-
29 W. Pawnee, Bloomfield, NJ 07003
Battery Posts and Terminals Guide: Types, Materials & Maintenance (2025)
Battery posts and terminals are fundamental components in every electrical system, creating the critical connection points that determine power delivery efficiency and system reliability. Whether you’re troubleshooting starting issues, planning maintenance, or designing custom power solutions, understanding these essential elements will help you maximize performance and extend battery life.
What is a Battery Terminal?
Battery terminals are the electrical contacts used to connect a load or charger to a single cell or multiple-cell battery. These critical connection points ensure stable and secure electrical pathways, allowing efficient power delivery for your devices and vehicles. Every battery features two primary terminals: a positive terminal (typically marked with red color or a ‘+’ symbol) and a negative terminal (usually identified by black color or a ‘-‘ symbol).
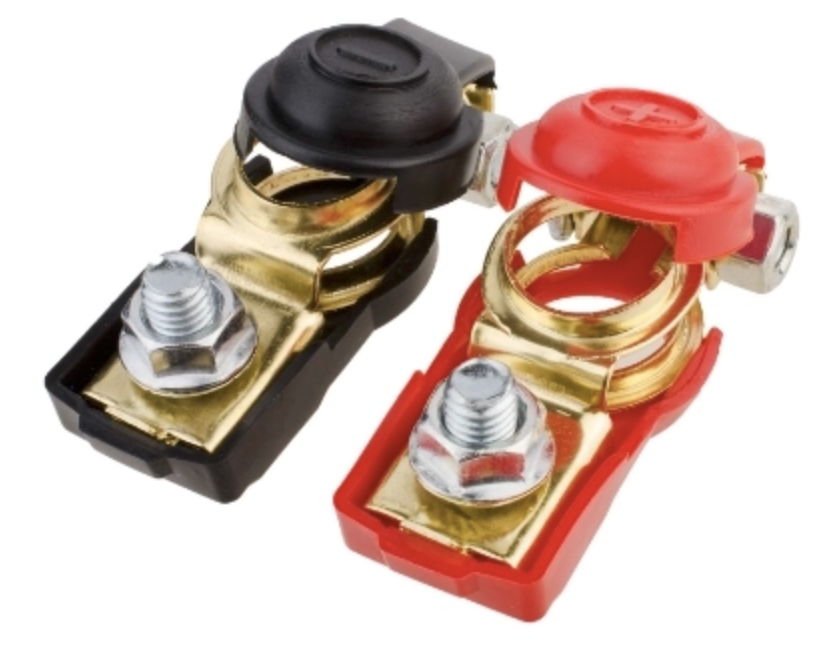
The quality of these terminals directly impacts your entire electrical system’s performance. Poor-quality or corroded connections significantly increase electrical resistance, reducing voltage delivery and generating excess heat that can damage components.
Types of Battery Terminals
Battery terminals come in numerous designs, each engineered for specific applications and environments. Understanding these differences helps you select the optimal terminal type for your power requirements.
Standard Automotive Battery Terminals
SAE Post Terminals
SAE Post terminals represent the North American standard for automotive batteries. They consist of two lead posts shaped like truncated cones, positioned on the battery’s top, with slightly different diameters (positive being larger than negative) to prevent reverse polarity connections. This design ensures you cannot accidentally connect the battery cables incorrectly.
JIS Post Terminals
Japanese Industrial Standard (JIS) terminals appear similar to SAE posts but have smaller dimensions. The JIS design is common in Japanese vehicles and requires properly sized terminals for secure connections. While they look similar to SAE posts, mixing SAE and JIS components creates loose connections that can cause voltage drops and potential fire hazards.
Side-Post Terminals
General Motors and other manufacturers often utilize side-post battery terminals, which consist of two recessed female 3/8″ threads (SAE 3/8-16) into which bolts or various battery terminal adapters are attached. These terminals are positioned on the battery’s side rather than the top, providing excellent protection against corrosion in certain installations.
L Terminals
L-shaped terminals feature a post with a bolt hole through the vertical side. These terminals are common in European vehicles, motorcycles, lawn equipment, snowmobiles, and other light-duty applications where space might be limited. Their design provides a secure connection in smaller battery compartments.
Stud Terminals
Stud terminals feature threaded rods extending from the battery. Electrical connections are made by screwing the battery connector directly to this post. These terminals are common in medium and heavy-duty trucks (Class 8), providing exceptional stability for applications requiring sustained high power output.
