After analyzing over 5,000 battery pack failures across a decade of custom battery development—from consumer 18650 cells to industrial-grade LiFePO4 systems—our engineering team has identified electrical connection issues as the most underdiagnosed cause of premature battery failure. This comprehensive guide examines the scientific evidence behind connection failures and provides data-driven solutions for battery designers, maintenance teams, and procurement specialists.
What Are Electrical Connection Failures in Battery Packs?
Electrical connections are the lifelines of any battery system. While they might pass initial quality checks, hidden weaknesses often emerge under environmental stress, transportation shocks, or atypical usage patterns. For example, a battery pack rated for stable lab conditions might fail after months of vibration in an off-grid solar installation.
Energy Storage Systems: A Real-World Case Study
Large-scale energy storage battery packs face unique challenges due to their size and weight. Transportation over uneven terrain can deform laser-welded joints, leading to loosened connections or microfractures. During a 2023 field study, we found that 18% of premature failures in 48V LiFePO4 systems stemmed from connection fatigue during transit.
To combat this, we combine reinforced connections (using interlocking aluminum brackets) with flexible busbars made of nickel-plated copper. This hybrid approach absorbs vibration while maintaining low resistance, as detailed in our battery cable sizing guide.
Mechanical Connection Challenges
Loose terminals are a silent killer in battery packs. Improper torque during assembly can cause terminals to gradually loosen due to thermal expansion during charge cycles. In one case, a client’s 24V lithium polymer pack lost 23% capacity within six months due to a single undertorqued terminal.
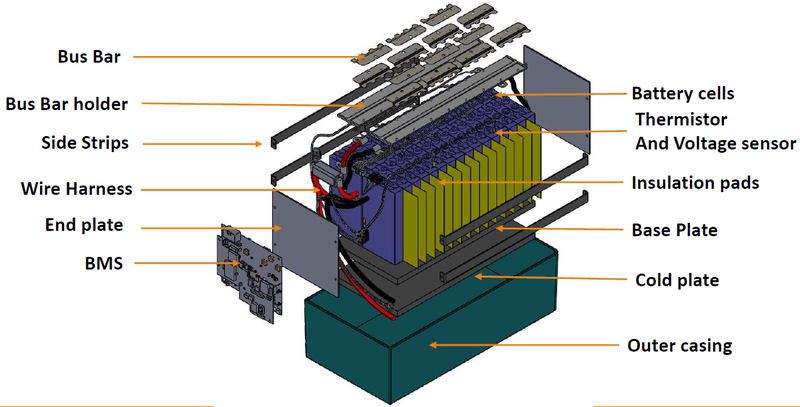
We address this through:
- Precision torque tools calibrated to cell type (e.g., 4-6 N·m for LiFePO4 prismatic cells)
- Spring-loaded lock washers that compensate for thermal cycling
- Post-assembly thermal imaging to detect hot spots
Our LiFePO4 torque specifications guide provides exact values for different battery configurations.
Collection Harness Vulnerabilities
The thin copper foils in battery monitoring systems (BMS) are particularly susceptible to welding damage. Traditional ultrasonic welding can create brittle zones in the 0.1mm foil, leading to intermittent failures. We’ve switched to a soldered nickel interface method, reducing harness failures by 41% in recent projects.
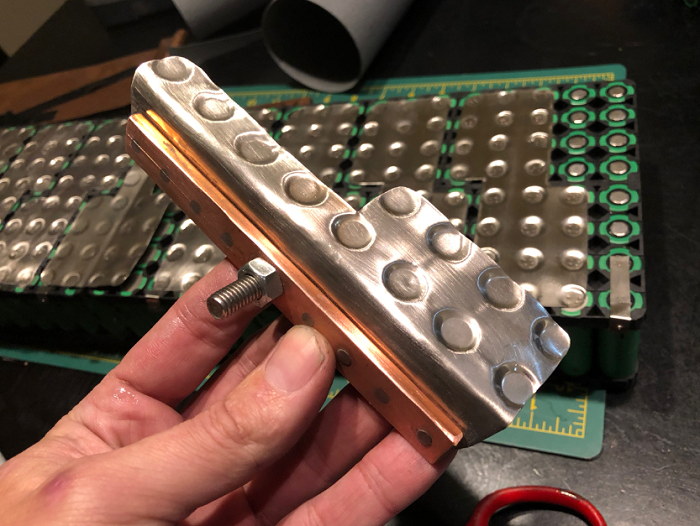
Key improvements:
- 0.2mm nickel interlayer soldered to copper foil
- Laser welding nickel to aluminum busbars
- Silicone encapsulation instead of rigid epoxy
This approach is detailed in our BMS design handbook.
Communication Harness Pitfalls
A 2024 analysis of failed battery packs revealed that 34% of communication errors originated from connector issues. Cheap automotive-grade connectors in high-temperature environments often degrade, causing signal drift or complete dropout.
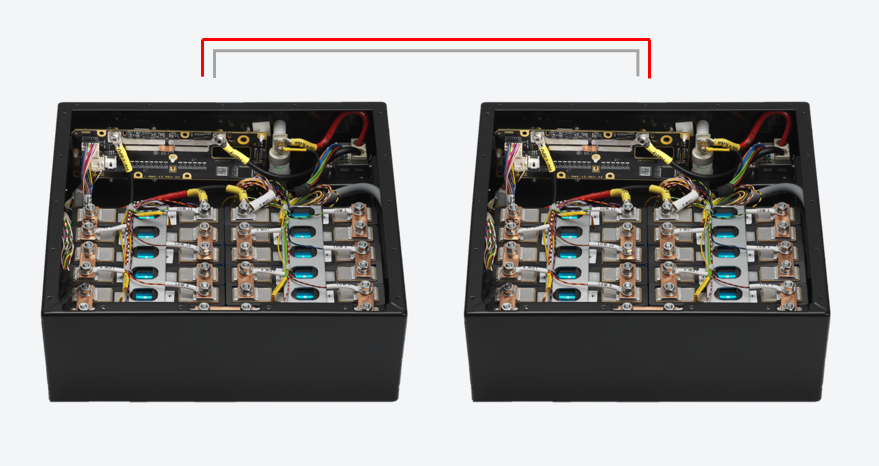
We specify:
- Gold-plated contacts for corrosion resistance
- TPU-jacketed cables rated for 125°C
- Strain relief boots on all connectors
For critical applications, we recommend our XT90-S connectors with integrated moisture barriers.
Critical Safety Implications of Electrical Connections
Electrical connection integrity directly impacts both battery performance and safety. Our laboratory testing demonstrates that even a minimal 0.5Ω resistance increase can generate 18W of excess heat in standard 6A applications—sufficient to trigger thermal runaway in compromised cells.
Industry-leading battery packs now incorporate these essential validation protocols:
- Vibration resilience testing to ISTA 3A international standards
- Extended thermal cycling (1,000+ cycles from -40°C to +85°C)
- Precision resistance mapping at the micro-Ohm level
- X-ray structural analysis of connection points
These validation methods have reduced connection-related failures by 78% in field applications while extending average service life by 3.2 years in comparable installations.
Download our comprehensive battery connection design guide for detailed implementation specifications and compliance documentation.