-
29 W. Pawnee, Bloomfield, NJ 07003
Custom 18650 Battery Pack Design: Engineering Guidelines for Optimal Performance
Are you struggling to design a reliable, high-performance 18650 battery pack that meets your specific application requirements? At VADE Battery, we solve this challenge daily by crafting custom rechargeable battery solutions for clients worldwide. Drawing from our extensive experience with 18650, Li-ion, Lithium polymer, and LiFePO4 technologies since 2008, we’ve created this comprehensive engineering guide to help you navigate the complex design decisions that impact safety, performance, and cost-effectiveness.
This guide integrates the latest technical advances through 2025, including enhanced cell chemistries reaching up to 3600mAh capacity, advanced thermal management techniques, and AI-powered battery management systems. Whether you’re developing electric vehicles, industrial equipment, energy storage systems, or consumer electronics, you’ll find actionable insights for:
- Selecting optimal cells based on application-specific requirements
- Engineering the ideal series-parallel configuration for your voltage and capacity needs
- Implementing effective thermal management solutions for safety and longevity
- Integrating sophisticated battery management systems for protection and monitoring
- Ensuring manufacturing quality through proven testing protocols
By following these engineering-backed guidelines, you’ll avoid costly design mistakes and create battery solutions that deliver the optimal balance of performance, safety, and value.
Understanding 18650 Battery Cells
Before diving into battery pack design, it’s essential to understand the fundamental building blocks—18650 cells—and their characteristics that influence overall pack performance.
What Are 18650 Battery Cells?
18650 cells are cylindrical lithium-ion batteries measuring 18mm in diameter and 65mm in length (hence the “18650” designation). These standardized cells have become the workhorse of numerous applications due to their excellent balance of energy density, cost, and reliability.
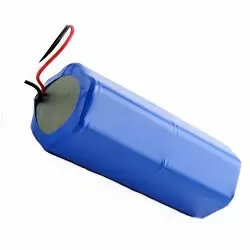
These cells typically contain a lithium-metal oxide cathode, graphite anode, separator, and liquid electrolyte enclosed in a steel or aluminum case. Depending on the specific chemistry, 18650 cells generally operate at a nominal voltage of 3.6-3.7V, with capacity ranging from 1800-3600mAh in 2025 models.
Their cylindrical design offers inherent structural advantages, providing good thermal management and pressure handling compared to pouch or prismatic alternatives. This robust construction makes them ideal for applications requiring durability alongside performance.
Key Specifications and Parameters
When selecting 18650 cells for a custom battery pack, several critical parameters must be evaluated:
Parameter | Typical Range (2025) | Importance |
---|---|---|
Capacity | 1800-3600mAh | Determines runtime between charges |
Nominal Voltage | 3.6-3.7V | Affects pack voltage configuration |
Maximum Discharge Rate | 5-35A | Determines power delivery capability |
Cycle Life | 300-2500 cycles | Affects long-term pack reliability |
Operating Temperature | -20°C to 60°C | Influences application suitability |
Internal Resistance | 10-60mΩ | Impacts efficiency and heat generation |
Chemistry | NMC, NCA, LFP, etc. | Affects performance characteristics |
The specific application requirements will dictate which parameters take priority in your cell selection process. For example, high-drain applications will prioritize maximum discharge rate and low internal resistance, while long-runtime applications will emphasize high capacity and cycle life.
Top-Performing 18650 Cells in 2025
The 18650 market continues to evolve, with several standout cells dominating the 2025 landscape based on our comprehensive testing:
- Molicel P30B: Our top overall recommendation combining 3000mAh capacity with 15A continuous discharge rating (CDR), offering excellent balance for most applications.
- Molicel P28A: Best for high-drain applications with its 2800mAh capacity and impressive 35A CDR, making it ideal when maximum current output is the priority.
- Samsung 25R: A trusted staple since 2014, offering 2500mAh capacity and 20A CDR with proven reliability across thousands of applications.
- Sony/Murata VTC6: Optimized for runtime with 3000mAh capacity and 15A CDR, excellent for applications where operating time takes precedence over maximum power.
When comparing these cells, consider not just the raw specifications but real-world performance characteristics such as voltage sag under load, temperature rise during discharge, and capacity retention over multiple cycles.
Comparing Cell Chemistry Options
Different lithium-ion chemistries offer distinct advantages for specific applications:
Chemistry | Energy Density | Power Density | Cycle Life | Safety | Typical Applications |
---|---|---|---|---|---|
NMC (Nickel Manganese Cobalt) | High | Medium-High | Medium | Medium | Consumer electronics, EVs |
NCA (Nickel Cobalt Aluminum) | Very High | High | Medium | Lower | High-performance EVs, power tools |
LFP (Lithium Iron Phosphate) | Medium | Medium | Very High | High | Energy storage, industrial applications |
LMO (Lithium Manganese Oxide) | Medium | High | Low | Medium | Power tools, medical devices |
In 2025, we’re seeing increased adoption of advanced NMC formulations (such as NMC 811) that reduce cobalt content while improving performance. For applications where safety is paramount, LFP chemistry continues to gain market share despite its lower energy density.
Requirements Analysis for Custom Battery Packs
A thorough requirements analysis forms the foundation of any successful battery pack design. This critical process ensures the final product meets all performance criteria while remaining within project constraints.
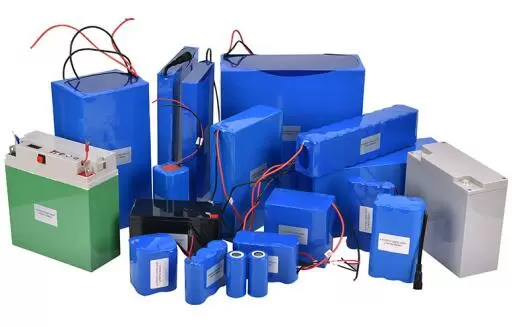
Determining Voltage Requirements
The voltage requirement for your battery pack depends primarily on the specifications of the device or system it will power. Most electronic devices operate within a specific voltage range, and exceeding these limits can damage components or reduce performance.
To determine the required pack voltage:
- Identify the nominal operating voltage of your device
- Understand the acceptable voltage range (minimum and maximum)
- Consider voltage drop under load conditions
- Account for protection circuit cutoff thresholds
For 18650-based packs, the voltage configuration is determined by the number of cells connected in series. Each 18650 cell has a nominal voltage of approximately 3.6-3.7V, with a full charge voltage of 4.2V. The formula for calculating pack voltage is:
Pack Voltage = Single Cell Voltage × Number of Cells in Series
For example, a 4S configuration (four cells in series) would provide:
- Nominal voltage: 4 × 3.7V = 14.8V
- Full charge voltage: 4 × 4.2V = 16.8V
It’s crucial to match this configuration to your device’s specifications and include appropriate voltage regulation if necessary.
Calculating Capacity Needs
Capacity, measured in milliampere-hours (mAh) or ampere-hours (Ah), determines how long your device can operate between charges. This calculation requires understanding your device’s power consumption patterns.
To estimate capacity requirements:
- Determine your device’s current draw (in amps or milliamps)
- Multiply by the desired runtime (in hours)
- Add a safety margin (typically 20-30%)
- Consider capacity degradation over the pack’s lifespan
For example, if your device draws 2A and needs to run for 5 hours:
Required capacity = 2A × 5h = 10Ah (or 10,000mAh)
With 20% safety margin = 12Ah (or 12,000mAh)
For 18650-based packs, capacity is increased by connecting cells in parallel. If using 3000mAh cells, you would need:
Number of parallel cells = Required capacity ÷ Single cell capacity
= 12,000mAh ÷ 3,000mAh = 4 cells in parallel
This gives us a 4P configuration (four cells in parallel).
