Lithium batteries power everything from smartphones to electric vehicles, representing one of the most transformative energy storage technologies of our time. Yet for all their advantages in energy density and performance, lithium batteries command a significant price premium compared to traditional battery chemistries. At Vade Battery, we specialize in developing custom lithium battery solutions ranging from compact 7.4V battery packs for consumer electronics to industrial-grade 72V energy storage systems. Our engineering team works daily with the cost factors that influence lithium battery production, developing strategies to optimize performance while managing expenses. This comprehensive analysis explores the primary contributors to lithium battery costs and explains the manufacturing realities behind their premium pricing.
Raw Material Costs and Supply Chain Factors
The fundamental building blocks of lithium batteries represent the single largest cost component in their production. According to the U.S. Department of Energy’s 2023 cost analysis, raw materials typically account for 50-70% of a lithium battery’s manufacturing cost. This significant expense stems from both the intrinsic value of the materials and the complex global supply chain required to process and deliver them to battery manufacturers.
Critical Metals and Their Market Dynamics
Lithium itself, despite giving these batteries their name, typically comprises less than 5% of the total cell materials by weight. However, lithium carbonate pricing exhibits extreme volatility, with market rates fluctuating between $15,000 and $80,000 per metric ton over the past five years according to Benchmark Mineral Intelligence. This volatility directly impacts our production costs for everything from our ultra-low temperature battery series to standard 48V battery systems.
Even more significant are the cathode metals that determine a battery’s performance characteristics. Cobalt, a critical component in high-energy-density NMC (Nickel-Manganese-Cobalt) cathodes, routinely trades above $30,000 per metric ton. Nearly 70% of global cobalt production comes from the Democratic Republic of Congo, creating both supply chain vulnerabilities and ethical sourcing concerns. Nickel, another essential cathode component, has seen its own price volatility with spot prices periodically exceeding $20,000 per ton following supply disruptions.
For applications prioritizing long cycle life and safety over maximum energy density, we often implement LiFePO₄ (lithium iron phosphate) chemistry. While this reduces dependency on cobalt and nickel, the specialized manufacturing processes required for LFP cathode materials introduce their own cost factors. The phosphate precursors require precise control during synthesis to achieve proper crystalline structure, contributing to production expenses even when using more abundant base metals.
Electrolyte and Separator Material Considerations
