Navigating the complex landscape of high-drain 18650 lithium-ion batteries presents a significant challenge for engineers, manufacturers, and enthusiasts requiring reliable power for demanding applications. With discharge requirements ranging from 20 to 35 amperes, these specialized cells demand careful selection to prevent performance failures, thermal issues, and safety hazards. This comprehensive technical guide, backed by laboratory testing and field experience, examines the specific electrical, thermal, and chemical characteristics that distinguish high-performance 18650 cells capable of delivering consistent power under extreme loads. Whether you’re designing battery packs for electric vehicles, professional power tools, or advanced portable devices, understanding the critical parameters outlined in this analysis will enable you to optimize performance, extend operational lifespan, and ensure safety across your high-drain applications.
Understanding High-Drain Battery Requirements
High-drain applications demand batteries capable of delivering substantial current over extended periods without performance degradation. These applications typically require batteries that can sustain discharge rates of 20A to 30A or higher while maintaining stable voltage output. Industries ranging from electric vehicles to power tools depend on these robust power sources to function optimally in challenging conditions.
The concept of high-drain refers specifically to a battery’s ability to deliver significant current output efficiently. Unlike standard batteries designed for low-power electronics, high-drain 18650 batteries feature specialized internal chemistry and construction that enables them to handle substantial power demands without overheating or suffering premature capacity loss. This capability makes them indispensable in scenarios where consistent power delivery is critical.
Defining High-Drain Power Demands
High-drain power demands are characterized by current requirements that exceed typical consumer electronics needs. While standard devices might draw 1-2 amperes, high-drain applications often pull 10-30 amperes continuously. This substantial current flow generates heat and places significant stress on battery components, requiring specialized design considerations to prevent failure or safety incidents.
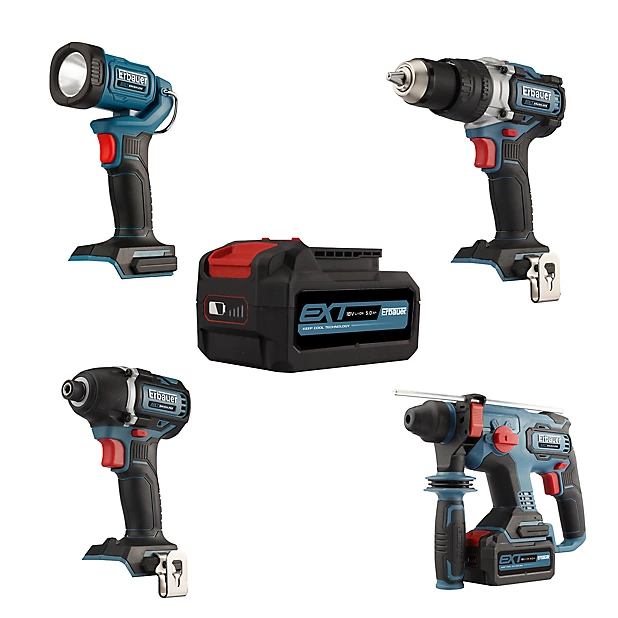
Power tools represent a classic example of high-drain applications, with cordless drills, saws, and impact drivers drawing substantial current during operation. These tools require batteries that can deliver bursts of high current while maintaining sufficient voltage to power motors effectively. Similarly, electric vehicles depend on high-drain batteries to provide acceleration and sustained performance during operation.
Cold Cranking Amp Principles in Battery Performance
Cold Cranking Amp (CCA) ratings, traditionally associated with lead-acid automotive batteries, share conceptual similarities with high-drain lithium battery performance metrics. Both measure a battery’s ability to deliver substantial current under demanding conditions. In high-drain 18650 applications, the principle translates to maintaining consistent voltage under heavy load, even as the battery discharges.
This sustained high-current delivery capability depends on several factors, including electrode design, electrolyte composition, and internal resistance. Batteries with lower internal resistance can deliver higher currents with less voltage drop, making them ideal for high-drain applications. Modern high-drain 18650 cells typically feature internal resistance values below 20mΩ, enabling efficient power delivery even under extreme demands.