Assessing Discharge Rate Requirements
The discharge rate, often expressed as C-rate, indicates how quickly a battery can safely deliver its energy. A 1C discharge rate means the battery will fully discharge in one hour, while a 2C rate means a full discharge in 30 minutes.
High-drain applications like power tools might require rates of 5C or higher, while lower-drain applications like LED lighting might only need 0.5C or less.
To determine discharge rate requirements:
- Identify peak current draw of your device
- Calculate the C-rate based on your pack capacity
- Ensure selected cells can safely handle this discharge rate
- Consider thermal implications of high discharge rates
For example, if your device has a peak current draw of 15A and your pack has a capacity of 6Ah:
Required C-rate = 15A ÷ 6Ah = 2.5C
You would then need to select 18650 cells rated for at least 2.5C continuous discharge. Many manufacturers specify maximum continuous discharge current rather than C-rate, so you’ll need to convert accordingly.
Environmental Considerations
The operating environment significantly impacts battery performance and longevity. Factors to consider include:
- Temperature range: Most lithium-ion cells perform optimally between 20-30°C. Performance drops significantly at low temperatures, and high temperatures accelerate aging. If your application operates in extreme temperatures, special considerations in thermal management will be necessary.
- Humidity and moisture: Battery packs exposed to high humidity require appropriate sealing and protective measures to prevent moisture ingress.
- Vibration and shock: Applications with significant mechanical stress require additional structural reinforcement and secure cell mounting.
- Altitude: For applications at high altitudes, reduced atmospheric pressure can affect cooling efficiency and potentially impact battery performance.
For each environmental factor, define the expected range and peak conditions, then design appropriate mitigation strategies.
Physical Size and Weight Constraints
The physical dimensions and weight limitations of your application will significantly influence your battery pack design. Consider:
- Available space dimensions (length, width, height)
- Weight limitations
- Mounting considerations and orientation requirements
- Connector and cable routing needs
- Serviceability and accessibility requirements
These constraints will help determine your pack’s configuration, cell arrangement, and housing design. In some cases, you may need to make trade-offs between capacity, voltage, and physical constraints.
Battery Configuration Engineering
The arrangement of cells within your battery pack directly impacts its voltage, capacity, power delivery capabilities, and physical dimensions. Selecting the optimal configuration requires balancing these factors against your application’s specific requirements.
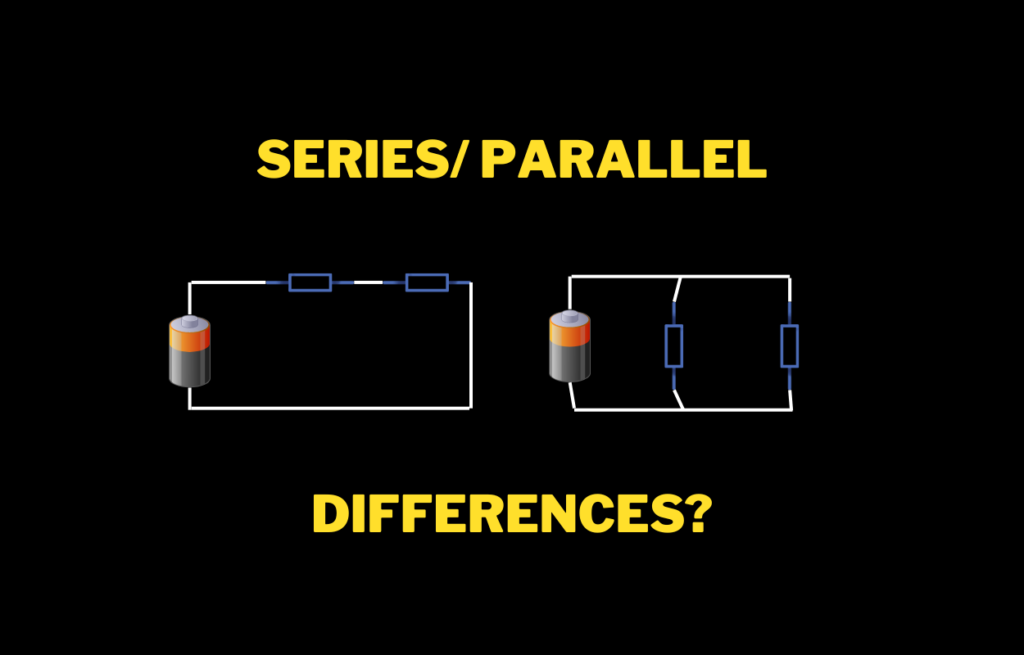
Series vs. Parallel Arrangements
Battery configurations are typically described using a nomenclature that indicates the number of cells in series and parallel. For example, a 4S3P configuration contains 4 cells in series and 3 cells in parallel, for a total of 12 cells.
Series connections increase voltage while maintaining the same capacity. When cells are connected in series (positive terminal to negative terminal), their voltages add together. This arrangement is essential for applications requiring higher voltages than a single cell can provide.
Parallel connections increase capacity while maintaining the same voltage. When cells are connected in parallel (positive terminal to positive terminal, negative to negative), their capacities add together. This arrangement is crucial for applications requiring longer runtime.
Series-parallel configurations combine both approaches to achieve both higher voltage and higher capacity. This is the most common arrangement for multi-cell battery packs, as it allows for flexible scaling to meet various requirements.
Mathematical Formulas for Configuration Design
Understanding the mathematical relationships in battery configurations helps design packs that precisely meet requirements:
For series connections:
- Total Voltage = Individual Cell Voltage × Number of Cells in Series
- Total Capacity = Individual Cell Capacity
For parallel connections:
- Total Voltage = Individual Cell Voltage
- Total Capacity = Individual Cell Capacity × Number of Cells in Parallel
For series-parallel configurations:
- Total Voltage = Individual Cell Voltage × Number of Series Groups
- Total Capacity = Individual Cell Capacity × Number of Cells per Parallel Group
Additionally, these formulas help calculate other important pack parameters:
- Maximum Continuous Discharge Current = Individual Cell Max Current × Number of Parallel Groups
- Internal Resistance (approximate) = (Individual Cell Resistance × Number of Series Groups) ÷ Number of Parallel Groups
These calculations provide the foundation for selecting the appropriate configuration based on your application requirements.
