de producción adicional a través de una mayor fiabilidad.
Desafíos de automatización y escalabilidad
Si bien la automatización ha reducido algunos costos de fabricación, los requisitos de precisión de la producción de baterías de litio limitan el potencial de reducción de costos mediante la mecanización únicamente. Los sistemas de manipulación de electrodos deben manejar materiales extremadamente delgados y que se dañan fácilmente con un control de tensión constante. Las operaciones de ensamblaje requieren herramientas especializadas para tareas como la soldadura de lengüetas, donde los sistemas de soldadura ultrasónica o láser unen las lengüetas del colector de corriente con tolerancias medidas en micrómetros.
El desafío de escalar la producción representa otro factor de costo en la fabricación de baterías de litio. A diferencia de muchas tecnologías donde las economías de escala siguen curvas de costos predecibles, la producción de baterías de litio requiere un equilibrio cuidadoso entre el rendimiento y el control de calidad. La velocidad de producción aumenta el riesgo de introducir defectos sutiles que pueden no manifestarse hasta después de que las celdas entren en servicio. Sistemas de baterías de 24 V de alta confiabilidad utilizado en aplicaciones de infraestructura crítica, priorizamos los procesos de fabricación que enfatizan la consistencia sobre el rendimiento máximo, aceptando la prima de costo asociada para garantizar la confiabilidad del rendimiento.
El consumo de energía durante la fabricación añade otro gasto significativo. Los entornos secos necesarios para el ensamblaje de las celdas suelen mantener una humedad relativa inferior a 1%, lo que requiere importantes sistemas de deshumidificación. El ciclo de formación consume una cantidad considerable de electricidad, y los pasos de procesamiento térmico para el secado de los electrodos y la activación del electrolito requieren un control preciso de la temperatura durante períodos prolongados. Estos procesos de alto consumo energético contribuyen a los costos de producción y, al mismo tiempo, influyen en la huella de carbono de la fabricación de baterías.
Sistemas de gestión de baterías y características de seguridad
La sofisticada electrónica necesaria para gestionar las baterías de litio representa una parte sustancial de su estructura de costes total. A diferencia de las baterías más sencillas, las celdas de litio requieren un control y una supervisión cuidadosos para garantizar un funcionamiento seguro y eficiente durante toda su vida útil. Estos sistemas de protección suelen representar entre el 15 y el 25 % del coste total del paquete, según su complejidad y funcionalidad.
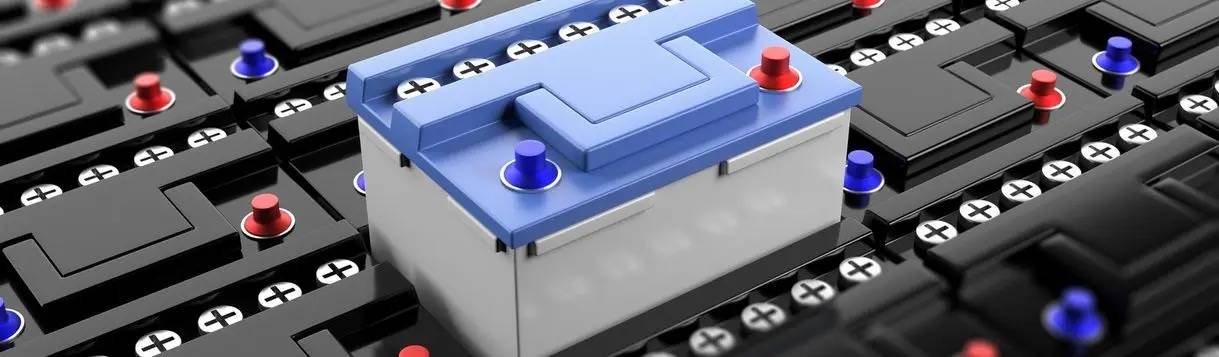
El papel fundamental del BMS en las baterías de litio
Cada paquete de batería de litio que producimos incorpora un Sistema de gestión de baterías (BMS) Adaptados a los requisitos específicos de la aplicación. Estos sistemas de control electrónico cumplen múltiples funciones críticas: evitar que las celdas superen los límites de voltaje seguros durante la carga, monitorear las tasas de descarga para evitar condiciones de sobrecorriente dañinas, equilibrar los niveles de carga entre celdas individuales y rastrear la temperatura en múltiples puntos dentro del paquete.
