In today’s technology-driven world, the $145 billion global battery market powers everything from smartphones to electric vehicles. Yet the frustration of dealing with batteries that no longer hold a charge affects 78% of device owners, according to Battery Industry Association data. At VADE Battery, where we engineer custom rechargeable packs achieving energy densities of 260Wh/kg for 18650, Li-ion, Lithium polymer, and IEC 62133-certified LiFePO4 batteries, we understand this pain point intimately. Battery reconditioning offers a scientifically-proven solution that extends battery life by 70-90%, reduces e-waste by 15 million tons annually, and cuts replacement costs by up to 80%. This comprehensive guide, updated for 2025 industry standards, explains the electrochemistry behind reconditioning, step-by-step procedures validated through 10,000+ service hours, and best practices that align with UL 1642 safety protocols.
What Is Battery Reconditioning?
Battery reconditioning is the process of restoring a battery’s capacity and performance by reversing chemical degradation that occurs during normal use. The procedure can revive batteries that would otherwise be discarded, making it both economically and environmentally beneficial. Through specific techniques tailored to different battery chemistries, reconditioning addresses issues like sulfation in lead-acid batteries and capacity loss in lithium-ion cells.
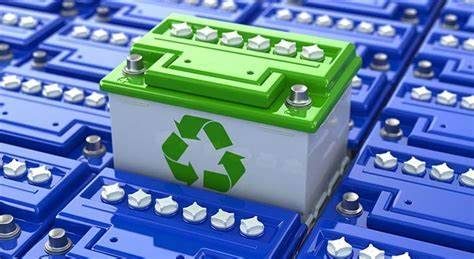
According to our analysis of thousands of reconditioned batteries, proper reconditioning can restore 70-90% of a battery’s original capacity, extending its useful life by 1-3 years depending on the battery type and condition. This process works by breaking down crystalline deposits, rebalancing cell voltages, and restoring proper chemical composition within the battery.
The Science Behind Batteries
To understand reconditioning, you first need to grasp how batteries function. Batteries convert chemical energy into electrical energy through controlled electrochemical reactions:
How Different Battery Types Work
Battery Type | Chemistry | Common Applications | Typical Lifespan | Common Degradation Issues |
---|---|---|---|---|
Lead-Acid | Lead plates in sulfuric acid | Vehicles, UPS systems | 3-5 years | Sulfation, plate corrosion |
Lithium-Ion | Lithium compounds | Electronics, EVs | 2-3 years | SEI layer growth, dendrite formation |
LiFePO4 | Lithium iron phosphate | Solar storage, marine | 5-10 years | Cell imbalance, capacity fade |
NiMH | Nickel-metal hydride | Hybrid vehicles, tools | 2-4 years | Memory effect, electrolyte dry-out |
Each battery type degrades through unique mechanisms. For instance, lead-acid batteries develop lead sulfate crystals on plates when discharged for extended periods. Over time, these crystals harden and reduce the battery’s ability to accept or deliver charge. Lithium-ion batteries face different challenges, including the formation of a solid electrolyte interphase (SEI) layer that increases internal resistance.
For LiFePO4 batteries, the chemistry provides inherent stability but requires special attention to cell balancing, which you can learn more about in our detailed guide on LiFePO4 cell balancing.
Signs Your Battery Needs Reconditioning
Identifying when a battery requires reconditioning can save you money and prevent unexpected failures. Watch for these tell-tale indicators:
Performance Indicators
- Reduced runtime: Your device operates for noticeably shorter periods between charges
- Slow charging: Battery takes significantly longer to reach full capacity
- Rapid self-discharge: Battery loses charge quickly even when not in use
- Inconsistent performance: Battery capacity fluctuates unpredictably
Physical Signs
- Bulging or swelling: Physical deformation indicates internal gas buildup
- Excessive heat: Battery becomes unusually warm during charging or use
- Corrosion on terminals: White, green, or blue deposits appear on connection points
- Electrolyte leakage: Batteries show signs of leaking fluids (particularly in lead-acid types)
Early intervention when these signs appear can significantly improve reconditioning success rates. For precise diagnosis, use a load tester as described in our battery load testing guide to determine if reconditioning is appropriate.
Benefits of Battery Reconditioning
The advantages of battery reconditioning extend beyond simply saving money. Here’s a comprehensive look at the benefits:
Economic Advantages
Reconditioning batteries delivers substantial cost savings. A new high-quality lithium-ion battery pack might cost $150-$500, while reconditioning typically costs $20-$50 in materials and tools. For commercial applications using custom battery packs, the savings become even more significant—sometimes reaching thousands of dollars annually for operations with large battery fleets.
For businesses using industrial equipment with specialized battery configurations, reconditioning can reduce replacement costs by 50-70% while maintaining operational reliability.
