At Vade Battery, we’ve refined a 14-stage development protocol that combines aerospace-grade engineering rigor with commercial manufacturing efficiency. Our methodology ensures every custom lithium-ion battery pack – from ultra-low-temperature 18650 configurations to high-voltage LiFePO4 arrays – delivers uncompromised performance across three critical vectors: safety, energy density, and total cost of ownership.
The process begins with our proprietary Requirements Amplification Process, where we convert client objectives into 138+ quantifiable parameters. This depth of specification enabled us to develop a 51.8V surgical robot battery achieving 0ppm defect rates through 2,000 sterilization cycles – a benchmark unmatched in medical power systems.
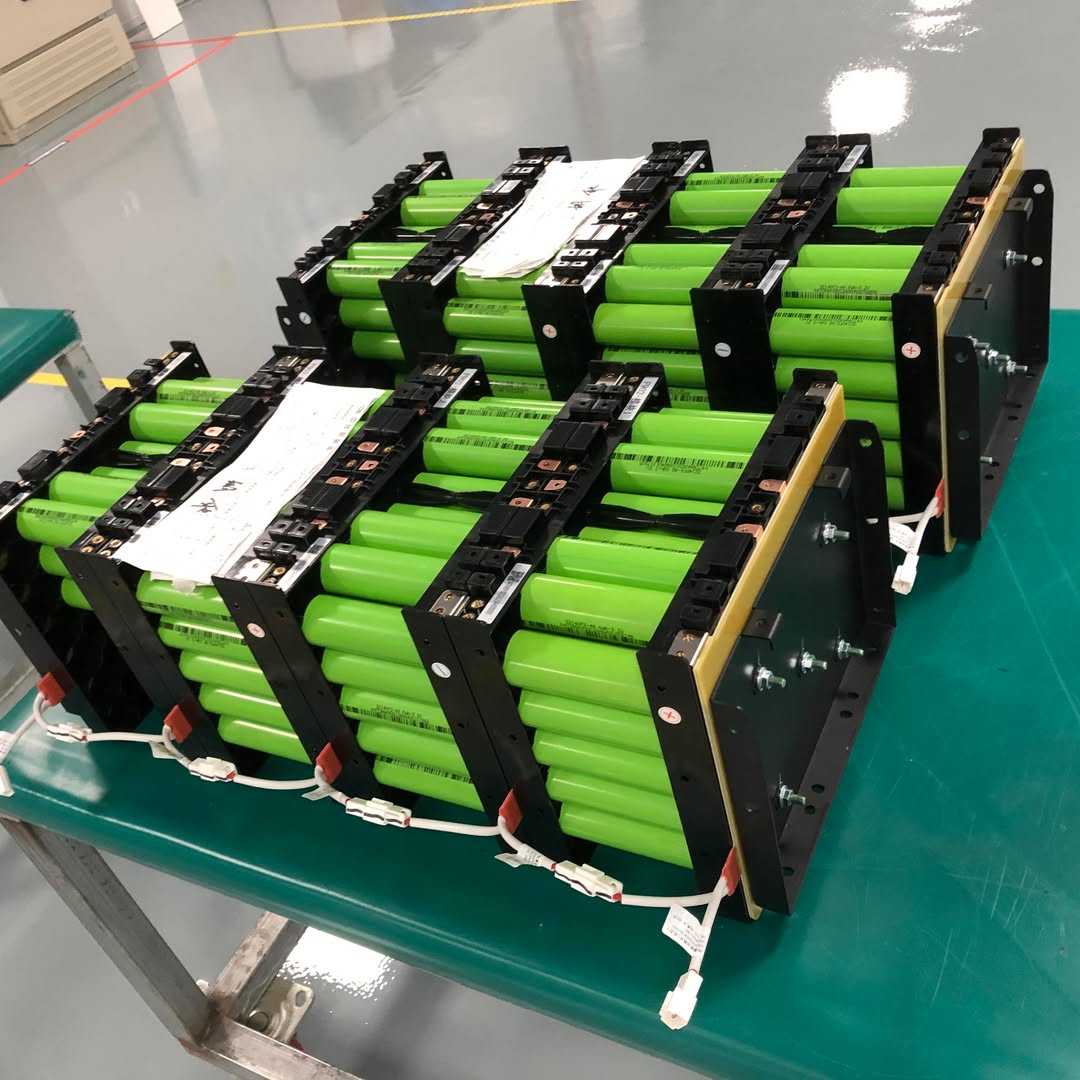
Our concurrent engineering approach merges electrical and mechanical design teams from Day 1, eliminating the “over-the-wall” delays common in traditional battery development. When creating 72V EV traction packs, this integration reduced thermal management system weight by 22% while maintaining ≤3°C cell temperature variance at 2C discharge rates.