Common Applications Requiring High-Drain Performance
Electric vehicles represent one of the most demanding applications for high-drain batteries. Tesla famously used thousands of 18650 cells in early Model S battery packs, requiring cells that could deliver consistent performance under variable load conditions. The automotive industry continues to rely on high-drain cells to power everything from hybrid vehicles to fully electric models.
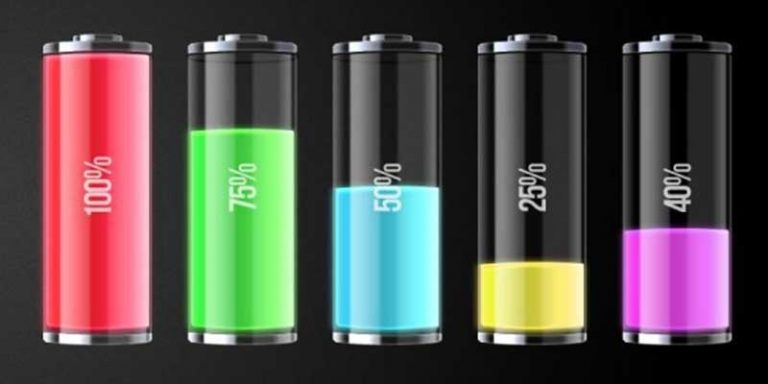
Power tools constitute another significant application category, with manufacturers like DeWalt, Milwaukee, and Makita building tool lines around high-drain battery packs. These tools require cells capable of delivering 15-30A discharge rates to power high-torque motors effectively. The ability to maintain performance through multiple high-current discharge cycles directly impacts tool reliability and runtime.
Vaping devices have emerged as another prominent high-drain application, with modern vaporizers drawing 20-30A during operation. These devices require batteries that can deliver high current safely while fitting within compact form factors. VADE Battery’s high-drain 18650 cells are specifically engineered to meet these demanding requirements while maintaining safety and performance.
Safety Considerations in High-Power Applications
Safety becomes particularly critical in high-drain applications due to the elevated current levels and associated heat generation. A primary concern involves thermal management, as high current flow generates significant heat that must be dissipated effectively to prevent dangerous temperature increases. Proper cell spacing and thermal insulation within battery packs help manage heat and prevent thermal runaway scenarios.
Battery protection circuits represent another essential safety element in high-drain applications. These circuits monitor current, voltage, and temperature parameters to prevent dangerous operating conditions. For applications drawing substantial current, protection circuits must be designed to handle high power levels without introducing excessive resistance that would impair performance.
Proper storage and handling procedures also contribute significantly to safety in high-drain applications. Batteries should never be exposed to extreme temperatures, which can trigger thermal runaway or cause internal damage. Similarly, metal objects should be kept away from battery terminals to prevent short circuits that could result in dangerous current spikes and potential fire hazards.
Top-Performing 18650 Cells for High-Drain Applications
Selecting the optimal 18650 cell for high-drain applications requires careful consideration of technical specifications and performance characteristics. Leading manufacturers have developed specialized high-drain cells offering exceptional performance across various demanding applications. Understanding the technical differences between these cells enables informed selection based on specific application requirements.
Technical Specifications of Leading High-Drain Cells
Molicel 18650 batteries stand among the top performers in high-drain applications, with their 2800mAh model capable of delivering an impressive 35A maximum discharge current. This exceptional current handling capability comes with minimal voltage sag under load, making these cells ideal for applications requiring significant power bursts. With an internal resistance of approximately 15mΩ, Molicel cells maintain efficiency even under extreme demands.
Sanyo 18650 batteries offer excellent balance between capacity and current handling. Their 3500mAh cell delivers stable performance under medium-high drain applications with a continuous discharge rating of 10A. This makes them particularly suitable for applications requiring extended runtime alongside reliable power delivery. The stable discharge platform of Sanyo cells ensures consistent performance throughout the discharge cycle.