Specialized Battery Terminals
Marine Battery Terminals
Marine batteries typically include two posts: a 3/8″-16 threaded post for the positive terminal and a 5/16″-18 threaded post for the negative terminal. These specialized terminals are designed to withstand harsh marine environments where corrosion poses a significant threat, incorporating corrosion-resistant coatings and often featuring both SAE and threaded post designs.
F1 and F2 Terminals (Faston Tabs)
Commonly found on Sealed Lead Acid (SLA) batteries used in medical mobility wheelchairs, UPS systems, and small electric vehicles, these flat blade terminals differ slightly in size:
- F1 Terminals (Tab 187): Measure 0.187″ wide (3/16″ or 4.75mm)
- F2 Terminals (Tab 250): Measure 0.25″ wide (1/4″ or 6.35mm)
While the 1/16″ difference might seem minimal, using the correct size ensures proper electrical contact and prevents connection issues.
Faston Polarized Terminals
These terminals combine F1 and F2 designs, with the wider F2 forming the positive terminal and the narrower F1 forming the negative terminal. This physical difference prevents reverse polarity connections in sensitive electronic equipment.
Spring Posts
Spring terminals, found primarily in lanterns and flashlights, feature a collapsible spring design that creates a reliable connection with the device. This design accommodates slight variations in battery compartment dimensions while maintaining consistent electrical contact.
Terminal Type | Width | Common Applications | Key Features |
---|---|---|---|
F1 (Tab 187) | 0.187″ (4.75mm) | UPS systems, medical equipment | Narrower connection |
F2 (Tab 250) | 0.25″ (6.35mm) | Electric scooters, power backup | Wider, more robust connection |
SAE Post | Varies (positive larger) | North American vehicles | Conical design, different diameters |
JIS Post | Smaller than SAE | Japanese vehicles | Smaller than SAE but similar design |
L Terminal | Varies | European vehicles, small equipment | L-shaped with bolt hole |
Stud Terminal | Varies | Heavy-duty trucks | Threaded rod design |
What is a Battery Post?
A battery post is the protruding metal component that extends from the battery casing to provide a connection point for terminals. These posts serve as the actual contact surfaces where electrical current transfers between the battery and your connected device or vehicle. The design, composition, and configuration of these posts significantly impact the battery’s performance and compatibility with various electrical systems.
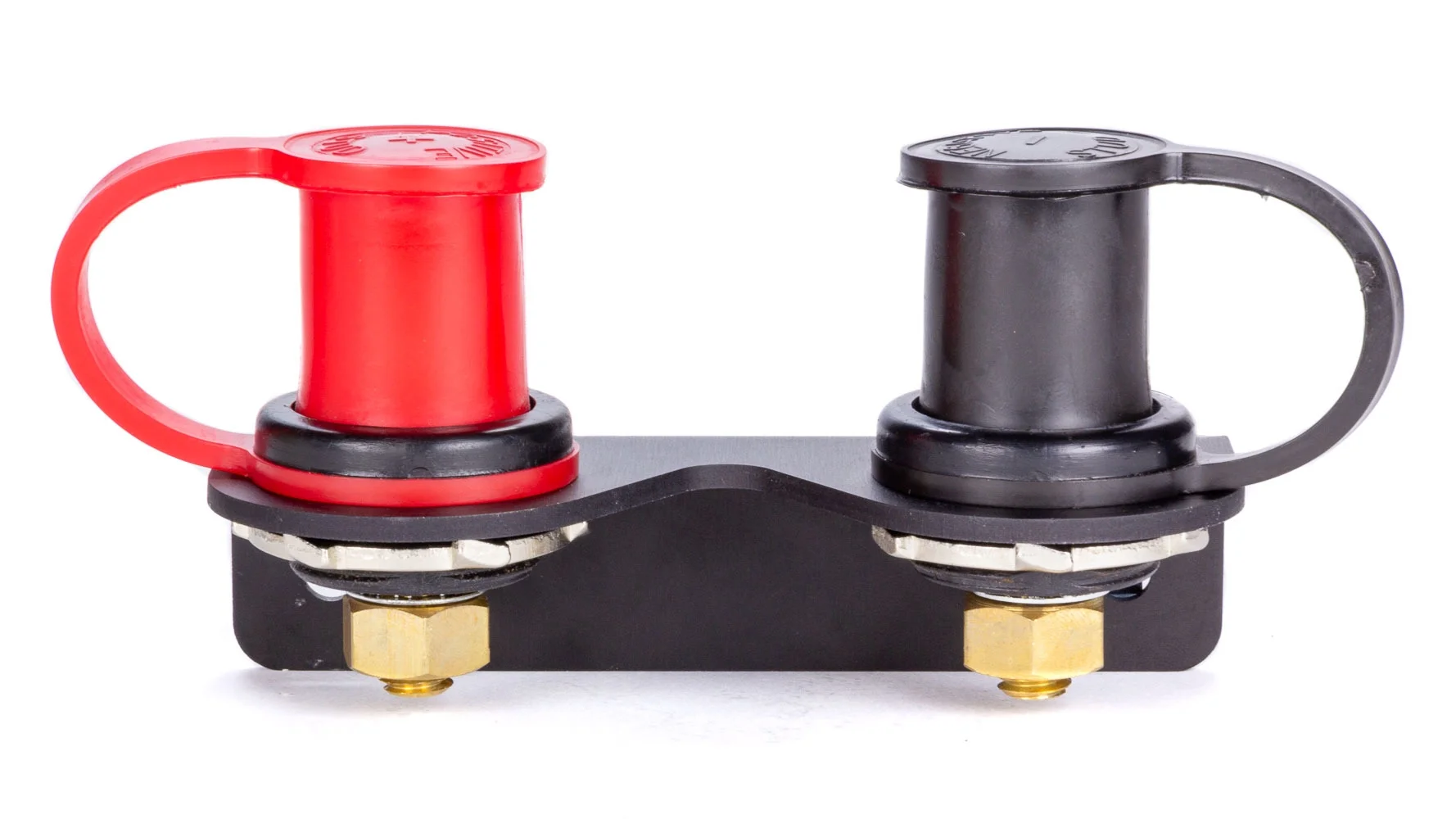
The taper of battery posts is particularly important, allowing for a wide variety of cable clamp sizes to create secure connections. This conical design creates maximum surface contact when terminals are attached, ensuring efficient electrical transfer with minimal resistance.
Types of Battery Posts
Battery posts come in several standardized designs that match specific terminal types and applications. Each post type offers unique advantages for particular uses:
SAE Posts