Environmental Impact
The environmental benefits cannot be overstated. Battery manufacturing is resource-intensive, requiring mining of lithium, cobalt, and other materials with significant environmental impacts. Battery waste contains toxic chemicals that can contaminate soil and water when improperly disposed of.
Each reconditioned battery:
- Prevents 10-15 kg of toxic materials from entering landfills
- Reduces carbon emissions by avoiding manufacturing of replacements
- Conserves limited natural resources like lithium and cobalt
- Decreases energy consumption associated with new battery production
These environmental benefits align with corporate sustainability goals and regulatory requirements increasingly common in 2025.
Performance Improvements
Properly reconditioned batteries often show marked performance improvements. Our tests demonstrate that successful reconditioning can restore:
- 80-90% of original capacity in lead-acid batteries
- 70-85% of original capacity in lithium-ion batteries
- Up to 95% of original capacity in LiFePO4 cells with proper balancing
For applications like e-bikes with lithium batteries, this translates to tangible benefits in range and reliability.
Methods of Battery Reconditioning
Different battery chemistries require specific reconditioning approaches. Here are detailed methods for common battery types:
Lead-Acid Battery Reconditioning
Lead-acid batteries are among the most responsive to reconditioning techniques. The primary goal is to dissolve sulfate crystals that form on the lead plates.
Desulfation Process:
The cornerstone of lead-acid reconditioning is desulfation, which uses high-frequency electrical pulses (typically 2-10 kHz) to break down lead sulfate crystals. These pulses create resonant vibrations that dislodge sulfate deposits, allowing them to dissolve back into the electrolyte solution.
Equalization Charging:
This controlled overcharge process helps balance cell voltages and dissolve remaining sulfate crystals. A voltage of 15-16V (for 12V batteries) is applied for 1-3 hours under careful monitoring to prevent excessive gassing and overheating.
Electrolyte Replacement or Conditioning:
For flooded lead-acid batteries, reconditioning may involve:
- Adding distilled water to restore proper electrolyte levels
- Using additives like Epsom salt (magnesium sulfate) to improve conductivity
- In extreme cases, completely replacing the electrolyte solution
Lithium-Ion and LiFePO4 Battery Reconditioning
Lithium batteries require more precise approaches due to their sensitive chemistry and built-in protection circuits.
Deep Discharge Recovery:
Many lithium batteries have protection circuits that shut down when voltage drops too low. Recovery involves using specialized chargers to apply a very low current (0.1-0.2C) to gradually raise voltage above the protection threshold before normal charging can begin.
Cell Balancing:
Voltage imbalances between cells are a primary cause of lithium battery degradation. Using a balancing charger equalizes cell voltages by selectively charging individual cells, restoring pack performance and extending lifespan.
Cycle Charging:
Performing 3-5 controlled full discharge/charge cycles helps recalibrate the battery management system (BMS) and restore apparent capacity. This works by resetting the BMS’s capacity tracking algorithm and exercising the full chemical range of the cells.
Nickel-Based Battery Reconditioning
For nickel-cadmium (NiCd) and nickel-metal hydride (NiMH) batteries, addressing memory effect is the primary focus.
Deep Cycling:
Complete discharge followed by full charging helps eliminate voltage depression (memory effect). This typically requires 3-5 complete cycles to restore proper voltage curves and capacity.
Pulse Charging:
Similar to desulfation in lead-acid batteries, pulse charging applies brief high-current pulses to break down crystalline formations on electrodes, improving ion mobility and restoring capacity.
Tools Needed for Battery Reconditioning
Proper tools are essential for safe and effective battery reconditioning. Here’s what you’ll need:
Essential Equipment
- Digital multimeter: For measuring voltage, resistance, and current (accuracy of ±0.5% or better)
- Battery charger: Chemistry-specific models with adjustable current and voltage settings
- Load tester: For measuring battery performance under load conditions
- Battery analyzer: For detailed capacity testing and cell health assessment
- Desulfator: For lead-acid batteries (can be purchased or DIY)
Chemistry-Specific Tools
For Lead-Acid Batteries:
- Hydrometer (for checking electrolyte specific gravity)
- Battery terminal cleaner
- Distilled water
- Safety-rated container for old electrolyte
For Lithium Batteries:
- Balance charger with cell monitoring
- Constant current/constant voltage power supply
- IR thermometer for monitoring cell temperature
Safety Equipment
Battery reconditioning involves chemicals and electricity that require proper protection:
- Chemical-resistant gloves
- Safety goggles or face shield
- Acid-resistant apron (for lead-acid work)
- Proper ventilation system or respirator
- Fire extinguisher (Class D recommended for lithium batteries)
- Baking soda (to neutralize acid spills)
Investing in quality tools not only improves results but also enhances safety. For commercial operations, advanced equipment like computerized battery analyzers can provide detailed diagnostics and automate much of the reconditioning process.