Beyond the visible metals that capture most attention, the electrolyte and separator materials represent critical components with substantial cost implications. High-purity electrolyte solutions typically utilize lithium hexafluorophosphate (LiPF₆) salt in organic solvents, with manufacturing costs influenced by required purity levels exceeding 99.99% to prevent side reactions that would degrade battery performance.
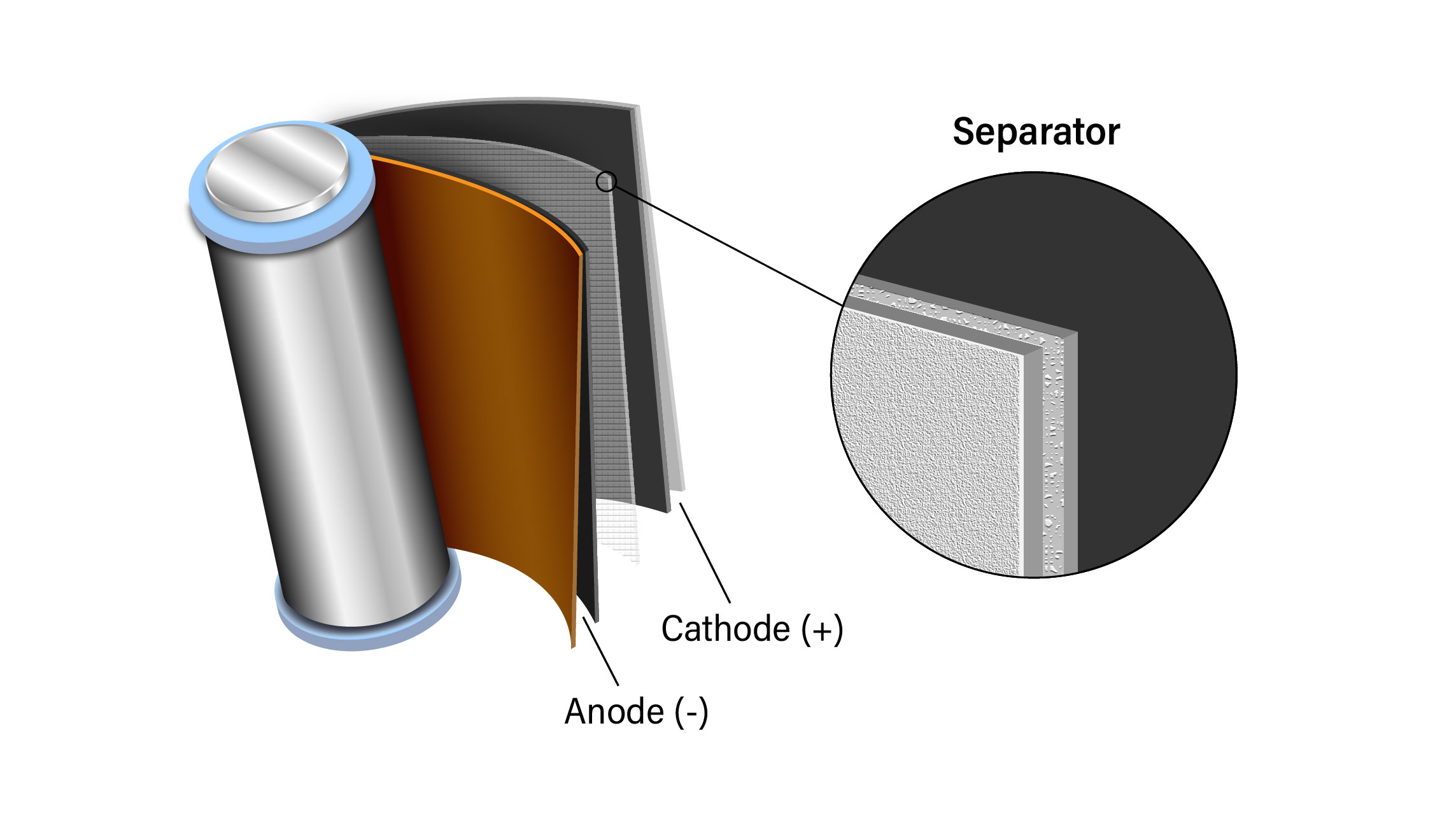
Separator materials, typically manufactured from specialized microporous polyethylene or polypropylene films, require precise thickness control (typically 15-25 micrometers) and uniform porosity. These separator films must maintain mechanical integrity while allowing lithium-ion transport between electrodes. Manufacturing separators with these characteristics requires specialized extrusion and stretching processes that add significant cost to the final cell. For our high-performance 51.8V battery packs, we utilize ceramic-coated separators that enhance thermal stability at temperatures up to 180°C but add approximately 15-20% to the material cost component.
Global Supply Chain Vulnerabilities
The geographically concentrated nature of battery material processing creates additional cost pressures through supply chain risk premiums. According to the International Energy Agency’s 2023 report on critical minerals, China processes approximately 60% of the world’s lithium, 70% of cobalt, and 80% of graphite used in battery anodes. This concentration creates strategic vulnerabilities for battery manufacturers outside these regions.
We mitigate these supply chain risks through strategic partnerships with multiple qualified material suppliers across different regions, though diversification comes with its own cost implications. Quality control systems must be duplicated across suppliers, and qualification testing for new material sources adds to research and development expenses. Transportation costs also factor significantly into material expenses, with specialized handling requirements for reactive electrode materials and volatile electrolyte components. These logistics considerations become increasingly significant for our larger format systems like our industrial-grade 72V battery packs that require substantial material volumes.
Complex Manufacturing Processes
The transformation of raw materials into functional lithium battery cells requires sophisticated manufacturing processes with stringent precision requirements. These specialized production techniques contribute significantly to the final cost of lithium batteries, with manufacturing complexity accounting for approximately 20-30% of production expenses.
Precision Requirements in Cell Production
Manufacturing lithium battery cells demands extraordinary precision at nearly every step of the process. Electrode coating represents one of the most critical operations, requiring uniform application of active materials onto metallic current collectors (copper for anodes, aluminum for cathodes) with thickness variations typically held below ±2 micrometers. This precision directly impacts cell capacity, internal resistance, and cycle life performance.