SAE posts represent the North American standard for automotive batteries, featuring different diameters for positive and negative connections to prevent incorrect installations. The positive terminal is slightly larger than the negative to reduce the chance of accidentally switching the cables. These widely-compatible posts work seamlessly with standard terminal clamps and connectors.
JIS Posts
JIS (Japanese Industrial Standard) posts appear similar to SAE posts but have smaller dimensions. Commonly found in Japanese vehicles, these posts require properly sized JIS terminals for secure connections. Attempting to use SAE terminals on JIS posts creates loose, inefficient connections.
Threaded Posts
Threaded posts incorporate screw threads for nut-and-bolt connections, providing superior stability in heavy-duty and marine applications. This design prevents accidental disconnection in high-vibration environments and offers excellent corrosion resistance when properly maintained.
Tapered Posts
Tapered posts feature a conical design that allows terminals to slide onto the post and tighten for a secure fit. This configuration ensures maximum surface contact for efficient electrical transfer, but requires regular maintenance to prevent corrosion in the contact area.
Battery Terminal Materials
The material composition of your battery terminals directly affects performance, longevity, and corrosion resistance. Several materials are commonly used, each with distinct advantages:
Lead Terminals
Traditional lead terminals offer affordability but corrode faster and provide less conductivity than alternatives. These terminals are still common in standard automotive applications but require more frequent maintenance to prevent performance degradation.
Copper Terminals
Copper terminals deliver superior conductivity (approximately 25% better than lead) and excellent corrosion resistance, making them ideal for marine applications and high-performance systems. For applications with high power demands like audio systems or commercial equipment, copper terminals provide meaningful performance benefits despite their higher initial cost.
Brass Terminals
Brass terminals provide a balanced middle ground with good conductivity and reasonable corrosion resistance at a moderate price point. They’re often found in applications where enhanced performance is desired without the premium cost of pure copper.
Zinc Terminals
Zinc battery terminals are an environmentally friendly alternative to lead, designed to comply with environmental directives such as Proposition 65 and RoHS. These terminals offer increased electrical conductivity, improved corrosion resistance, and reduced environmental impact compared to traditional lead alloy terminals.
Battery Terminal Corrosion: Causes, Prevention, and Solutions
Battery terminal corrosion appears as a white-blue or greenish powder that accumulates around battery posts, creating resistance that impedes electrical flow. This common issue can lead to starting problems, electrical system malfunctions, and shortened battery life.
What Causes Battery Terminal Corrosion?