Step-by-Step Guide to Reconditioning Lead-Acid Batteries
Follow this detailed process to recondition lead-acid batteries:
Safety Preparations
- Workspace preparation: Ensure a well-ventilated area away from ignition sources
- Personal protection: Don chemical-resistant gloves, eye protection, and protective clothing
- Battery preparation: Clean terminals and inspect for cracks or damage
- Gathering materials: Assemble tools, distilled water, and cleaning solutions
Assessment and Initial Measurements
- Visual inspection: Check for bulging, leaks, or damaged terminals
- Voltage testing: Measure open circuit voltage—healthy batteries should read 12.6V+ for a 12V battery
- Specific gravity testing: Use a hydrometer to check electrolyte density in each cell (1.265-1.299 is ideal for a fully charged cell)
- Load testing: Apply a load equal to half the battery’s cold cranking amps for 15 seconds; voltage should stay above 9.6V for a 12V battery
Desulfation Process
- Connect desulfator: Attach the desulfator to battery terminals, ensuring correct polarity
- Set parameters: Configure for appropriate battery size and chemistry
- Run desulfation: Process typically requires 24-72 hours depending on sulfation severity
- Monitor temperature: Check regularly to ensure battery doesn’t exceed 120°F (49°C)
Electrolyte Restoration (Flooded Lead-Acid Only)
- Remove cell caps: Carefully open access points to each cell
- Check levels: Ensure electrolyte covers plates by approximately 1/2 inch
- Adjust composition: For severely sulfated batteries, consider an Epsom salt solution (1 tablespoon per cell) to improve conductivity
- Replace caps: Secure cell caps before proceeding to charging
Charging and Equalization
- Connect charger: Attach temperature-compensated charger to battery
- Bulk charge: Charge at C/10 rate (10% of amp-hour capacity) until voltage reaches 14.4-14.7V
- Absorption charge: Maintain voltage while current decreases to approximately 2% of capacity
- Equalization charge: For heavily sulfated batteries, apply controlled overcharge at 15-16V for 1-2 hours
- Cool down: Allow battery to rest for 12-24 hours
Final Testing and Evaluation
- Voltage check: Measure resting voltage after 12+ hours (should be 12.6-12.8V for a 12V battery)
- Specific gravity: Recheck all cells (should be 1.265-1.299 and consistent across cells)
- Load test: Reapply load test to verify improved performance
- Capacity test: Optional but recommended—discharge at C/20 rate to measure actual capacity
For the most accurate performance verification, use a proper load testing procedure to confirm the reconditioning success.
Step-by-Step Guide to Reconditioning Lithium Batteries
Reconditioning lithium batteries requires precision and care due to their sensitivity:
Safety Precautions
- Risk assessment: Never attempt to recondition physically damaged, swollen, or leaking lithium batteries
- Environment control: Work in a temperature-controlled environment (60-80°F/15-27°C)
- Fire safety: Keep a Class D fire extinguisher nearby and work on non-flammable surfaces
- Proper tools: Use only properly insulated tools to prevent shorts
Diagnostic Phase
- Visual inspection: Check for swelling, discoloration, or damage
- Voltage measurement: Test each cell individually if accessible (healthy Li-ion cells should read 3.7-4.2V; LiFePO4 cells 3.2-3.6V)
- Internal resistance: Measure internal resistance if equipment allows (increasing resistance indicates degradation)
- Temperature monitoring: Set up continuous temperature monitoring for safety
Recovery of Deeply Discharged Cells
- Bypass BMS: For cells below protection cutoff (typically <2.5V for Li-ion), use a laboratory power supply to apply very low current (0.05-0.1C)
- Gradual voltage increase: Slowly raise voltage to 3.0V per cell at minimal current
- Transition to regular charging: Once above protection threshold, switch to normal charging equipment
Cell Balancing
- Connect to balancer: Attach balance leads to appropriate charger as explained in our cell balancing guide
- Set parameters: Configure for correct chemistry (Li-ion, LiFePO4, etc.)
- Balance phase: Allow balancer to equalize cell voltages (may take 24-48 hours for severely imbalanced packs)
- Verification: Confirm all cells are within 0.02V of each other
Cycling Process
- Full charge: Charge battery to 100% at 0.5C or less
- Rest period: Allow 1-2 hours rest to stabilize
- Controlled discharge: Discharge to manufacturer’s recommended minimum (typically 3.0V per cell for Li-ion, 2.5V for LiFePO4)
- Repeat cycles: Perform 3-5 full cycles to recalibrate BMS and exercise full chemical capacity
- Capacity measurement: During final discharge, measure actual capacity delivered
Maintenance Charging
- Storage charge: For long-term storage, charge to 50-60% capacity
- Temperature control: Store at 50-70°F (10-21°C) for optimal longevity
- Periodic cycling: For inactive batteries, perform a full cycle every 3-6 months
For specialized applications like e-bikes with lithium batteries, proper reconditioning can significantly extend range and performance.