Para nuestro Reemplazos de baterías de litio de 12 V En equipos industriales, implementamos diseños BMS que mantienen el desequilibrio de voltaje de las celdas por debajo de los 50 mV durante todo el ciclo de descarga, lo que extiende significativamente la vida útil en comparación con los sistemas con protección básica. Los costos de desarrollo de estos sistemas de control especializados incluyen tanto la ingeniería de hardware como el desarrollo extenso de firmware, con algoritmos patentados refinados a través de miles de ciclos de prueba en condiciones operativas variables.
La complejidad del BMS aumenta con el voltaje y la capacidad de la batería. sistemas de alto voltaje de 72 V Incorporan capas de protección redundantes con monitoreo independiente de sobretemperatura, múltiples sensores de corriente y monitoreo de aislamiento sofisticado para detectar la degradación del aislamiento antes de que pueda crear riesgos de seguridad. Estas características avanzadas requieren componentes de mayor calidad, incluidos microcontroladores calificados para automoción, convertidores analógicos a digitales de precisión y múltiples capas de aislamiento entre los circuitos de detección y control.
Especificaciones y costos de circuitos de protección
Los componentes de protección de un paquete de baterías de litio deben cumplir con estándares de confiabilidad excepcionales mientras funcionan en condiciones difíciles. Los elementos de detección de corriente deben medir con precisión flujos que van desde miliamperios durante el modo de espera hasta cientos de amperios durante las cargas pico en nuestros sistemas de alta potencia. El monitoreo de temperatura requiere redes de termistores o sensores de temperatura digitales ubicados en ubicaciones estratégicas determinadas a través de modelado térmico y verificadas con imágenes infrarrojas durante las pruebas de calificación.
Función de protección | Rango de costo de componentes típico | Especificación de rendimiento |
---|---|---|
Monitoreo de voltaje de celda | $0,25-1,50 por celda | Precisión de ±10 mV, frecuencia de muestreo de 50 ms |
Detección de corriente | $3.50-20.00 por paquete | Precisión de ±1%, tiempo de respuesta de aislamiento de 500 V, fuga de <250 μA |
Interfaz de comunicación | $5.00-35.00 por paquete | Bus CAN, Modbus o protocolo propietario |
Para aplicaciones que requieren la máxima tolerancia a fallos, como nuestra Paquetes de baterías de 36 V de grado médicoImplementamos sistemas de monitoreo redundantes dobles con referencias de voltaje independientes y microcontroladores separados que verifican las mediciones. Estas arquitecturas redundantes agregan costos de componentes y al mismo tiempo mejoran significativamente la seguridad para aplicaciones críticas donde las fallas no son una opción.
La inteligencia incorporada en los diseños modernos de BMS se extiende más allá de las funciones de seguridad básicas para incluir características que mejoran la longevidad y el rendimiento de la batería. Los algoritmos avanzados de estimación del estado de carga combinan mediciones de voltaje con conteo de culombios y seguimiento de impedancia para brindar información precisa sobre la capacidad durante todo el ciclo de descarga. Las interfaces de control de gestión térmica regulan los sistemas de enfriamiento activo en aplicaciones de alta descarga, lo que preserva la vida útil de la celda al evitar variaciones de temperatura durante casos de uso exigentes.
Requisitos de prueba y certificación
Los requisitos regulatorios para la seguridad de las baterías de litio representan otro factor de costo significativo. Todos los diseños de baterías que fabricamos se someten a pruebas de certificación exhaustivas según normas como la UN 38.3 para seguridad en el transporte, la IEC 62133 para seguridad de celdas y la UL 1642/2054 para diversas aplicaciones. Estos protocolos de prueba incluyen condiciones de uso extremo, como pruebas de aplastamiento, resistencia a la penetración, ciclos térmicos entre -40 °C y +75 °C, y evaluación de cortocircuito.