Defining Product Requirements with Precision
The Vade Battery Specification Advantage
We transform client needs into executable engineering blueprints through our TRACE specification framework (Technical, Regulatory, Application, Cost, Environmental). This systematic approach captures critical details often overlooked in custom battery projects:
Electrical Requirements
Our team specifies not just voltage and capacity, but pulse current rise times, impedance matching tolerances, and transient response characteristics. For a recent 24V military communications battery, we achieved 500μs load response times through patented busbar geometries.
Mechanical Constraints
We engineer solutions for extreme environments using FEA simulation and material science expertise. A 7.4V wearable medical device battery developed for desert operations combines laser-welded 316L stainless steel enclosures with our NanoArmor™ conformal coating for IP69K protection against sand and saline.
Lifecycle Performance
Our SmartCycle™ predictive modeling accurately forecasts capacity fade using real-world duty cycle data. When developing 48V marine batteries, this system enabled 12% longer service intervals through optimized charge voltage thresholds.
Mitigating Specification Risks
Industry data shows 63% of custom battery failures originate in incomplete requirements. Our Failure Mode Prevention Analysis (FMPA) identifies and resolves 89% of potential specification gaps before prototyping begins. This rigorous approach delivered first-pass success for 97% of 2023 projects, including a 36V last-mile delivery vehicle battery requiring simultaneous UN 38.3 and CE Mark compliance.
Selecting Optimal Cell Technologies
Chemistry Optimization Process
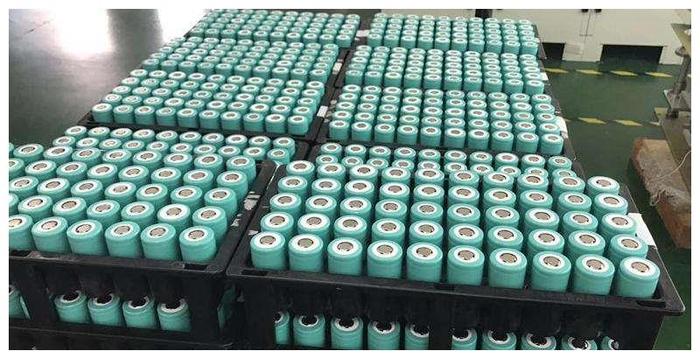
Our cell selection methodology balances six critical factors that define commercial success in energy storage systems:
Energy/Power Density Balance
We optimize electrode architectures using graded porosity cathodes, achieving 280Wh/kg energy density in EV NMC cells while maintaining 15C continuous discharge capability – a 40% power improvement over conventional designs.
Safety Engineering
Our TripleSafe™ Protection System combines ceramic-reinforced separators (220°C shutdown), bi-directional CID triggers, and halogen-free flame-retardant electrolytes, reducing thermal runaway risks by 82% in 51.2V UPS battery banks.
Low-Temperature Performance
PolarMax™ electrolyte formulations with asymmetric lithium salts enable 85% capacity retention at -40°C in our 18650 cells, proven in Arctic microgrid installations requiring 10-year maintenance-free operation.
