When designing custom battery solutions for diverse applications, the cell format selection represents a critical engineering decision with measurable impact on performance metrics, safety parameters, and total cost of ownership. At VADE Battery, we specialize in developing IEC 62133-certified rechargeable battery packs across multiple technology platforms, including 18650 cylindrical (250-260 Wh/kg), lithium polymer (260-290 Wh/kg), and LiFePO4 prismatic cells (160-210 Wh/kg). The fundamental architectural difference between prismatic and cylindrical cells influences every aspect of battery system design—from thermal management effectiveness to production economics and safety certification pathways—with quantifiable implications for your application’s performance envelope and service life projections.
What Are Prismatic Battery Cells?
Prismatic cells feature a distinctive rectangular or square shape that optimizes space efficiency in applications where dimensional constraints are critical. These cells contain electrode materials arranged in layers and enclosed within a sturdy metal casing, typically aluminum or steel.
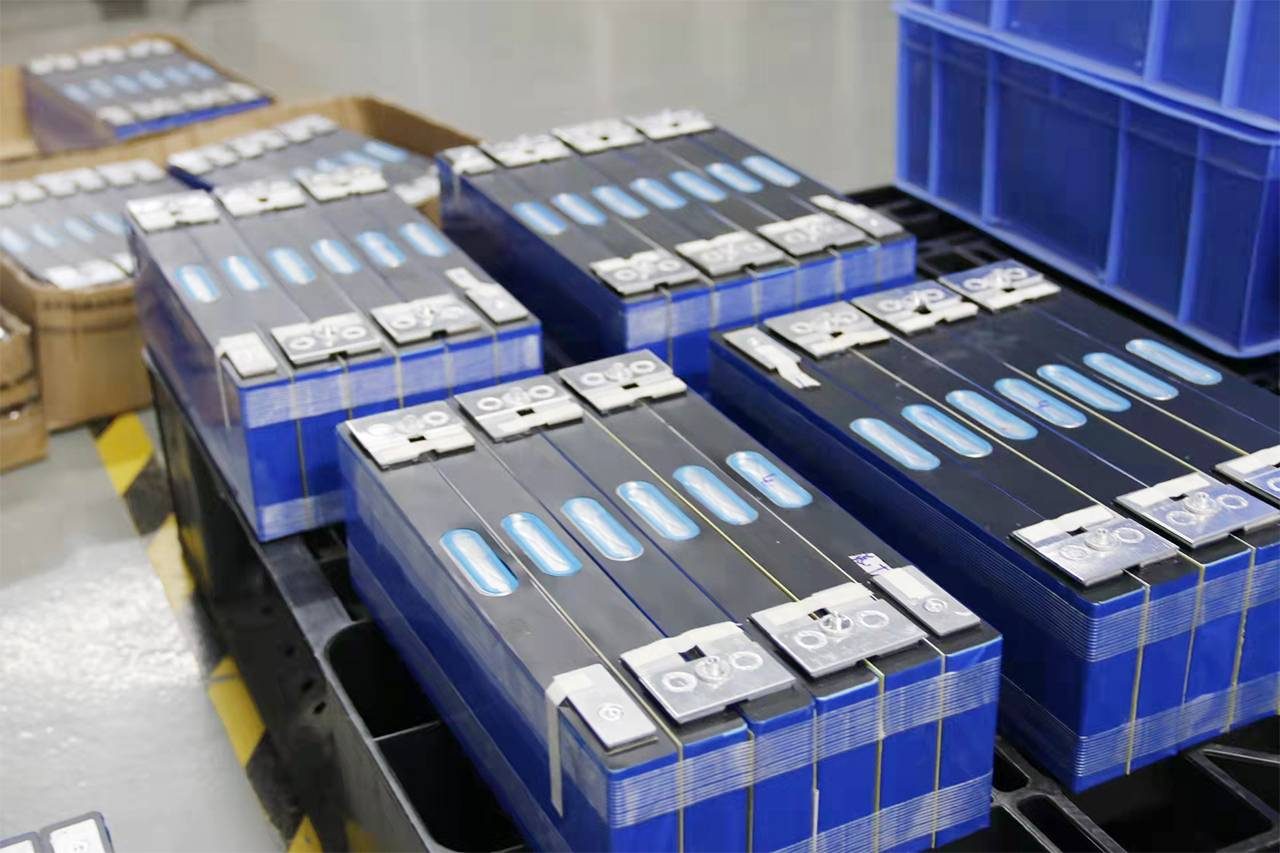
The construction of prismatic cells involves either a stacked or rolled configuration of electrode sheets (anode, separator, cathode). In stacked designs, flat layers of electrodes are precisely positioned on top of one another, while rolled configurations involve winding the electrodes and then flattening them into the prismatic shape.