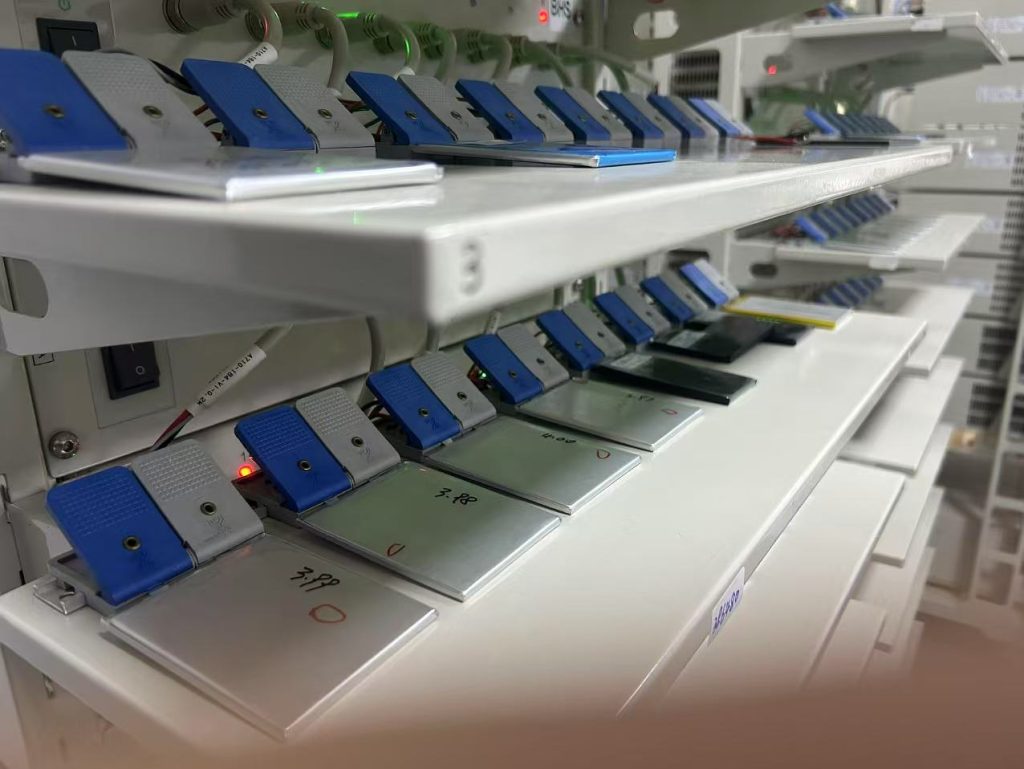
Para nuestro Sistemas de baterías de 48 V enfocados en el transporte, pueden aplicarse normas adicionales como ECE R100 (para aplicaciones automotrices) o EN 50604 (para vehículos eléctricos ligeros), lo que requiere pruebas especializadas adicionales. Estos procesos de certificación suelen costar entre $15,000 y $50,000 por modelo de batería, según la complejidad y los requisitos de la aplicación. Si bien estos gastos se amortizan en los volúmenes de producción, contribuyen significativamente a los costos de desarrollo de soluciones de baterías especializadas.
Las pruebas internas se extienden más allá de los requisitos normativos para incluir la validación específica de la aplicación. Para las baterías destinadas a entornos con mucha vibración, realizamos pruebas extensas en agitadores electrodinámicos que replican las condiciones de campo aceleradas para comprimir años de servicio en semanas de evaluación de laboratorio. Las cámaras ambientales personalizadas simulan temperaturas extremas, ciclos de humedad y exposición a la niebla salina para aplicaciones marinas. Estos programas de pruebas integrales aumentan los gastos de desarrollo, pero garantizan que nuestras baterías brinden un rendimiento confiable durante toda su vida útil prevista.
Gastos de embalaje e integración mecánica
Para convertir las celdas de litio individuales en sistemas de baterías funcionales se requieren tecnologías de empaquetado sofisticadas que protejan los componentes electroquímicos y permitan un funcionamiento seguro y confiable en diversos entornos. Estos elementos de integración mecánica suman 10-15% a los costos generales de la batería, pero brindan protección y funcionalidad esenciales que afectan directamente el rendimiento y la seguridad.