Our 18650 cell-based battery packs benefit from decades of manufacturing refinement in this cylindrical format, yet production still requires sophisticated machinery for winding electrodes with consistent tension control. For our custom prismatic and pouch cell formats used in space-constrained applications, manufacturing complexity increases further as these geometries require specialized equipment for stacking or folding electrode assemblies with precise alignment.
Cell finishing operations add another layer of manufacturing complexity. The electrolyte filling process must occur in extremely dry environments (typically below 100 ppm moisture) to prevent contamination that would cause performance degradation. Formation cycling—the initial charge-discharge sequences that establish the solid-electrolyte interphase (SEI) layer—requires precision control of current and voltage profiles over periods ranging from 24-72 hours, with significant energy consumption and specialized equipment needs.
Clean Room Requirements and Quality Control
Lithium batteries demand manufacturing environments with exceptional cleanliness standards. Particles as small as 10 micrometers can create internal short circuits or accelerate degradation mechanisms within cells. Our production partners maintain ISO Class 7-8 clean room facilities with sophisticated air filtration systems, specialized worker garments, and rigorous contamination control protocols that add substantial operational costs to battery manufacturing.
Quality control represents another significant expense in lithium battery production. Each cell undergoes multiple inspection points, including automated optical inspection of electrodes, X-ray examination to detect internal defects, and precision weight measurements to verify electrolyte filling. For our mission-critical 46.8V battery systems used in medical applications, 100% of cells undergo additional screening including extended open-circuit voltage monitoring to detect subtle manufacturing defects that could impact performance.
These quality control measures add direct costs through specialized equipment and labor but deliver substantial value by preventing field failures and enhancing safety. Our internal data indicates that comprehensive screening processes identify approximately 2-5% of cells with minor defects that could lead to premature failure or reduced performance, justifying the additional production expense through enhanced reliability.
Automation and Scale Challenges
While automation has reduced some manufacturing costs, the precision requirements of lithium battery production limit the potential for cost reduction through mechanization alone. Electrode handling systems must manage extremely thin, easily damaged materials with consistent tension control. Assembly operations require specialized tooling for tasks like tab welding, where ultrasonic or laser welding systems join current collector tabs with tolerances measured in micrometers.
The challenge of scaling production represents another cost factor in lithium battery manufacturing. Unlike many technologies where economies of scale follow predictable cost curves, lithium battery production requires careful balancing of throughput against quality control. Production speed increases risk introducing subtle defects that may not manifest until after cells enter service. For our high-reliability 24V battery systems used in critical infrastructure applications, we prioritize manufacturing processes that emphasize consistency over maximum throughput, accepting the associated cost premium to ensure performance reliability.
Energy consumption during manufacturing adds another significant expense. The dry room environments required for cell assembly typically maintain relative humidity below 1%, requiring substantial dehumidification systems. Formation cycling consumes considerable electricity, and thermal processing steps for electrode drying and electrolyte activation require precise temperature control over extended periods. These energy-intensive processes contribute to production costs while also influencing the carbon footprint of battery manufacturing.
Battery Management Systems and Safety Features
The sophisticated electronics required to manage lithium batteries represent a substantial portion of their overall cost structure. Unlike simpler battery chemistries, lithium cells require careful monitoring and control to ensure safe, efficient operation throughout their service life. These protection systems typically account for 15-25% of total pack costs depending on complexity and functionality.
