The global lithium battery market is projected to grow at a 14.6% CAGR through 2030, driven by rising demand in electric vehicles, renewable energy storage, and portable electronics. However, selecting the right lithium battery pack manufacturer can make or break your product’s performance, safety, and profitability. At Vade Battery, we specialize in crafting custom rechargeable solutions—including 18650 cells, Li-ion packs, Lithium polymer batteries, and LiFePO4 systems—for industries requiring precision, durability, and innovation.
This guide breaks down the critical factors to consider when evaluating lithium battery suppliers, with actionable insights to help you identify partners that align with your technical, operational, and financial goals.
What Are Your Core Battery Requirements?
Before approaching manufacturers, define your project’s non-negotiable parameters. Lithium battery packs are not one-size-fits-all solutions—their performance hinges on how well their design matches your application’s demands.
Performance Specifications
Start by outlining voltage, capacity (Ah), discharge rate (C-rate), and cycle life. For example, industrial drones require lightweight high-C-rate batteries (like our 24V Lithium Polymer Packs) capable of rapid energy bursts, while solar storage systems prioritize long cycle life (10,000+ cycles) found in LiFePO4 configurations.
Physical & Environmental Needs
Size, weight, and environmental resilience directly impact integration. Medical devices often need ultra-thin Lithium polymer batteries (as slim as 2mm), while outdoor equipment relies on ultra-low-temperature Li-ion cells (functional at -40°C) from our specialized range.
Certifications & Compliance
Safety is non-negotiable. Ensure your manufacturer adheres to:
- UL 1642 (cell safety)
- UN 38.3 (transportation testing)
- IEC 62133 (portable battery compliance)
- RoHS/REACH (hazardous substance restrictions)
At Vade Battery, all packs undergo 12-stage quality checks, including thermal shock testing, crush resistance validation, and overcharge protection audits.
What Manufacturing Capabilities Matter Most?
A supplier’s technical infrastructure determines their ability to deliver consistent quality at scale.
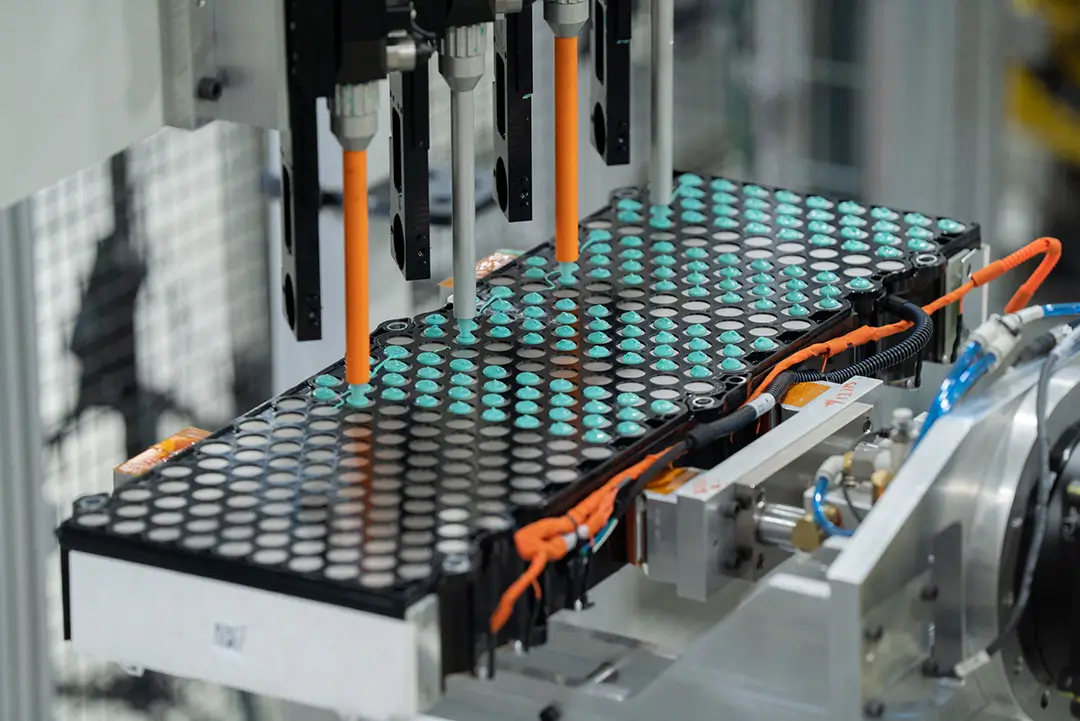
Cell Chemistry Expertise
Not all lithium chemistries suit every application. For instance:
- NMC (LiNiMnCoO₂): Balances energy density and cost (ideal for EVs).