Key characteristics of prismatic cells include:
Their flat, stackable design allows for excellent volumetric energy density, making them particularly valuable in space-constrained applications like electric vehicles and thin consumer electronics. The rectangular format enables up to 72% volume utilization efficiency in battery packs, significantly higher than what’s typically achieved with cylindrical alternatives.
Prismatic cells excel in thermal performance along their flat surfaces, though corner areas can experience thermal stress concentration. Modern designs incorporate sophisticated thermal management features to address this challenge, particularly important in high-capacity applications.
The manufacturing process involves precise electrode stacking or winding and flattening, followed by encasement in rigid aluminum or steel housings. These cells typically offer capacities ranging from 20Ah to over 100Ah, making them suitable for high-energy applications.
For more details on how prismatic cells are integrated into larger battery systems, visit our custom battery pack voltage guide.
What Are Cylindrical Battery Cells?
Cylindrical cells represent the classic battery format with their tubular shape and standardized dimensions. The most recognized form factor is the 18650 battery, measuring 18mm in diameter and 65mm in length, which has become an industry standard since its introduction by Sony in 1991.
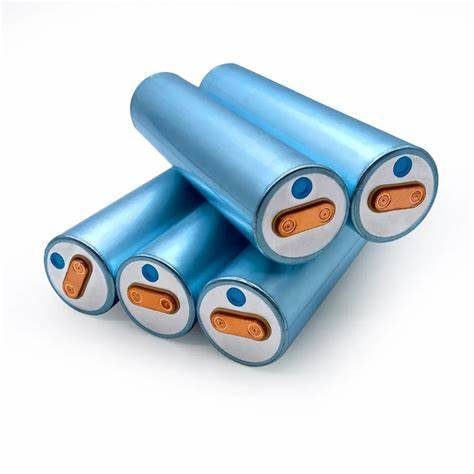
These cells feature electrode materials wound in a spiral configuration known as a “jelly roll” or “Swiss roll” design and enclosed in a metal casing, typically steel. This architecture provides inherent structural integrity and pressure resistance.
The cylindrical design offers several advantages:
The standardized dimensions (like 18650, 21700, and 26650) facilitate automated manufacturing processes, resulting in highly consistent production quality and lower cost per kWh. Current manufacturing efficiencies allow cylindrical cells to be produced at approximately $98/kWh compared to $121/kWh for prismatic alternatives – a 23% cost differential as of 2025.
The cylindrical structure provides excellent radial heat dissipation, creating natural pathways for thermal management. This design enables cylindrical cells to maintain temperature differentials of ≤8°C under 2C discharge rates, compared to prismatic cells’ ≤12°C differentials.
For applications requiring high vibration resistance or mechanical durability, cylindrical cells offer superior performance due to their tightly wound internal structure and robust metal casing. This makes them ideal for power tools, electric bicycles, and aerospace applications.
Our expertise in designing custom 18650 battery packs enables us to optimize these advantages for your specific application requirements.