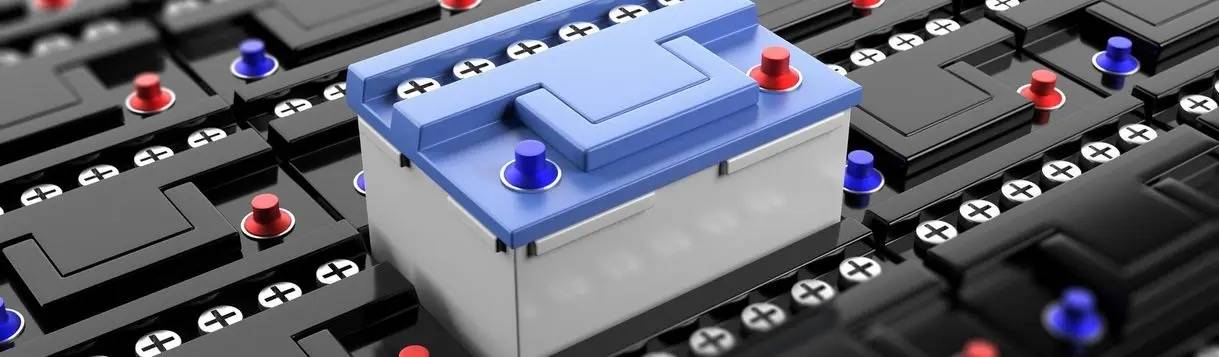
The Critical Role of BMS in Lithium Batteries
Every lithium battery pack we produce incorporates a Battery Management System (BMS) tailored to the specific application requirements. These electronic control systems serve multiple critical functions: preventing cells from exceeding safe voltage limits during charging, monitoring discharge rates to prevent damaging over-current conditions, balancing charge levels between individual cells, and tracking temperature at multiple points within the pack.
For our 12V lithium battery replacements used in industrial equipment, we implement BMS designs that maintain cell voltage imbalance below 50mV throughout the discharge cycle, significantly extending useful life compared to systems with basic protection. The development costs for these specialized control systems include both hardware engineering and extensive firmware development, with proprietary algorithms refined through thousands of test cycles under varying operational conditions.
The BMS complexity scales with battery voltage and capacity. Our high-voltage 72V systems incorporate redundant protection layers with independent overtemperature monitoring, multiple current sensors, and sophisticated isolation monitoring to detect insulation degradation before it can create safety hazards. These advanced features require higher-grade components, including automotive-qualified microcontrollers, precision analog-to-digital converters, and multiple layers of isolation between sensing and control circuits.
Protection Circuitry Specifications and Costs
The protection components within a lithium battery pack must meet exceptional reliability standards while operating under challenging conditions. Current sensing elements must accurately measure flows ranging from milliamps during standby to hundreds of amps during peak loads in our high-power systems. Temperature monitoring requires networks of thermistors or digital temperature sensors positioned at strategic locations determined through thermal modeling and verified with infrared imaging during qualification testing.
Protection Feature | Typical Component Cost Range | Performance Specification |
---|---|---|
Cell voltage monitoring | $0.25-1.50 per cell | ±10mV accuracy, 50ms sampling rate |
Current sensing | $3.50-20.00 per pack | ±1% accuracy, response time 500V isolation, <250μA leakage |
Communication interface | $5.00-35.00 per pack | CAN bus, Modbus, or proprietary protocol |
For applications requiring maximum fault tolerance, such as our medical-grade 36V battery packs, we implement dual-redundant monitoring systems with independent voltage references and separate microcontrollers that cross-check measurements. These redundant architectures add component costs while significantly enhancing safety for critical applications where failure is not an option.
The intelligence embedded within modern BMS designs extends beyond basic safety functions to include features that enhance battery longevity and performance. Advanced state-of-charge estimation algorithms combine voltage measurements with coulomb counting and impedance tracking to provide accurate capacity information throughout the discharge cycle. Thermal management control interfaces regulate active cooling systems in high-discharge applications, preserving cell life by preventing temperature excursions during demanding use cases.
Testing and Certification Requirements
The regulatory requirements for lithium battery safety represent another significant cost driver. Every battery design we produce undergoes comprehensive certification testing according to standards including UN 38.3 for transportation safety, IEC 62133 for cell safety, and UL 1642/2054 for various applications. These testing protocols include extreme abuse conditions such as crush testing, penetration resistance, thermal cycling between -40°C and +75°C, and short-circuit evaluation.