Several factors contribute to terminal corrosion:
- Hydrogen Gas Leakage: Batteries release hydrogen gas during charging, which combines with atmospheric elements to create corrosive compounds. The side where corrosion forms can indicate specific issues: corrosion on the negative terminal suggests undercharging, while corrosion on the positive terminal indicates overcharging.
- Electrolyte Leakage: Overfilling batteries can cause electrolyte to leak onto terminals, accelerating corrosion. This is particularly common in batteries with removable caps for water addition.
- Charging Issues: If your alternator slightly overcharges your battery (above 14.5 volts), it can accelerate terminal corrosion. Similarly, frequent hard charging with external battery chargers can contribute to this problem.
- Environmental Factors: Moisture, road salt, and atmospheric pollutants create an ideal environment for accelerated corrosion, especially in coastal or industrial areas.
How to Clean Battery Terminal Corrosion
Cleaning corrosion requires specific materials and careful technique:
Materials needed:
- Baking soda
- Water
- Wire brush or battery terminal cleaner
- Protective gloves and eye protection
- Clean cloth or paper towels
Step-by-step cleaning process:
- Disconnect the battery by removing the negative (black) cable first, followed by the positive (red) cable to prevent electrical shorts.
- Prepare a cleaning solution by mixing one tablespoon of baking soda with one cup of warm water. This solution neutralizes battery acid and dissolves corrosion effectively.
- Apply the solution to the corroded areas using a wire brush or toothbrush, scrubbing thoroughly until all visible corrosion disappears. Ensure no liquid enters the battery cells.
- Rinse and dry all components with clean water and thoroughly dry with a clean cloth or compressed air. Any remaining moisture can accelerate future corrosion.
- Reconnect the battery, attaching the positive terminal first, followed by the negative terminal to minimize the risk of electrical shorts.
How to Prevent Battery Terminal Corrosion
Preventing corrosion extends battery life and maintains reliable electrical connections:
- Apply protective coatings such as battery terminal protector spray, dielectric grease, or petroleum jelly to create a moisture barrier. CRC’s Battery Terminal Protector is specifically designed for this purpose, forming a lead-free soft coating that protects terminals from corrosion.
- Use anti-corrosion washers containing sacrificial metals that corrode preferentially, protecting your actual terminals and posts from damage.
- Install copper compression terminals, which are among the best options for preventing further battery terminal corrosion. Their superior conductivity and corrosion resistance provide excellent long-term protection.
- Implement a corrosion prevention composition consisting of lithium grease, sodium bicarbonate, and magnesium oxide. This combination effectively stops corrosion by neutralizing acids and preventing gas exchange.
- Maintain proper charging levels by ensuring your alternator isn’t overcharging (above 14.5 volts) and your battery isn’t consistently undercharged.
Battery Terminal Configurations
Battery terminals can be arranged in various configurations depending on their intended application. The most common configurations include:
- Positive on left, negative on right corner
- Negative on left, positive on right corner
- Both terminals on the long side
- Both terminals on the short side
- Diagonally opposed terminals
- Terminals in the middle
Selecting the correct configuration is crucial, as purchasing a battery with the wrong layout may prevent cables from reaching the terminals properly. This is particularly important in tight engine compartments where cable routing options might be limited.
How to Replace Battery Terminals
When cleaning isn’t sufficient, replacing severely corroded or damaged terminals becomes necessary:
- Disconnect the battery, removing the negative cable first, then the positive cable to minimize the risk of electrical shorts.
- Remove old terminals using the appropriate wrench to loosen and detach them completely from both cable ends.
- Inspect cable ends for damage or corrosion that might require additional repair before attaching new terminals.
- Clean battery posts thoroughly with a wire brush to ensure optimal contact with new terminals.
- Install new terminals by placing them securely on the battery posts and tightening according to manufacturer specifications. Avoid over-tightening as this can damage both terminals and posts.
- Reconnect the battery, attaching the positive cable first, then the negative cable, and test connections by starting your vehicle or device.
Common Issues with Battery Terminals
Understanding common terminal problems helps you diagnose and resolve issues before they cause system failures:
Corrosion
Battery terminal corrosion creates resistance that impedes electrical flow, causing starting problems, electrical system malfunctions, and potentially shortened battery life. Regular inspection and cleaning prevent this common issue from escalating.
Loose Connections
Terminals that aren’t properly secured create intermittent electrical contact, resulting in power fluctuations, starting difficulties, and potential damage to sensitive electronic components. Regular vibration from vehicle operation often contributes to connection loosening over time.
Cracked or Damaged Terminals
Physical damage to terminals from impacts, extreme temperatures, or improper installation prevents proper connections and creates potential safety hazards. Damaged terminals should be replaced immediately to prevent electrical shorts and system failure.