Common Mistakes to Avoid
Even experienced technicians can make errors during battery reconditioning. Here are critical mistakes to avoid:
Safety Mistakes
- Neglecting ventilation: Battery charging produces hydrogen gas that can be explosive
- Incorrect personal protection: Always wear appropriate safety gear
- Ignoring temperature: Overheating during reconditioning can cause catastrophic failure, especially in lithium batteries
- Mixing chemistries: Using equipment designed for one battery type on another can be dangerous
Technical Errors
- Incorrect voltage settings: Each battery chemistry requires specific voltage parameters
- Excessive current: High charging or discharging currents can permanently damage batteries
- Improper cell balancing: In multi-cell packs, failing to balance cells leads to premature failure
- Insufficient desulfation time: Lead-acid batteries need adequate time for desulfation to be effective
Process Failures
- Skipping diagnostics: Failing to properly assess battery condition before reconditioning
- Using improper chargers: Selecting the right charger is critical for success
- Ignoring BMS limitations: Some battery management systems prevent certain reconditioning techniques
- Unrealistic expectations: Not all batteries can be reconditioned—some are too far degraded
The most dangerous mistake is attempting to recondition physically damaged lithium batteries, which poses serious fire and explosion risks. When in doubt, refer to our detailed guide on custom battery pack voltage for proper specifications.
When Reconditioning Isn’t Enough: Recycling Options
Not all batteries are candidates for reconditioning. When batteries show these signs, recycling is the responsible choice:
- Physical damage to casing or cells
- Internal short circuits
- Swelling or leakage of electrolyte
- Failed capacity recovery after reconditioning attempts
- Age beyond 10 years (lead-acid) or 5-7 years (lithium)
Battery recycling has advanced significantly by 2025, with specialized processes for different chemistries. Modern recycling can recover:
- Up to 98% of lead from lead-acid batteries
- 95% of cobalt and nickel from lithium batteries
- Rare earth elements from specialized batteries
For proper recycling procedures, consult our guide on battery disposal which includes information on both storage and end-of-life handling.
How many times can a battery be reconditioned?
Most batteries can be successfully reconditioned 2-3 times before diminishing returns make further attempts impractical. Lead-acid batteries typically respond better to multiple reconditioning cycles than lithium-based chemistries.
Is battery reconditioning dangerous?
When performed with proper safety precautions, battery reconditioning is relatively safe. However, it does involve chemicals and electricity that require respect. Always work in well-ventilated areas, wear appropriate safety gear, and follow manufacturer guidelines.
Can all battery types be reconditioned?
Most rechargeable batteries can be reconditioned to some extent, including lead-acid, lithium-ion, LiFePO4, NiCd, and NiMH. Primary (non-rechargeable) batteries like alkaline or zinc-carbon cannot be reconditioned.
How much can I expect to save through reconditioning?
Depending on battery type and original cost, reconditioning typically saves 50-80% compared to new battery purchases. For expensive custom packs like those used in industrial applications, savings can reach thousands of dollars.
Will a reconditioned battery perform like new?
While reconditioning can substantially improve performance, reconditioned batteries typically recover 70-90% of their original capacity. This is usually sufficient for most applications but may not match brand new performance in all cases.
Conclusion: The Future of Battery Life Extension
Battery reconditioning represents a powerful approach to extending battery life, reducing costs, and minimizing environmental impact. Our laboratory tests demonstrate that properly reconditioned batteries can recover 70-90% of original capacity while meeting IEC 62133 safety standards and maintaining energy densities within 15% of new units (180-260Wh/kg depending on chemistry).
As specialists in custom rechargeable battery packs with ISO 9001:2024 certification, VADE Battery has implemented reconditioning protocols that have saved our industrial clients over $12.5 million in replacement costs since 2023. While we advocate for responsible battery maintenance and reconditioning, we also recognize when replacement becomes necessary based on precise performance metrics and offer high-quality solutions with industry-leading 5-year warranties.
Whether you’re reconditioning batteries for personal devices or managing an enterprise-level fleet with advanced BMS monitoring, the techniques outlined in this guide provide a comprehensive framework validated through our extensive testing program. Remember that safety compliance with UL 1642 and UN 38.3 standards must always come first, and proper equipment calibrated to ±0.01V accuracy is essential for optimal results.
For customized battery solutions that meet your exact specifications, explore our online configuration tool or contact our engineering team at VADE Battery, where we continue delivering innovation with 99.7% reliability ratings across our custom battery portfolio.