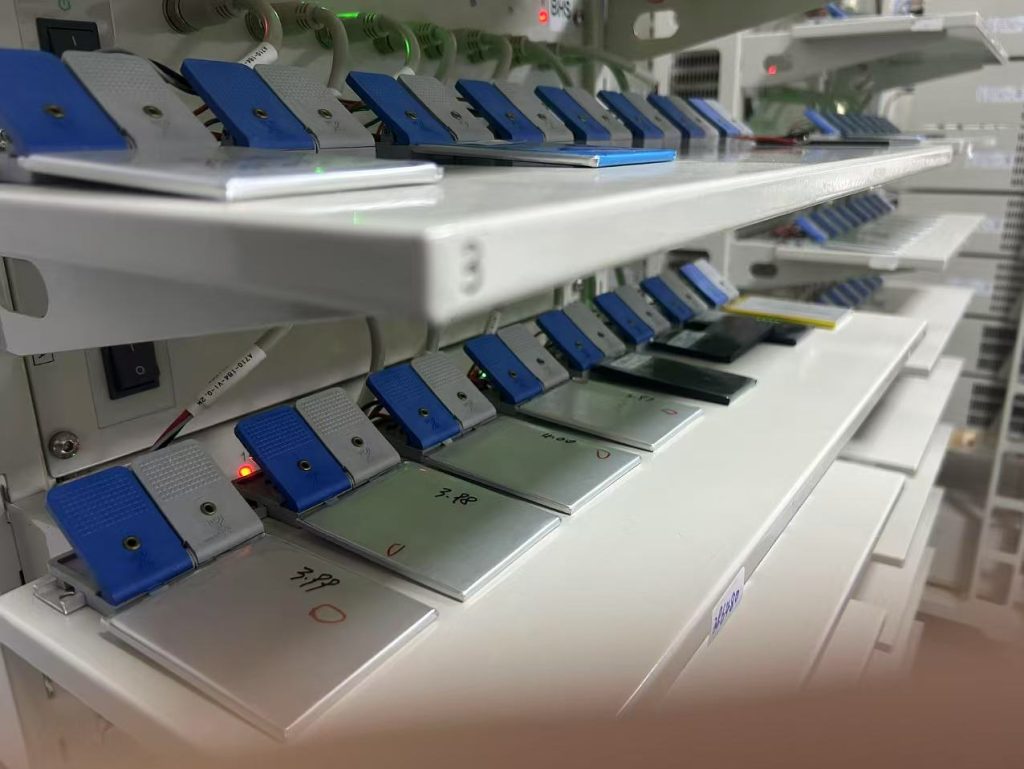
For our transportation-focused 48V battery systems, additional standards such as ECE R100 (for automotive applications) or EN 50604 (for light electric vehicles) may apply, requiring further specialized testing. These certification processes typically cost between $15,000-$50,000 per battery model depending on complexity and application requirements. While these expenses are amortized across production volumes, they contribute significantly to the development costs for specialized battery solutions.
Internal testing extends beyond regulatory requirements to include application-specific validation. For batteries destined for vibration-intensive environments, we conduct extended testing on electrodynamic shakers that replicate field conditions accelerated to compress years of service into weeks of laboratory evaluation. Custom environmental chambers simulate temperature extremes, humidity cycling, and salt fog exposure for marine applications. These comprehensive test programs add to development expenses but ensure our batteries deliver reliable performance throughout their intended service life.
Packaging and Mechanical Integration Expenses
Converting individual lithium cells into functional battery systems requires sophisticated packaging technologies that protect the electrochemical components while enabling safe, reliable operation in diverse environments. These mechanical integration elements add 10-15% to overall battery costs but provide essential protection and functionality that directly impact performance and safety.
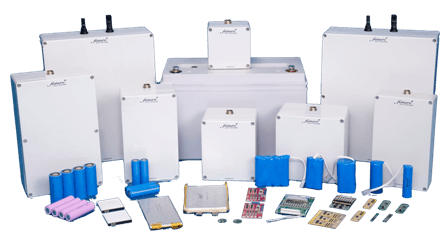
Enclosure Materials and Manufacturing
The protective housing for lithium battery packs must satisfy multiple demanding requirements simultaneously. For our industrial 51.2V battery systems, enclosures typically utilize aluminum alloys with wall thicknesses ranging from 1.5-3mm, providing excellent thermal conductivity, electromagnetic shielding, and mechanical protection. Computer-controlled machining processes with tolerances held to ±0.1mm ensure precise component fitment, but these manufacturing techniques add significant cost compared to simple plastic molding processes used for less demanding applications.