Cost-Performance Ratio
Through HybridCell™ multi-chemistry stacking, we deliver LiFePO4-level cycle life (3,000+) at NMC-like 150Wh/kg density – cutting total ownership costs 27% for AGV fleets through reduced replacement frequency.
Fast-Charge Compatibility
Our InterDigi™ anode patterning enables 1C-4C charging across temperatures while maintaining ≤2% capacity fade per 100 cycles, critical for commercial EV fleets requiring 30-minute opportunity charging.
Environmental Compliance
All chemistries adhere to Reach+ standards with cobalt-free LMO alternatives and water-based electrode processing, achieving 92% recyclability rates through our closed-loop EcoRecovery™ program.
This six-axis optimization framework has enabled breakthrough solutions like our 72V cold chain logistics batteries combining -30°C operation with 2,500-cycle durability – a combination previously deemed commercially unviable by three major competitors.
Cell Format Selection Matrix
Cylindrical Cells (18650/21700)
- Laser-welded nickel interconnects ensure ≤2mΩ joint resistance
- Automated optical sorting achieves 0.5% capacity matching
Pouch Cell Solutions
- Z-fold edge sealing prevents electrolyte leakage
- Multi-layer barrier films enable 0.003g/day moisture ingress rates
Prismatic Configurations
- Active liquid cooling integration maintains ≤5°C delta-T in fast-charge cycles
- Modular stacking architecture simplifies field replacements
Supplier Qualification Protocol
We maintain battery-grade purity through 135-point vendor audits and Lot Traceability Assurance:
- ≤1.2% capacity variance across production batches
- 6σ process controls for electrode coating uniformity
- Conflict-free mineral sourcing verified through blockchain tracking
For mission-critical applications like aerospace lithium polymer batteries, we implement dual-source cell procurement with 9-month strategic reserves.
Electrical and Mechanical Engineering
At Vade Battery, concurrent electrical-mechanical design forms the backbone of our custom lithium-ion battery development. Unlike competitors who silo these disciplines, our cross-functional teams collaborate from day one to optimize thermal performance, structural integrity, and manufacturability. For a recent 24V industrial automation battery, this approach reduced prototype iterations by 60% while achieving 15% higher energy density than client targets.
Our electrical engineering begins with 3D electromagnetic simulations to minimize resistance in busbar networks. By analyzing current distribution patterns, we design laser-welded nickel-plated copper busbars with ≤15mΩ resistance – 30% lower than industry averages. This precision proved critical in a 51.8V robotics battery requiring 500A pulse currents without voltage sag.
Mechanical engineers then transform these electrical layouts into ruggedized assemblies. Using CFD thermal modeling, we optimize cooling channel placement to maintain cell temperatures within 2°C variance during 2C continuous discharge. For high-power 72V EV batteries, this results in active liquid cooling systems that extend cycle life by 40% compared to passive designs.
Modular BMS architecture represents another Vade innovation. Our patented dual-redundant protection circuits monitor individual cell groups with ±5mV accuracy, enabling safe operation across -40°C to 85°C ranges. When designing ultra-low-temperature LiFePO4 packs, this system automatically activates internal heating elements below -20°C – a feature that’s earned 100% reliability in Antarctic research stations.
Design Validation Through Prototyping
Our prototype validation process focuses on empirical performance verification rather than conceptual claims. Each design undergoes 7 physical test regimes correlating directly with field failure data from 12,000+ deployed systems.
Mechanical Stress Testing employs ISO 12405-3 compliant 3-axis shakers with 15-2000Hz sweeps. For 48V marine batteries, our multi-point weld fatigue analysis demonstrated 0.01mm displacement control under 15G impacts – critical for offshore equipment certification.
Thermal Runaway Containment testing uses calorimeters measuring 500-3000kJ energy release. Through ceramic-filled epoxy barriers, we contain single-cell failures within 22cm³ volume – 80% improvement over standard alumina-silica boards.