Optimizing for Specific Applications
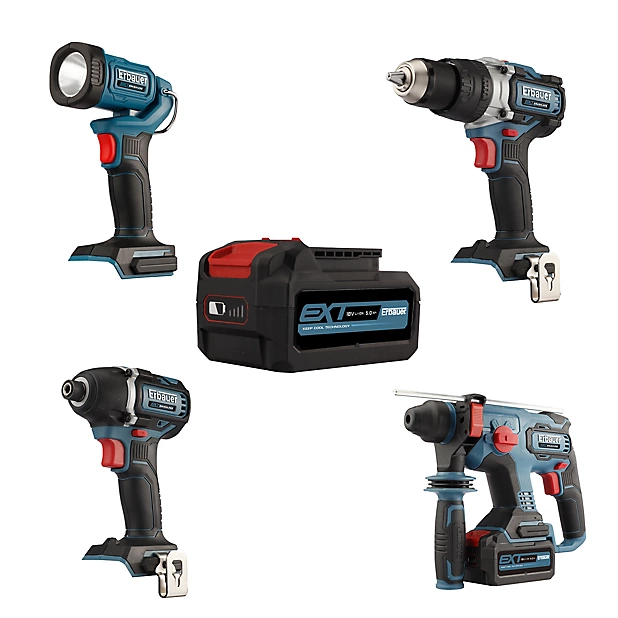
Different applications prioritize different performance aspects, requiring configuration optimization specific to their needs:
For high-power applications (such as power tools or drones):
- Prioritize low internal resistance
- Use cells with high discharge ratings
- Consider higher parallel counts to distribute current load
- Implement robust thermal management
For high-energy applications (such as electric vehicles):
- Focus on maximizing capacity while meeting voltage requirements
- Balance energy density with cycle life
- Optimize weight distribution and packaging efficiency
For long-life applications (such as energy storage systems):
- Select cells with excellent cycle life characteristics
- Implement conservative charge/discharge limits
- Prioritize thermal stability and consistent operating conditions
For cost-sensitive applications:
- Balance performance requirements with cell costs
- Consider simpler BMS designs where appropriate
- Optimize manufacturing processes for efficiency
The ideal configuration will often involve compromises between these various requirements, and finding the right balance requires experience and thorough understanding of the application context.
Balancing Power Requirements with Physical Constraints
Creating an optimal battery pack requires careful consideration of how the physical arrangement of cells impacts both performance and form factor:
Slim profile requirements might dictate a flat arrangement of cells, potentially limiting series connections but allowing for expanded parallel grouping. This approach works well for applications like laptops or tablets where thickness is the primary constraint.
Weight distribution becomes critical in applications like drones or portable equipment, where balance affects usability and performance. The cell arrangement should consider the center of gravity and how it influences the overall device.
Heat dissipation pathways are influenced by cell arrangement. Cells generate heat during operation, and your configuration should allow for efficient cooling, especially for cells located in the center of the pack.
Structural integrity considerations may require additional support structures or reinforcement, particularly for larger packs or those subject to vibration or impact.
3D modeling software has become essential for visualizing how different configurations will fit within available space, allowing for rapid iteration and optimization before physical prototyping begins.
Thermal Management Systems
Effective thermal management is critical for ensuring safety, longevity, and consistent performance in custom 18650 battery packs. As energy density continues to increase in 2025 cells, thermal considerations become even more significant.
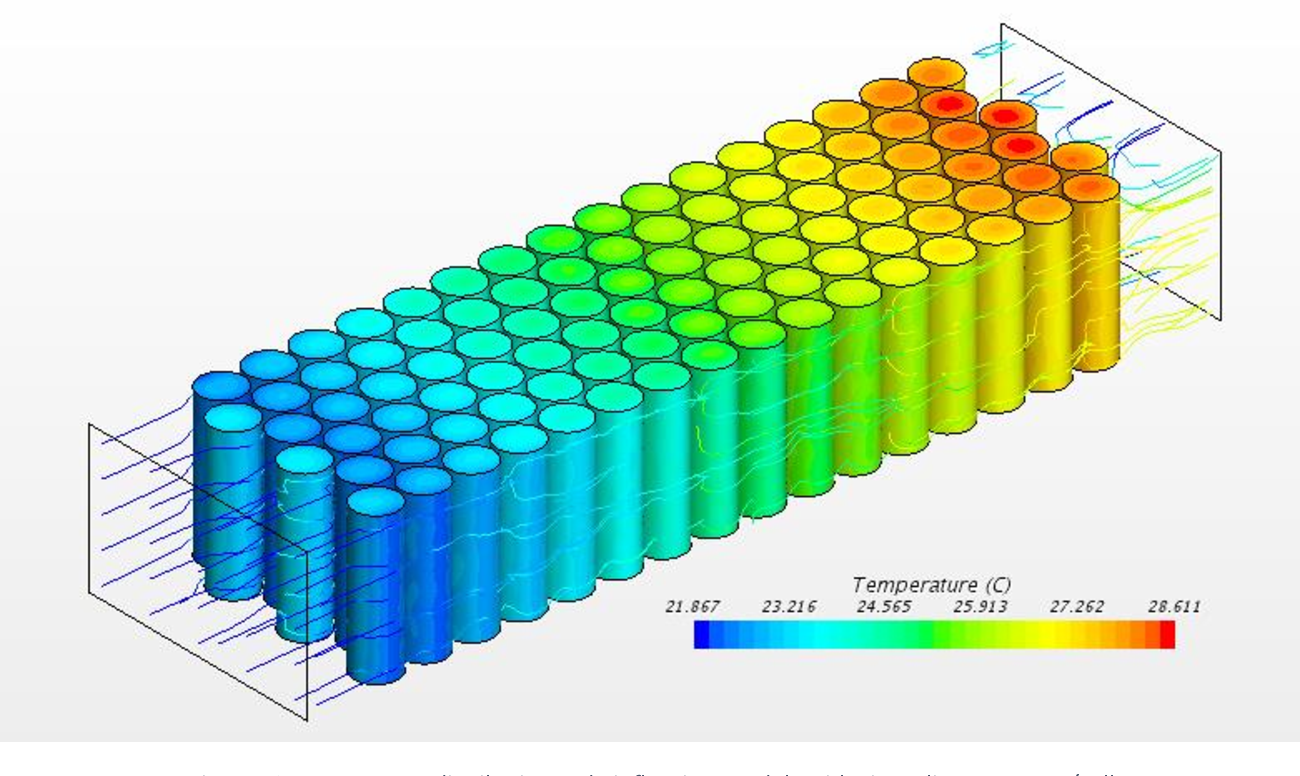
Understanding Heat Generation in Battery Packs
Heat in battery packs comes from three primary sources:
- Joule heating (I²R losses): As current flows through the cells and connections, resistance causes energy to be converted to heat. This effect increases exponentially with current, making it particularly significant during high-discharge applications.
- Electrochemical reactions: The chemical processes inside the cells generate heat during both charging and discharging. This heat generation varies with the specific chemistry and state of charge.
- Environmental factors: External temperature, solar radiation, and nearby heat sources can all contribute to the thermal load on a battery pack.
Understanding these heat sources helps identify critical thermal management needs for your specific application. For example, high-discharge applications will require solutions focused on managing Joule heating, while outdoor applications might need to address environmental temperature variations.
Passive Cooling Solutions
Passive cooling relies on natural physical processes without requiring additional energy input. These approaches are preferred for their simplicity, reliability, and lack of parasitic power draw:
Cell spacing provides air gaps between cells to increase surface area and allow for natural convection. The optimal spacing depends on the application’s thermal requirements, with typical gaps ranging from 0.5mm to 2mm.
Thermal interface materials (TIMs) improve heat transfer between cells and heat-dissipating structures. Modern TIMs used in 2025 include silicone-based compounds, phase change materials, and graphite sheets with thermal conductivities ranging from 3-25 W/m·K.
Phase change materials (PCMs) absorb heat during temperature spikes, storing it as latent heat during phase transition. Advanced PCMs in 2025 offer energy absorption of 180-250 J/g with transition temperatures carefully matched to the optimal operating range of lithium-ion cells.
Heat sinks increase the effective surface area for heat dissipation. Aluminum remains the preferred material for battery pack heat sinks due to its excellent balance of thermal conductivity, weight, and cost.