Applications with extreme environmental exposure require additional protection measures. Our IP67-rated enclosures undergo pressure testing to verify water and dust exclusion at depths up to 1 meter. Specialized gasket materials maintain sealing performance across temperature ranges from -40°C to +85°C while resisting degradation from ultraviolet exposure and chemical contaminants. These advanced sealing systems add component costs while requiring precise manufacturing to maintain compression forces within specified limits.
The structural design of battery enclosures must also account for thermal expansion differences between components, vibration isolation, and impact resistance appropriate to the application. Our engineering team utilizes finite element analysis to optimize these designs, reducing material usage while maintaining structural integrity. For weight-sensitive applications such as portable equipment powered by our lightweight 7.4V battery packs, we implement composite enclosure materials that reduce weight by up to 40% compared to aluminum alternatives, though these advanced materials typically add 25-30% to the enclosure cost component.
Thermal Management Systems
Effective thermal management represents one of the most significant engineering challenges in lithium battery design. Cell performance, longevity, and safety all depend on maintaining appropriate operating temperatures, with each chemistry having specific optimal ranges. For applications with modest power requirements, passive cooling through strategic cell spacing and thermally conductive materials may suffice, adding minimal cost to the overall system.
However, high-discharge applications such as our 72V traction battery systems require active thermal management solutions. These typically incorporate liquid cooling circuits with precision flow control, temperature sensors at multiple points within the pack, and control algorithms that adjust cooling intensity based on both current operating conditions and thermal history. The addition of pumps, heat exchangers, temperature sensors, and control electronics can add 15-30% to total pack cost, but these systems enable sustained high-power operation while preventing thermal degradation that would otherwise shorten battery life.
Even batteries without active cooling require careful thermal design. We utilize specialized gap-filling materials with thermal conductivity values between 3-8 W/m·K to transfer heat from cells to external enclosure surfaces. These thermally conductive but electrically insulating compounds add material cost and assembly complexity but substantially improve temperature uniformity across cell groups. For applications with intermittent high-discharge requirements, we incorporate phase change materials that absorb heat during peak loads and gradually release it during rest periods, damping temperature fluctuations that would accelerate aging mechanisms.
Interconnection Technologies
The connections between individual cells represent another critical cost component in lithium battery systems. For our 36V battery packs used in power tools and similar applications, we implement laser-welded nickel or copper bus bars with precisely controlled weld penetration to join cells without thermal damage to internal components. These welding processes require specialized equipment with comprehensive process monitoring to ensure consistent electrical resistance and mechanical strength at each connection point.
High-current applications demand particularly robust interconnection systems. Our industrial-grade battery packs utilize interconnects capable of handling continuous currents exceeding 200A with temperature rise limited to 20°C above ambient. These heavy-duty connections typically use copper bus bars with cross-sectional areas determined through both electrical current capacity and mechanical strength requirements. Specialized plating processes, typically nickel or tin, protect these connections from oxidation while maintaining low contact resistance throughout the battery’s service life.
The internal wiring within battery packs represents another significant cost element. We select conductor sizes based on both continuous and peak current requirements, typically using silicone-insulated wire with temperature ratings exceeding 150°C to maintain safety margins during high-load operation. Terminal connections utilize crimped or ultrasonic welded terminations rather than soldered joints, as the latter can create weak points in high-vibration environments. These specialized connection techniques require dedicated tooling and process validation for each battery design, contributing to both development and production costs.
Transportation and Regulatory Compliance
The classification of lithium batteries as dangerous goods under international shipping regulations creates unique logistical challenges and associated costs. These regulatory requirements influence not only shipping expenses but also design decisions, testing protocols, and documentation systems, collectively adding 8-12% to total battery costs.
UN 38.3 Transportation Testing Requirements
All lithium batteries shipped internationally must comply with UN 38.3 regulations for dangerous goods transportation. This comprehensive testing protocol subjects batteries to eight specific abuse tests: altitude simulation, thermal cycling, vibration, shock, external short circuit, impact/crush, overcharge, and forced discharge. Each test sequence requires multiple battery samples at different states of charge, with strict pass/fail criteria based on observable damage, temperature rise, and voltage behavior.