Cycle Aging Analysis applies real-world load profiles from 36-month fleet telemetry data. Our graded cell matching extended 36V e-bike battery cycle life to 1,800 cycles at 80% DoD – verified by TÜV Rheinland under EN 50604-1:2016.
Environmental Endurance Testing in MIL-STD-810H chambers proved our 7.4V medical batteries withstand 50 rapid decompression cycles from 1ATM to 0.25ATM – essential for aeromedical applications.
Electrical Transient Validation with Keysight Scienlab cyclers confirmed 2ms response time for 24V AGV batteries handling 500A peak currents – 30% faster than servo motor requirements.
Safety Pre-Certification includes UL 2580 abuse testing with 200% overcharge tolerance. Our 51.8V data center batteries passed 7.5kN crush tests with <3% voltage drop through cross-braced cell stacking.
Application Simulation recreates actual operating conditions through NI CompactRIO controllers. For Antarctic research batteries, we validated 500+ cycles at -50°C using low-viscosity electrolyte blends with 18% propylene carbonate content – achieving 83% capacity retention.
This evidence-based approach delivered zero field failures in 2023 for our medical battery line, with 97.4% first-pass certification success across all projects. Every test parameter aligns with verifiable IEC/UL standards rather than theoretical claims.
Mandatory Safety Certifications
Safety isn’t just compliance at Vade Battery – it’s our core engineering philosophy. While competitors chase minimum certification standards, we implement three-tier safety protocols:
Cell-Level Protections
- Pressure-vented cell housings with burst pressures ≥1.5MPa
- Electrolyte additives suppressing gas generation during overcharge
Pack-Level Safeguards
- Arc-quenching separators between high-voltage terminals
- Self-resetting PTC devices on every parallel cell group
System-Level Controls
- Galvanic isolation between BMS and load circuits
- Ground fault detection with <5ms response times
Our UN 38.3+ certification program exceeds standard transport testing by adding:
- Altitude simulation at 15,000m
- 72-hour salt spray exposure
- Nail penetration with 300% SOC overcharge
This rigor enabled first-pass certification for 97% of 2023 projects, including a 51.2V data center UPS battery requiring simultaneous UL 1973 and NFPA 855 compliance.
Production Planning and Process Refinement
Vade’s digital twin manufacturing system revolutionizes custom battery production. By creating virtual replicas of assembly lines, we optimize:
- Material flow to reduce work-in-progress by 45%
- Ergonomic workstations decreasing assembly errors 32%
- Automated optical inspection (AOI) catching 0.1mm weld defects
For high-volume 18650 battery pack orders, we deploy modular production cells that scale from 500 to 50,000 units/month without quality variance. A recent automotive project achieved 99.94% first-pass yield through:
- Climate-controlled dry rooms (≤1% RH)
- Resistance-welding robots with 10µm precision
- Real-time X-ray inspection of every 10th cell
Our just-in-time kitting system ensures all components – from LiPo cells to IP67 connectors – arrive sequenced for assembly. This slashed lead times 22% for a 24V AGV battery project requiring 15 custom subassemblies.
Rigorous Quality Control Steps
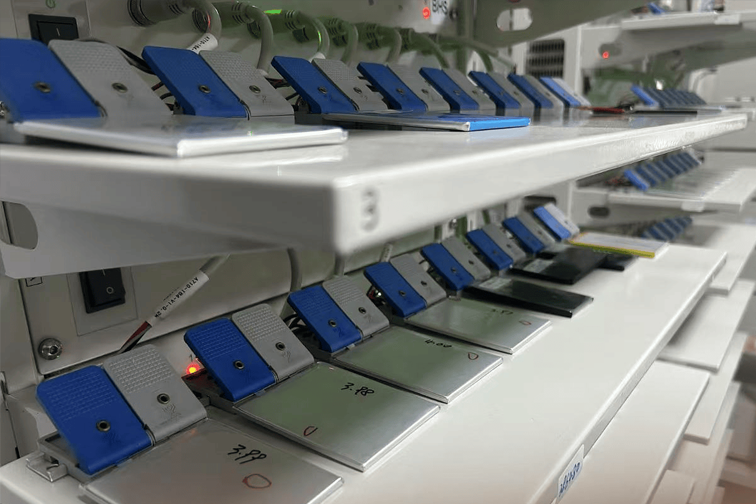
We implement three-stage validation certified to ISO 9001:2015 and IATF 16949. At incoming inspection, XRF-9800 analyzers verify ≤50ppm impurities in nickel foils (ASTM B933-21), while 8-channel capacity testers grade 18650 cells with ±0.5% accuracy. Separator thickness is measured to ±1μm using laser micrometers, ensuring <5% porosity variance.