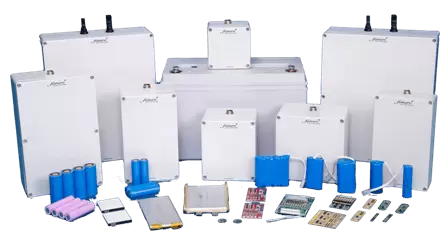
Materiales de cerramiento y fabricación
La carcasa protectora para baterías de litio debe satisfacer múltiples requisitos exigentes al mismo tiempo. Sistemas de baterías industriales de 51,2 VLas carcasas suelen utilizar aleaciones de aluminio con espesores de pared de entre 1,5 y 3 mm, lo que proporciona una excelente conductividad térmica, blindaje electromagnético y protección mecánica. Los procesos de mecanizado controlados por computadora, con tolerancias de ±0,1 mm, garantizan un ajuste preciso de los componentes. Sin embargo, estas técnicas de fabricación suponen un coste considerable en comparación con los procesos de moldeo de plástico más sencillos, utilizados para aplicaciones menos exigentes.
Las aplicaciones con exposición ambiental extrema requieren medidas de protección adicionales. Cajas con clasificación IP67 Se someten a pruebas de presión para verificar la exclusión de agua y polvo a profundidades de hasta 1 metro. Los materiales de junta especializados mantienen el sellado en rangos de temperatura de -40 °C a +85 °C, a la vez que resisten la degradación por la exposición a la luz ultravioleta y los contaminantes químicos. Estos sistemas de sellado avanzados incrementan el costo de los componentes y requieren una fabricación precisa para mantener las fuerzas de compresión dentro de los límites especificados.
El diseño estructural de los compartimentos de las baterías también debe tener en cuenta las diferencias de expansión térmica entre los componentes, el aislamiento de las vibraciones y la resistencia al impacto adecuadas para la aplicación. Nuestro equipo de ingeniería utiliza el análisis de elementos finitos para optimizar estos diseños, lo que reduce el uso de material y, al mismo tiempo, mantiene la integridad estructural. Para aplicaciones sensibles al peso, como equipos portátiles alimentados por nuestros Paquetes de baterías ligeras de 7,4 VImplementamos materiales de gabinete compuestos que reducen el peso hasta en 40% en comparación con las alternativas de aluminio, aunque estos materiales avanzados generalmente agregan 25-30% al componente de costo del gabinete.
Sistemas de gestión térmica
La gestión térmica eficaz representa uno de los desafíos de ingeniería más importantes en el diseño de baterías de litio. El rendimiento, la longevidad y la seguridad de las celdas dependen de mantener temperaturas de funcionamiento adecuadas, y cada composición química tiene rangos óptimos específicos. Para aplicaciones con requisitos de potencia modestos, puede ser suficiente la refrigeración pasiva mediante un espaciado estratégico de las celdas y materiales conductores térmicos, lo que agrega un costo mínimo al sistema general.
Sin embargo, las aplicaciones de alta descarga como nuestra Sistemas de batería de tracción de 72 V requieren soluciones de gestión térmica activa. Estas suelen incorporar circuitos de refrigeración líquida con control de flujo de precisión, sensores de temperatura en varios puntos dentro del paquete y algoritmos de control que ajustan la intensidad de refrigeración en función de las condiciones de funcionamiento actuales y el historial térmico. La incorporación de bombas, intercambiadores de calor, sensores de temperatura y electrónica de control puede sumar 15-30% al coste total del paquete, pero estos sistemas permiten un funcionamiento sostenido de alta potencia al tiempo que evitan la degradación térmica que, de otro modo, acortaría la vida útil de la batería.
Incluso las baterías sin refrigeración activa requieren un diseño térmico minucioso. Utilizamos materiales especializados de relleno de huecos con valores de conductividad térmica de entre 3 y 8 W/m·K para transferir el calor de las celdas a las superficies externas de la carcasa. Estos compuestos, conductores térmicos pero aislantes eléctricamente, aumentan el coste del material y la complejidad del montaje, pero mejoran sustancialmente la uniformidad de la temperatura entre los grupos de celdas. Para aplicaciones con requisitos intermitentes de alta descarga, incorporamos materiales de cambio de fase que absorben calor durante las cargas máximas y lo liberan gradualmente durante los períodos de descanso, amortiguando las fluctuaciones de temperatura que acelerarían los mecanismos de envejecimiento.