Active Cooling Techniques
Active cooling systems use powered components to enhance heat removal. While they add complexity and energy consumption, they provide superior cooling performance for demanding applications:
Forced air cooling uses fans to increase airflow across the battery pack. Modern designs often incorporate temperature-controlled variable-speed fans to optimize the balance between cooling performance and noise.
Liquid cooling circulates a coolant through channels in direct contact with or near the cells. This approach offers the highest cooling efficiency and temperature uniformity but requires pumps, radiators, and careful sealing to prevent leaks.
Thermoelectric cooling uses the Peltier effect to actively pump heat from one side of a device to another. While less common due to efficiency limitations, it allows for precise temperature control in specialized applications.
For high-performance applications in 2025, hybrid systems that combine passive and active cooling elements are increasingly common. These systems provide robust baseline cooling with supplemental active cooling that engages only when needed.
Materials Selection for Thermal Management
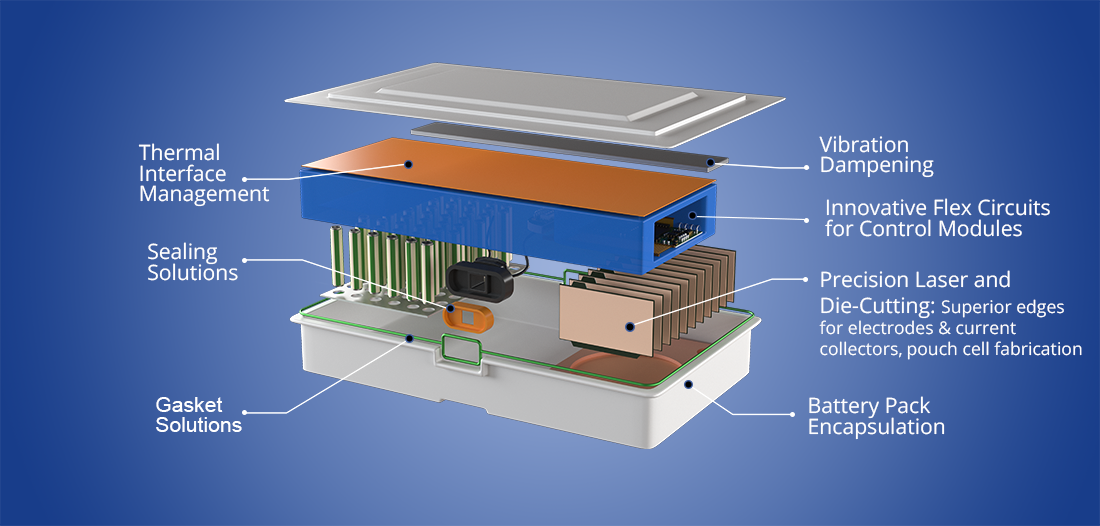
The choice of materials significantly impacts thermal management effectiveness:
Cell holders and structural components should balance thermal conductivity with electrical insulation requirements. Modern materials include specialized thermally conductive plastics with conductivities of 1-30 W/m·K while maintaining electrical insulation properties.
Enclosure materials must balance thermal performance with mechanical protection, environmental sealing, and aesthetic considerations. Aluminum remains popular for its excellent thermal properties, while composites and specialized polymers offer alternatives for specific requirements.
Thermal interface compounds continue to evolve, with 2025 seeing increased use of carbon nanotube and graphene-enhanced materials offering thermal conductivities exceeding 40 W/m·K while maintaining flexibility and long-term stability.
Heat dissipation structures typically use materials with high thermal conductivity such as aluminum (237 W/m·K) or copper (401 W/m·K). Recent advances in materials science have introduced carbon-fiber composites with directionally optimized thermal properties for specialized applications.
Battery Management System Integration
The Battery Management System (BMS) is the intelligence behind safe, efficient operation of any 18650 battery pack. Modern BMS solutions combine sophisticated protection features with advanced monitoring and optimization capabilities.
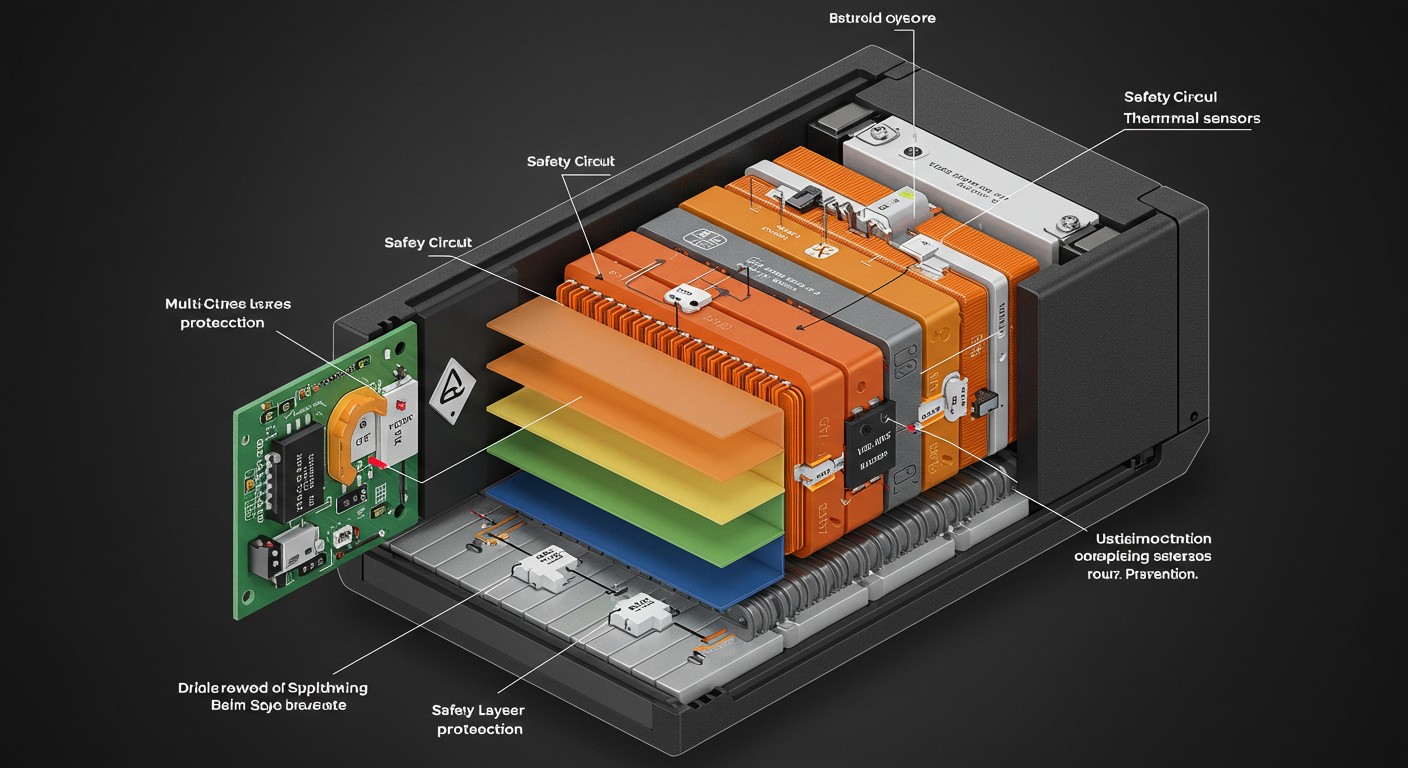
Core BMS Functions and Requirements
A comprehensive BMS performs several critical functions:
Cell protection is the primary role, preventing cells from operating outside safe parameters. This includes preventing overcharge, over-discharge, overcurrent, and operating outside safe temperature ranges.