- LiFePO4: Offers unmatched thermal stability (perfect for solar storage).
- LCO (LiCoO₂): Provides high energy density for consumer electronics.
Vade Battery’s engineers excel in chemistry customization, tweaking electrode compositions and electrolytes to optimize performance metrics like energy density or charge speed.
Production Scale & Flexibility
Verify if the manufacturer can handle both prototyping and mass production. For example, our 18650 battery line supports small-batch R&D runs (50–100 units) and high-volume orders (50,000+ monthly).
Automation & Precision
Advanced facilities use laser welding, automated stacking, and AI-driven inspection systems to minimize defects. Vade Battery’s ISO 9001-certified factories employ robotic assembly lines with ≤0.02% defect rates—critical for aerospace and automotive clients.
Why Does Industry Experience Matter?
A manufacturer’s track record reveals their ability to solve real-world challenges.
Proven Success in Your Sector
Suppliers familiar with your industry’s standards can anticipate pitfalls. For example:
- E-bike batteries require IP67 waterproofing and vibration resistance.
- Industrial IoT sensors demand miniaturized packs with 10+ year lifespans.
Vade Battery has delivered 36V and 48V packs (view 48V options) for e-mobility startups, achieving 98% capacity retention after 1,200 cycles.
R&D Investment
Leading manufacturers allocate ≥8% of revenue to R&D. Our team’s breakthroughs include:
- Silicon-anode cells boosting energy density by 20%.
- Solid-state prototypes with 500 Wh/kg capacity.
Case Studies & References
Ask for verifiable data:
- Cycle life test reports (e.g., 80% capacity after 2,000 cycles).
- Field failure rates (Vade Battery maintains <0.1% annual returns).
How to Evaluate Supplier Responsiveness and Support
A manufacturer’s ability to collaborate dynamically during development and production is as critical as their technical specs. Delays in prototyping or poor communication can derail product launches.
Prototyping Speed and Customization
Top-tier suppliers like Vade Battery offer 10-day prototyping cycles for standard configurations, leveraging modular designs from our lithium-ion battery pack catalog. For complex projects—such as 72V battery systems for electric motorcycles—we deploy cross-functional teams to refine:
- Mechanical integration (e.g., shock-resistant casings)
- BMS (Battery Management System) programming (voltage balancing, thermal cutoff)
- Connector customization (waterproof MC4, Anderson SB®)
Engineering Collaboration
Avoid manufacturers that treat your project as a “black box.” Vade Battery assigns dedicated engineers to:
- Simulate load profiles using your device’s current draw data.
- Optimize charge algorithms to extend cycle life.
- Conform to IP ratings (e.g., IP68 for submersible applications).
For a robotics startup, we redesigned a 51.8V LiFePO4 pack to withstand 15G vibration loads while reducing weight by 22%—achieved through proprietary cell stacking and aluminum-composite enclosures.
Post-Sale Support
Post-production issues like cell balancing failures or capacity fade require rapid resolution. Look for:
- 24/7 technical hotlines (Vade Battery’s team resolves 90% of issues within 4 hours).
- Warranty terms (We offer up to 5 years for industrial LiFePO4 systems).
- Field failure analysis (Root cause diagnostics with 72-hour reporting).
Why Facility Audits Are Non-Negotiable
Third-party certifications provide baseline assurance, but firsthand audits reveal operational realities.
Critical Audit Checklists
During Vade Battery’s facility tours, clients inspect:
Area | Key Metrics |
---|---|
Electrode Production | Coating uniformity (±2μm tolerance) |
Cell Assembly | Moisture levels (<50 ppm in dry rooms) |
Formation & Aging | Cycle testing (100% of cells graded) |
Pack Integration | Torque consistency in screw fastening (±0.1 Nm) |
Quality Lab | CT scan results for internal voids |
Case Study: Aerospace Audit Insights
A drone manufacturer rejected three suppliers before selecting Vade Battery. Our audit revealed:
- Laser-welded nickel strips (vs. ultrasonic welding) preventing micro-cracks.