Tecnologías de interconexión
Las conexiones entre celdas individuales representan otro componente crítico de costo en los sistemas de baterías de litio. Paquetes de baterías de 36 V En herramientas eléctricas y aplicaciones similares, implementamos barras colectoras de níquel o cobre soldadas con láser con penetración de soldadura controlada con precisión para unir celdas sin causar daños térmicos a los componentes internos. Estos procesos de soldadura requieren equipos especializados con un control integral del proceso para garantizar una resistencia eléctrica y una resistencia mecánica constantes en cada punto de conexión.
Las aplicaciones de alta corriente requieren sistemas de interconexión especialmente robustos. Paquetes de baterías de grado industrial Utilizan interconexiones capaces de soportar corrientes continuas superiores a 200 A con un aumento de temperatura limitado a 20 °C por encima de la temperatura ambiente. Estas conexiones de alta resistencia suelen utilizar barras colectoras de cobre cuyas secciones transversales se determinan según los requisitos de capacidad de corriente eléctrica y resistencia mecánica. Procesos especializados de recubrimiento, generalmente de níquel o estaño, protegen estas conexiones de la oxidación, manteniendo una baja resistencia de contacto durante toda la vida útil de la batería.
El cableado interno de los paquetes de baterías representa otro elemento de costo significativo. Seleccionamos el tamaño de los conductores según los requisitos de corriente continua y de pico, y generalmente utilizamos cable con aislamiento de silicona con resistencias de temperatura superiores a 150 °C para mantener los márgenes de seguridad durante el funcionamiento con alta carga. Las conexiones de terminales utilizan terminaciones engarzadas o soldadas por ultrasonidos en lugar de uniones soldadas, ya que estas últimas pueden generar puntos débiles en entornos de alta vibración. Estas técnicas de conexión especializadas requieren herramientas específicas y la validación del proceso para cada diseño de batería, lo que contribuye a los costos de desarrollo y producción.
Transporte y Cumplimiento Normativo
La clasificación de las baterías de litio como mercancías peligrosas según las normas de transporte marítimo internacional genera desafíos logísticos únicos y costos asociados. Estos requisitos regulatorios influyen no solo en los gastos de envío, sino también en las decisiones de diseño, los protocolos de prueba y los sistemas de documentación, lo que en conjunto suma 8-12% a los costos totales de las baterías.
Requisitos de pruebas para el transporte de la ONU 38.3
Todas las baterías de litio enviadas a nivel internacional deben cumplir con las normas UN 38.3 para el transporte de mercancías peligrosas. Este protocolo de prueba integral somete a las baterías a ocho pruebas de abuso específicas: simulación de altitud, ciclo térmico, vibración, choque, cortocircuito externo, impacto/aplastamiento, sobrecarga y descarga forzada. Cada secuencia de prueba requiere múltiples muestras de batería en diferentes estados de carga, con estrictos criterios de aprobación/rechazo basados en daños observables, aumento de temperatura y comportamiento de voltaje.
Para nuestro diseños de baterías personalizadosEstas pruebas obligatorias suelen costar entre $8,000 y $15,000 por modelo, según el tamaño y la complejidad. Los laboratorios de pruebas especializados mantienen el equipo calibrado y los entornos controlados necesarios para estos protocolos estandarizados. Si bien estos gastos suelen amortizarse en las cantidades de producción, representan un costo de desarrollo significativo, en particular para baterías especializadas con volúmenes de producción limitados. Nuestro equipo de ingeniería diseña teniendo en cuenta estos requisitos e incorpora características que mejoran la robustez en las condiciones de estrés específicas evaluadas en las pruebas UN 38.3.