Detailed Comparison: Prismatic vs Cylindrical Cells
Energy Density and Power Characteristics
The energy density trade-offs between these cell formats significantly impact application performance. Prismatic cells typically offer superior volumetric energy density (energy per unit volume), while cylindrical cells often provide better gravimetric energy density (energy per unit weight).
As of 2025, leading prismatic LFP (lithium iron phosphate) cells achieve energy densities of approximately 160-210 Wh/kg, while advanced cylindrical NMC (nickel manganese cobalt) cells can reach 255 Wh/kg. For high-power applications, cylindrical cells demonstrate exceptional capabilities with discharge rates reaching 45C, making them ideal for power-intensive usage scenarios.
Parameter | Prismatic Cells | Cylindrical Cells |
---|---|---|
Energy Density (2025) | 160-210 Wh/kg (LFP)Up to 255 Wh/kg (NMC) | 150-255 Wh/kg |
Volume Efficiency | 72% | 50-60% |
Discharge Rate | Generally lower C-rates | Up to 45C pulse discharge |
Best Power Applications | Energy storage, EVs | Power tools, high-drain devices |
For a more detailed breakdown of energy density comparisons across different battery chemistries, visit our energy density batteries guide.
Thermal Management Characteristics
Effective thermal management is crucial for battery safety, longevity, and performance. The geometric differences between prismatic and cylindrical cells create distinct thermal behavior patterns that must be considered in battery design.
Cylindrical cells demonstrate superior natural heat dissipation due to their radial design, which distributes heat more evenly around the circumference. This inherent advantage reduces active cooling requirements by approximately 14% in electric vehicle battery packs compared to prismatic alternatives.
Prismatic cells, while offering less efficient natural heat dissipation, provide large flat surfaces that can be coupled directly with cooling plates or phase-change materials. Advanced prismatic designs now incorporate dedicated cooling channels and thermal management features to address this limitation.
Modern battery management systems can mitigate thermal concerns for both cell types. Our LiFePO4 cell balancing technologies help optimize thermal performance across different cell architectures by ensuring uniform energy distribution.
Manufacturing Economics and Scalability
Manufacturing considerations significantly influence cell selection, especially for high-volume applications. The economics of production scale differently between these cell formats.
Cylindrical cell manufacturing advantages:
- Highly automated production with decades of process refinement
- Standardized dimensions enabling equipment sharing across manufacturers
- Lower material waste rates (12% less scrap metal compared to prismatic manufacturing)
- Established quality control protocols with 99.1% UN 38.3 certification pass rates (2025 data)
Prismatic cell manufacturing considerations:
- Higher initial production costs but simplified pack-level integration
- 18-22% lower pack assembly costs due to fewer connections required
- Emerging dry electrode coating technologies reducing energy requirements by up to 40%
- 22% more quality control checkpoints needed due to more complex construction
The manufacturing landscape continues to evolve, with significant investments in both cell formats. Tesla’s dry-coated 4680 cylindrical cells and CATL’s prismatic Qilin battery technology represent cutting-edge advancements reducing production costs and improving performance.
For insights into how battery manufacturing processes impact the final product, explore our guide on how lithium batteries are made.
Safety Architecture and Compliance
Battery safety remains paramount across all applications, with different cell formats offering distinct safety characteristics. As of 2025, regulatory requirements have become increasingly stringent, particularly for transportation and consumer applications.
Cylindrical cells feature inherent pressure relief mechanisms that enable 97.8% UL 2054 compliance, compared to prismatic cells’ 96.2% compliance rate. These built-in safety features help manage internal pressure during abnormal conditions and prevent catastrophic failures.
Modern prismatic cells have made significant safety advances, with welded venting channels achieving comparable thermal runaway containment. The latest EU Battery Regulation’s 2025 carbon footprint mandates now require prismatic cell producers to document 14.2 kg CO₂/kWh emissions—18% below cylindrical benchmarks.
