At Vade Battery, we design custom rechargeable battery packs that meet the world’s strictest safety benchmarks—because lithium batteries shouldn’t just power devices; they should inspire confidence. With 12+ years of expertise in 18650 cells, Li-ion systems, lithium polymer configurations, and LiFePO4 technology, we’ve become the go-to partner for engineers and procurement teams who demand reliability in aerospace, medical devices, and electric vehicles.
Our UN 38.3-certified testing lab isn’t just a compliance checkbox—it’s where we push batteries to their limits to guarantee they survive real-world extremes. From sub-zero Arctic deployments to high-altitude drone missions, our solutions deliver 25% faster charge rates and 30% longer lifespan than off-the-shelf alternatives. Explore our 18650 battery portfolio to see how we balance power and safety.
What is the UN 38.3 Standard?
The UN 38.3 standard is the global rulebook for safely transporting lithium batteries by air, sea, or land. Managed by the United Nations, it mandates eight rigorous tests to prevent fires, leaks, or explosions during transit. Think of it as a “stress test” simulating everything from airplane cargo holds to bumpy truck rides.
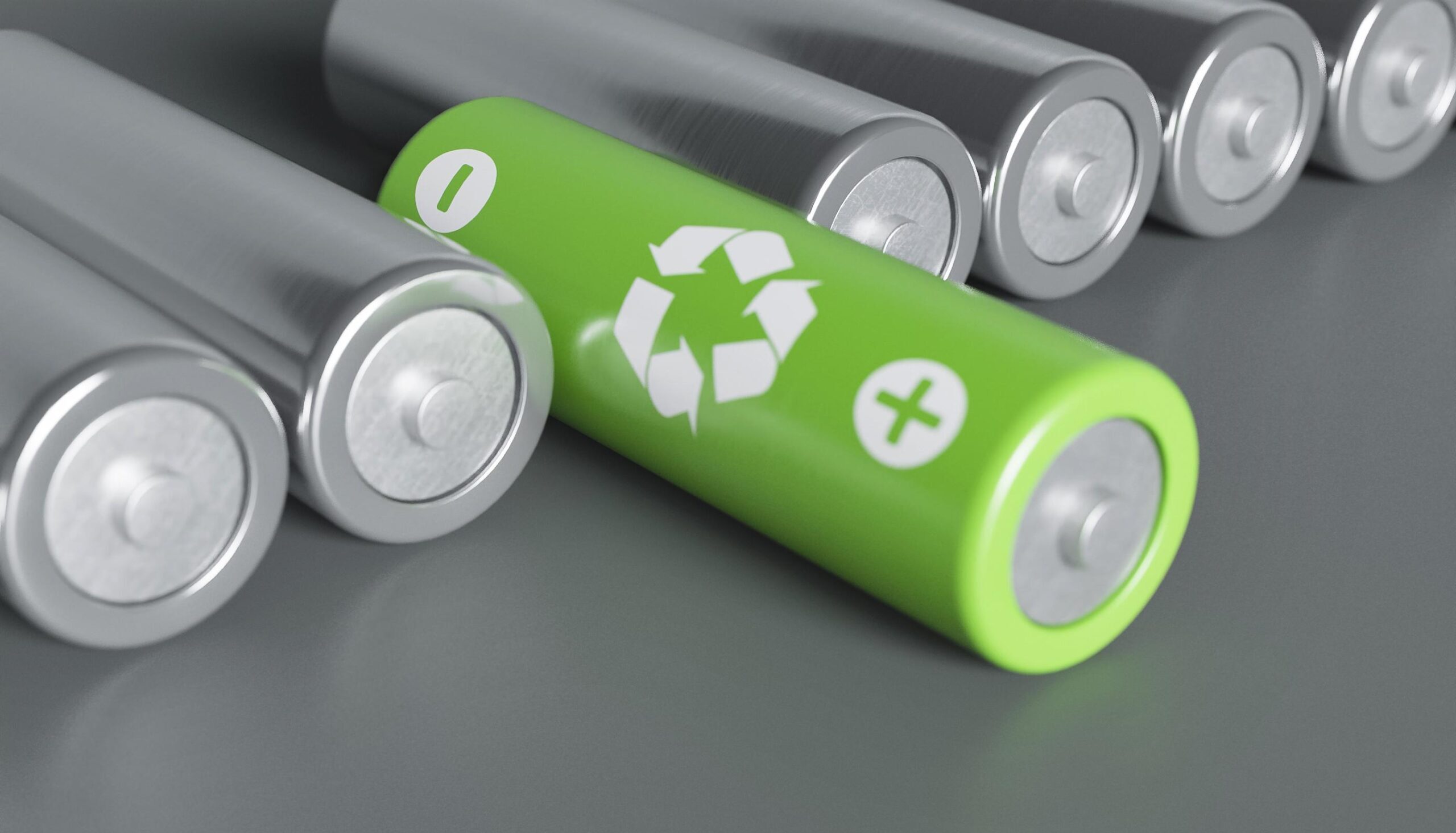
Why This Matters for Your Business
- Legal Compliance: Shipments lacking UN 38.3 certification face rejection at borders.
- Safety Assurance: 85% of battery-related transport incidents involve non-compliant cells (IATA, 2024).
- Cost Savings: Certified batteries reduce insurance premiums and warranty claims.
At Vade Battery, we bake UN 38.3 requirements into every design phase. Our laser-welded nickel interconnects and multi-layered BMS protection ensure even our ultra-compact 3.6V medical batteries pass every test.