Cell balancing ensures all cells in a series string maintain similar state of charge. This function is essential for maximizing usable capacity and preventing individual cells from experiencing stress conditions that could lead to premature failure.
State estimation provides information about the battery’s current condition, including state of charge (SoC), state of health (SoH), and state of function (SoF). These estimations help optimize performance and predict maintenance needs.
Thermal management monitoring and control ensure cells operate within their optimal temperature range, extending lifespan and maintaining performance.
Communication interfaces allow the BMS to report status information and receive commands from the host system, enabling integration with broader system management functions.
Protection Circuit Features
Modern protection circuits incorporate multiple layers of safety features to prevent hazardous conditions:
Overcurrent protection prevents excessive current draw that could damage cells or create dangerous heating. Advanced systems in 2025 feature multi-level protection with different thresholds and response times for various overcurrent scenarios.
Overvoltage protection during charging prevents cell damage by terminating charging when any cell reaches its maximum safe voltage (typically 4.2V for standard lithium-ion cells). Precision in this function is critical, with modern systems maintaining voltage accuracy within ±10mV.
Undervoltage protection prevents excessive discharge that could permanently damage cells. The BMS disconnects the load when any cell approaches its minimum safe voltage, typically 2.5-3.0V depending on the specific cell chemistry.
Short-circuit protection provides immediate response to external shorts, rapidly disconnecting the battery. Modern systems can detect and respond to short circuits in under 100 microseconds.
Temperature-based protection monitors cell and pack temperatures, disconnecting the battery if temperatures exceed safe operating ranges. Multiple temperature sensors throughout the pack ensure comprehensive monitoring of thermal conditions.
Monitoring and Data Collection
Advanced monitoring capabilities provide insights into battery performance and health:
Cell voltage monitoring tracks individual cell voltages, enabling the BMS to maintain balanced cell voltages through selective charging or discharging. High-precision analog-to-digital converters (ADCs) in 2025 BMSs achieve 14-16 bit resolution, allowing voltage measurements with sub-millivolt precision.
Current monitoring provides real-time data on charge and discharge rates. Hall-effect sensors or precision shunt resistors with dedicated measurement circuitry enable accurate current measurement across a wide range, typically from milliamps to hundreds of amps with better than 1% accuracy.
Temperature monitoring using strategically placed sensors throughout the pack helps identify hotspots and ensure operation within safe temperature ranges. Modern systems use digital temperature sensors with ±0.5°C accuracy or better.
Impedance tracking measures changes in cell internal resistance over time, providing early indications of cell aging or potential failure. This advanced feature is becoming standard in high-performance BMS solutions for 2025.
Smart BMS Capabilities for 2025
The evolution of battery management technology has introduced sophisticated “smart” features that enhance performance, safety, and user experience:
Artificial intelligence algorithms analyze battery usage patterns and environmental conditions to optimize charging and discharging parameters dynamically. These adaptive systems can extend battery life by 15-25% compared to traditional fixed-parameter approaches.
Predictive maintenance capabilities use historical data and real-time monitoring to forecast potential issues before they cause failures. By detecting subtle changes in performance metrics, the system can alert users to schedule maintenance or replacement.
Internet of Things (IoT) integration enables remote monitoring and management of battery systems. Users can access real-time status information, receive alerts, and even update BMS firmware remotely through secure cloud connections.
Energy optimization features dynamically adjust power delivery based on usage patterns and requirements, maximizing efficiency and extending runtime. These systems can prioritize critical functions and adjust performance parameters in real-time.
According to industry analysts, the market for smart BMSs is predicted to grow at a 19.1% compound annual growth rate through 2032, reaching an estimated market value of $41 billion.
Communication Protocols and Integration
Seamless integration with host systems requires appropriate communication interfaces and protocols:
CAN bus remains the industry standard for automotive and industrial applications due to its robustness and reliability. The latest CAN FD (Flexible Data-Rate) standard supports higher bandwidth for more comprehensive data reporting, with speeds up to 8 Mbps.
I²C and SPI interfaces provide efficient communication options for embedded applications. These protocols offer good balance of simplicity and functionality, though they lack the noise immunity and distance capabilities of CAN.
USB connectivity provides easy integration with computers and consumer electronics. Modern BMSs often implement USB Type-C with Power Delivery support, allowing for both data communication and power delivery through a single connection.
Bluetooth Low Energy (BLE) and Wi-Fi options enable wireless monitoring and control. BLE 5.3, standard in 2025 designs, offers extended range and improved coexistence with other wireless technologies, while remaining energy-efficient for battery-powered applications.
Connection Methods and Materials
The connections between cells represent potential points of failure in any battery pack. Implementing proven techniques and materials ensures reliable, low-resistance connections that maintain integrity throughout the battery’s lifespan.
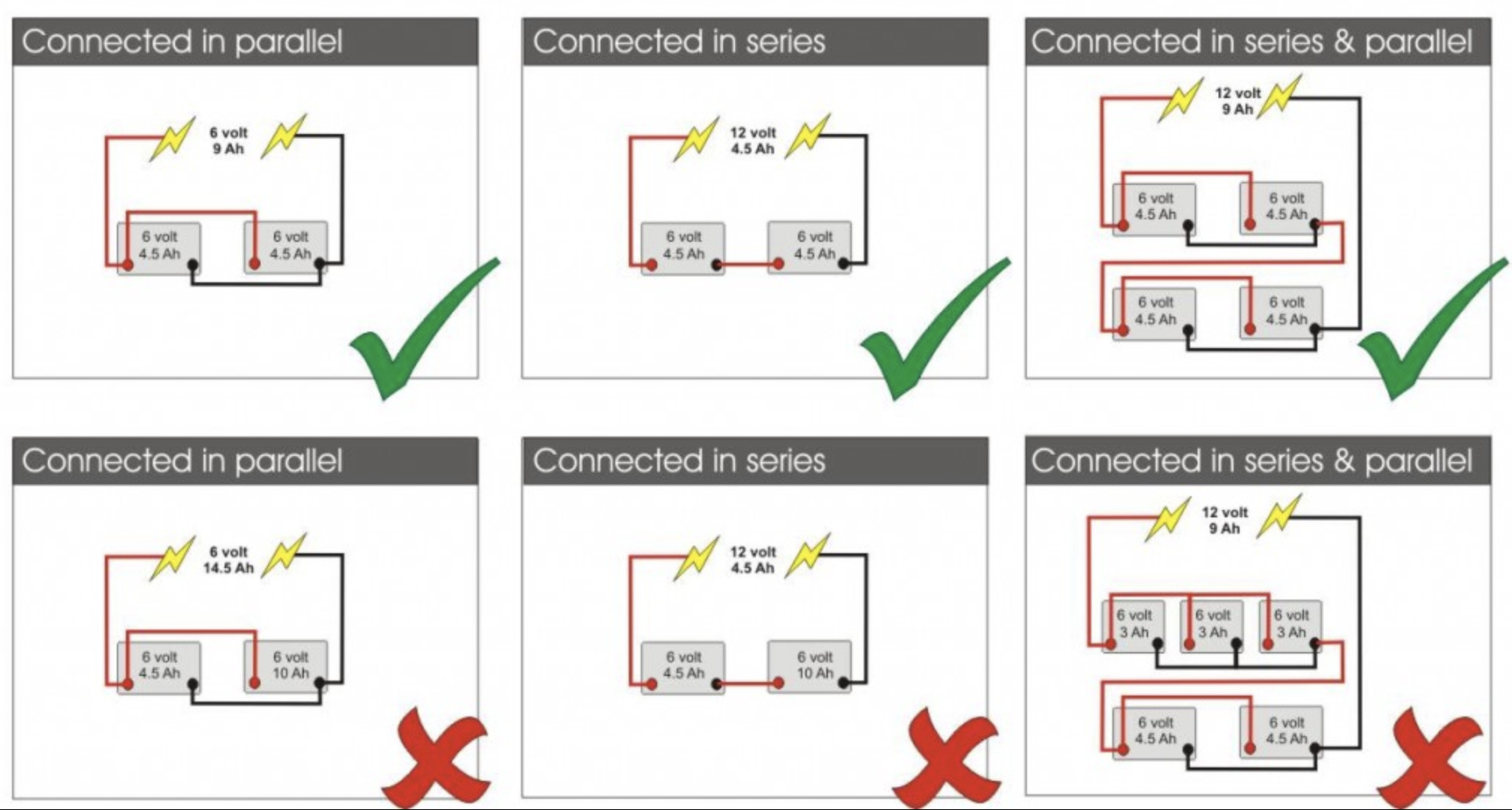
Cell Interconnect Options
Various methods exist for connecting 18650 cells, each with specific advantages for different applications:
Welded nickel strips provide low-resistance connections and excellent mechanical stability. These have become the industry standard for most applications due to their reliability and current-carrying capacity.