Incompatible Terminals and Posts
Using mismatched components (like SAE terminals on JIS posts) creates loose, inefficient connections that cause voltage drops, excessive heat, and potential fire hazards. Always ensure compatibility between terminal and post types.
FAQs about Battery Posts and Terminals
Can You Mix SAE and JIS Battery Terminals?
I strongly advise against mixing SAE and JIS terminal types. SAE posts (19.5mm diameter) are significantly larger than JIS posts (17.3mm), creating loose connections when pairing JIS terminals with SAE posts. These incompatible connections cause voltage drops, excessive heat, and potential fire hazards.
Why Do Battery Terminals Corrode So Fast in Hot Weather?
Heat accelerates the chemical reactions between lead posts and sulfuric acid vapors that escape from the battery, intensifying corrosion rates. You can minimize this effect by using AGM or gel batteries that produce fewer emissions, applying quality silicone-based terminal protectors, and installing heat shields in engine compartments with high temperatures.
How Tight Should Battery Terminal Clamps Be?
Terminal clamps should be tightened until they cannot rotate on the post but avoid excessive force that might crack lead posts. For precise installation, use a torque wrench with settings of 5-7 Nm for standard automotive applications and 8-10 Nm for larger trucks and RVs.
Are Copper Battery Terminals Worth the Cost?
For high-demand applications like audio systems, marine installations, or commercial equipment, copper terminals deliver meaningful performance benefits. Their superior conductivity (approximately 25% better than lead) reduces voltage drop and improves efficiency in power-hungry systems. When combined with anti-oxidation coatings, copper terminals provide excellent long-term value despite their higher initial cost.
Can Corroded Battery Terminals Drain Your Battery?
Yes, corroded terminals create resistance that forces your alternator to work harder during operation and can establish parasitic drains that deplete your battery even when the vehicle is off. This continuous low-level drain eventually leads to complete battery discharge and potentially premature battery failure.
What’s the Difference Between Battery Posts and Terminals?
Battery posts are the fixed contact points protruding from the battery casing, while terminals are the adjustable connectors that attach to these posts. Posts are integral parts of the battery itself, while terminals are typically attached to the cables connecting to your electrical system.
Battery Venting Systems
While focusing on terminals and posts, it’s important to understand how battery venting systems interact with these components:
The cells of vented lead-acid batteries include openings that allow hydrogen and oxygen gas to escape during charging and provide access for adding water lost during gas production. These venting systems come in several configurations:
- Open caps – The most common design, allowing gases to escape freely
- Flame arrester caps – Prevent external flames from entering the cell
- Recombinant caps – Contain catalysts that cause hydrogen and oxygen gases to recombine into water, significantly reducing maintenance requirements
Proper venting is crucial for battery safety, as hydrogen gas buildup can create explosive conditions if not properly managed.
Modern Battery Terminal Technology
Battery terminal technology continues to evolve to meet the demands of modern electrical systems:
Smart Battery Terminals
The latest developments include smart terminals with integrated sensors that monitor battery health, connection quality, and electrical load. These advanced terminals can communicate with vehicle management systems to provide early warnings of potential issues.
High-Current Terminals for Electric Vehicles
Electric vehicle applications require specialized high-current terminals capable of handling continuous high-amperage loads. These terminals utilize advanced materials and cooling designs to prevent overheating during rapid charging and discharging cycles.
Military-Grade Terminals
Military and aerospace applications employ specialized terminals designed to withstand extreme environments, vibration, and electromagnetic interference. These ruggedized terminals often incorporate redundant connection points and advanced sealing technologies.
Conclusion: Ensuring Reliable Power Delivery
Understanding battery terminals and posts is essential for ensuring reliable power delivery in any application. By selecting the appropriate terminal types, performing regular maintenance, and implementing effective corrosion prevention measures, you can significantly extend the life of your batteries and ensure consistent performance in all conditions.
Whether you’re working with automotive, marine, industrial, or specialized battery systems, the fundamentals of proper terminal selection, installation, and maintenance remain critical for optimal performance. As battery technology continues to evolve, staying informed about the latest terminal designs and materials will help you make the best choices for your specific applications.
For more detailed information about custom battery solutions including 18650, Li-ion, Lithium polymer, and LiFePO4 battery packs, visit VADE Battery. Their engineering team specializes in designing battery systems with proper terminal selection for optimal performance and longevity. You can also explore their lithium battery types comparison guide or battery terminal corrosion prevention guide for additional resources.