Más allá de la certificación inicial, el cumplimiento continuo de las regulaciones sobre mercancías peligrosas requiere documentación detallada para cada envío. Nuestros sistemas de baterías incluyen un etiquetado obligatorio con capacidad en vatios-hora, números de la ONU y advertencias de peligro adecuadas. La documentación de envío debe incluir información resumida de las pruebas que confirme el cumplimiento de la norma 38.3 de la ONU, con requisitos de formato y contenido que cambiaron significativamente con las actualizaciones de 2020 de las Regulaciones sobre mercancías peligrosas de la IATA. El mantenimiento de estos sistemas de documentación agrega una sobrecarga administrativa a cada envío de baterías.
Restricciones y alternativas al transporte aéreo
El mayor desafío para el transporte de baterías de litio tiene que ver con las restricciones de transporte aéreo. Las regulaciones actuales de la IATA prohíben el envío de baterías de litio como carga en aviones de pasajeros, excepto cuando están instaladas o embaladas con equipos, e incluso los aviones de carga tienen limitaciones estrictas en cuanto al tamaño de las baterías y los requisitos de embalaje. Estas restricciones crean desafíos logísticos para la distribución internacional, en particular para nuestros clientes. sistemas de baterías de mayor capacidad superior a 100 vatios-hora.
Los métodos de envío alternativos, como el transporte marítimo, implican tiempos de tránsito más largos, que suelen sumar de 3 a 5 semanas para los movimientos internacionales en comparación con el transporte aéreo. Estos plazos más largos aumentan los requisitos de capital de trabajo, ya que el inventario pasa más tiempo en tránsito. Es posible que se necesiten contenedores con clima controlado para evitar temperaturas extremas durante el transporte marítimo, lo que aumenta los costos de flete que pueden superar los $2000 por contenedor de envío para las rutas transoceánicas.
Nuestro equipo de logística aborda estos desafíos implementando inventarios regionales estratégicos para los modelos de baterías más utilizados, lo que permite una respuesta más rápida a los requisitos de los clientes y, al mismo tiempo, cumple con las regulaciones de envío. Para los diseños de baterías personalizados, colaboramos con los clientes en las primeras etapas del proceso de desarrollo para establecer expectativas de cronograma realistas que tengan en cuenta la complejidad necesaria del transporte. Estas consideraciones logísticas agregan costos indirectos que, en última instancia, influyen en el precio de las baterías de litio en comparación con alternativas menos reguladas.
Limitaciones del estado de carga
Las normas que rigen el transporte de baterías de litio incluyen limitaciones específicas del estado de carga (SoC) destinadas a reducir el riesgo durante el envío. Los requisitos actuales especifican un estado de carga máximo de 30% para las celdas y baterías de iones de litio enviadas por separado (no incluidas en el equipo). Este requisito crea pasos de procesamiento adicionales en nuestro flujo de trabajo de producción, ya que cada batería debe someterse a un procedimiento de descarga controlada para alcanzar el estado adecuado para el transporte.
Para nuestro Baterías de alta capacidad de 51,8 VEste proceso de descarga puede requerir de 4 a 6 horas por paquete en un equipo especializado que controla con precisión las tasas de descarga mientras monitorea los voltajes de cada celda. La energía descargada representa una pérdida de producción, ya que las baterías deben ser recargadas posteriormente por el usuario final antes del uso inicial. Optimizamos este proceso recuperando energía durante el ciclo de descarga a través de bancos de carga regenerativos, lo que reduce tanto el desperdicio de energía como la generación de calor durante la producción.
Si bien estos requisitos regulatorios agregan complejidad y costos a la logística de las baterías de litio, reflejan las consideraciones legítimas de seguridad asociadas con estas fuentes de energía de alta densidad energética. Nuestros programas integrales de cumplimiento garantizan que todas las baterías lleguen a los clientes de manera segura y al mismo tiempo mantienen el cumplimiento regulatorio total, protegiendo tanto la seguridad humana como las consideraciones ambientales a lo largo de la cadena de suministro.
Investigación, desarrollo y mejora continua
El panorama tecnológico de las baterías de litio, que evoluciona rápidamente, impulsa una inversión sustancial y continua en investigación y desarrollo. Estos gastos de I+D contribuyen aproximadamente con un 5-10% a los costos generales de las baterías, pero permiten mejoras continuas en el rendimiento que hacen que las baterías de litio sean cada vez más valiosas a pesar de su precio elevado.