- In-line X-ray inspection detecting 99.98% of electrode misalignments.
- Automated electrolyte filling with ±0.5% precision.
Which Certifications Guarantee Safety and Compliance?
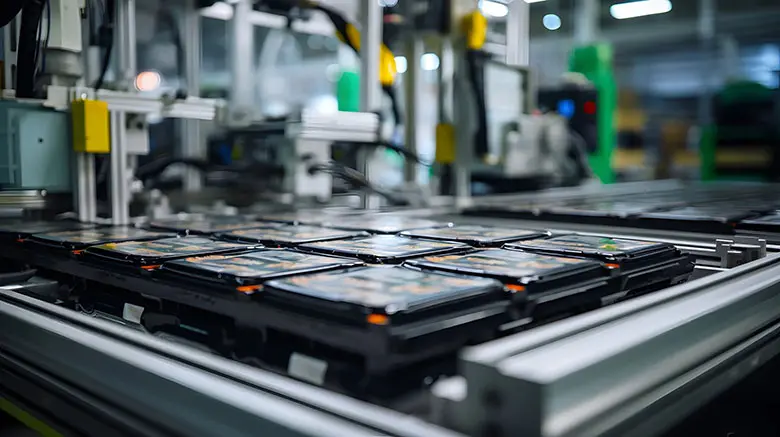
Regulatory hurdles can block international shipments or trigger recalls. Prioritize manufacturers with these certifications:
Mandatory Certifications
- UN 38.3: Passed crush, altitude, and thermal tests (mandatory for air freight).
- UL 2054: Certifies pack-level safety (overcharge, short circuit).
- IATF 16949: Automotive-grade process controls (PPAP documentation).
Niche Certifications
- CE Mark: For EU market access (EMC Directive compliance).
- KC Certification: South Korea’s safety standard.
- GB 31241: China’s strict cell safety regulation.
Vade Battery’s 7.4V LiPo batteries exceed IEC 62133 requirements, with self-extinguishing separators that halt thermal runaway at 150°C.
How to Assess Financial Stability and Pricing Models
A manufacturer’s fiscal health ensures long-term supply continuity.
Financial Red Flags
- Overdue Payables: >60 days overdue to raw material suppliers.
- Debt-to-Equity Ratio: >2.0 indicates overleveraging.
- Inventory Turnover: <4x yearly suggests poor demand forecasting.
Vade Battery maintains a 0.8 debt-to-equity ratio and 6x annual inventory turnover—key reasons we’ve supplied 12V lithium packs to the marine industry for 8+ years without disruption.
Cost Drivers in Lithium Battery Pricing
Factor | Price Impact |
---|---|
Cell Chemistry | NMC costs 15% less than LTO |
Cycle Life | 2,000-cycle packs cost 30% more |
Custom Tooling | $8,000–$20,000 one-time fee |
Order Volume | 50,000-unit orders save 18% |
We mitigate costs via semi-solid state electrodes (20% cheaper than traditional LiPo) and localized sourcing (80% of raw materials from ASEAN suppliers).
The Ideal Lithium Battery Partner Checklist
Summarize your findings using this actionable scorecard:
Technical Capabilities (40% Weight)
- Chemistry customization expertise
- Automation level (≥80% robotic assembly)
- Cycle life validation reports
Operational Excellence (30%)
- Prototyping lead time (<15 days)
- Defect rate (<0.05%)
- Audit transparency
Business Alignment (30%)
- Total cost of ownership (TCO)
- Payment term flexibility
- Scalability to 5x order volume
Vade Battery scores 93/100 across these parameters for clients in mission-critical industries like healthcare and defense.
Final Thoughts: Building a Future-Ready Supply Chain
Selecting a lithium battery manufacturer isn’t a transaction—it’s a strategic partnership. With 46.8V systems powering next-gen AGVs and ultra-low-temperature packs enabling Arctic research, Vade Battery combines cutting-edge R&D with scalable manufacturing.
Ready to Discuss Your Project?
- Request a Custom Battery Design
- Contact Our Engineering Team
- Email Directly: service@vadebattery.com
By prioritizing technical rigor, transparency, and shared innovation goals, you’ll secure a lithium battery partner capable of powering your vision—today and tomorrow.