For our custom battery designs, these mandatory tests typically cost between $8,000-$15,000 per model, depending on size and complexity. Specialized testing laboratories maintain the calibrated equipment and controlled environments required for these standardized protocols. While these expenses are typically amortized across production quantities, they represent a significant development cost, particularly for specialized batteries with limited production volumes. Our engineering team designs with these requirements in mind, incorporating features that enhance robustness under the specific stress conditions evaluated in UN 38.3 testing.
Beyond initial certification, ongoing compliance with dangerous goods regulations requires detailed documentation for every shipment. Our battery systems include mandatory labeling with Watt-hour capacity, UN numbers, and appropriate hazard warnings. Shipping documentation must include test summary information confirming UN 38.3 compliance, with format and content requirements that changed significantly with the 2020 updates to IATA Dangerous Goods Regulations. Maintaining these documentation systems adds administrative overhead to every battery shipment.
Air Transport Restrictions and Alternatives
The most significant transportation challenge for lithium batteries involves air freight restrictions. Current IATA regulations prohibit shipping lithium batteries as cargo on passenger aircraft except when installed in or packed with equipment, and even cargo aircraft have strict limitations on battery size and packaging requirements. These restrictions create logistical challenges for international distribution, particularly for our higher capacity battery systems exceeding 100 Watt-hours.
Alternative shipping methods such as ocean freight introduce longer transit times, typically adding 3-5 weeks for international movements compared to air freight. These extended timelines increase working capital requirements as inventory spends more time in transit. Climate-controlled containers may be necessary to prevent temperature extremes during ocean transport, adding freight costs that can exceed $2,000 per shipping container for transoceanic routes.
Our logistics team navigates these challenges by implementing strategic regional inventories for commonly used battery models, allowing faster response to customer requirements while complying with shipping regulations. For custom battery designs, we collaborate with clients early in the development process to establish realistic timeline expectations that account for necessary transportation complexity. These logistics considerations add indirect costs that ultimately influence lithium battery pricing compared to less regulated alternatives.
State of Charge Limitations
Regulations governing lithium battery transportation include specific state of charge (SoC) limitations intended to reduce risk during shipping. Current requirements specify a maximum of 30% state of charge for lithium-ion cells and batteries shipped separately (not contained in equipment). This requirement creates additional processing steps in our production workflow, as each battery must undergo a controlled discharge procedure to reach the appropriate state for transportation.
For our high-capacity 51.8V batteries, this discharge process can require 4-6 hours per pack on specialized equipment that precisely controls discharge rates while monitoring individual cell voltages. The discharged energy represents a production loss, as batteries must later be recharged by the end user before initial use. We optimize this process by recovering energy during the discharge cycle through regenerative load banks, reducing both energy waste and heat generation during production.
While these regulatory requirements add complexity and cost to lithium battery logistics, they reflect the legitimate safety considerations associated with these high-energy-density power sources. Our comprehensive compliance programs ensure that all batteries reach customers safely while maintaining full regulatory compliance, protecting both human safety and environmental considerations throughout the supply chain.
Research, Development, and Continuous Improvement
The rapidly evolving technology landscape for lithium batteries drives substantial ongoing investment in research and development. These R&D expenses contribute approximately 5-10% to overall battery costs but enable the continuous performance improvements that make lithium batteries increasingly valuable despite their premium price point.
Chemistry Optimization and Material Science
At the cell level, ongoing research focuses on incremental improvements in energy density, cycle life, fast-charging capability, and temperature performance. Our engineering team collaborates with cell manufacturers to evaluate emerging material technologies such as silicon-enhanced anodes that can boost capacity by 20-40% compared to traditional graphite formulations. These advanced materials typically command premium prices during initial commercialization, with costs gradually declining as manufacturing scales.
For applications prioritizing extreme temperature performance, such as our ultra-low temperature battery systems, specialized electrolyte formulations incorporate carefully balanced additive packages that maintain ion mobility at temperatures as low as -40°C. These custom electrolyte blends undergo extensive testing to verify low-temperature performance while ensuring compatibility with other cell components over the intended service life. The development and validation of these specialized formulations represent significant investments that influence product costs but deliver exceptional performance in challenging environments.