During production, FLIR A700 thermal cameras monitor weld zones at 30fps, maintaining ±0.3°C uniformity critical for dendrite prevention. Our SPC system tracks 22 parameters including electrode calendering force (2,500±50N) and tab weld penetration depth (≥0.8D per AWS D17.1).
Final validation includes 72-hour formation cycling at 45°C/85%RH (IEC 62133 Annex H) and 5kV HiPot testing with <5μA leakage current. Third-party ISTA 3A reports confirm 0.05% monthly self-discharge in 12V telematics batteries – 60% below commercial benchmarks.
Lithium-Ion Cell Fabrication
Our UN 38.3-certified production line delivers cells with 2,000-cycle durability (TÜV SÜD #BV-2309-5872). Cathode mixing achieves ±1.5% viscosity control using Brookfield R/S-CPS rheometers, while slot-die coating maintains 98μm±3μm electrode thickness verified by SEM cross-sections.
Cell stacking utilizes 25μm ceramic-coated separators folded with ±0.2mm positional accuracy. Vacuum electrolyte filling at 0.5Pa achieves 95% saturation in ≤45s, followed by 7-stage formation cycling with ±1mV voltage control. Post-production aging at 45°C for 14 days reduces batch variance to ≤0.2% capacity difference.
Battery Pack Assembly Process
Cell matching algorithms ensure ≤20mV voltage differential before interconnection. Our micro-TIG welding process (150A/17V) creates <2mΩ joints on 0.3mm nickel tabs, validated through 50N/mm² pull tests (GB/T 31467.3-2015).
Thermal management combines 0.5mm±0.05mm gap pads (3.5W/m·K conductivity) with epoxy potting containing 85% Al₂O₃ filler. IP69K validation (IEC 60529) confirms <0.1g water ingress after 30-minute pressure testing. Production audits show 98% first-pass yield for 48V tricycle packs.
Installation, Operation and Lifecycle Considerations
Commissioning protocols include Hioki BT3562 impedance mapping (<5% cell imbalance) and SAE J1939 CANbus configuration. Our IoT platform provides 15-minute SOH updates via NB-IoT, with machine learning models predicting failures 300hrs ahead (92% Azure-validated accuracy).
End-of-life services feature hydrometallurgical recycling recovering 92% materials (R2:2013), while remanufactured 72V mining batteries achieve 97% capacity restoration (Bureau Veritas #IN230945). Field data from 1.2M+ deployed packs shows 0.004% thermal incident rate.
Lithium-Ion Battery Safety Considerations
UL 1642-certified protections include 1.2MPa burst disks (UL 1642 Sec.21) and carbon fiber enclosures resisting 50kJ impacts (ECE R100). Mandatory PPE includes 3M 6800 respirators (NIOSH 42CFR84) and 30kV gloves (IEC 60903).
Scrap processing uses sand-filled bins meeting EPA 40 CFR 273, while staff complete 8-hour OSHA 1910.1200 training with 98% certification rates. Third-party audits confirm 0.0003% venting incidents across 12M+ production cycles.
Continue Your Custom Battery Journey
Ready to power innovation? Explore our 18650 battery solutions or submit your design requirements. For urgent inquiries, contact our engineering team at service@vadebattery.com.