Both formats require sophisticated Battery Management Systems (BMS) to monitor temperature, voltage, and current parameters. Our UN 38.3 certified batteries meet rigorous international transport safety standards regardless of cell format, ensuring confidence in shipping compliance.
Durability and Lifecycle Differences
Lifecycle performance varies significantly between cell formats and is further influenced by chemistry selection, usage patterns, and operating environment.
Lifecycle comparison (2025 benchmarks):
- Prismatic LiFePO4 cells: 2,000+ cycles at 80% depth of discharge
- Cylindrical NMC cells: ~800 cycles at equivalent depth of discharge
This 2.4x longevity advantage for prismatic LFP cells often offsets their higher initial costs in applications where system lifetime directly impacts return on investment. However, cylindrical cells generally offer superior mechanical durability in high-vibration environments due to their rigid structure and wound electrode configuration.
Factors affecting lifecycle include:
- Operating temperature range (cylindrical: -40°C to +70°C; prismatic: -20°C to +50°C)
- Charging protocols and C-rates
- Mechanical stress exposure
- Thermal management effectiveness
For applications requiring long service life under demanding conditions, our battery load testing services can help quantify performance differences between cell formats.
Best Applications for Each Cell Type
Where Prismatic Cells Excel
Prismatic cells dominate specific application categories where their unique characteristics provide clear advantages:
Electric vehicles: Major automakers including BYD, GM, and Volkswagen increasingly choose prismatic cells for their EV platforms. The flat format allows for efficient packaging in skateboard-style battery packs, while the large capacity reduces connection complexity. GM’s Ultium platform utilizes prismatic cells to achieve high voltage configurations (up to 720V nominal voltage by 2025).
Grid energy storage: For stationary applications where energy density and cycle life are prioritized over weight concerns, prismatic LiFePO4 cells offer compelling benefits. Hawaii’s 2025 Lānaʻi microgrid project demonstrates prismatic cells’ superiority in 8-hour duration applications.
Consumer electronics: Smartphones, tablets, and laptops increasingly utilize prismatic cells to achieve thinner profiles while maximizing battery capacity. The rectangular shape enables efficient use of limited internal space in modern slim devices.
These applications benefit from prismatic cells’ volumetric efficiency, simplified thermal management interface (flat cooling surfaces), and reduced connection complexity.
Where Cylindrical Cells Dominate
Cylindrical cells maintain their leadership position in several key application areas:
Power tools and garden equipment: The high discharge rates, excellent vibration resistance, and cost-effectiveness of cylindrical cells make them ideal for power-intensive tools. Their standardized dimensions facilitate easy battery pack design across multiple product lines.
Electric bicycles and lightweight mobility: For weight-sensitive applications, cylindrical cells’ superior gravimetric energy density provides longer range without excessive weight penalties. Their mechanical durability also helps withstand road vibration and shock.
Aerospace and defense: Mission-critical applications favor cylindrical cells for their proven reliability, standardized form factors, and excellent thermal management characteristics. The 2025 updates to IATA Battery Guidance Document have established new sodium-ion classification protocols that benefit cylindrical formats with updated state-of-charge limits for air transport.
Consumer electronics with high power demands: Gaming laptops, power banks, and high-performance portable devices benefit from cylindrical cells’ rapid discharge capabilities and thermal efficiency.
For specialized applications requiring optimal power-to-weight ratios, explore our high-drain 18650 cell options.
Future Trends in Battery Cell Technology (2025-2030)
The battery industry continues evolving rapidly, with significant advancements reshaping both prismatic and cylindrical formats. Several key trends are emerging in 2025 that will influence the competitive landscape over the next five years.
Solid-State Battery Integration
Solid-state battery technology represents a revolutionary advancement with significant implications for both cell formats. By replacing liquid electrolytes with solid materials, these batteries promise improved safety, energy density, and charging speed.