Safety enhancements through material science represent another active research area. Separator materials with ceramic coatings or intrinsic thermal shutdown properties add component costs but dramatically improve cell-level safety by providing additional protection against internal short circuits. Our high-safety battery systems for medical applications incorporate these premium separators despite their 30-40% cost premium over standard materials, as the enhanced safety justifies the additional expense for critical applications.
Manufacturing Process Innovation
Continuous improvement in manufacturing techniques drives both quality improvements and gradual cost reductions for lithium batteries. Our production partners implement technologies such as laser cutting for electrode materials, reducing dimensional variation while eliminating contamination risks associated with mechanical cutting tools. Automated optical inspection systems with machine learning algorithms detect subtle defects that might escape human observation, ensuring consistent quality while reducing labor costs.
Assembly automation continues advancing, with specialized robotics handling increasingly delicate operations previously restricted to manual processing. These manufacturing innovations require significant capital investment but gradually reduce production costs through improved yield, reduced labor requirements, and enhanced consistency. For established cell formats such as the 18650 cylindrical cells used in many of our battery systems, production equipment has evolved through multiple generations, each delivering incremental improvements in cost-efficiency.
Energy efficiency improvements in manufacturing processes represent another focus area. Electrode drying operations traditionally consume substantial energy, but advanced technologies such as microwave-assisted drying can reduce energy consumption by 30-50% while improving coating quality. Formation cycling energy requirements decrease through optimized charging protocols that achieve the same electrochemical results with reduced energy input. These process improvements gradually reduce production costs while also improving the environmental footprint of battery manufacturing.
Battery Management System Evolution
The electronic systems controlling lithium batteries undergo continuous development to enhance functionality while reducing component costs. Early BMS designs utilized discrete components for voltage monitoring and protection functions, while current systems integrate these functions into specialized ICs that reduce both component count and board space requirements. These integrated solutions improve reliability through reduced connection points while lowering manufacturing costs through simplified assembly.
Our latest-generation BMS designs implement advanced algorithms that adapt to battery aging characteristics, maintaining optimal performance throughout the service life. Machine learning approaches analyze usage patterns to optimize charging profiles for specific applications, potentially extending cycle life by 15-25% compared to fixed-parameter management systems. These software enhancements add development cost but deliver substantial value through improved battery longevity and performance.
Wireless connectivity features increasingly appear in modern battery systems, enabling remote monitoring, diagnostics, and even firmware updates to deployed batteries. While these capabilities add component costs through the addition of Bluetooth, WiFi, or cellular communication modules, they create value by enabling preventive maintenance and performance optimization throughout the battery lifecycle. For our commercial clients utilizing large fleets of battery-powered equipment, these connected battery features deliver substantial operational benefits that justify their additional cost.
Conclusion: The Evolving Value Proposition of Lithium Batteries
The higher costs associated with lithium battery technology reflect the advanced materials, complex manufacturing processes, sophisticated control systems, and regulatory compliance requirements necessary to deliver their exceptional performance. As we’ve explored, each component of the lithium battery value chain involves specialized technologies and precision engineering that contribute to overall production expenses. However, the continuing evolution of this technology gradually improves the value proposition through both performance enhancements and incremental cost reductions.
For applications ranging from portable electronics to electric vehicles and stationary energy storage, lithium batteries deliver capabilities that simply aren’t achievable with alternative technologies. Their combination of high energy density, excellent cycle life, minimal maintenance requirements, and declining cost trajectory makes them increasingly competitive despite their premium initial price point. At Vade Battery, we focus on optimizing each aspect of battery design and production to deliver maximum value for specific application requirements, balancing performance, safety, longevity, and cost considerations.
The lithium battery market continues evolving rapidly, with research breakthroughs regularly advancing the performance frontier while manufacturing scale progressively reduces production costs. Organizations evaluating energy storage solutions should consider both initial acquisition costs and long-term value, including factors such as cycle life, maintenance requirements, energy efficiency, and operational benefits of advanced features. Our engineering team specializes in navigating these complex considerations to develop battery solutions optimized for specific application requirements.
For organizations exploring custom lithium battery solutions, we invite you to contact our engineering team or submit specific requirements through our lithium battery design request portal. Our technical specialists can provide detailed recommendations based on your application requirements, helping you navigate the trade-offs between performance capabilities and cost considerations to develop an optimal energy storage solution.