Vapcell K25 18650 batteries specialize in extreme high-drain applications with their 2500mAh cell delivering 20A continuous discharge and 35A pulse discharge capabilities. This exceptional current handling makes them ideal for applications requiring short bursts of extremely high power. Their nominal voltage of 3.7V and flat top design facilitate efficient integration into multi-cell battery packs for high-power systems.
Discharge Curve Analysis and Performance Comparisons
Discharge curve analysis reveals significant performance differences between high-drain 18650 cells under load conditions. Premium high-drain cells maintain relatively flat voltage curves throughout much of the discharge cycle, typically holding above 3.6V until 70-80% depth of discharge when delivering moderate currents. This voltage stability ensures consistent power delivery to the connected device throughout the operating period.
In contrast, standard 18650 cells exhibit steeper voltage decline under high-current conditions, with voltage dropping below usable levels at just 40-50% depth of discharge. This premature voltage sag results in apparent capacity loss and reduced runtime in high-drain applications. When selecting cells for high-drain applications, prioritizing those with stable discharge curves ensures optimal performance and prevents unexpectedly short runtimes.
Comparative testing between leading high-drain cells reveals that capacity ratings alone fail to predict real-world performance under load. A 3000mAh cell with poor high-drain characteristics may deliver less usable energy than a 2500mAh cell specifically designed for high-current applications. This phenomenon results from the voltage sag that occurs when standard cells encounter high current demands, effectively reducing their usable capacity in demanding applications.
Temperature Effects on High-Drain Performance
Temperature significantly impacts high-drain battery performance, with both high and low temperatures potentially limiting current delivery capabilities. At low temperatures (below 0°C), internal cell resistance increases substantially, reducing maximum current delivery by 30-50% compared to room temperature performance. This reduced capability must be considered when designing systems operating in cold environments.
High temperatures present different challenges, potentially enabling higher current delivery but accelerating degradation and creating safety concerns. Above 45°C, many high-drain cells can temporarily deliver higher currents due to reduced internal resistance. However, operating at elevated temperatures significantly reduces cell lifespan and may activate thermal protection systems in battery management circuits.
For optimal high-drain performance across temperature ranges, VADE Battery’s custom lithium battery manufacturing process incorporates advanced thermal management considerations. This approach ensures reliable performance across diverse operating conditions while maintaining safety margins and maximizing battery longevity even in demanding high-drain applications.
Balancing Capacity vs. Power Output in Cell Selection
The fundamental tradeoff between capacity and current handling capability represents a critical consideration in 18650 cell selection. Higher capacity cells typically incorporate thicker electrode materials that increase energy density but also raise internal resistance, limiting maximum current delivery. Conversely, high-drain specialized cells often sacrifice some capacity to achieve lower internal resistance and superior current handling.
Applications requiring maximum runtime might benefit from higher capacity cells provided their current demands remain moderate. For example, LED flashlights drawing 2-3A might perform better with 3500mAh cells than with 2500mAh high-drain variants. However, devices drawing over 10A will likely achieve better overall performance with dedicated high-drain cells despite their somewhat lower nominal capacity ratings.
Understanding the actual energy delivery capabilities under specific load conditions enables informed selection between capacity-optimized and power-optimized cells. VADE Battery offers specialized guidance on battery load testing to help customers evaluate real-world performance under application-specific conditions rather than relying solely on datasheet specifications that may not reflect actual usage scenarios.
Custom Pack Design for Optimal High-Drain Performance
Creating effective battery packs for high-drain applications requires careful consideration of cell configuration, thermal management, protection circuitry, and mechanical design. Custom pack design enables optimization across these parameters to achieve maximum performance within specific application constraints. Understanding key design principles facilitates development of battery solutions that excel in demanding high-drain environments.
Series vs. Parallel Configurations for Different Requirements
Battery configuration fundamentally impacts voltage, capacity, and current delivery capabilities in high-drain applications. Series connections increase pack voltage while maintaining the capacity (ampere-hours) of individual cells. For example, connecting two 3.6V 2500mAh cells in series creates a 7.2V 2500mAh pack suitable for higher voltage applications while retaining the current handling capabilities of the component cells.