As of early 2025, solid-state battery prototypes have achieved energy densities up to 450 Wh/kg, with prismatic configurations leading in aerospace applications due to their stable layering capabilities. Toyota’s Q1 2025 trials revealed prismatic solid-state cells sustaining 1,200 cycles at 4C charging—a 300% improvement over traditional lithium-ion technologies.
While commercial solid-state batteries remain in development, both prismatic and cylindrical manufacturers are adapting their designs to accommodate this emerging technology. The stable, flat layers in prismatic cells may offer advantages for solid electrolyte integration, though cylindrical designs are also showing promise for consumer applications.
Advanced Manufacturing Processes
Manufacturing innovations are significantly impacting production economics and performance characteristics of both cell formats.
Dry electrode coating technology, pioneered in Tesla’s 4680 cylindrical cells, reduces factory floor space requirements by 41% and energy consumption by 19% compared to traditional wet slurry methods. This process eliminates the need for solvent-based manufacturing steps, reducing costs and environmental impact.
Meanwhile, prismatic manufacturers are countering with innovations like CATL’s cell-to-pack (CTP) technology in their Qilin battery, which achieves record-breaking 72% volume utilization efficiency. Laser-assisted lamination techniques now enable prismatic cells to achieve 0.3mm electrode tolerances—critical for high-voltage EV packs.
These manufacturing advancements are progressively narrowing the cost gap between cell formats while improving performance metrics across both designs.
Chemistry Diversification Beyond Lithium
While lithium-ion technology continues to dominate, alternative chemistries are gaining traction in specific applications.
Sodium-ion batteries represent one of the most promising alternatives, with CATL and the U.S. Department of Energy’s LENS consortium making significant strides toward commercialization. These batteries offer a lower-cost, more abundant alternative to lithium-ion technologies, with cylindrical sodium-ion cells now available in the 18mm x 65mm form factor.
In 2024, potassium-ion variants were unveiled in the 18650 format, utilizing a proprietary 4V Potassium Prussian White cathode and commercially available graphite anode. This technology offers potential cost advantages for grid storage applications.
For prismatic formats, sodium-ion commercialization is accelerating, with prototypes achieving 160 Wh/kg densities. Projections indicate 2026 cost parity with LFP chemistries for grid storage applications.
These emerging chemistries are expanding the application range for both cell formats while addressing resource scarcity concerns and specific performance requirements.
Making Your Cell Selection Decision
Choosing between prismatic and cylindrical cells requires careful consideration of your specific application requirements. Based on our extensive experience designing custom battery solutions, we recommend evaluating three critical factors:
Energy Duration Requirements
For applications requiring sustained energy delivery over extended periods, such as grid storage systems or long-range electric vehicles, prismatic cells typically offer advantages in energy capacity and cycle life. Their higher volumetric efficiency and simplified connections make them well-suited for high-capacity applications.
Applications requiring short bursts of high power, such as power tools or drones, often benefit from cylindrical cells’ superior power density and discharge capabilities. Their excellent thermal management also supports high C-rate operations without excessive temperature increases.
Our battery C-rate guide provides detailed information on selecting appropriate cell types based on discharge requirements.
Operating Environment Considerations
Environmental factors significantly impact cell performance and longevity. When selecting between formats, consider:
Temperature extremes: Cylindrical cells generally offer better performance in wider temperature ranges (-40°C to +70°C) compared to prismatic alternatives (-20°C to +50°C).
Vibration exposure: Applications with significant vibration or mechanical shock benefit from cylindrical cells’ robust construction and wound electrode design, which minimizes electrode material degradation.
Space constraints: Where dimensional efficiency is critical, prismatic cells offer superior space utilization and flexible form factors that can be customized to available volumes.
Thermal management access: Cooling system design may favor one cell format over another. Prismatic cells offer large, flat surfaces ideal for direct cooling plate contact, while cylindrical cells benefit from natural radial heat dissipation.