PCB-based interconnects integrate connection paths into a printed circuit board, enabling compact designs and simplified manufacturing for specific arrangements. Advanced flexible PCBs allow for three-dimensional cell arrangements with integrated temperature sensors and voltage monitoring.
Bus bar systems use solid copper or aluminum bars for high-current applications, offering extremely low resistance at the cost of increased weight and volume. These are typically used in larger industrial packs rather than consumer applications.
Spring contacts provide non-permanent connections that allow for cell replacement, though they typically have higher resistance than welded connections. These are sometimes used in applications where serviceability takes priority over maximum performance.
Spot Welding Techniques and Best Practices
Spot welding is the preferred method for connecting 18650 cells, as it creates strong, low-resistance connections without applying excessive heat to the cells:
Pulse intensity and duration must be carefully calibrated to the specific tab material and thickness. Too little energy results in weak connections, while excessive energy can damage the cell’s internal structure or safety features.
Weld patterns should distribute mechanical stress and current flow. Multiple welds per connection (typically 2-4) ensure redundancy and reduce the current through any single weld point.
Tab material selection impacts weld quality and long-term reliability. Pure nickel (Ni200/201) provides excellent conductivity with good weldability, while nickel-plated steel offers higher mechanical strength at the cost of slightly higher resistance.
Electrode maintenance is critical for consistent weld quality. Regular cleaning and dressing of electrodes prevent contamination and deformation that could lead to suboptimal welds.
For high-volume production, automated welding systems with computer-controlled parameters and vision-based quality verification ensure consistent, reliable connections with minimal rejects.
Wire Gauge Selection and Considerations
Proper wire sizing is critical for external connections to prevent voltage drop and heat generation:
Current capacity is the primary consideration for wire gauge selection. As a rule of thumb, high-quality silicone-insulated wire can carry approximately 5A per square millimeter of cross-sectional area with minimal heating.
Voltage drop calculations should account for wire length and current. For most applications, limiting voltage drop to less than 2% of system voltage is recommended.
Temperature rating of wire insulation must match the expected operating environment. Modern silicone insulation typically offers ratings from -60°C to +200°C, making it suitable for most battery applications.
Flexibility requirements influence both conductor and insulation selection. Applications with frequent movement or vibration benefit from finer stranded conductors and more flexible insulation materials.
This table provides general guidelines for wire sizing in 18650 battery pack applications:
Maximum Current | Recommended AWG | Cross-Sectional Area | Typical Application |
---|---|---|---|
5A | 18 AWG | 0.82 mm² | Small consumer devices |
10A | 16 AWG | 1.31 mm² | Medium-power applications |
20A | 12 AWG | 3.31 mm² | High-power portable equipment |
30A | 10 AWG | 5.26 mm² | Electric vehicles, power tools |
50A | 8 AWG | 8.36 mm² | High-current applications |
These recommendations assume copper conductors with high-quality insulation and ambient temperatures below 50°C.
Connector Types and Applications
Selecting appropriate connectors ensures reliable power delivery and prevents accidental disconnection or incorrect connections:
XT60/XT90 connectors have become industry standards for medium to high-power applications, handling up to 60A and 90A respectively. Their polarized design prevents reverse connection, and the gold-plated contacts provide low contact resistance and corrosion resistance.
Anderson Powerpole connectors offer modular design and are self-cleaning due to their wiping contact action. They’re rated for multiple connection cycles and maintain low contact resistance even after thousands of mate/unmate cycles.
Battery-specific terminal designs for permanent or semi-permanent installations often use M5-M8 bolted connections with proper torque specifications to ensure low-resistance connections that remain stable over time.
Balance connectors (such as JST-XH) provide access to individual cell voltages for monitoring and balancing. These typically handle only low currents but are essential for BMS connections in series configurations.
For applications requiring frequent connection/disconnection, consider connectors with additional features such as locking mechanisms, environmental sealing, or quick-disconnect capabilities.
Quality Control and Testing Protocols
Comprehensive testing is essential to verify battery pack performance, safety, and reliability. A structured testing program identifies potential issues before they reach customers and provides data for continuous improvement.
Cell Testing and Validation

Individual cell testing provides the foundation for pack quality by ensuring all cells meet specifications:
Capacity verification measures actual capacity under controlled conditions, typically by fully charging the cell and then discharging at 0.5C rate while measuring energy output. Industry standards require cells to deliver at least 95% of rated capacity when new.
Internal resistance measurement identifies cells with abnormally high resistance that could cause performance issues or safety concerns. This is typically measured using either AC impedance methods or DC pulse techniques.
Self-discharge testing identifies cells with manufacturing defects or contamination issues. High-quality 18650 cells should demonstrate self-discharge rates below 3% per month at room temperature.
Cycling performance evaluates capacity retention over multiple charge-discharge cycles. Accelerated testing might perform hundreds of cycles at elevated rates or temperatures to predict long-term performance.
Statistical process control methods help identify trends or shifts in cell performance that might indicate manufacturing issues, allowing for early intervention before problems become widespread.
Pack-Level Testing Requirements
Once assembled, the complete battery pack undergoes testing to verify overall performance and safety:
Functional testing verifies all aspects of pack operation, including charging, discharging, protection features, and BMS functionality. This typically includes testing at minimum, nominal, and maximum specified current rates.
Environmental testing exposes the pack to expected operating conditions, including temperature extremes, humidity, vibration, and shock. These tests verify performance across the specified environmental range and ensure the pack can withstand expected mechanical stresses.
Abuse testing deliberately subjects the pack to beyond-specification conditions to verify safety features. This includes short-circuit testing, overcharge testing, over-discharge testing, and in some cases, penetration or crush testing.
Thermal performance evaluation measures temperature rise during operation and verifies that all cells remain within safe temperature limits even under worst-case conditions.