Parallel connections maintain voltage while increasing capacity and maximum current handling capability. Connecting two 3.6V 2500mAh cells in parallel creates a 3.6V 5000mAh pack capable of delivering twice the current of a single cell. This configuration proves particularly valuable in high-drain applications requiring maximum current delivery but moderate voltage.
Series-parallel configurations combine both approaches to achieve desired voltage and capacity characteristics simultaneously. These configurations require careful cell matching to prevent uneven loading that could compromise performance and safety. VADE Battery’s expertise in series-parallel battery configurations ensures optimal performance in custom high-drain battery packs requiring specific voltage and capacity specifications.
Heat Management in High-Current Applications
Thermal management represents a critical consideration in high-drain battery pack design due to substantial heat generation during high-current operation. Effective thermal design prevents hotspots and maintains cell temperatures within optimal operating ranges, typically between 20-40°C. Temperature gradients within packs can lead to performance imbalances and accelerated degradation of cells exposed to higher temperatures.
Physical cell spacing within packs significantly impacts thermal performance by facilitating airflow and preventing heat concentration. Sophisticated designs incorporate thermal padding between cells to dissipate heat while maintaining electrical isolation. For extremely high-drain applications, active cooling systems using forced air or liquid cooling may be incorporated to maintain optimal operating temperatures even under sustained high-current operation.
Thermal design considerations extend beyond normal operation to include fault scenarios where individual cells might generate excessive heat. VADE Battery incorporates advanced thermal management techniques in their custom battery pack designs to ensure safety and performance even under extreme operating conditions, preventing thermal issues from cascading into dangerous failure modes.
BMS Requirements for High-Drain Safety and Performance
Battery Management Systems (BMS) play a crucial role in high-drain applications by monitoring and controlling critical parameters including current, voltage, and temperature. High-drain applications require specialized BMS designs capable of handling substantial current flows without introducing excessive resistance that would impair performance. These systems must provide robust protection while minimizing impact on power delivery.
Current monitoring and limitation functions prevent overcurrent conditions that could damage cells or create safety hazards. Advanced BMS designs incorporate fast-acting protection circuits capable of responding within milliseconds to dangerous current spikes. The BMS must accurately measure pack and individual cell voltages to prevent over-discharge conditions that could permanently damage high-drain cells operating near their maximum capabilities.
Temperature monitoring becomes particularly important in high-drain applications due to significant heat generation under load. Modern BMS designs incorporate multiple temperature sensors distributed throughout the pack to detect local heating issues before they escalate into dangerous conditions. VADE Battery’s comprehensive approach to lithium-ion battery pack components and BMS design ensures optimal protection while maintaining maximum performance in high-drain applications.
Case Studies of Successful High-Drain Custom Packs
Electric bicycles represent a common high-drain application requiring carefully designed battery packs. A successful e-bike battery pack design typically incorporates high-drain 18650 cells configured to deliver 30-50A continuous current while maintaining voltage stability under variable load conditions. VADE Battery has developed specialized lithium battery solutions for e-bikes that balance power delivery with weight considerations and safety requirements.