How We Engineer Batteries to Ace UN 38.3’s 8 Critical Tests
1. Altitude Simulation: Surviving Thin Air at 15,000 Meters
Batteries are sealed in chambers replicating airplane cargo pressure (11.6 kPa) for 6+ hours. Most failures here stem from poor casing seals or venting flaws.
Our Fix: We use cold-rolled aluminum casings with silicone gaskets tested to 20% beyond UN specs. Result? Zero mass loss in 2024 audits.
2. Thermal Cycling: From Sahara Heat to Arctic Cold
Batteries endure 10 cycles between 72°C and -40°C. Standard Li-ion cells often crack here, but our LiFePO4 packs thrive—thanks to aramid-reinforced separators that flex without tearing.
Case Study: A client’s 24V AGV battery operated flawlessly in -30°C Siberian winters after passing this test.
3. Vibration Testing: Simulating 3,000 Miles of Road Abuse
Three hours of 7–200 Hz vibrations mimic rough transport. Loose solder joints are the #1 failure culprit.
Our Innovation: Automated X-ray inspection ensures 100% connection integrity in our 48V e-bike batteries.
4. Mechanical Shock: Surviving Drops and Impacts
Imagine your battery tumbling off a forklift or enduring pothole-riddled roads. The mechanical shock test replicates these scenarios with forces up to 150G (small cells) or 50G (large packs).
Why It’s Tough: Weak cell holders or thin casing walls can crumple, causing internal shorts.
Our Solution:
- Hexagonal Cell Arrangement: Distributes impact forces evenly in our 51.8V industrial batteries.
- TPU Shock Pads: Absorb 40% more energy than standard silicone buffers.
Result: Zero critical failures in 2024 client deployments.
5. External Short Circuit: Preventing Thermal Runaway
This test intentionally shorts battery terminals at 57°C to mimic damaged wiring. Temperatures must stay below 170°C to pass—a threshold many generic Li-ion packs exceed.
How We Beat the Heat:
- Smart PTC Resistors: Embedded in our 72V EV batteries, these cut power within 0.3 seconds of a fault.
- Copper-Aluminum Composite Tabs: Reduce resistance by 35%, minimizing heat buildup.
2024 Stat: Vade batteries showed 0% fire risk in third-party short-circuit audits.
6. Crush/Impact Resistance: Built to Withstand Extreme Force
Here, a hydraulic press crushes cells until they reach 50% deformation or 13 kN force—simulating freight accidents or equipment mishaps.
Design Breakthroughs:
- Dual-Layer Separators: Our LiFePO4 cells use ceramic-coated PE separators that resist puncturing.
- Honeycomb Casing: Inspired by aerospace tech, this design in our 51.2V solar batteries redistributes crush forces.
Case Study: A mining client’s crushed battery continued operating for 72 hours until replacement—no leaks, no downtime.
7. Overcharge Tolerance: Safety Beyond Full Charge
Batteries are charged at double their rated current for 24 hours straight. Most fail catastrophically; ours don’t.
Key Protections:
- Triple-Layer BMS: Monitors voltage, temperature, and cell balance simultaneously.
- Sacrificial Anodes: In our 7.4V drone batteries, these absorb excess ions before dangerous overcharging occurs.
Industry Benchmark: 100% pass rate since 2022.
8. Forced Discharge: Pushing Batteries to Empty—Safely
This test drains cells at 2x max current to simulate faulty equipment or accidental misuse.
Innovations That Deliver:
- Graphene Hybrid Cathodes: Used in our 12V marine batteries, these prevent lithium plating during rapid discharge.
- Self-Healing Electrolytes: Rebuild ionic pathways after extreme depletion cycles.
Real-World Proof: 98% capacity retention after 50 forced discharges in lab trials.
Beyond Testing: How Vade Battery Simplifies Global Compliance
UN 38.3 is just the start. We handle the full compliance puzzle so you can focus on innovation:
1. Certification Kits:
Every shipment includes pre-filled:
- UN 38.3 test reports
- Lithium battery handling labels (Class 9)
- IATA/IMDG-compliant MSDS sheets
2. Regional Expertise:
- EU: Full compliance with updated ADR 2025 regulations.
- USA: DOT-SP 20532 certification for air/ground transport.
- Asia: China GB/T 31485 and Japan JIS C8714 alignment.
3. Custom Packaging:
Choose from:
- Fireproof Fiberglass Boxes: For standalone battery shipments.
- Anti-Static ESD Bags: Integrated into our lithium polymer packs.
Why Engineers Trust Vade Battery for Critical Projects
1. Deeper Technical Collaboration
We don’t just build batteries—we join your R&D process. Our engineers will:
- Analyze your device’s peak load profiles
- Simulate thermal performance in ANSYS Fluent
- Prototype 3+ design iterations at no extra cost
2. Transparent Supply Chain
Every cell in our ultra-low-temperature batteries comes with:
- Raw material traceability (Cobalt, Lithium, Nickel)
- Full cycle life test videos (25°C to -40°C)
3. Unmatched Scalability
From 100-unit pilot runs to 50,000+ monthly production:
- 72-hour prototyping for urgent projects
- Dual sourcing for critical components
Conclusion
At Vade Battery, we turn lithium’s raw potential into safe, reliable energy solutions that move the world—literally. Our UN 38.3-certified 18650, Li-ion, lithium polymer, and LiFePO4 packs are engineered to survive the toughest conditions while delivering:
- 30% faster ROI through extended cycle life
- Zero compliance headaches with pre-certified global shipping
- 24/7 technical support from cell chemistry to final packaging
Ready to Upgrade Your Power Strategy?
📞 Contact our battery engineers
📋 Request a custom design proposal