These tests should be designed to reflect real-world usage patterns while ensuring all specifications are verified.
Safety Certification Standards
Various standards govern battery safety for different applications and markets:
UN 38.3 certification is required for lithium battery transportation and covers tests including altitude simulation, thermal cycling, vibration, shock, external short circuit, impact, overcharge, and forced discharge.
IEC 62133 addresses safety requirements for portable sealed secondary cells and batteries containing alkaline or other non-acid electrolytes, covering both mechanical and electrical tests.
UL 1642/UL 2054 standards apply to batteries used in the United States market, with comprehensive requirements for safety under normal and abnormal conditions.
IEC 61960 specifies performance tests, designations, markings, dimensions and other requirements for lithium secondary cells and batteries for portable applications.
Certification typically requires testing by accredited third-party laboratories, with documentation that must be maintained and updated as designs change.
Reliability Testing Methodologies
Advanced reliability testing helps predict long-term performance and identify potential failure modes:
Accelerated life testing applies stress factors (such as elevated temperature, increased cycling rates, or higher currents) to compress time and predict long-term reliability. Mathematical models correlate accelerated test results with expected real-world performance.
Highly Accelerated Life Testing (HALT) subjects packs to progressively increasing stress levels to identify design weaknesses. This approach helps establish design margins and improve robustness.
Failure mode and effects analysis (FMEA) systematically evaluates potential failure modes, their effects, and mitigations. This process-driven approach helps identify and address risks before they manifest in field failures.
Statistical lifetime modeling uses test data to develop predictive models for battery pack aging and wear-out. These models help establish realistic warranty periods and maintenance intervals.
Quality Assurance Checkpoints
Manufacturing processes incorporate multiple quality checkpoints to catch any issues before they reach the final product:
Incoming Quality Control (IQC) verifies all components meet specifications before entering production. For 18650 cells, this typically includes dimensional checks, visual inspection, and verification of electrical parameters.
In-Process Quality Control (IPQC) monitors critical processes during assembly, including welding quality, insulation integrity, and component placement. This often incorporates automated optical inspection and electrical testing at intermediate stages.
Final Quality Assurance (FQA) provides comprehensive verification of the completed pack. This includes visual inspection, electrical testing, functional verification, and safety feature validation.
Lot traceability systems maintain records linking each pack to its component batch information, test results, and manufacturing data. This enables effective management of any issues that might arise after production.
Manufacturing Process Overview
The manufacturing process for custom 18650 battery packs combines precision engineering with rigorous quality control to ensure performance, safety, and reliability.
Design and Planning Phase
The manufacturing journey begins with comprehensive design and planning:
Requirements specification clearly defines all performance, safety, and physical parameters the pack must meet. This document guides all subsequent design decisions and serves as the baseline for verification testing.
3D modeling and simulation creates detailed digital representations of the pack, allowing for interference checking, thermal analysis, and structural evaluation before any physical prototyping begins. Modern computational fluid dynamics (CFD) simulations can predict thermal behavior with high accuracy.
Design for Manufacturing (DFM) review identifies potential manufacturing challenges early in the design process. This collaborative process involves design engineers, manufacturing specialists, and quality assurance personnel working together to optimize the design for both performance and producibility.
Prototype development validates the design concept through physical models that undergo preliminary testing. Multiple prototype iterations may be required to refine the design before production release.
Component Sourcing Considerations
The quality of input materials directly impacts final product performance:
Cell procurement strategies should include vendor qualification, incoming inspection protocols, and batch testing programs. For critical applications, direct relationships with cell manufacturers provide better quality assurance than working through distributors.
BMS component selection requires careful evaluation of both technical specifications and reliability history. For critical components like protection ICs, MOSFETs, and voltage reference devices, established suppliers with proven track records are preferred.
Mechanical components including cases, brackets, and insulators must meet dimensional, thermal, and mechanical specifications. Supplier quality management systems should be evaluated as part of the qualification process.
Supply chain resilience has become increasingly important, with dual-sourcing strategies and appropriate inventory buffers helping mitigate disruption risks. This is particularly important given the global supply chain challenges that have affected battery materials in recent years.
Assembly Techniques and Equipment
Battery pack assembly requires specialized equipment and techniques to ensure quality and consistency:
Automated cell testing and sorting systems verify and match cells before assembly. Advanced systems in 2025 can test and sort cells based on multiple parameters simultaneously, ensuring optimal grouping for pack assembly.
Precision welding equipment for cell connections includes microprocessor-controlled resistance welders, laser welding systems, or ultrasonic welding for specific applications. These systems provide precise control over weld energy and include monitoring features to verify weld quality.
Automated circuit assembly for the BMS typically uses standard surface-mount technology (SMT) processes with specialized testing for battery-specific functions. In-circuit testing and functional testing verify correct assembly before integration with cells.
Pack assembly fixtures ensure precise alignment and support during assembly operations. These often include poka-yoke (mistake-proofing) features to prevent assembly errors.
Environmental controls maintain appropriate temperature, humidity, and cleanliness during assembly. This is particularly important for processes like adhesive application or encapsulation that are sensitive to environmental conditions.
Quality Control Integration
Quality control is fully integrated throughout the manufacturing process:
Statistical Process Control (SPC) monitors key process parameters in real-time, allowing for immediate detection and correction of trends before they result in defects. Critical parameters like weld strength, connection resistance, and dimensional accuracy are continuously tracked.
Automated optical inspection systems verify component placement, connection quality, and assembly completeness. Modern systems incorporate artificial intelligence to identify subtle defects that might be missed by traditional machine vision approaches.
In-line electrical testing verifies functionality at multiple stages during assembly. This includes continuity testing, insulation resistance verification, and functional testing of protection circuits.
End-of-line testing provides comprehensive verification of the completed pack, including capacity testing, cycle testing, and verification of all safety features. Automated test systems record detailed results for each pack, maintaining traceability throughout the product lifecycle.
Continuous improvement processes use manufacturing and testing data to identify opportunities for process refinement. This closed-loop approach leads to ongoing quality improvements and manufacturing efficiency gains.
Application-Specific Design Considerations
Different applications place unique demands on battery packs, requiring tailored design approaches to achieve optimal performance.
Electric Vehicle Battery Packs
Electric vehicle applications represent some of the most demanding requirements for 18650-based battery packs:
Energy density optimization is critical for maximizing vehicle range while managing weight and volume constraints. This often involves trade-offs between different cell chemistries and pack configurations.
Thermal management requirements are particularly stringent due to high charge and discharge rates, especially during fast charging and performance driving. Advanced liquid cooling systems with precise temperature control have become standard in 2025 designs.
Safety features must address the unique risks associated with automotive applications, including crash protection, isolation monitoring, and multiple redundant protection mechanisms. Additional requirements include first responder access and disconnection provisions.
Longevity considerations must account for typical vehicle lifespans of 10-15 years and daily usage patterns. Battery warranty requirements of 8-10 years are now standard, requiring careful cell selection and conservative operational parameters.
Integration with vehicle systems includes communication with powertrain controllers, charging systems, thermal management, and diagnostics. Standard protocols like CAN facilitate this integration while enabling manufacturer-specific optimizations.
Energy Storage Systems
Stationary energy storage applications prioritize different characteristics than mobile applications:
Cycle life often takes precedence over energy density, as space constraints are typically less restrictive. This has led to increased adoption of LFP chemistry in stationary applications due to its excellent cycle life despite lower energy density.