Optimización química y ciencia de los materiales
A nivel de celdas, la investigación en curso se centra en mejoras incrementales en la densidad energética, la vida útil, la capacidad de carga rápida y el rendimiento térmico. Nuestro equipo de ingeniería colabora con los fabricantes de celdas para evaluar tecnologías de materiales emergentes, como ánodos mejorados con silicio que pueden aumentar la capacidad en un 20-40% en comparación con las formulaciones de grafito tradicionales. Estos materiales avanzados suelen tener precios superiores durante la comercialización inicial, y los costos disminuyen gradualmente a medida que aumenta la escala de fabricación.
Para aplicaciones que priorizan el rendimiento en temperaturas extremas, como nuestra sistemas de baterías de temperatura ultrabajaLas formulaciones especializadas de electrolitos incorporan paquetes de aditivos cuidadosamente equilibrados que mantienen la movilidad iónica a temperaturas de hasta -40 °C. Estas mezclas de electrolitos personalizadas se someten a pruebas exhaustivas para verificar su rendimiento a baja temperatura, garantizando al mismo tiempo la compatibilidad con otros componentes de la celda durante su vida útil prevista. El desarrollo y la validación de estas formulaciones especializadas representan inversiones significativas que influyen en los costos del producto, pero ofrecen un rendimiento excepcional en entornos exigentes.
Las mejoras de seguridad a través de la ciencia de los materiales representan otra área de investigación activa. Los materiales separadores con revestimientos cerámicos o propiedades intrínsecas de apagado térmico aumentan los costos de los componentes, pero mejoran drásticamente la seguridad a nivel de celda al brindar protección adicional contra cortocircuitos internos. sistemas de baterías de alta seguridad Para aplicaciones médicas, incorpore estos separadores premium a pesar de su costo superior al de los materiales estándar, ya que la seguridad mejorada justifica el gasto adicional para aplicaciones críticas.
Innovación en procesos de fabricación
La mejora continua de las técnicas de fabricación impulsa mejoras de calidad y reducciones graduales de los costes de las baterías de litio. Nuestros socios de producción implementan tecnologías como el corte por láser de los materiales de los electrodos, lo que reduce la variación dimensional y elimina los riesgos de contaminación asociados a las herramientas de corte mecánicas. Los sistemas de inspección óptica automatizada con algoritmos de aprendizaje automático detectan defectos sutiles que podrían escapar a la observación humana, lo que garantiza una calidad constante y reduce los costes laborales.
La automatización del ensamblaje continúa avanzando, con robótica especializada que maneja operaciones cada vez más delicadas que antes estaban restringidas al procesamiento manual. Estas innovaciones en la fabricación requieren una inversión de capital significativa, pero reducen gradualmente los costos de producción a través de un mejor rendimiento, menores requisitos de mano de obra y una mayor consistencia. Para formatos de celdas establecidos, como las celdas cilíndricas 18650 que se usan en muchos de nuestros sistemas de baterías, el equipo de producción ha evolucionado a través de múltiples generaciones, cada una de las cuales ofrece mejoras incrementales en la rentabilidad.
Las mejoras en la eficiencia energética en los procesos de fabricación representan otra área de enfoque. Las operaciones de secado de electrodos tradicionalmente consumen una cantidad sustancial de energía, pero las tecnologías avanzadas, como el secado asistido por microondas, pueden reducir el consumo de energía en un 30-50% y, al mismo tiempo, mejorar la calidad del recubrimiento. Los requisitos de energía del ciclo de formación disminuyen mediante protocolos de carga optimizados que logran los mismos resultados electroquímicos con un menor consumo de energía. Estas mejoras de proceso reducen gradualmente los costos de producción y, al mismo tiempo, mejoran la huella ambiental de la fabricación de baterías.