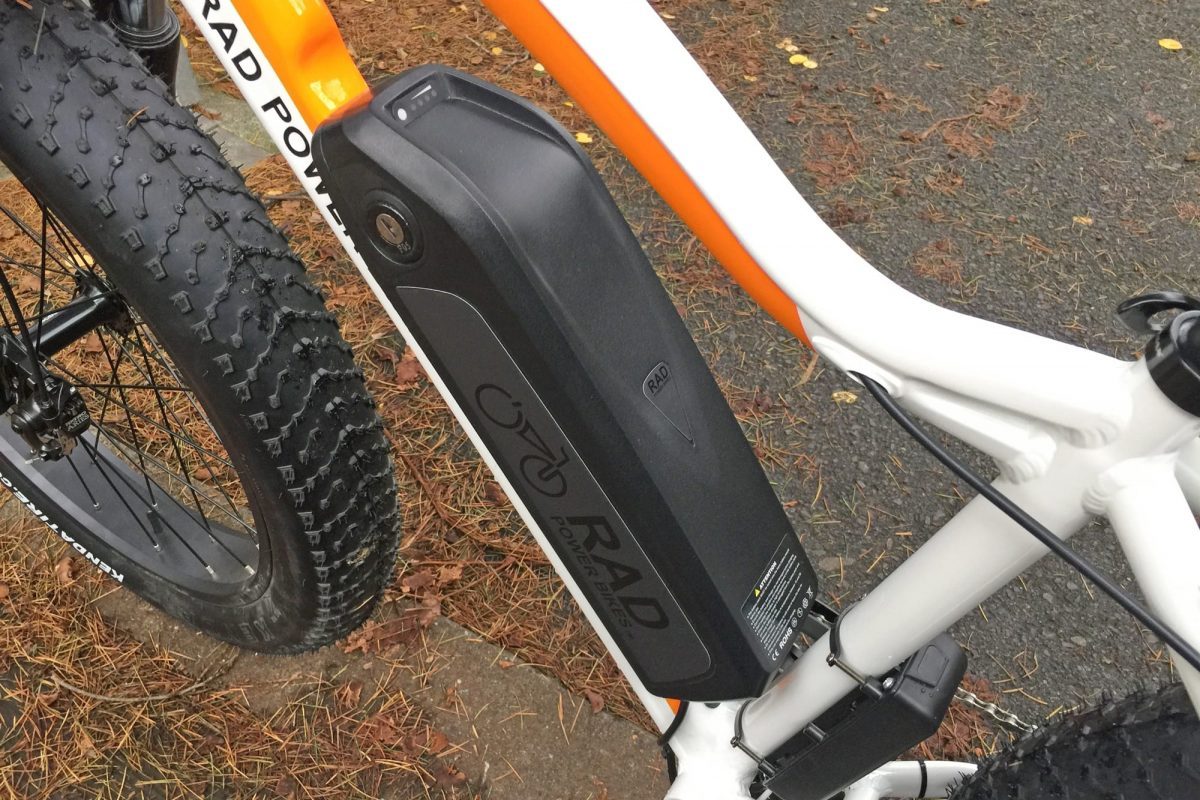
Power tool batteries represent another challenging high-drain application. Professional-grade cordless tools require packs capable of delivering 20-30A continuously while withstanding frequent high-current surge demands. Successful designs incorporate sophisticated thermal management, robust interconnections between cells, and specialized BMS solutions that protect cells while permitting the high current flow necessary for optimal tool performance.
Aviation and drone applications present unique high-drain challenges combining weight constraints with high reliability requirements. Successful drone battery designs optimize the energy density of batteries while ensuring sufficient discharge capability to handle power spikes during maneuvers. The reliability and performance of these packs directly impact flight time and operational capabilities in these demanding applications.
Testing and Validating High-Drain Battery Performance
Comprehensive testing protocols ensure high-drain batteries meet performance and safety requirements before deployment in critical applications. Standardized testing methodologies enable meaningful comparison between different battery options while identifying potential issues before they impact real-world operation. Understanding these testing approaches helps in selecting properly validated batteries for high-drain applications.
Industry-Standard Testing Protocols
The high-rate discharge performance test represents a fundamental evaluation method for high-drain batteries. This standardized protocol measures capacity when discharged at the maximum rate permitted by the manufacturer, typically conducted at 20°C ± 5°C. The test reveals actual energy delivery capability under high-current conditions, often showing significant differences from rated capacity figures based on standard discharge rates.
External short circuit testing evaluates battery safety under fault conditions by connecting terminals through a low-resistance pathway. This test verifies that protective mechanisms prevent dangerous thermal events when batteries encounter short circuit conditions. For high-drain applications where short circuits might involve substantial energy, this testing proves particularly important in validating safety systems.
Cycle life testing assesses battery durability by subjecting cells to repeated charge-discharge cycles at specified current levels. This evaluates capacity degradation over time, requiring batteries to maintain a specified minimum capacity after completing the defined number of cycles. High-drain applications typically accelerate degradation due to higher current stress, making cycle life testing especially relevant for evaluating long-term reliability.