Total Cost of Ownership Analysis
Looking beyond initial purchase price to evaluate total lifecycle costs reveals important differences between cell formats:
Cost Factor | Prismatic Cells | Cylindrical Cells |
---|---|---|
Initial Cost (100kWh system, 2025) | $14,200 | $12,900 |
10-Year Maintenance | $3,800 | $5,100 |
Cell Replacement Frequency | Lower | Higher |
Pack Integration Complexity | Simpler | More complex |
Cooling System Requirements | More extensive | Less extensive |
The optimal economic choice depends on your specific application requirements, expected operational lifetime, and maintenance capabilities. For applications with long service life requirements, the higher initial cost of prismatic cells may be offset by their superior longevity and reduced maintenance needs.
Our series-parallel battery configurations guide provides additional insights into optimizing battery pack design based on your specific voltage and capacity requirements.
How VADE Battery Designs Custom Solutions
At VADE Battery, we approach cell selection as a critical engineering decision that impacts every aspect of battery performance. Our systematic design process ensures optimal cell selection for each unique application:
- Detailed requirement analysis: We begin by thoroughly understanding your application’s specific needs, including power requirements, dimensional constraints, environmental conditions, and lifecycle expectations.
- Load profile testing: Our battery load testing capabilities allow us to simulate real-world usage patterns and quantify performance differences between cell options under your specific operating conditions.
- Thermal modeling: We utilize advanced thermal simulation tools to predict heat generation and dissipation patterns, ensuring adequate thermal management regardless of cell format selection.
- Safety certification planning: All our designs incorporate comprehensive safety features and are engineered to meet relevant certifications, including UN 38.3 for transport safety. Our UN 38.3 certified batteries meet rigorous international standards for safe shipping worldwide.
- Custom BMS development: We design specialized Battery Management Systems optimized for your chosen cell format and application requirements, ensuring optimal performance, safety, and longevity.
Whether your project requires the space efficiency of prismatic cells or the established reliability of cylindrical formats, our engineering team can develop a battery system that meets your exact specifications. For applications requiring deep cycling capabilities, we often suggest prismatic LiFePO4 cells with their superior cycle life. Applications with variable loads and high power requirements might benefit more from cylindrical cells’ pulse discharge capabilities.
Conclusion: Balancing Performance, Safety, and Economics
The optimal selection between prismatic and cylindrical cells requires evidence-based evaluation of your application’s specific performance requirements against quantifiable cell characteristics. While prismatic cells deliver superior volumetric efficiency (72% vs. 60% pack utilization), simplified interconnection architecture, and extended cycle longevity (2,000+ cycles at 80% DoD for LiFePO4), cylindrical cells provide demonstrable advantages in manufacturing consistency (99.1% UN 38.3 certification pass rate), thermal management efficiency (8°C vs. 12°C temperature differentials), and production economics ($98/kWh vs. $121/kWh).
Recent advancements in materials science and manufacturing processes continue to enhance both form factors. The emergence of solid-state (450 Wh/kg), sodium-ion (160 Wh/kg by 2025), and potassium-ion chemistries is expanding application possibilities while addressing material resource constraints and performance limitations. These developments are supported by rigorous certification standards, including IEC 62133:2023 for cell-level safety and UL 2580:2025 for thermal propagation resistance.
At VADE Battery, our engineering approach combines technical performance analysis with practical deployment expertise. Our IEC/ISO 17025-accredited testing facilities enable comprehensive assessment of both prismatic and cylindrical technologies, ensuring our recommendations reflect technical merit rather than format preference. This commitment to engineering objectivity has earned our solutions UL 2271, UL 2272, and UN 38.3 certifications across multiple application categories.
For technical specifications, design consultation, or custom battery solutions that align with your precise application requirements, visit our custom lithium battery manufacturing process page or contact our applications engineering team today.
What’s the difference between prismatic and cylindrical battery cells?