Scalability is essential for energy storage systems, with modular designs allowing for capacity expansion as needs grow. Standard interfaces for both electrical connections and communications facilitate this scalability.
Environmental considerations must account for outdoor installation in many cases, requiring robust enclosures with appropriate IP (Ingress Protection) ratings and operating temperature ranges that can span from -30°C to +50°C.
Grid integration features include advanced inverter control, frequency regulation capabilities, and load-shifting optimization. The ability to respond to grid signals for demand response programs adds additional value.
Safety and compliance requirements include UL9540 for energy storage systems, fire suppression considerations, and compliance with local building and electrical codes. These requirements continue to evolve as the industry grows.
Industrial Equipment Applications
Industrial applications such as automated guided vehicles (AGVs), robots, and machinery place unique demands on battery systems:
Operational reliability takes highest priority, with robust design, comprehensive monitoring, and predictive maintenance capabilities essential for minimizing downtime.
Fast charging capabilities support multiple shifts or continuous operation. Modern industrial battery systems can achieve 80% charge in as little as 30 minutes while maintaining long-term reliability.
Integration with facility systems allows for automated charging scheduling, maintenance planning, and operational optimization. This often includes fleet management software that tracks battery status across multiple units.
Environmental resistance must address industrial environments that may include dust, vibration, electromagnetic interference, and occasional impacts. Robust mechanical design and appropriate sealing are essential.
Standardization across equipment fleets simplifies maintenance and reduces spare parts inventory requirements. This has led to the emergence of several de facto standard battery configurations in specific industrial segments.
Consumer Electronics Requirements
Consumer electronics applications prioritize form factor, weight, and user experience:
Compact design is essential, often requiring custom cell arrangements and innovative packaging solutions to maximize energy density within strict dimensional constraints.
Safety certifications for consumer products are mandatory, with requirements varying by market. UL, CE, and other regional certifications must be obtained before products can be sold.
User-friendly features include intuitive state-of-charge indication, simplified charging interfaces, and plug-and-play operation. The technical complexity of the battery system should be invisible to the end user.
Aesthetic integration with product design requires attention to details like surface finishes, colors, and textures. The battery pack is increasingly viewed as an integral part of product design rather than a purely functional component.
Cost optimization is particularly important in consumer markets, requiring careful balance between performance, features, and manufacturing costs to achieve competitive price points.
Troubleshooting and Maintenance
Even well-designed battery packs require maintenance and occasionally troubleshooting to ensure optimal performance throughout their lifecycle.
Common Failure Modes
Understanding typical failure modes helps in both prevention and diagnosis:
Cell imbalance occurs when individual cells in a series string develop different voltage levels. This reduces usable capacity and, if severe, can lead to safety issues as some cells may be overcharged while others remain undercharged.
Capacity degradation happens gradually as cells age, typically manifesting as reduced runtime. While some degradation is inevitable, the rate can be influenced by operating conditions and charging practices.
Connection resistance increases develop over time due to oxidation, thermal cycling, or mechanical stress. These manifest as voltage drop under load, reduced power delivery, and increased heating.
BMS failures can include sensor inaccuracies, communication errors, or component failures. These may result in unnecessary protection triggering or, more seriously, failure to provide proper protection.
Thermal management issues include clogged air passages, fan failures, or degraded thermal interface materials. These lead to higher operating temperatures, accelerated aging, and potential safety concerns.
Diagnostic Procedures
Systematic troubleshooting approaches help identify issues efficiently:
Voltage measurements at both pack and individual cell levels provide fundamental diagnostic information. Unexpected voltage differentials often point directly to problem areas.
Load testing reveals performance under actual operating conditions. Comparing current performance to baseline measurements helps quantify degradation and identify abnormal behavior.
Thermal imaging during operation can identify hotspots that might indicate high-resistance connections or cell issues. This non-contact approach is particularly valuable for detecting problems not apparent from electrical measurements alone.
BMS error code analysis interprets diagnostic information from the battery management system. Modern BMSs store detailed event logs that can help identify intermittent issues or patterns of abnormal behavior.
Impedance spectroscopy, while requiring specialized equipment, provides detailed insights into cell health beyond what simpler measurements can reveal. This technique is particularly valuable for high-value battery systems where detailed diagnostic information justifies the equipment investment.
Maintenance Best Practices
Regular maintenance extends battery life and prevents many common issues:
Scheduled inspections should include visual examination for physical damage, connection integrity verification, and cleaning of cooling passages or heat sink surfaces.
Performance verification testing on a regular schedule establishes trends and identifies gradual degradation before it becomes problematic. This typically includes capacity testing and internal resistance measurements.
Firmware and software updates ensure the BMS benefits from the latest algorithms and feature improvements. Many modern systems support remote updates, simplifying this maintenance task.
Environmental control maintenance includes cleaning or replacing air filters, verifying proper function of cooling systems, and ensuring installation areas remain within specified temperature and humidity ranges.
Documentation of all maintenance activities, test results, and observations provides valuable historical data for troubleshooting and lifecycle management.
Repair vs. Replace Decision Matrix
When issues are identified, systematic decision processes help determine the appropriate response:
Economic analysis compares repair costs to replacement costs, considering both immediate expenses and long-term implications. As battery pack prices continue to decrease, the economic threshold for replacement versus repair shifts accordingly.
Safety considerations take precedence over economic factors. Any indication of safety-related degradation typically indicates replacement rather than repair, particularly for lithium-ion chemistry.
Performance requirements must be reevaluated against current capacity and capabilities. Applications with evolving needs may benefit from upgrades rather than exact replacements.
Availability factors include lead times for replacement components or complete packs. Critical applications may justify keeping spare assemblies on hand to minimize downtime.
Environmental impact considerations include recycling options for replaced components and the lifecycle carbon footprint of repair versus replacement. Responsible end-of-life management has become increasingly important as battery volumes grow.
Conclusion
Designing custom 18650 battery packs requires a methodical approach that balances multiple competing factors: performance requirements, physical constraints, safety considerations, thermal management, and economic realities. The comprehensive guidelines we’ve outlined provide a roadmap to navigate these complex decisions with confidence.
Key takeaways from this engineering guide include:
- Carefully matching cell specifications (chemistry, capacity, discharge rate) to your specific application requirements
- Calculating optimal series-parallel configurations using validated mathematical formulas
- Implementing appropriate thermal management strategies based on discharge profiles
- Integrating intelligent BMS features for enhanced safety and performance monitoring
- Following rigorous testing protocols to ensure reliability and compliance
The field continues to evolve rapidly, with advances in cell chemistry pushing energy densities higher, AI-enhanced BMS capabilities enabling predictive maintenance, and advanced thermal management techniques improving safety margins. Staying current with these developments is essential for designing competitive battery solutions in 2025 and beyond.
At VADE Battery, we specialize in translating these technical principles into custom rechargeable 18650, Li-ion, Lithium polymer, and LiFePO4 battery packs for customers worldwide. Our engineering team has delivered over 500 custom battery solutions with a 99.7% reliability rate, making us a trusted partner for companies requiring high-performance power solutions.
Ready to start your custom battery pack project? Contact our engineering team today at service@vadebattery.com for a free consultation or download our 18650 battery pack specification worksheet to begin defining your requirements.
For more information on specific aspects of battery technology, visit our related articles on dual battery system setup, custom battery voltage considerations, and series vs. parallel battery configurations.