Key Performance Indicators to Measure
Battery capacity represents a fundamental performance indicator, measured in ampere-hours (Ah) or milliampere-hours (mAh). For high-drain applications, capacity should be measured at relevant discharge rates rather than standard rates, as high-current operation typically reduces deliverable capacity compared to manufacturer ratings based on lower discharge rates.
Internal resistance provides critical insight into high-drain performance capability, with lower values enabling higher current delivery with less voltage sag and heat generation. Advanced testing equipment measures AC impedance across multiple frequencies to characterize internal resistance under conditions resembling actual usage scenarios. This testing helps identify cells optimized for high-drain applications.
Discharge platform time measures voltage stability under load, a critical factor in high-drain applications requiring consistent power delivery. Premium high-drain cells maintain stable voltage for most of their discharge cycle, while lower-quality options exhibit rapid voltage decline under load. This performance characteristic directly impacts usable capacity and runtime in high-drain devices.
Self-discharge rate indicates a battery’s ability to maintain charge during storage periods, with lower rates preferred for applications with intermittent usage patterns. This characteristic becomes particularly relevant for emergency equipment and seasonal devices where batteries must remain ready for high-drain operation even after extended storage periods.
Common Failure Points and Prevention Strategies
Thermal management failures represent a primary concern in high-drain applications. Inadequate heat dissipation during high-current operation can trigger thermal runaway, potentially resulting in catastrophic failure. Prevention strategies include proper cell spacing, thermal insulation between cells, and potentially active cooling for extreme high-drain scenarios. Regular thermal monitoring during operation helps identify potential issues before they escalate.
Connection resistance between cells often creates vulnerability in high-drain packs. Poor connections introduce additional resistance that generates heat and reduces efficiency during high-current operation. Implementing robust welded connections rather than mechanical contacts helps minimize this issue. Regular inspection and maintenance of connection points ensures continued performance in high-drain applications.
Battery Management System (BMS) failures can compromise both performance and safety in high-drain applications. Undersized components may fail under sustained high-current operation, while software issues might trigger inappropriate protection responses. Implementing redundant protection mechanisms and thorough testing under worst-case load scenarios helps identify and address potential BMS vulnerabilities before deployment.
Longevity Expectations in High-Demand Applications
Cycle life in high-drain applications typically ranges from 300-500 cycles at 80% depth of discharge, though premium cells may exceed 1000 cycles under optimal conditions. Operating temperature significantly impacts longevity, with each 10°C increase above room temperature potentially reducing cycle life by 50%. Maintaining temperatures between 20-30°C maximizes longevity even in demanding high-drain applications.
Calendar aging affects all lithium batteries regardless of usage, with high-drain cells typically losing 3-5% capacity annually even when not cycled. This degradation accelerates at elevated temperatures or when stored at high state-of-charge levels. Proper storage protocols maintaining moderate charge levels (30-50%) and cool temperatures significantly extend calendar life for high-drain batteries.
Usage patterns dramatically impact longevity, with frequent deep discharges accelerating degradation compared to partial discharge cycles. Implementing usage protocols that avoid complete depletion while providing occasional full cycles for calibration helps maximize service life. VADE Battery offers comprehensive guidance on how to store lithium batteries safely to extend their service life while maintaining performance and safety.
Conclusion: Implementing Best Practices for High-Drain 18650 Battery Selection and Implementation
The technical complexities of high-drain 18650 cells demand a methodical approach to selection and implementation. By prioritizing the critical parameters identified in this guide—internal resistance below 20mΩ, stable discharge voltage curves, appropriate thermal management systems, and application-specific capacity-to-power ratios—engineers and system designers can achieve optimal performance even under extreme discharge conditions of 20-35A. Laboratory testing under actual load conditions remains essential, as datasheet specifications often fail to accurately predict real-world performance in high-drain scenarios. For mission-critical applications, implementing comprehensive battery management systems with temperature monitoring, balanced cell configurations, and appropriate protection circuits provides the foundation for both performance and safety. As lithium battery technology continues to evolve, staying informed about emerging cell chemistries and construction techniques will ensure your high-drain applications maintain their competitive edge in an increasingly power-dependent world.