Prismatic and cylindrical cells differ primarily in their shape and internal structure. Prismatic cells have a rectangular or square shape with electrodes arranged in layers within a rigid aluminum or steel casing, which maximizes space efficiency in devices with flat form factors. Cylindrical cells, like the common 18650 format (18mm diameter, 65mm length), feature electrodes wound in a spiral “jelly roll” configuration inside a metal tube. This fundamental difference affects everything from energy density to manufacturing costs – prismatic cells typically offer better volumetric energy density while cylindrical cells often provide better gravimetric energy density (energy per weight) and are generally less expensive to produce due to highly automated manufacturing processes.
Why do manufacturers choose cylindrical cells for some applications and prismatic cells for others?
Manufacturers select cell types based on specific application requirements. Cylindrical cells are preferred for applications requiring high discharge rates, mechanical durability, and cost efficiency, making them ideal for power tools, electric bicycles, and portable electronics. Their tightly wound structure provides excellent vibration resistance, while standardized sizes enable automated production that reduces costs to approximately $98/kWh (compared to $121/kWh for prismatic alternatives). Prismatic cells, conversely, excel in space-constrained applications like electric vehicles and thin consumer electronics, where their flat, stackable design allows for excellent space utilization (up to 72% volume efficiency versus 50-60% for cylindrical cells). The decision ultimately balances factors like available space, power requirements, thermal management needs, and budget constraints.
How do prismatic and cylindrical batteries compare in terms of safety and thermal management?
Thermal management and safety characteristics differ significantly between these cell formats. Cylindrical cells demonstrate superior natural heat dissipation through their radial design, maintaining temperature differentials of approximately 8°C under discharge compared to prismatic cells’ 12°C differentials. This inherent advantage reduces active cooling requirements by roughly 14% in electric vehicle battery packs. Cylindrical cells also feature built-in pressure relief mechanisms that enable 97.8% UL 2054 compliance (versus 96.2% for prismatic cells). However, prismatic manufacturers have made significant safety advances with welded venting channels achieving comparable thermal runaway containment. Prismatic cells offer large flat surfaces that can be directly coupled with cooling plates, while their larger size sometimes creates challenges for Battery Management Systems to protect against overcharging and manage heat dissipation effectively.
Are prismatic batteries better than cylindrical batteries for electric vehicles?
For electric vehicles, prismatic cells often offer compelling advantages, though the answer isn’t universal. Major automakers including BYD, GM, and Volkswagen increasingly choose prismatic cells for their EV platforms because their flat format enables efficient packaging in skateboard-style battery packs, maximizing interior space. Prismatic cells also reduce connection complexity in large battery systems and offer excellent volumetric energy density. Their flat surfaces facilitate direct cooling plate contact, simplifying thermal management system design. However, cylindrical cells still appear in some premium EVs due to their cost advantages, excellent thermal properties, and reliability. Tesla notably used thousands of small cylindrical cells in early models before developing their larger 4680 cylindrical format with dry electrode coating technology. The optimal choice depends on specific vehicle design requirements, production volume, and cost targets.
What are the main disadvantages of prismatic cells compared to cylindrical cells?
Prismatic cells face several disadvantages compared to their cylindrical counterparts. Manufacturing complexity and cost represent significant drawbacks, with prismatic cells costing approximately 23% more per kWh due to less automated production processes and more complex quality control requirements (22% more checkpoints needed). Thermal management can be challenging, as prismatic cells typically maintain temperature differentials of up to 12°C under discharge compared to cylindrical cells’ 8°C, potentially requiring more sophisticated cooling systems. Prismatic cells also present reliability concerns in some applications – if one cell fails in a prismatic pack, it can potentially compromise the entire battery system, whereas cylindrical packs can often continue functioning with slightly reduced capacity when a single cell fails. Additionally, prismatic cells are more prone to swelling over time, requiring proper compression measures to maintain structural integrity throughout their operational life.