Evolución del sistema de gestión de baterías
Los sistemas electrónicos que controlan las baterías de litio se someten a un desarrollo continuo para mejorar la funcionalidad y reducir los costos de los componentes. Los primeros diseños de BMS utilizaban componentes discretos para funciones de protección y monitoreo de voltaje, mientras que los sistemas actuales integran estas funciones en circuitos integrados especializados que reducen tanto la cantidad de componentes como los requisitos de espacio en la placa. Estas soluciones integradas mejoran la confiabilidad mediante la reducción de puntos de conexión y al mismo tiempo reducen los costos de fabricación mediante un ensamblaje simplificado.
Nuestro diseños BMS de última generación Implementar algoritmos avanzados que se adapten a las características de envejecimiento de la batería, manteniendo un rendimiento óptimo durante toda su vida útil. Los enfoques de aprendizaje automático analizan los patrones de uso para optimizar los perfiles de carga para aplicaciones específicas, lo que potencialmente extiende la vida útil del ciclo en un 15-25% en comparación con los sistemas de gestión de parámetros fijos. Estas mejoras de software agregan costos de desarrollo, pero brindan un valor sustancial a través de una mayor longevidad y rendimiento de la batería.
Las funciones de conectividad inalámbrica aparecen cada vez más en los sistemas de baterías modernos, lo que permite la monitorización remota, el diagnóstico e incluso las actualizaciones de firmware de las baterías instaladas. Si bien estas capacidades aumentan los costos de los componentes mediante la incorporación de módulos de comunicación por Bluetooth, WiFi o celular, crean valor al permitir el mantenimiento preventivo y la optimización del rendimiento durante todo el ciclo de vida de la batería. Para nuestros clientes comerciales que utilizan grandes flotas de equipos alimentados por batería, estas funciones de batería conectada brindan importantes beneficios operativos que justifican su costo adicional.
Conclusión: La evolución de la propuesta de valor de las baterías de litio
Los mayores costos asociados con la tecnología de baterías de litio reflejan los materiales avanzados, los complejos procesos de fabricación, los sofisticados sistemas de control y los requisitos de cumplimiento normativo necesarios para ofrecer su excepcional rendimiento. Como hemos explorado, cada componente de la cadena de valor de las baterías de litio implica tecnologías especializadas e ingeniería de precisión que contribuyen a los gastos generales de producción. Sin embargo, la continua evolución de esta tecnología mejora gradualmente la propuesta de valor mediante mejoras de rendimiento y reducciones graduales de costos.
Para aplicaciones que abarcan desde electrónica portátil hasta vehículos eléctricos y almacenamiento de energía estacionario, las baterías de litio ofrecen capacidades que simplemente no se pueden lograr con tecnologías alternativas. Su combinación de alta densidad energética, excelente ciclo de vida, mínimos requisitos de mantenimiento y una trayectoria de costos decreciente las hace cada vez más competitivas a pesar de su elevado precio inicial. En Vade Battery, nos centramos en optimizar cada aspecto del diseño y la producción de baterías para ofrecer el máximo valor para los requisitos específicos de cada aplicación, equilibrando el rendimiento, la seguridad, la longevidad y el costo.
El mercado de baterías de litio continúa evolucionando rápidamente, con avances en la investigación que amplían regularmente las fronteras del rendimiento, mientras que la escala de fabricación reduce progresivamente los costos de producción. Las organizaciones que evalúan soluciones de almacenamiento de energía deben considerar tanto los costos iniciales de adquisición como el valor a largo plazo, incluidos factores como el ciclo de vida, los requisitos de mantenimiento, la eficiencia energética y los beneficios operativos de las características avanzadas. Nuestro equipo de ingeniería se especializa en abordar estas complejas consideraciones para desarrollar soluciones de baterías optimizadas para requisitos de aplicaciones específicas.
Para las organizaciones que exploran soluciones de baterías de litio personalizadas, lo invitamos a Contacte con nuestro equipo de ingeniería o presentar requerimientos específicos a través de nuestro Portal de solicitud de diseño de baterías de litioNuestros especialistas técnicos pueden brindarle recomendaciones detalladas en función de los requisitos de su aplicación, ayudándolo a explorar las compensaciones entre las capacidades de rendimiento y las consideraciones de costo para desarrollar una solución óptima de almacenamiento de energía.